Citation: Schmidt Moeller C, “Wearable Injectors: Choosing and Testing Adhesives for Optimal Performance”Development of an Osmotic Larger Volume Wearable Bolus Injector”. ONdrugDelivery Magazine, Issue 100 (Sep 2019), pp 46-48.
Claus Schmidt Moeller provides an overview of the mechanism, functionality and applications of the company’s osmotic, single-use, low-cost, versatile wearable bolus injector.
As of today, only a few wearable injectors for the subcutaneous home administration of pharmaceuticals – also called large volume injectors and wearable bolus injectors – are marketed or in clinical development. They can deliver viscous drugs at about 1 mL per minute. They represent a promising class of delivery device and many pharma companies have high expectations of what wearable injectors can bring to the table for the delivery of biologics.
“Disposal of electronics after a single use is not preferential in an ever more environmentally conscious world, and cold storage of batteries for years represents another challenge.”
Subcutaneous injection of high viscosity liquids, or injection against high back-pressures through thin needles, has a number of challenges and requires a high force. Therefore, most wearable injectors are based on electromechanical solutions that can control the injection and generate the needed high force, often by means of an electrical motor, a battery and a gearing mechanism. But electromechanical solutions generally become complicated and expensive, and most solutions do require more user steps than would be the case with, for example, a prefilled autoinjector. Furthermore, disposal of electronics after a single use is not preferential in an ever more environmentally conscious world, and cold storage of batteries for years represents another challenge.
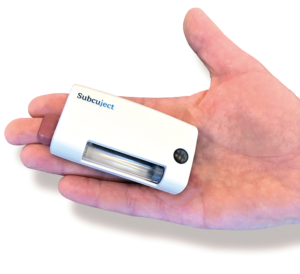
Figure 1: Functional model of the Subcuject device with a 3 mL standard cartridge.
In response to these challenges, Subcuject is developing a wearable bolus injector, the Subcuject WBI, based on osmosis as the driving force. Osmosis as a power source is inexpensive, does not require an additional energy supply (such as electricity from a battery), is noiseless and can create very high forces in a smooth and controlled way. Furthermore, disposal of an osmosis-powered device has a low environmental impact due to there being no electronics or batteries.
“The patented, osmotically driven Subcuject WBI creates pressure by drawing water through two semipermeable forward osmosis membranes into a pressure chamber, by means of a patented osmotic agent.”
Subcuject is currently testing a moulded functional model of the device (see Figures 1 and 2) and preliminary results of these tests – as well as earlier tests – show that the osmotic actuator’s function is not sensitive to higher viscosities or high back pressures. This also means that the device functions well with a range of needle gauges, even with relatively high-viscosity formulations. Specifically, injection rate is approximately 1 min/mL and it is seen that injection of water against a very high back-pressure of 69 kPa (10 psi) only takes about 30% longer than injection against a back-pressure of 21 kPa (3 psi). Injection of 50 cP sucrose solution with a G27 needle also takes about 30% longer compared with water (1 cP) with any needle gauge.
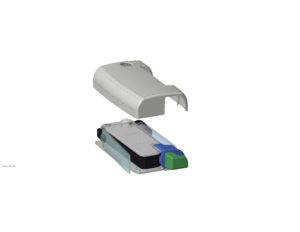
Figure 2: Inside of the functional model, where in
the actuator with the feed water pouch attached, the 3 mL cartridge and the needle unit can be seen.
The patented, osmotically driven Subcuject WBI creates pressure by drawing water through two semipermeable forward osmosis (FO) membranes into a pressure chamber, by means of a patented osmotic agent. The excess water in the pressure chamber then acts as a hydraulic plunger rod, pushing the plunger in a cartridge forward.
A constant flow rate is provided by gradually increasing the membrane area that is subjected to the osmotic agent over the injection time. This compensates for dilution, while at the same time it prevents the majority of the osmotic agent from escaping with the excess water from the actuator and into the back end of the drug cartridge, pushing the plunger. This ensures a relatively constant flow up to at least 10 mL of injection (Figure 3). Furthermore, the device’s function is quite independent of physical orientation (up, down etc). The use of two membranes ensures that approximately the same amount of osmotic agent is in contact with the membrane, irrespective of the orientation.
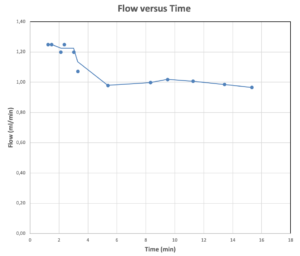
Figure 3: Graph showing results from an earlier isolated actuator test with same internal geometry as the above functional device model. Flow rate stabilises at about 1 mL/min and is stable for minimum 15 mL injection.
The osmotic process is initiated when the user presses the start button. This releases the dissolved osmotic agent from a non-permeable container inside the pressure chamber. As the osmotic agent cannot pass out through the forward osmosis membranes, the actuator will instead draw water into the pressure chamber from a water supply on the outside of the actuator, in an attempt to create an ionic balance.
Needle insertion and retraction is automatic and controlled mechanically. The needle is inserted into the patient when the start button is pressed and, by means of a patented cartridge valve, the needle is caused to be retracted by a spring when the cartridge plunger reaches the end position.
The Subcuject device currently in development is a 3 mL version, which makes use of off-the-shelf cartridges and off-the-shelf plungers. This means that all primary packaging materials are known and well characterised in relation to drug stability. Given the osmotic actuator performance, the device can be developed for injection volumes up to 10 mL.
From a users’ point of view, the Subcuject WBI is a prefilled, relatively small, noiseless device with only one button to push, and which is acceptable for disposal after single use.
From a pharma company’s point of view, the device contains only a small number of inexpensive components and the manufacturing price is comparable with that of autoinjectors. Only the assembled and filled cartridge and the needle unit need to be sterilised, meaning no terminal sterilisation is necessary.