To Issue 129
Citation: Deutsch M, Merhige J, “Taking Integrated Needle Safety Systems for Prefilled Syringes to the Next Level”. ONdrugDelivery Issue 129 (Feb 2022), pp 47–51.
Michelle Deutsch and John Merhige discuss the needle safety requirements of prefilled syringes and consider how SCHOTT TOPPAC® and syriQ® PFS with Credence Companion® technology combine to meet these challenges, while ensuring the device meets sustainability demands.
“Multidose vials, commodity syringes and user-activated needle safety devices offer the first level of protection and usability, while single-dose, PFSs and passive safety devices represent a step- change in safety, convenience and flexibility.”
Needle safety and usability is a greater challenge than ever for new types of medication in new types of surroundings. Today’s mass vaccination programmes highlight the increasing importance of needle safety and enhanced usability in drug delivery systems. Enabling both successful dose delivery and protection from sharps injuries is critical.
Multidose vials, commodity syringes and user-activated needle safety devices offer the first level of protection and usability, while single-dose, prefilled syringes (PFSs) and passive safety devices represent a step-change in safety, convenience and flexibility. Additionally, a superior PFS safety device should feature easy integration with fill-finish lines and environmental sustainability. User-centric design and an awareness of the complex issues facing modern pharmaceutical manufacturers are key to the successful delivery of such solutions.
PARTNERING TO ADDRESS THE CHALLENGE: SCHOTT AND CREDENCE
SCHOTT and Credence MedSystems have collaborated to meet today’s stringent requirements for safety and usability. SCHOTT’s technological expertise in glass and polymer primary packaging, combined with Credence’s award-winning innovation talents, have combined to create an integrated PFS system that closes the gaps in existing offerings and opens up new possibilities in flexibility, convenience and usability. The integration of SCHOTT and Credence products and competencies has enabled a broad choice of PFS safety options – materials, components, design options – with expert support.
THE CHALLENGES IN DETAIL
“The right approach should improve the shortcomings of today’s traditional safety syringes while also offering advantages in usability and sustainability.”
The US Needlestick Safety and Prevention Act was passed in 2000, when it was estimated that over 600,000 needlestick injuries occurred in the US alone.1 In 2010, an EU mandate addressed the danger of accidental sharps injuries with legislation on the issue, coming into force from 2013. In 2011, ISO 23908 was created to set out test methods and performance parameters for evaluating the performance of sharps injury protection devices.
Today, with user injury rates continuing to be much higher from active compared with passive safety devices,² it is hardly surprising that authorities have demonstrated a strong preference for passive safety devices. New vaccines are coming onto the market, the move to home-based care continues and more dual chamber applications are entering the pipeline. The need to accelerate the move to patient and user needle safety has never been clearer. PFSs and passive safety devices are the obvious solution.
Given the pressing need, it is not surprising that conventional “add-on” safety devices are being challenged by “integrated” alternatives, where the safety mechanism is incorporated into the syringe before delivery to the fill-finish suite. However, as new technologies are developed to address the shortcomings of conventional approaches, usability must be enhanced rather than hindered.
Premature activation of the safety mechanism can be a recurring failure mode in both traditional and recently introduced developmental safety systems. This is a significant disadvantage because once activated during transport or use, the syringe is no longer able to inject the drug, leading to the waste of potentially costly and scarce medications. Activation failures and limitations on the angle of injection are other drawbacks associated with some needle safety mechanisms.
The right approach should improve the shortcomings of today’s traditional safety syringes while also offering advantages in usability and sustainability. Additionally, it is critical to identify an approach that is flexible enough to support full drug platforms as well as the needs of specific drugs.
“Companion® incorporates different cues to support a user-friendly experience. In addition to an audible click marker, tactile and visual indicators combine to mark the end-of-dose and the needle safety.”
CREDENCE COMPANION®: COMBINING ENHANCED SAFETY AND USABILITY WITH OPERATIONAL EFFICIENCY
The Companion® safety syringe system has been developed to overcome challenges with both existing and in-development approaches, as well as to offer enhanced safety and usability features, while benefitting from compatibility with existing PFSs and other primary package components. Its performance robustness has been demonstrated in rigorous evaluations and customer assessments, including, among other verification activities, drop testing and retraction reliability studies (Figure 1).
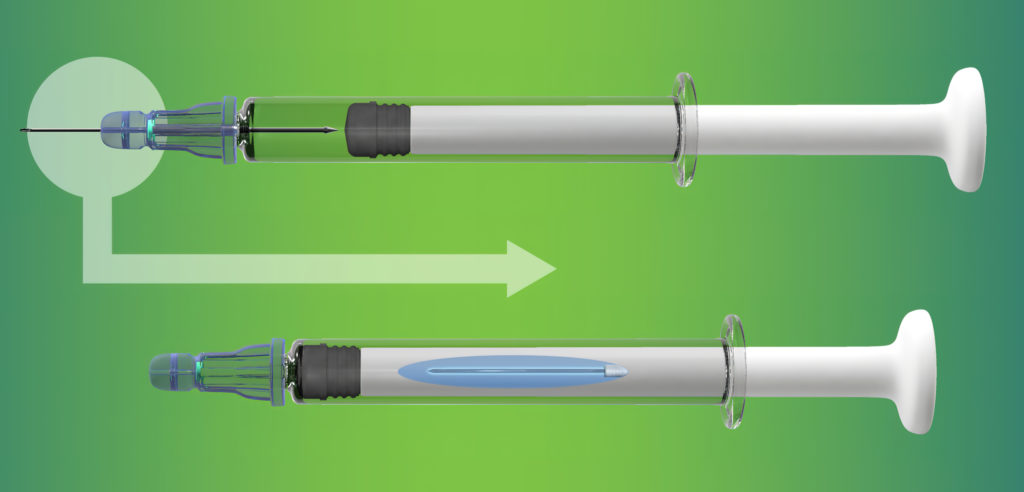
Figure 1: At the end the injection, the user receives an audible and tactile cue that the dose has been delivered, the needle has been retracted into the plunger rod and the syringe is prevented from re-use.
Companion® incorporates different cues to support a user-friendly experience. In addition to an audible click marker, tactile and visual indicators combine to mark the end-of-dose and the needle safety. In conventional approaches, complex external structures can obscure the view of the syringe, but Companion® features a streamlined design that provides a clear view of the syringe barrel and drug product. This has the advantages of allowing users to perform the common syringe techniques that Companion® supports – air bubble purging and aspiration – and confirm full drug delivery and needle retraction. Both customer-sponsored and Credence’s own human factors testing has consistently shown a higher user preference for Companion® compared with alternative approaches.
Besides these usability advantages, a design that eliminates the complex add-on structure delivers further advantages in fill-finish processing. Companion® is compatible with existing nest and tub configurations, allowing for high-speed processing through fill-finish lines. Additional production steps and scrap associated with the mounting of conventional add-on devices can be eliminated, offering pharmaceutical manufacturers the opportunity to innovate and implement more efficient equipment configurations and processing flows.
While Companion® therefore has the advantage of supporting industry-standard processing, packaging and equipment, it also incorporates its own value associated with the control of undesirable added residuals. Its needle assembly is mounted on standard glass and polymer syringe barrels without the use of glue, removing an unwanted material. Tungsten-free and stainless steel-free options are also available. Superior fit with the existing fill-finish landscape, the ability to integrate with a broad portfolio of PFSs and critical differentiating features combine to make Credence Companion® the ideal safety device for SCHOTT PFSs (Figure 2).
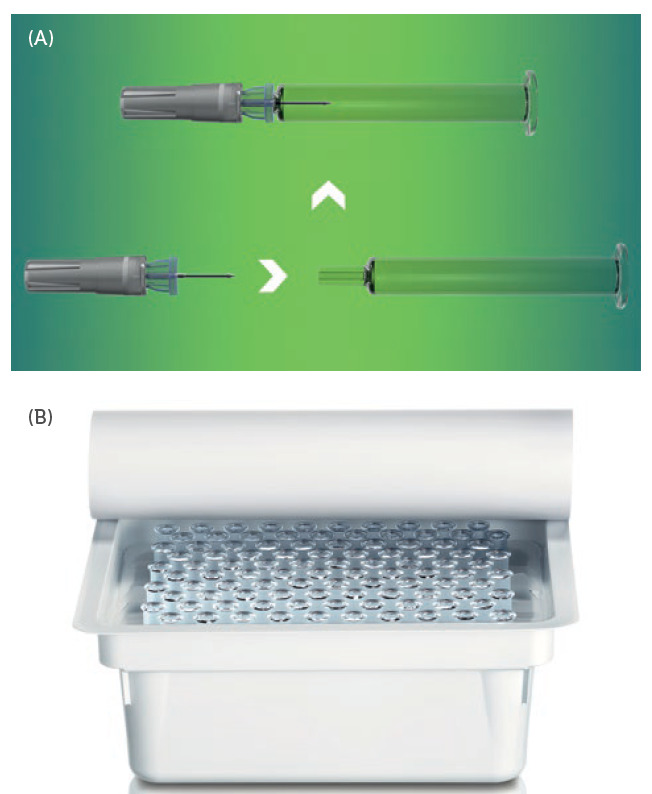
Figure 2: The Companion® needle assembly is integrated with SCHOTT PFSs (A) and
delivered to the filling suite in the preferred presterilised nest and tub configuration
ready for filling (B).
“The advantages of Credence Companion® combined with syriQ® glass and SCHOTT TOPPAC® polymer prefillable syringes create a powerful primary packaging value proposition, taking the safety and usability of injectables administration to the next level.”
syriQ® AND SCHOTT TOPPAC® SYRINGES: PROVEN SOLUTIONS
An industry leader in pharmaceutical packaging, SCHOTT offers customers a choice of PFS to meet the needs of drugs across a range of market segments. syriQ® glass syringes and SCHOTT TOPPAC® prefillable syringes made of cyclic olefin copolymer (COC) can be found in traditional and modern vaccines, sensitive biologics, cosmetics and intravenous applications in homecare, clinical, hospital and operating room settings across the world. SCHOTT PFSs are at the forefront of cutting-edge vaccine programmes and biologic drug delivery. The engineering teams behind this work lead the way in applying packaging science to solving the human health challenges of today.
syriQ®
The full syriQ® portfolio offers all the advantages of SCHOTT FIOLAX® glass tubing, with the FIOLAX® Controlled Hydrolytic Resistance syringe barrel option offering additional resistance against leachables and the attack of aggressive buffers. Ultra-low tungsten options prevent potential protein agglomeration in sensitive drugs.
Homogeneous low-silicone layers applied with state-of-the-art diving nozzle technology ensure that break-loose gliding forces remain consistent over the ageing process for a range of plunger stoppers. Ongoing particulate reduction programmes and major investments in new washing lines and camera inspection systems have supported increasingly tighter acceptance quality limits across the full syriQ® portfolio. syriQ® is bolstered by multiple suppliers for raw materials and access to world-class internal materials expertise gained across a range of glass product lines.
The advantages of Credence Companion® combined with syriQ® glass and SCHOTT TOPPAC® polymer prefillable syringes create a powerful primary packaging value proposition, taking the safety and usability of injectables administration to the next level.
SCHOTT TOPPAC®
Rapidly gaining acceptance in new market segments, polymer PFSs have long been a staple in applications demanding a PFS in sizes and configurations less suitable to glass syringes. Polymer syringes have also stood out for their specific advantages when delivering highly viscous injectables and their regulatory acceptance in intravenous drug delivery.
The manufacturing process for COC PFSs generates no heavy metals and requires no adhesives, resulting in a product that contains no tungsten, guarantees no ion leaching and maintains a consistent product pH over time. SCHOTT TOPPAC® syringes feature silicone-free oil. Like the syriQ® portfolio, they are verified with a choice of plunger stoppers. SCHOTT TOPPAC® syringes support different sterilisation modalities – gamma, e-beam and X-ray – and their COC material lends itself to highly flexible design.
The combination of SCHOTT TOPPAC® and Companion® technology is a breakthrough – the first prefillable syringe made of COC to be commercially available with a staked needle and integrated passive safety device. With this comes the important potential benefit of extending sharps injury protection to user populations in a wider range of applications. An additional breakthrough stemming from this combination of leading technologies is evident in applications requiring point-of-care reconstitution of large volume pharmaceuticals. Integrating the Credence Dual Chamber Reconstitution technology with larger SCHOTT TOPPAC® barrels (e.g. 10 and 20 mL) results in a safe and convenient method to reconstitute and deliver large volumes, and leverages the weight and break-resistance of polymer syringes.
THE FREEDOM TO CHOOSE WITH CONFIDENCE AND SUSTAINABILITY
Credence Companion® and SCHOTT syringes will be integrated using a flexible approach that can support a wide range of drugs, administration routes and patient populations. A versatile portfolio of prefilled safety syringes is planned to support syriQ® glass syringes from 0.5 to 3 mL and SCHOTT TOPPAC® polymer syringes from 0.8 to 20 mL, with needles for either glass or polymer from 22 to 32G including both 1/2 and 5/8th needle lengths. The system will also lend itself to adaptation for autoinjector use.
The Credence Companion® and SCHOTT prefilled safety syringes will use familiar, existing components and materials – glass, polymer, siliconisation technologies and closure components – already used in standard syriQ®, syriQ BioPure® glass and SCHOTT TOPPAC® polymer syringes, reducing the burden of change management. As well as existing syringe components and materials, the integrated Companion® and SCHOTT syringe safety system will also be built around existing packaging and equipment, working seamlessly with industry-standard SCHOTT syringe nests and tubs and supporting easy integration with existing fill-finish lines. Familiar tubs containing the nested safety syringe will be delivered to the fill-finish site together with plunger rods to complete the assembly following a standard manufacturing and supply chain flows. Equipment changes will not be required to process the Companion® PFS.
The streamlined, flexible design of Companion® results in an environmental footprint that approximates that of a standard “naked” PFS and is a significant improvement compared with conventional add-on systems. Compared with a leading add-on safety syringe system, Companion® reduces the weight of added components by 58%, uses 38% of the plastic, occupies 47% of the volume pre-use and occupies 33% of the volume post-use, according to an internal Credence study (ENG-0141). Lighter, smaller and using less plastic, the Companion® system can provide pharmaceutical manufacturers with sustainability and cost advantages; the integrated Companion® and SCHOTT syringe can reduce the burden on in-plant material processing, the size of secondary packaging, cost of shipping and space needed in cold storage (Table 1).
Sustainability Category | Advantage of Companion® Compared with Leading Add-On Device |
Weight of Added Components* | Weight of added components reduced by 58% |
Polymer/Plastic Consumption | Weight of Polymer/Plastic used reduced by 62% |
Pre-Use Volume Occupied by Device | 3D Footprint reduced by 53% |
Post-Use Volume Occupied by Device | 3D Footprint reduced by 67% |
*Incremental to baseline syringe, stopper and needle shield
Table 1: Companion® sustainability advantages: 1 mL long syringe (Credence internal study ENG-0141)
SCHOTT PFS, integrated with Companion® technology, minimises disruption to existing injectables manufacturing and supply chain flows, allowing pharmaceutical manufacturers to innovate without the burden of significant change management, resulting in a more environmentally sustainable safety syringe option.
UPGRADING INTEGRATED SAFETY SYSTEMS TO THE NEXT LEVEL
Integrated safety systems have a vital part to play in preventing sharps injuries and supporting positive clinical use experiences. They also offer important opportunities for drug lifecycle management and product differentiation. Choosing the right safety system, especially for multiple drugs or an enterprise platform, is not a trivial decision. Reliable partners, ease of integration, environmental sustainability and a product that offers the flexibility to support a wide range of different drugs are all critical selection criteria. The integrated Companion® and SCHOTT syringe safety system (Figure 3) can deliver all of these advantages, from stability testing through launch, with a range of creative, versatile formats and with the assurance of SCHOTT as a full system supplier.

Figure 3: Credence Companion® on SCHOTT prefilled 1 mL long syringe.
REFERENCES
- “CDC urges caution to reduce workplace needlestick injuries”. Press Release, US Centers for Disease Control and Prevention, November 23, 1999.
- Healthcare Policy Canada study, 2011–2013 data.