To Issue 136
Citation: Abildgaard O, Berninger-Lund S, “Embracing Opportunities Presented by Digitalisation: Using Data to Drive Performance”. ONdrugDelivery, Issue 136 (Aug 2022), pp 18–21.
Otto Abildgaard and Sebastian Berninger-Lund review the four-stage process Stevanato has developed to bring improvements in time to market through optimised manufacturing. They present how machine design and assembly is being enhanced through developments such as the digital twin and discuss how the collection and use of data throughout the manufacturing process can drive improved performance.
“Organisations must embed smarter thinking throughout their business and couple it with continued investment in innovative technologies.”
As an industry, pharma is renowned for innovation, responsiveness to unmet needs and a determination to continuously improve. Whether it is the development of more personalised drugs to treat complex diseases or the implementation of connected devices to track and improve patient adherence, many recent advances have come from greater insight supported by data. Nowhere is this striving for improvement seen more than in device manufacturing, where the momentum for more rapid deployment of products through the digitisation of manufacturing is gathering real pace (Figure 1).
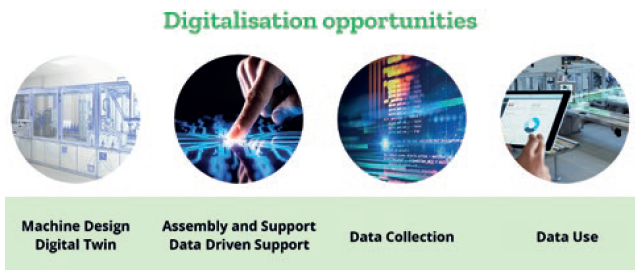
Figure 1: Harnessing digitalisation for a new era of pharma manufacturing.
Across all sectors, healthcare and pharma included, covid-19 has accelerated underlying digital change. In doing so, it has accelerated the pace of business, with research from global consulting firm McKinsey & Company suggesting that business practices considered best-in-class in 2018 would today be regarded as slower than average.1
To achieve the higher levels of operational agility now required to sustain competitive advantage, organisations must embed smarter thinking throughout their business and couple it with continued investment in innovative technologies. Harnessed correctly and used in the right way, such technologies have the potential to enhance accuracy, efficiency and productivity while limiting risks and costs.
At Stevanato Group, the potential of technology to advance pharmaceutical manufacturing environments is a key focus. While this incorporates the digitisation of individual activities and specific processes, there is an opportunity for stakeholders to collaborate and innovate together on a more fundamental transition to digitally integrated environments, where continual improvements are fuelled by the systematic capture and purposeful analysis of relevant data.
The company is developing a four-stage framework to support its pharmaceutical partners in realising this transformation, resulting in manufacturing processes and workflows that are digitally optimised. This framework can help achieve gains in operational performance while sustaining consistency of product quality, minimising demands on resources and avoiding costly disruption.
The first element of the framework relates to machine design, where a digitally led approach can be used to simplify and derisk the journey from prototyping to the point at which components and equipment are engineered into existence. The focus here is on exploiting all the advantages afforded by a virtual environment by developing a digital twin of the machine. This combines physical computer-aided design (CAD) with machine behaviour – using a programmable logic controller (PLC) – enabling iterations to be made quickly and cost effectively before the transition is made to three-dimensional (3D) reality.
“Continual improvements are fuelled by the systematic capture and purposeful analysis of relevant data.”
The digital twin technology creates a copy of the machine, precisely mirroring within a digital environment what can be expected of the physical version. This means that process optimisation can be incorporated into the design phase, where new developments on a machine are tested and validated before they are manufactured. This has the benefit of accelerating implementation and reducing potential disruption, since component and software changes can be validated virtually in parallel with the actual machine. This approach reduces the likelihood of iterative real-world developments and therefore reduces waste in terms of materials and time. All the while, machine owners are left with a comprehensive digital record of their equipment that can also be employed as a platform for virtual training.
The second element of the Stevanato Group framework encompasses the digitisation of machine assemblies. This involves using high-definition cameras to record in critical detail the machinery within an entire assembly line at the point at which it is validated on the shopfloor. From these source images, an accurate 3D model of the set-up can be rendered using CAD software and, because the virtual image is a precise replica of the delivered system, it can be cross-referenced against a digital “blueprint” to interrogate and highlight any discrepancies between the two.
This process is conducted using an on-screen, colour-coded “heat map” that visualises any deviations and highlights where attention might be required. At a component level, it will show, for example, areas of wear and tear that might have an influence on performance. On high-performance production units, such deviations can impact a machine’s productivity but are too subtle to be detected via manual inspection. By digitising the machinery, however, issues can be identified, diagnosed and corrected through interactive remote analysis, speeding up the process and minimising downtime while ensuring consistency of quality is maintained and failure rates are kept to a minimum.
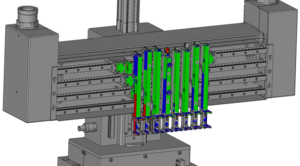
Figure 2: Colour-coded “heat map” indicating where to pay attention, based on any deviations.
In Figure 2, the parts with blue marking should be adjusted inwards by the assembly engineer and areas with a red marking should be adjusted outwards for ideal operation of the equipment module.
Knowing that the machine is designed, assembled and performing correctly as a result of the first two stages, the focus is then on the area of digital surveillance and the collection of data from various operational phases, including running-in, factory acceptance testing, site acceptance testing and production. Subsequently, the collected data can be used and analysed for continual improvement.
Regarding collection – the third stage – Stevanato Group can facilitate high-level data capture through data monitoring and measuring. The data-collection platform has been designed on the principles of compatibility and interoperability to ensure it can be integrated with equipment from any major supplier – not just Stevanato Group’s own machinery – and with software interfaces provided by third-party providers across the market.
The data-collection platform conforms to the rule of “garbage in, garbage out” – if the data capture and recording process is not performed at the highest level, then its usefulness will necessarily be diminished. It follows, therefore, that enabling the collection of item-level, batch-traceable, high-integrity data at a superior sampling rate allows the insights derived – and their resultant value – to be significantly enhanced.
Typically, there are a variety of hurdles to establishing a framework and process for the collection of such data. The platform addresses many of the key challenges here, with no additional coding required inside the process code, and the advanced filter set-up ensures only data of value is captured at a high sampling rate of each PLC scan, with item-level traceability to inform diagnostic activity. The vendor-agnostic nature of the data-collection platform also means that the end user does not require multiple suppliers to manage and maintain a series of separate data interfaces – nor are they burdened with creating such interfaces in-house. In this way, it creates a unified interface for end users in the pharma industry, simplifying IT systems and, therefore, reducing ongoing maintenance requirements. Simultaneously, machine builders are provided with access to a broad range of data interfaces, databases and analytics without investing in internal competences.
Value creation by data analytics and visualisation occurs in this final stage, which is predicated on creating meaningful, actionable insight from the collected data. To achieve this, it is essential for the data not to be considered as an abstract asset, held away from the organisation, but rather for it to be “plugged in” at an operational level and made available to people in specific roles who can act upon it accordingly.
Operators, for example, can create maximum value if they are provided with immediate feedback from equipment in a live setting. Maintenance teams, meanwhile, are seeking underlying machine operation data provided over a period of time to feed into root cause analysis and long-term optimisation strategies. Line managers will require different datasets or analysis patterns to assess trends in shopfloor operations, while quality managers will benefit from insight into the components sourced from providers across the supply chain.
Sifting through a continuously generated “fire hose” of production data to arrive at these various tailored insights makes for a challenging task. However, this task can be simplified by translating the acquired data into dynamic, 3D visualisations accessed via a dashboard, giving users at all levels access to the information they need in a digestible, graphical form (Figure 3).
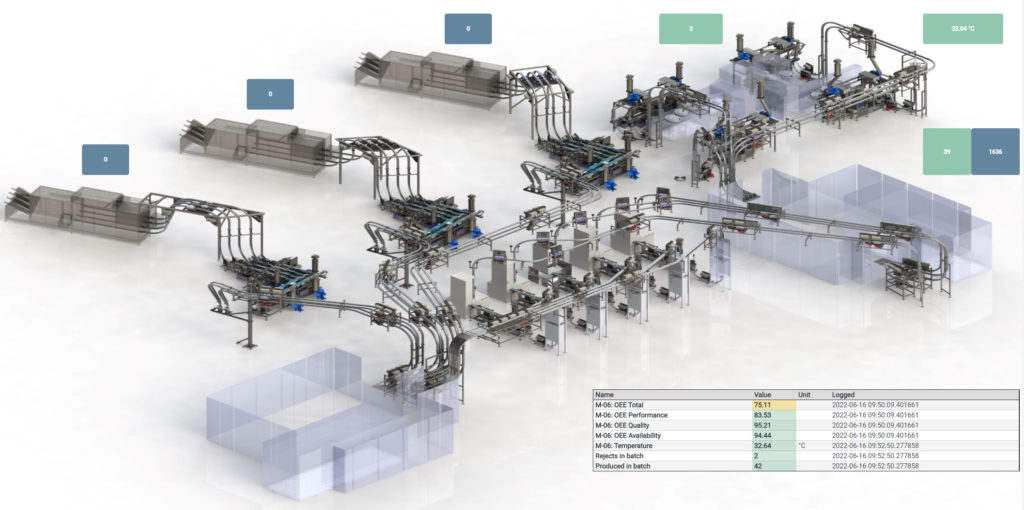
Figure 3: Real-time tracking of markers through 3D visualisation.
This provides operators with access to near-real-time tracking of markers such as temperature and process speed, while those with a focus on longer-term performance can track machine-level issues over time to inform iterative improvements. As such, it neatly dovetails with the Six Sigma approach adopted within many manufacturing environments to sustain quality of performance and limit defects, as measured by process capability index (Cpk) values.
Traceability adds an important layer of value in these circumstances because data values are associated with recorded imagery that can act as reference evidence. Video feeds from the constant surveillance tools used on production lines, for example, can be accessed where deviations are highlighted, presenting an opportunity for deeper analysis.
This example highlights the interlinked nature of truly digital systems, and the benefits that can be realised when the thread of digital thinking is embedded throughout all stages of the production chain, from design and operation to support and performance analysis. As an enabler within this chain, Stevanato Group integrates at whatever point its tools and equipment can be employed to optimise certain processes or functions. For some partners, this will mean an exclusive focus on the collection of data that can be digested and interpreted within their own systems, while others will take advantage of associated stages of the Stevanato Group offering to support engineering design or facilitate data analysis.
This open, integrated alignment of capabilities among partners is fundamental to the digital philosophy that pharmaceutical companies must adopt for their operations to adapt quickly to the production challenges associated with rapidly deploying new products to market. Under these intensified conditions, where defects and deviations from a desired target can extend timeframes and costs exponentially, the answers to sustained performance enhancement will exist within the data. Uncovering them is not simply a case of data gathering but, rather, ensuring that systems are designed to manage the flow, capture and analysis of high-volume, high-integrity data, and then making it come alive in the eyes of the individual who can act upon it.
REFERENCES
- “The new digital edge: Rethinking strategy for the postpandemic era”. Survey, McKinsey & Company, May 26, 2021.