To Issue 138
Citation: Canner J, “Developing, Manufacturing and Delivering a Fill-Finish Pilot Line for Tub-Based Prefilled Syringes”. ONdrugDelivery, Issue 138 (Oct 2022), pp 92–94.
Jake Canner discusses the latest project arising out of 3P innovation’s partnership with Cambridge Pharma and its sister company Oval Medical Technologies – including the challenges involved and how they were overcome.
The task facing 3P innovation was to develop a custom automated nest-based filling line for fill-finish of a bespoke primary drug container (PDC) with a suspension formulation, for later assembly into an autoinjector. Cambridge Pharma needed a fully aseptic filling and proprietary closure system, aligning with developed and pre-approved clinical processes.
The device had been developed by Cambridge Pharma’s sister company Oval Medical Technologies and included a unique PDC design using cyclic olefin copolymer (COC). Oval’s proprietary PDCs offer a wide range of benefits over traditional glass-based systems. The use of COC allows for much greater design flexibility, and the creation of more robust containers, whilst also allowing the removal of materials that could potentially interact with the drug.
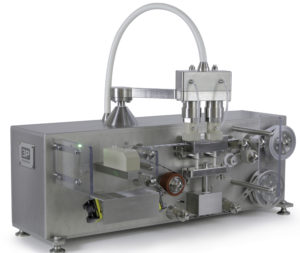
Figure 1: Oval Medical’s clinical foil sealing machine.
3P innovation has worked with Oval Medical in the past to help with the development of automation equipment for the sterile closure process of its COC containers on a clinical scale (Figure 1). This project was a scale-up project incorporating those processes.
Cambridge Pharma specialises in small-batch sterile fill-finish operations for a range of presentations including vials, syringes and cartridges, as well as custom PDCs. The company’s state-of-the-art GMP facility is equipped to work with small molecules, cytotoxic formulations and large molecules (non-active biologics), and can handle a wide range of solution viscosities, suspensions and gels.
3P innovation was commissioned to design a nest-based system, able to handle the specialist COC containers and fill them with a suspension formulation. Amongst other requirements, there was a need for 100% in-process fill weight checking, vacuum plunger insertion, the addition of a spacer component for variation of fills – and Oval Medical’s proprietary container closure. One key differentiator from previous work was the requirement for processing multiple containers in parallel, in order to hit throughput requirements. Handling products “in nest” allowed for higher speed parallel processing and, more critically, a vast reduction in operator interactions with the product itself – therefore improving the sterility assurance of the process.
PROJECT CHALLENGES
Limited Footprint
The machine was designed to go into a bespoke cleanroom, where floor space is always at a premium. Inside the machine, products are handled, filled and closed in their nest. This potentially requires more space than processing containers individually, but there is better control compared with a system requiring more interventions, yielding a significant reduction in contamination risk.
3P innovation worked to design a novel system for handling nests so that the machine would have enough working travel to be able to process nests but be sufficiently compact so that it would not take up a lot of space. Using the principles of a five-bar linkage, the company was able to design a sterile-compatible nest-handling robot that turns a pair of axis rotations into parallel, cartesian motion of the payload.
Avoiding Wetted Parts and Reducing Cleaning Times and Costs
Cambridge Pharma wanted to use single-use system components where possible, to speed up changeover and cleaning of the equipment. So 3P innovation incorporated peristaltic pumps in its design, which meant that only the filling lines and needles would be in contact with the liquid drug. These must be disposed of after every batch but make for a significant reduction in cleaning between batches, helping to reduce both changeover times and cleaning requirements.
Liquid Filling of a Suspension Drug
Liquid filling of a suspension drug presented a couple of challenges – the first one being the dose size and accuracy required and the second being the nature of the formulation. Cambridge Pharma needed two different dose volumes (1 and 1.4 mL) with 1% accuracy. Each dose is check-weighed, and the dosing system operates a closed-loop trend correction algorithm to account for any variations in the formulation over the course of a batch. For more homogenous liquids, the machine can also be configured for a lower-resolution “per-nest” check, allowing for increased process speed.
Colour Vision Sensor
The spacer components allow Cambridge Pharma to achieve variable fill volumes within the same PDC body. The spacers are a coloured device component, where the colour is specific to the spacer length and, consequently, the dose in the container. To ensure the correct match of component to dose, 3P innovation worked with the customer to incorporate a colour vision sensor to check for the presence and position of the correct spacer, based on the target fill volumes at the point of batch set-up and recipe selection. This is a cost-effective solution compared with a full vision system.
Grade A Environment
When it came to the general handling of the open COC containers, 3P innovation had to consider the internal layout of an isolator to manage the grade A environment. The pilot line’s design aims to reduce the risk of any particulates generated during processing migrating over to the open product – and the risk of the PDCs being exposed to “first-air” throughout processing (Figure 2). To this end, the closure process step – the punching of foil discs for induction sealing – was physically separated from the open product by a solid wall. In addition, the decision was taken to separate the liquid filling from the foil punch-and-seal in a wholly separate isolator chamber to ensure isolation of the highest risk step within the filling chamber.
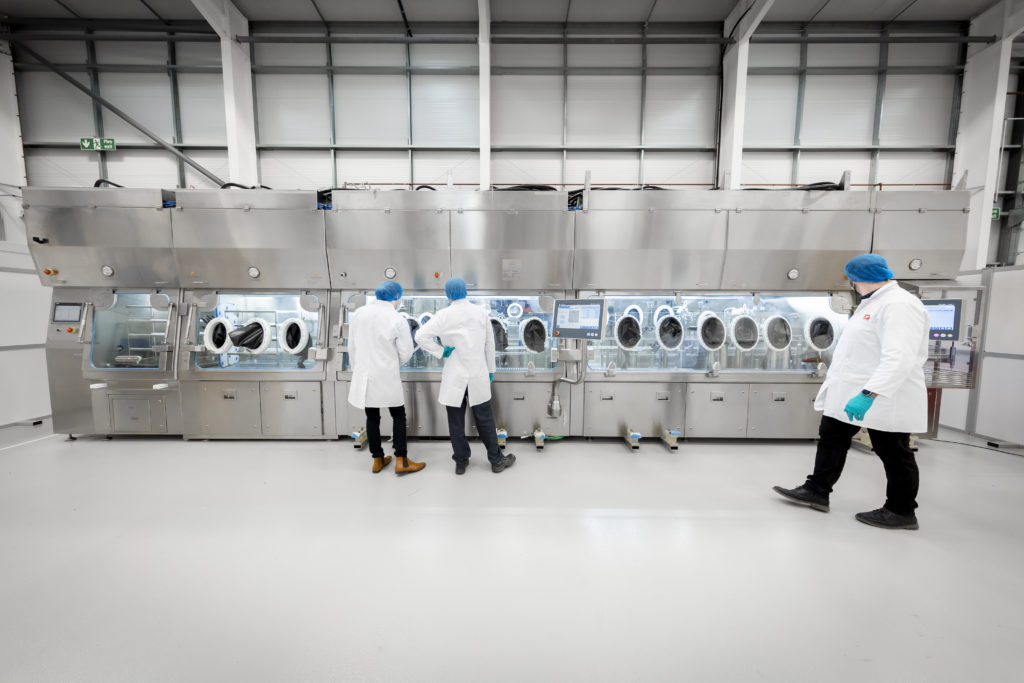
Figure 2: 3P innovation engineers working on the pilot line.
Validated Process
As the pilot line was required to manufacture sterile parenteral products, 3P innovation worked with Cambridge Pharma from the outset on the validation approach. Existing, validated, clinical processes were referenced and reused to de-risk the validation steps throughout the development process. This added a number of design constraints that were identified right at the start of the project and followed through the validation lifecycle.
Reject Handling
In order to achieve required cycle times, certain machine processes included up to four containers at once. 3P innovation had to design an intelligent way of handling rejected products that minimised the impact on the containers with no flagged errors. The pilot line’s reject strategy is configured such that it will always try to maximise good products (Figure 3). The system tracks rejects at a PDC level, despite generally processing at a nest level. This means that the machine is capable of selecting which process stations can be bypassed or used based on the individual PDCs presented each cycle.
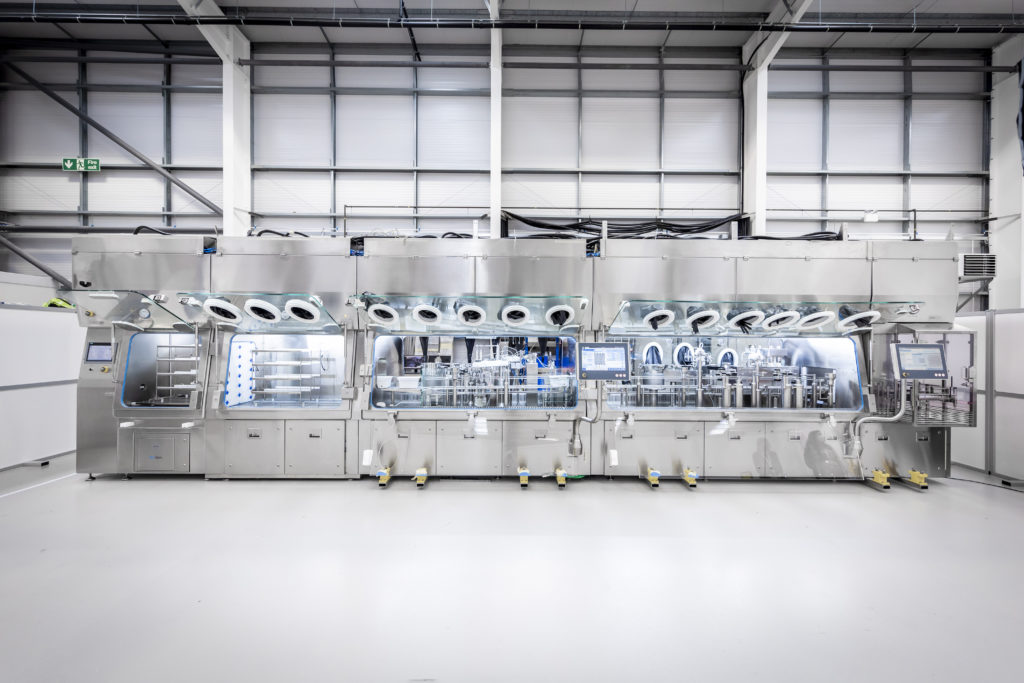
Figure 3: Cambridge Pharma’s fill-finish pilot line.
After the process equipment was built and acceptance tested at 3P innovation’s facility in Warwick, UK, it was integrated into a sterility isolator provided by Howorth Air Technology (Bolton, UK). The response from Cambridge Pharma at the end of the project was that, despite the rigorous nature of the sterile process requirements and tight timescales, 3P innovation rose to the challenge of developing,
manufacturing and delivering the line to meet its needs.