Maximilian Vogl describes how Gerresheimer is expanding its range of prefillable polymer syringes to include a new product: the Gx RTF® ClearJect® polymer syringe, 2.25 mL.
Building on the Gx RTF® ClearJect® 1.0 mL “long” syringe, Gerresheimer is expanding its range of prefillable polymer syringes to include a 2.25 mL version, the Gx RTF® ClearJect® polymer syringe, 2.25 mL (Figure 1).
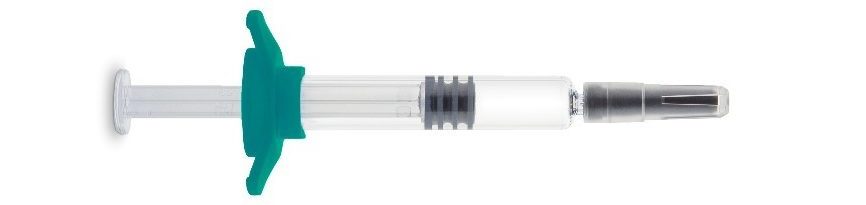
Figure 1: The new Gx RTF® ClearJect® 2.25 mL polymer syringe.
The syringe is made from cyclic olefin polymer( COP), equipped with a 27-gauge, 1/2-inch (12.7 mm), thin-walled stainless-steel needle with three bevels, and is suitable for use as primary packaging for sophisticated medications, especially for sensitive, biologicals, biosimilars, and biobetters.
The product was developed in close co-operation between two Gerresheimer locations in order to create synergy between the syringe experts in Bünde, Germany, and the plastic experts in Wackersdorf, also in Germany.
The syringes are engineered for use in autoinjectors thanks to their robustness and precision.
Low Potential for Interaction with Medication
COP does not release tungsten metal ions into the medication solution as glass syringes can, which is a major concern for some. Since the entire syringe, including the insert-moulded needle, is produced in a single step, the product is free of tungsten and adhesives. The material has a high pH tolerance and the pH value does not change while in storage. The oxygen permeation rate is low in comparison with other plastics, and the values for extractables and leachables are low.
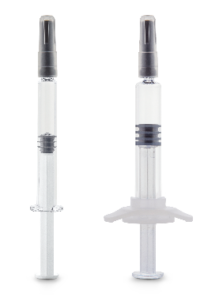
Figure 2: The Gx RTF® ClearJect® polymer syringe is now available in 1.0 mL “long” and 2.25 mL versions.
Safety and Reliable Functionality for the End User
Another important argument in favour of the Gx RTF® ClearJect® needle syringe is its end-user safety. COP is particularly break-resistant, making it suitable for packaging aggressive or toxic materials. The syringes are siliconised with a precisely controlled quantity of the highly viscous 360 MD (12,500 cST) silicone oil Dow Corning (Midland, MI, US), in order to ensure reliable syringe functionality with low breakaway and sliding forces with the lowest possible particle load.
Precision and Flexible Design
Production in the injection moulding process ensures precise dimensions. The dead volume in the syringe is also minimised, reducing overall waste of the costly drugs. The material enables a broad range of design options, which make it ideal for customer specific-requirements. The syringes are engineered for use in autoinjectors thanks to their robustness and precision.
Economic Efficiency Through Standard Components
This 2.25 mL syringe system, like the 1.0 mL syringe (both shown in Figure 2), is economical thanks to the fact that the innovative COP syringe body is designed to use commercially available standard components throughout. This starts with the use of standard cannulas and continues with the piston rods, piston plungers, backstops and closure systems used.