Citation: Mussoi C, Prete R, Katz M, “Stevanato Group and Eitan Medical Bring Next-Generation Wearable Drug Delivery Solutions to Market”. ONdrugDelivery, Issue 117 (Mar 2021), pp 32–36.
Chiara Mussoi, Riccardo Prete and Mindy Katz outline the benefits of collaboration when it comes to bringing wearable drug delivery solutions to market.
The collaboration between Stevanato Group and Eitan Medical (developer of the Sorrel wearable injection device platform) is founded on the principal aim of bringing to market wearable injection solutions for the simple and efficient subcutaneous administration of large-volume and high viscosity medications that serve the interests of both patients and pharmaceutical companies. As a leading producer of primary packaging and integrated capabilities for drug delivery systems, Stevanato Group plays a key role in the optimisation of primary containers – both cartridges and vials – for integration into large-volume wearable injectors.
“The Sorrel wearable drug delivery device platform is designed to provide both a patient-centric and partner-focused solution for the self-administration of large-volume and high viscosity medications.”
The collaboration began with the development of cartridges to serve as primary drug reservoirs for Eitan Medical’s Sorrel wearable device line, later expanding to include the supply of glass containers for vial-based configurations of the device. Sorrel devices are, by design, primary-container agnostic, being able to accommodate a variety of different container types in a range of volumes and dimensions. Although not tied to a specific primary container manufacturer or proprietary design, the unique collaboration leverages the core strengths of both companies: Stevanato Group’s extensive experience in the design and testing of glass primary containers and its position as a leading provider of containment solutions combined with Eitan Medical’s development expertise in the area of smart, electromechanical drug delivery and infusion devices.
Both companies are united in their commitment to improve the self administration experience and outcomes for patients, while helping pharmaceutical partners mitigate risks and minimise time to market with proven technical, regulatory and manufacturing expertise.
THE SORREL WEARABLE DRUG DELIVERY DEVICE PLATFORM
The Sorrel wearable drug delivery device platform is designed to provide both a patient-centric and partner-focused solution for the self-administration of large volume and high-viscosity medications. The prefilled and preloaded configuration encourages adherence to treatment therapies while reducing the risk of medication errors. The incorporation of multiple smart sensors and indicators further guarantees patients a successful self-administration experience.
Because the platform is primary-container agnostic (Figure 1), pharmaceutical companies working with the Sorrel platform enjoy the flexibility to use the primary container of their choice, thus enabling Eitan Medical to collaborate with multiple pharmaceutical partners across a wide range of molecules, volumes and indications. Additionally, the Sorrel platform’s proprietary technology provides a distinctive solution for drawing medication directly from a vial, while still enabling a prefilled and preloaded configuration, presenting several advantages to customers. Pharmaceutical partners can thereby save considerable time and risk by commercialising a combination product with the device constituent being a Sorrel vial-based wearable injector.
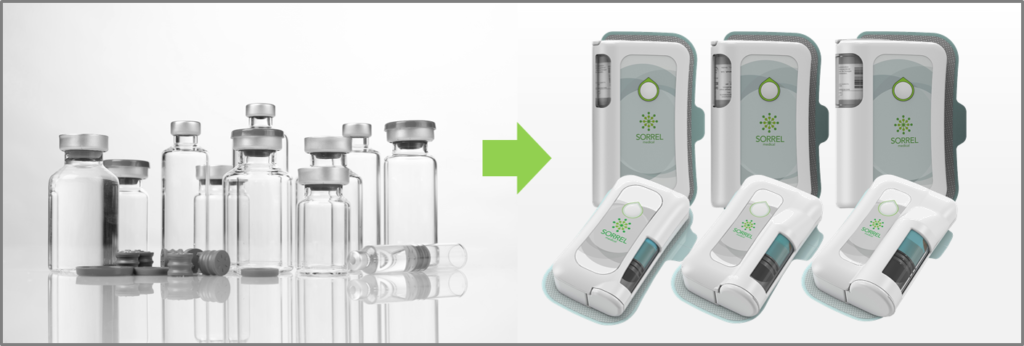
Figure 1: The Sorrel platform is primary container agnostic.
“The Sorrel platform’s proprietary technology provides a distinctive solution for drawing medication directly from a vial, while still enabling a prefilled and preloaded configuration.”
Eitan Medical’s decision to introduce a vial-based configuration for its Sorrel wearable platform provides a number of key benefits for pharmaceutical partners. Glass vials constitute the most versatile primary packaging containment solution, as almost all pharmaceutical companies already possess internal vial filling capabilities. This can help to ensure compatibility with a wearable drug delivery platform from the initial development stages of new drug formulations, while also enhancing the lifecycle management of those products already on the market with established supply chains.
OPTIMISING GLASS CONTAINMENT SOLUTIONS
Stevanato Group’s contribution to the development of the Sorrel wearable devices surpasses the mere provision of glass primary packaging to include technical, analytical and project management competencies that provide fully integrated containment solutions for wearable drug delivery devices. The customised package comprises several key components, primarily high quality primary packaging in the form of Stevanato Group’s SG EZ-fill format. Also included is the identification of the most suitable add-on components according to the final application and the filling process, leveraging Stevanato Group’s proficiency and long history of collaboration with leading closure manufacturers of rubber plunger stoppers, lined caps, front caps and aluminium crimps for cartridges, as well as front caps and aluminium crimps for vials.
Stevanato Group can additionally provide standard and ad-hoc testing of drug-container and container-device interaction within the company’s ISO/IEC 17025 certified internal laboratory. Additionally, project management support enables partners to focus their energies on core activities while Stevanato Group co-ordinates parties to provide container closure systems that are ideally suited for the device platform. Internally developed glass converting technologies, scalable and flexible assembly solutions and sterilisation processes allow the company to strictly control all manufacturing parameters relating to drug product quality and safety.
“Pharmaceutical companies can easily address specific concerns – such as breakages, cosmetic issues and particle generation – enabling them to devote greater energy to core activities such as new drug development.”
SG EZ-FILL FOR ASEPTIC MANUFACTURING
Stevanato Group’s EZ-fill platform provides a fully integrated pre-sterilised solution for aseptic manufacturing, developed in close collaboration with equipment manufacturers in response to the growing demand for increased operational flexibility. Available in a double secondary packaging configuration (nest-and-tub and tray), SG EZ-fill provides an optimal solution for both small-batch and industrial-scale production.
Close collaboration with key providers of ready-to-use closures and add-on components has enabled Stevanato Group to offer systems fully compliant with international regulations. Pharmaceutical companies can therefore easily address specific concerns – such as breakages, cosmetic issues and particle generation – enabling them to devote greater energy to core activities, such as new drug development. Additionally, by using proven packaging, SG EZ-fill is able to maximise filling efficiency by allowing for different filling nozzle combinations. Every aspect of the filling process can therefore be streamlined, from incoming material to final product shipment.
The use of a nest-and-tub configuration confers further key benefits to the SG EZ-fill platform, minimising glass-to-glass contact, increasing cosmetic quality and reducing particles, which results in a lower risk of rejection and waste of drug products, along with higher mechanical resistance, thus reducing the risk of container breakage and further drug loss.
PRIMARY CONTAINER CONSIDERATIONS FOR OPTIMISATION INTO LARGE-VOLUME WEARABLE DEVICES
Using the SG EZ-fill format enables Stevanato Group to provide large-volume primary cartridges ranging from 5 mL to 20 mL that can be integrated into wearable delivery systems suitable for treatment of chronic illnesses. With complete control of the forming conditions, and through continuous product improvement, Stevanato Group can optimise the internal shape of the primary container, thus maximising dosing accuracy. Furthermore, every aspect of the drug reservoir – length, diameter, volume, neck size, flange design and closure – can be customised according to a specific device’s technical needs.
With the aim of obtaining a homogenous silicone layer in terms of thickness and distribution, the proper and optimised silicone recipe for each format is defined by a tailored design of experiment study. Using proprietary siliconisation technology and automatic camera controls guarantees optimal results for gliding profile and good cosmetic appearance.
As a full solution provider, Stevanato Group is further able to support plunger development to reduce the dead volume and optimise “glideability” by using the partner’s preferred rubber manufacturer, formulation and coating. Moreover, Stevanato Group can pre-assemble cartridges with the customer’s closure of choice (for example, a front stopper with or without flip-off) from all major closure manufacturers. Specific in-line cameras are dedicated to control the quality of the crimping to improve container closure integrity.
EVOLUTION OF A PROVEN VIAL SOLUTION FOR INTEGRATION IN WEARABLE DEVICES
Stevanato Group has developed rigorous inspection protocols to ensure compliance with the strictest partner requirements in terms of both dimensional and cosmetic parameters. Dimensional conformance is integral to ensuring compatibility between primary containers and drug delivery devices, while maintaining cosmetic standards reduces the risk of non-quality rejection in fill-and-finish lines, avoiding wastage of valuable drugs (Figure 2).
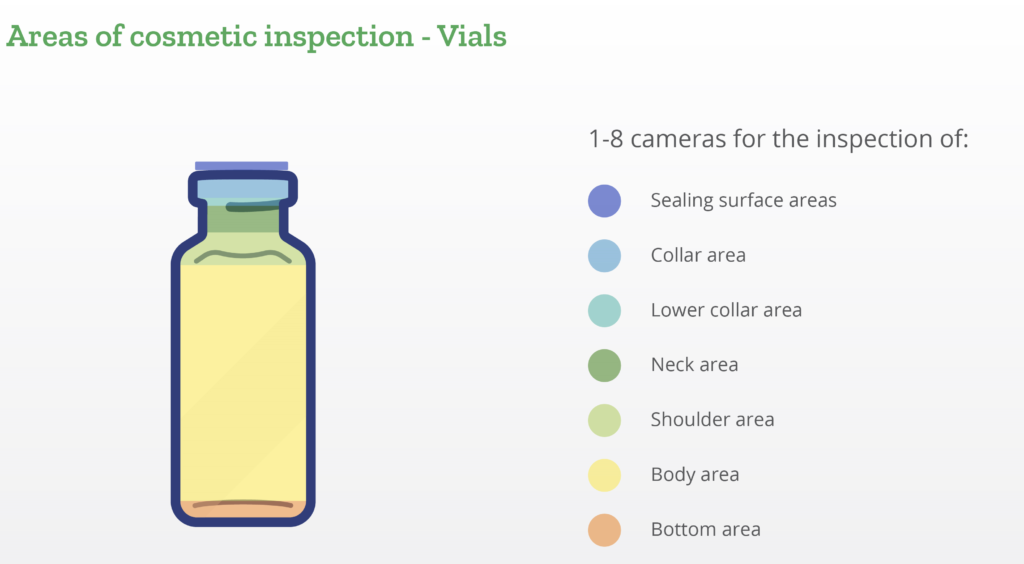
Figure 2: Cosmetic controls on Stevanato Group vials.
Dimensional and cosmetic quality of the vials is maintained through automated inspection systems installed in production lines. Cameras positioned before the packing station detect scratches, deformations, bubbles, pressure marks, airlines, chips and cracks. Manual controls are performed before, during and after both the production process and the SG EZ-fill process. Using specially designed techniques and instruments, quality control teams ensure that all products fully meet both customers’ and regulators’ quality and dimensional requirements (Figure 3).
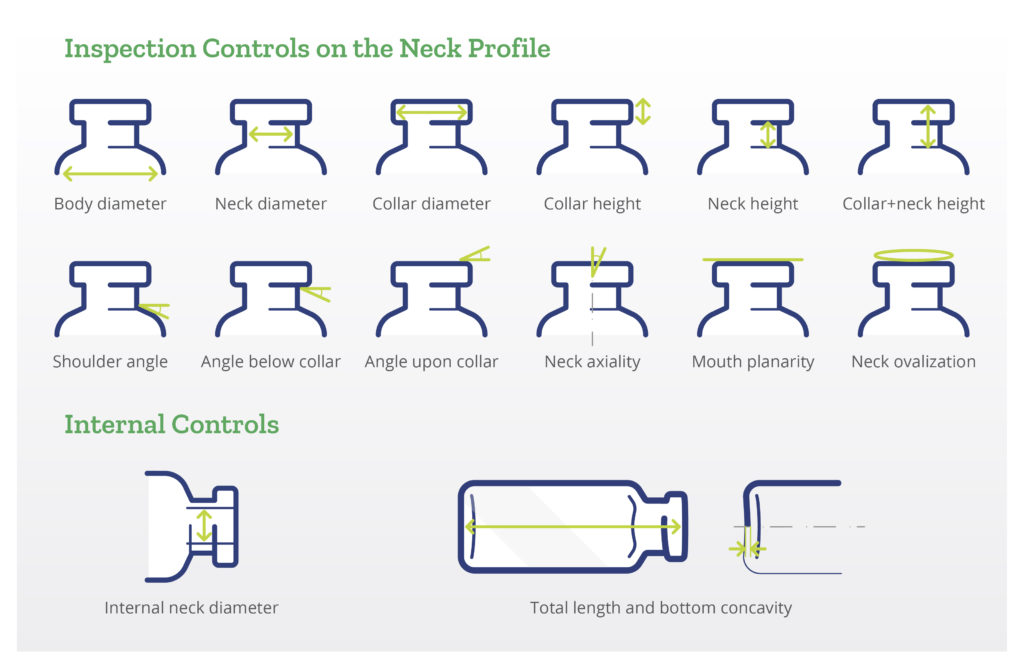
Figure 3: Dimensional controls on Stevanato Group vials.
SORREL DEVICE ASSESSMENT PROTOCOLS
In addition to the inspection protocols performed by Stevanato Group, once received by Eitan Medical a thorough testing regime is conducted by the verification and validation teams, ensuring that the Sorrel device and the relevant primary container and closure components work together seamlessly.
“Early co-operation can expedite the introduction of new drug delivery systems for the benefit of all parties – the device manufacturer, container provider, pharmaceutical developer and, ultimately and most importantly, the patient.”
General dose accuracy testing is performed with any new primary container and components to determine overall device performance and functionality. Needle penetration force and depth measurements are taken for each new device/container/component configuration, optimising the depth to which the needle penetrates the septum to ensure it always clears the rubber partition to enter and draw medication from the primary container.
To ensure proper mechanical fit of the primary container within the Sorrel device, Eitan Medical can easily customise the device’s plastic casing to adapt to different dimensions of a primary container. Certain device configurations include an internal adapter that can be employed to allow smaller primary containers to use the same device for testing purposes. For example, the Sorrel fully functional 20R vial-based wearable injector can easily be configured to accommodate 10R vials, allowing pharmaceutical companies to test different vial sizes with just a quick insertion of an adapter in the device assembly line. This is yet another example of how pharmaceutical companies can test products more quickly, and kick off development projects faster, with the platform approach of a medical device manufacturer (Figure 4).
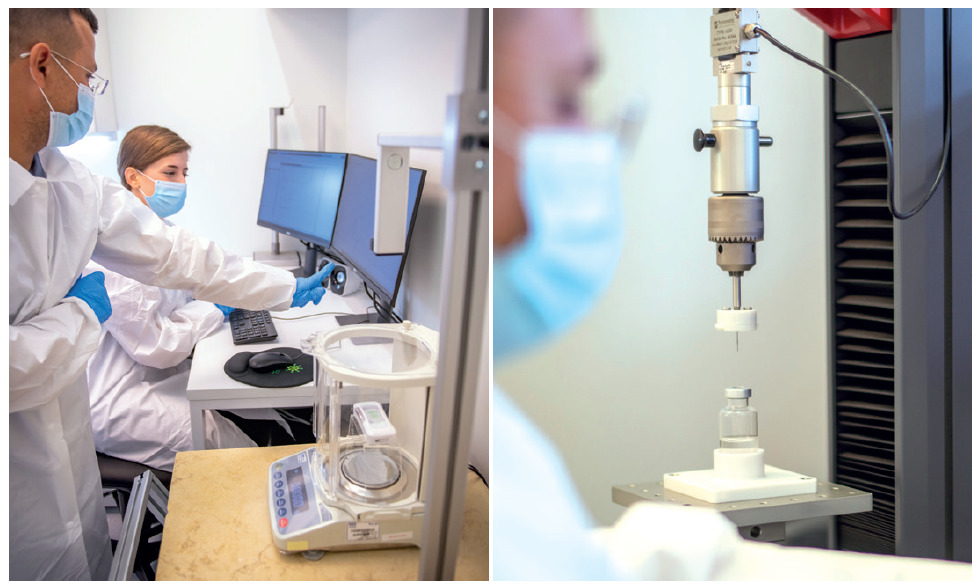
Figure 4: Sorrel testing of new primary containers in process.
Hold-up volumes of both vial and cartridge primary containers are measured alongside the dead volume within needles to provide an overall understanding of the hold-up volume of the entire wearable system. This allows for primary container fill volumes to be further adjusted as needed to guarantee optimal performance.
To overcome the inherent challenge of maintaining sterility in preloaded devices, the Sorrel devices use UV-C LED technology for disinfection at the point of care, disinfecting the point of engagement between the primary container and the device’s fluid path. Intensive UV disinfection validations are therefore performed on every rubber septum to conform to the six-log bacteria reduction as stipulated by the US FDA for low-level disinfection.
THREE-WAY COLLABORATION FROM THE OUTSET
The collaboration between Eitan Medical and Stevanato Group has resulted in the ability to offer a full portfolio of subcutaneous wearable drug delivery solutions, in both vial and cartridge configurations and across a range of different sizes, that are able to meet any drug development phase, from preclinical studies to lifecycle management, and can be easily adapted to the maturity of a project.
However, when looking to introduce drug delivery combination products to market, it is imperative that all participants – the device manufacturer, primary container manufacturer and drug developer – are brought into play and that collaboration is established as early in the process as possible. As activities are often intertwined, early engagement will ensure that interdependencies are considered, and timelines aligned to streamline the entire process. This early co-operation can thus expedite the introduction of new drug delivery systems for the benefit of all parties – the device manufacturer, container provider, pharmaceutical developer and, ultimately and most importantly, the patient.
* Q Core Medical Ltd is the legal manufacturer of the Sapphire infusion pump.
**Sorrel Medical Ltd is the legal manufacturer of the Sorrel wearable drug delivery platform (FDA investigational device).
***Avoset devices are currently under development.