To Issue 133
Citation: Farina S, “Injecting the Future”. ONdrugDelivery, Issue 133 (May 2022), pp 86–89.
Simone Farina discusses Flex’s new smart autoinjector platform for the healthcare market, designed to enable original equipment manufacturers to accelerate time-to-market, reduce costs and boost reliability, while ensuring patient compliance.
The global covid-19 vaccination rollout brought into sharp focus the importance of speed when bringing new drugs to market. It has highlighted the complexity of administering drugs and keeping track of patient drug dosing and timing of doses. Even at a personal level, if you have had the vaccine, that recent experience may have surfaced some of your own concerns about being injected. The fact is that injections are a day-to-day reality for millions of chronic disease patients who feel the same. The market has been ready for low-cost, smart autoinjection devices that are easier to use.
“The Flex design team engineered and created a new autoinjector platform in response to the growing adoption of autoinjector devices and the corresponding increase in the diverse demands placed upon them.”
SMART AUTOINJECTOR PLATFORM
The Flex design team engineered and created a new autoinjector platform in response to the growing adoption of autoinjector devices and the corresponding increase in the diverse demands placed upon them. The platform is designed to help medical device original equipment manufacturers (OEMs) overcome design delays and costs and to facilitate a smoother path from production to patient.
The Flex autoinjector platform features:
- A drug delivery engine capable of managing multiple drugs, as it can identify a cassette and the type of drug inserted.
- Temperature monitoring for the management of less painful injections.
- A skin sensor for optimal placement of the autoinjector on the injection site.
- Voice control through an advanced touchless user interface able to recognise sequences of human speech and translate them into operative commands for the device.
- Support for low-power Bluetooth and CatM1/NB-IoT connectivity to mobile phones or the cloud for managing information about drugs delivered and related therapy.
- Modular firmware composed of an application layer, allowing for customisation to meet unique medical device OEM requirements, and built on top to a predeveloped and tested standard part.
ADVANCED DRUG DELIVERY ENGINE
Motor Regulation for Drug Delivery and Needle Insertion Speed Control
At the core of the platform are two motors: one to manage the needle insertion, the other to manage drug delivery. Needle insertion is performed via a direct current motor connected to a syringe. A leadscrew transforms the rotational movement of the motor into a linear one and a proportional-integral-derivate (PID) algorithm is used to control speed during needle movements. The end of needle insertion and its retraction are defined by stall conditions that are detected by the encoder movement. This design protects patients from accidentally puncturing themselves and can reinforce confidence when using the device. Patients can also control the variable needle insertion speed, optimising it to deliver less painful injections.
“Temperature monitoring checks for drug degradation or unacceptable levels of drug viscosity, both of which can lead to more painful injections.”
The drug delivery motor subsystem moves a prefilled syringe (PFS) of 1 mL/vial plunger at a constant speed, selected by the user. The speed of the injection and speed of drug delivery can affect the patient’s perception of pain – which, of course, varies from person to person. The speed selected is kept constant by a PID algorithm. If a full dose is delivered, the end of the injection is detected by a stall condition. If only a portion is provided to the patient, a fine position control is used to monitor the end of the dose delivered.
Another benefit from the motor-driven systems in the platform is that different kinds of drugs can be used. Identification details on the cassette mean the drug and dose are recognised immediately by the device. The PID parameters are adjusted to meet the viscosity characteristics of that specific drug and a constant speed is set for drug delivery.
Identification of the Cassette and Type of Drug
The autoinjector is equipped with a near field communication (NFC) reader that can communicate with the NFC tags of the drug cartridges (Figure 1). This assures the authenticity of the cartridge, identifies the type of drug and checks its validity (i.e. expiry date). It also reads delivery parameters and stores logs about injections completed. All of these processes can be encrypted. Additionally, the passive NFC tags can harvest energy from the same electromagnetic field used for communication, so power is not needed – offering a cost-effective solution.
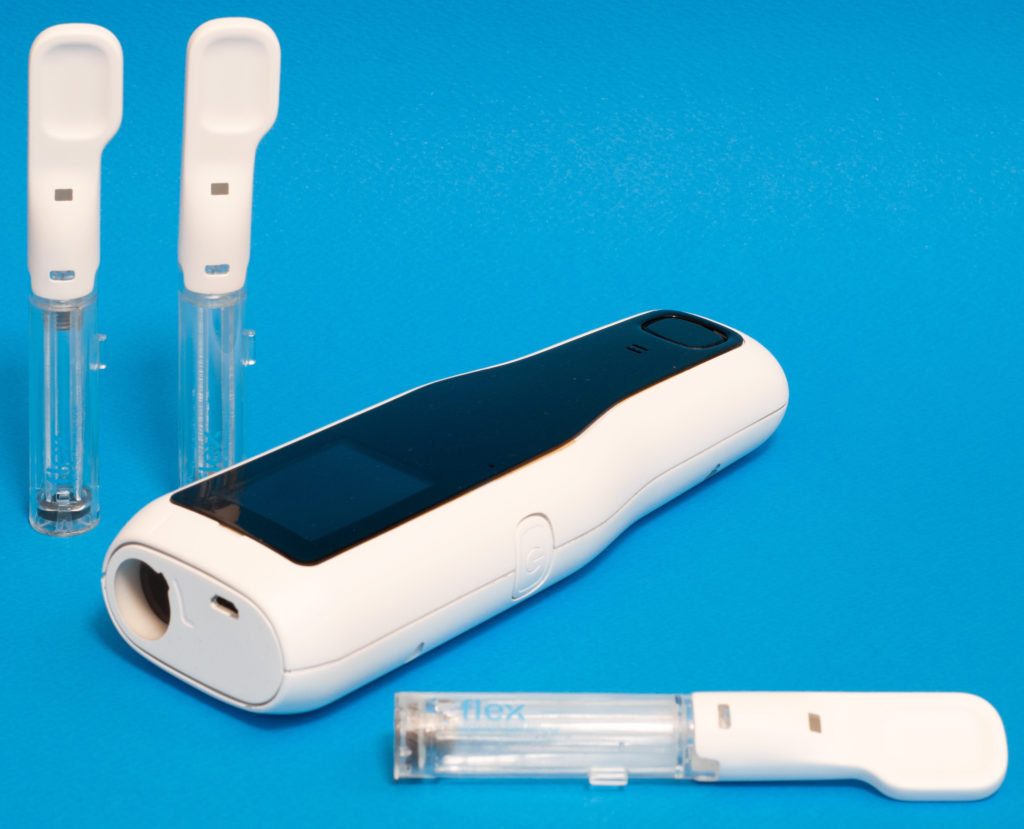
Figure 1: The autoinjector is equipped with an NFC reader that communicates with the drug cartridge tags.
Temperature Monitoring to Improve the Injection Experience
Multiple temperature sensors are integrated into the platform. These sensors monitor various components, including the autoinjector itself, to ensure the unit is only used within the defined operating conditions. The rechargeable battery temperature is also monitored to verify the battery is only charged within its defined operating temperature range. Temperature monitoring also checks for drug degradation or unacceptable levels of drug viscosity, both of which can lead to more painful injections.
Skin Sensor Detector for Correct Device Placement
To help deliver an optimal injection, a sensor in the apical part of the device detects the presence of skin and the angle of the autoinjector (Figure 2). The skin sensor is a capacitive model embedded in the printed circuit board and can precisely distinguish skin from other surfaces. The unit can also detect the autoinjector’s tilt angle to perfectly position over the ideal injection zone; if contact with the skin is lost, the delivery of the drug is interrupted. This sensor essentially self-regulates to compensate for changes in environmental conditions.

Figure 2: The skin sensor helps deliver an optimal injection.
VOICE CONTROL/TOUCHLESS USER INTERFACE
As medical devices move towards consumerisation, particularly in the drug delivery space, both usability and user interface have grown in importance. Voice control in smart consumer products has paved the way for voice-enabled injection devices. Through a more natural human-machine interaction, the patient can issue commands directly to the autoinjector, instructing it to start or suspend the injection or to adjust speed settings.
Machine-learning algorithms have allowed the platform to implement a speech recognition model optimised to run on low-power and low-memory-size microcontrollers. This also ensures an increased level of data privacy because the information is exclusively processed on the device, with no connection to the cloud.
The effectiveness of speech recognition depends on a unit’s ability to operate in noisy conditions. The Flex platform uses an on-board voice solution where sensors capture motor and ambient background sounds and, with real-time edge processing, mutes those sounds from the recognition software. This enables the embedded speech recognition engine to recognise the user’s voice commands easily.
“Providing family members, caregivers or clinicians with drug delivery data can save time and worry for all concerned.”
AN INTEGRAL PART OF DIGITAL HEALTH ECOSYSTEMS
Providing family members, caregivers or clinicians with drug delivery data can save time and worry for all concerned. The Flex platform transfers data to mobile phones or clouds.
Data Transfer to Smartphone via Low-Power Bluetooth
The platform can send data via low-power Bluetooth directly to a smartphone or equivalent media. This inexpensive short-range communication technology has evolved to be transformational in the world of drug delivery. As smartphone ownership becomes increasingly common, patients can access a colourful and interactive user interface where data measurements sets, with the corresponding time stamps (i.e. complete data sets), can be stored or shared.
Data collected can be uploaded to a cloud-hosted database, where algorithms instruct data processing to extract patterns and inform, for example, therapy changes. In this sense, smartphones are used as a communication gateway between the medical device and the data backend. The Bluetooth interface supported by the platform is an ideal technology to enable data to reach smartphones. This solution optimises battery life and ensures enough data throughput and physical connectivity at less cost.
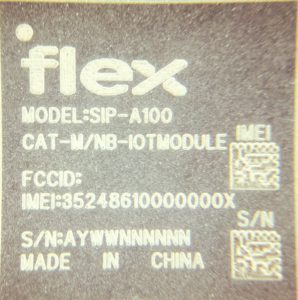
Figure 3: Cat-M1/NB-IoT cellular connectivity allows automatic and direct access to the cloud.
Data Transfer Directly to Cloud
Flex’s expertise in cloud and communications infrastructure enables it to deliver a solution ready for the data-driven, 5G smart and connected future (Box 1). The Flex autoinjector platform is equipped with low-power wide-area Cat-M1/NB-IoT cellular connectivity (Figure 3). This emerging technology for Internet of Things (IoT) applications allows automatic and direct access to the cloud via an integrated SIM card. There is no need for the patient to initiate the communication.
Cat-M1 and NB-IoT leverage existing 5G network infrastructure, so they do not require additional deployment of an antenna, radio or other hardware. They use smaller bandwidth than standard long-term evolution, which is convenient for battery-operated IoT application needs.
BOX 1: STANDARDS AND REGULATIONS
Flex designs needle-based injection systems containing electronics (NIS-Es) that are compliant to international standards required to demonstrate conformity to the essential requirements of the Medical Devices Regulations (Regulation (EU) 2017/745 of the European Parliament and of the Council of 5 April 2017 on medical devices), US FDA regulations and other national requirements.
Flex leads product development according to several standards – ISO 10993 to guarantee the biocompatibility of the materials, REACH regulation to improve the protection of human health and the environment from the risks that can be posed by chemicals, the RoHS Directive related to the restriction of hazardous substances in electrical and electronic equipment and the Waste Electric and Electronic Equipment Regulations.
Flex designs medical devices in line with the IEC 62366-1 usability standard, the IEC62304 software lifecycle requirements and the standards related to electromagnetic compatibility, wireless communication and cybersecurity.
With a patient-safety-first approach, Flex designs NIS-Es with features designed to reduce risk for the patient and meet the IEC 60601 standard related to basic safety and essential performance and the ISO 11608 standard focused on accuracy of delivered doses. The Flex Milan Design Center is one of the few ISO 17025-certified test laboratories to verify requirements for the ISO 11608-1 standard, and a Flex Milan representative is a member of the technical committee appointed to develop these standards. Flex actively collaborates with the most important international certification agencies, offering its customers a support service for a smooth and straightforward certification of their products.
FIRMWARE FRAMEWORK
The Flex autoinjector platform is equipped with modular firmware created by reusable and customisable building blocks designed to speed up the process of firmware development and testing in relation to the final customer product (Figure 4). Flex offers pharmaceutical companies a software development service for the application layer, which creates the unique solution based on a customer’s requirements.
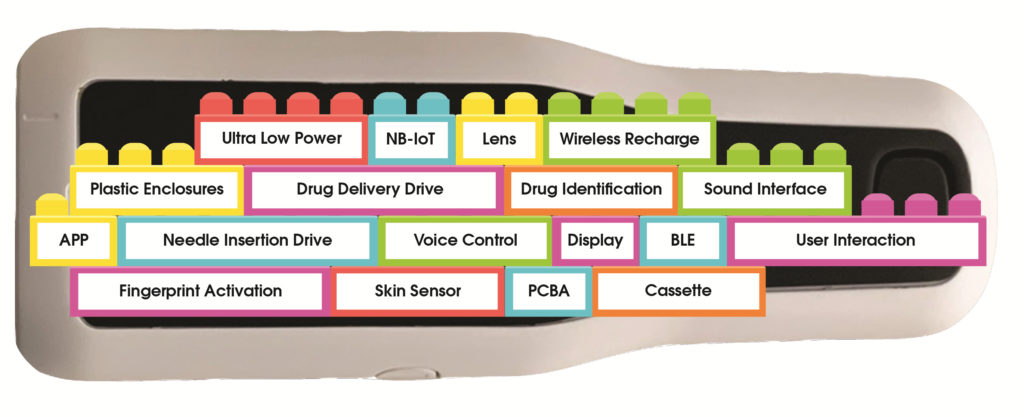
Figure 4: The autoinjector platform is modular to accommodate features such as multiple drug delivery speeds.
The software is created using building blocks, similar to how a house is built with prefabricated bricks. The blocks are Flex’s intellectual property (IP), while the customised parts are the OEM’s IP.
The firmware is compliant with the IEC 62304 standard, which specifies lifecycle requirements for the development of medical software and software within medical devices.
SUMMARY
The demand for effective homecare and remote monitoring has increased the relevance of autoinjectors for patients looking to manage chronic illnesses and allergies conveniently without visiting hospital. This has been especially true in the case of diabetes, Crohn’s disease and rheumatoid arthritis patients relying on PFSs and autoinjectors to manage their condition at home. Pharmaceutical companies looking to meet these rising at-home needs are going to require flexibility, faster time to market, cost efficiencies and reliability in their autoinjector products, while ensuring patient compliance.
The Flex autoinjector platform offers a modular approach that addresses these needs:
- An efficient drug delivery system
- An advanced touchless user interface
- A complete set of connectivity solutions that places the autoinjector at the heart of a digital health ecosystem
- A flexible firmware framework able to implement the customer’s requests on top of a robust preconstituted stack.