Citation: Lavin A, “Benefits of Innovative Compressed Gas-Powered Intranasal Drug Delivery Devices”. ONdrugDelivery, Issue 154 (Nov 2023), pp 66–70.
Albie Lavin discusses the exciting potential of propellant-driven systems for intranasal delivery, and how Picocyl’s Pico-Cylinders provide the ideal mechanism to take advantage of this potential.
GROWING SHIFT FROM PARENTERAL TO INTRANASAL DELIVERY
Many existing molecules that are currently marketed for oral or intramuscular delivery are finding alternative applications in the intranasal space. Intranasal drug delivery has the potential to combine the non-invasive, patient friendly delivery of oral tablets or capsules with the rapid pharmacokinetic absorption profile of intramuscular injections.
Furthermore, there is potential for new drug formulations to benefit from innovations in intranasal drug delivery that enable direct nose-to-brain absorption pathways or more efficient systemic uptake. Many developing therapies in the central nervous system (CNS) and nasal vaccine spaces are harnessing these advances in delivery technology, and, as a result, the intranasal drug delivery sector is poised to experience significant growth over the next decade.
“The Pico-Cylinder was developed to provide handheld devices with a drive system that can deliver precise primary drug container force profiles for a wide variety of applications and liquid viscosities.”
CURRENT STATE OF INTRANASAL DRUG DELIVERY TECHNOLOGY
The current landscape for intranasal drug delivery technology includes five different types of delivery device (Table 1):
- Pump-driven liquid reservoir systems for liquid formulations and suspensions
- Prefilled syringe-driven systems for liquid formulations and suspensions
- Hand-actuated piston-driven systems for liquid and dry powder formulations
- Breath-actuated systems for liquid and dry powder formulations
- Propellant-driven systems for liquid and dry powder formulations.
Drive System | Devices | Manufacturers | Formulation Types | Marketed Products |
Pump | ![]() |
Aptar Pharma, Nemera | Liquid, Suspensions | Many |
Prefilled Syringe | ![]() |
Aptar Pharma, Nipro, Teleflex | Liquid, Suspensions | Many |
Hand-Actuated Piston | ![]() |
Aptar Pharma, Nemera, Janssen | Liquid, Suspensions, Dry Powder |
Narcan, Spravato |
Breath-Actuated | ![]() |
Optinose | Liquid, Suspensions, Dry Powder |
Xhance, Xsail |
Propellant | ![]() |
Impel | Liquid, Suspensions, Dry Powder |
Trudhesa |
Table 1: Current landscape of intranasal drug delivery devices.
The use of propellants to drive nasal drug delivery can result in significant improvements in spray performance and consistency over pump-driven and hand-actuated systems, which can have variable dose delivery and spray characteristics depending on how hard or soft the user squeezes the device. However, propellant-driven systems typically require a constant trip force to release the propellant (which is what the user feels), after which the energy released by the propellant is metered by either a valve in the device or the mass of propellant filled during the manufacturing process. Therefore, variation in the actuation force applied by the user does not contribute to variation in the dose delivered.
Some currently marketed devices require breath co-ordination to achieve appropriate deposition inside the nasal cavity. Typical spray-pump devices require the user to breathe in and pump simultaneously, while some other devices are breath-actuated, requiring the user to inhale or exhale to generate propulsion. Propellant-driven systems can provide enough energy and particle velocity to overcome the pressure gradients created by the typical breath cycle, meaning patients do not need to co-ordinate breathing with dosing. This makes medication delivery easier for the user or caregiver.
Propellant-driven systems can also provide enough energy to deliver drug formulations into hard-to-reach areas inside the nasal cavity, specifically the olfactory region or upper nasal cavity. Intranasal delivery has also been identified as a potential nose-to-brain pathway, and an increasing number of CNS therapies are seeing success in targeting and delivering drugs to this region.1,2 The use of propellant typically provides drug particles with sufficient momentum to overcome the airflow generated by the breathing cycle, which can help to avoid losing dose down to the lungs and throat.
Currently marketed propellant-driven intranasal drug delivery systems use multi-use metered dose inhaler (MDI) canisters filled with HFA-134a to propel drug in the nasal cavity. These canisters are robust and well-studied, and there are several options available for shot-metering valves and propellant fill capacity with different manufacturing and filling partners. However, these canisters are optimised for MDIs, which are typically used on a daily basis in a controlled environment. Consequently, their features do not always align well with single-use intranasal drug delivery applications.
COMPRESSED GAS CYLINDERS ENABLE PROPELLANT-DRIVEN SINGLE-USE INTRANASAL DRUG DELIVERY
Compressed gas cylinders are a great fit for single-use spray applications. However, until recently, there have not been any compressed gas cylinders produced specifically for medical devices and combination products. Enter the Pico-Cylinder, the world’s first small-volume, single-use compressed gas cylinder manufactured in a Class 8 cleanroom. The Pico-Cylinder was developed to provide handheld devices with a drive system that can deliver precise primary drug container force profiles for a wide variety of applications and liquid viscosities.
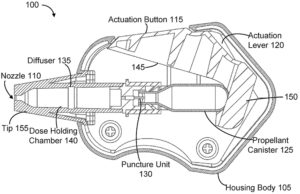
Figure 1: Impel Pharmaceuticals’ single-use nasal drug delivery device, Patent US20200360627-A1, cross-section.
Pico-Cylinders have been used in intra-ocular lens inserters, autoinjectors, gas therapy delivery systems, subretinal injectors, ingestible small intestine drug delivery capsules and, most recently, in Impel Pharmaceuticals’ (WA, US) I143 device, a single-use intranasal powder drug delivery device detailed in US patent 20200360627-A1.3 The I143 device (Figure 1) was developed to deliver spray-dried powder formulations to the upper nasal cavity to facilitate precision olfactory delivery, with the spray directly powered by the gas expelled from a Pico-Cylinder.
Pico-Cylinders are deep-drawn stainless steel containers that can be filled with both vapour-phase (N2, Ar) or dual-phase (CO2) compressed atmospheric gases at pressures from 5 to 350 bar.4 The cylinder is sealed with a proprietary stamped steel cap component with a breakaway septum that requires a secondary opening pin component to open – a Pico-Pin.5 Altaviz, a medical device design company and affiliate company to Picocyl, designed the Pico-Pin to reliably open the breakaway septum and allow for a consistent gas flow path both through and around the pin (Figure 2).
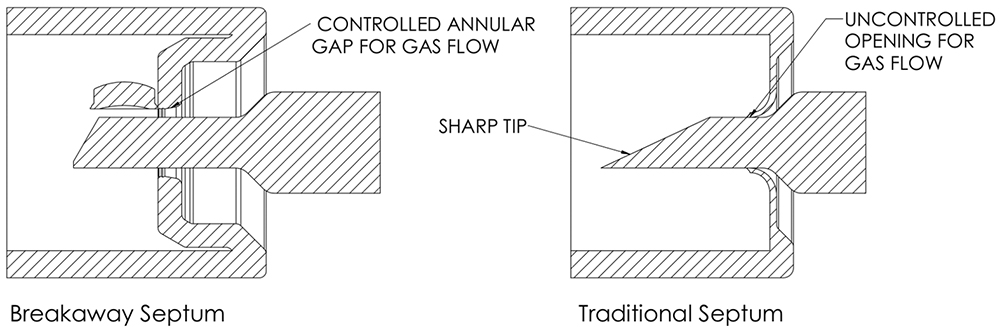
Figure 2: Proprietary breakaway septum vs traditional septum.
“Because compressed gas cylinders are single-use pressurised vessels, high reliability is imperative for enabling successful drug products.”
Traditional septum-based compressed gas cylinders use a sharp puncture to cut a flat sheet metal septum, which means that the position and puncture mechanics can be unpredictable. This can lead to gas flow issues after puncture, including cases where the punctured material covers the exit hole in the puncture pin.
Because of the Pico-Cylinder’s material selection, cylinder neck design and cap design, the Pico-Pin preferentially tears the perimeter of the septum to “open the hatch” in a controlled manner with a fourfold reduction in stroke length and a tenfold reduction in energy. This reduction in stroke length and force required to open the cylinder enables device embodiments that allow for user hand-actuation of the device without large spring-loaded systems – a unique offering in the compressed gas cylinder space.
Because compressed gas cylinders are single-use pressurised vessels, high reliability is imperative for enabling successful drug products. Cylinders must not leak over the shelf life of the combination product, and they must open consistently without any blockages. The Pico-Cylinder manufacturing process achieves this high reliability production using the following quality inspections.6
Fill Weight Verification
Each Pico-Cylinder is weighed before and after filling during the validated automated gas-filling and welding process to ensure that the correct amount of gas makes it into 100% of the cylinders.
Gross Mass and Part Identification
Each Pico-Cylinder is permanently laser-marked with its gross mass for downstream quality checks. Custom QR codes and human-readable information are possible to enable traceability throughout the manufacturing process and lifetime of the Pico-Cylinder.
Heat Conditioning
Each Pico-Cylinder undergoes a high-temperature soak to increase the internal pressure and heat stress the weld and the integrity of the components to accelerate any leaks for the subsequent leak detection process.
Leak-Free Verification Analysis
Each Pico-Cylinder is analysed for leaks using validated gas-analysis equipment. Vapour phase Ar and N2 systems are mixed with 5% He trace gas to enable inspection with an He leak detection mass spectrometer system. This provides a conservative estimate of leak rates without compromising internal pressure or gas reactivity. Dual phase CO2 gas is detected using gas chromatography and does not require any trace gas mixture.
Empty Canister Detection System
Each Pico-Cylinder is weighed to ensure that some gas was filled into the capsule. Without this step, it is possible that a leak detection system would not detect a fast-leaking part that had completely emptied prior to gas analysis.
Picocyl, the manufacturer of the Pico-Cylinder, has performed real-time leak testing out to 48 months using approximately 86 bar Ar gas with a 5% He trace gas using a sample size of 150. The maximum individual Pico-Cylinder mass loss at 48 months was 0.4 mg (<0.5% of gas fill mass), which is within the average measurement error of the scale used. This result demonstrates that the components do not leak over the typical shelf life of a combination product (Table 2).
Real Time Ageing (months) | Maximum Individual Mass Loss (mg) |
9 | 0.3 |
12 | 0.5 |
18 | 0.2 |
24 | 0.5 |
36 | 0.3 |
48 | 0.4 |
Avg scale measurement error = 0.5 mg
Table 2: Pico-Cylinder real-time leak data at four years.
“Compressed gas cylinders are filled with a tightly controlled amount of propellant that is all released at once, so the user simply needs to overcome the opening force of the cylinder to achieve consistent spray characterisation.”
COMPRESSED GAS CYLINDERS ENABLE SIGNIFICANT PERFORMANCE AND USER BENEFITS
Consistent Spray Characterisation
Typical pump-driven or hand-actuated systems are rate dependent. This can alter the velocity of the spray, which, in turn, can alter plume geometry, spray pattern or droplet size distribution from patient to patient, or even spray to spray. Compressed gas cylinders are filled with a tightly controlled amount of propellant that is all released at once, so the user simply needs to overcome the opening force of the cylinder to achieve consistent spray characterisation. This opening force is not rate-dependent, so the spray output is much more consistent across a wide range of patients.
No Priming Required
Typical pump-driven or hydrofluoroalkane (HFA) propellant-driven systems require a priming step to load liquid drug or liquid propellant into the dose chamber prior to dosing. This typically requires the device to have a drug storage chamber and a dose chamber, which makes the device larger and inevitably creates some dead volume in the flow path. This can result in wasted dose in the form of residual loss. The priming step is also typically the most common human factors error in a device’s workflow, and any extra steps in the dosing process can lead to use errors.
Compressed gas cylinders do not require priming prior to actuation, which reduces the number of required user steps and enables the reduction of drug-loading procedures. This makes compressed gas cylinders an ideal drive system for rescue applications and patient populations with impaired cognitive ability or reduced fine motor function.
Consistent, Low Actuation Force
The Pico-Cylinder is designed to have an opening force low enough to enable human actuation. This enables the use of simple levers or buttons in device design rather than requiring large springs, allowing devices to be smaller and more convenient to carry and use. Table 3 lists typical puncture force data. Typical hand-actuated devices use a 3:1 or 4:1 lever to reduce user forces down to 10–20 N.
Parameter | Lot 1 (Low Pressure) |
Lot 2 (High Pressure) |
Internal Pressure (Bar) | 55 | 180 |
Average Puncture Force (N) | 39.7 | 48.1 |
St. Dev. Puncture Force (N) | 4.4 | 7.3 |
Minimum Puncture Force (N) | 32.8 | 31.3 |
Maximum Puncture Force (N) | 51 | 60.5 |
Cpk for 80 N Maximum Puncture Force Specification |
3.08 | 1.46 |
Table 3: Pico-Cylinder puncture force data.
Separation of Propellant and Drug
Typical MDIs mix liquid propellant and liquid drug formulation inside the canister. Traditional HFA propellants can be volatile and pose drug stability or extractables and leachables issues in drug products. Compressed gas cylinders ensure that the propellant is kept separate from the drug inside the device, enabling all stability testing to be performed on the drug product alone. This can accelerate development time and allow the same device platform to support multiple drug products without requiring extensive stability testing.
Range of Stable Gas Options
Pico-Cylinders can be filled with a wide range of gases and gas fill masses to suit any application. Typical community use products will benefit most from using vapour phase atmospheric gases, such as N2 and Ar, due to their pressure consistency across temperature ranges. Across a standard community-use product temperature range of 0°C to 40°C, vapour phase gases experience a ±7% pressure shift (following the ideal gas law), while traditional dual-phase HFA-134a experiences ±77% pressure shift. Higher pressure applications can benefit from dual-phase gases, such as CO2, in a temperature-controlled environment (15°C to 25°C).
Environmentally Friendly
Pico-Cylinders do not use the HFAs that are currently used throughout the inhaled and cosmetic industries for propellants – instead, they use inert gases such as N2, Ar and CO2. They provide a solution that complies with the Kigali Amendment (2019) of the Montreal Protocol on Substances that Deplete the Ozone Layer established in 1987.7 Furthermore, gases such as N2, Ar and CO2 can be sustainably sourced and managed, making gas supply independent of worldwide chemical supply shocks, such as those experienced in the wake of the covid-19 pandemic.
CAPABILITIES OF PICO-CYLINDERS FOR INTRANASAL DRUG DELIVERY
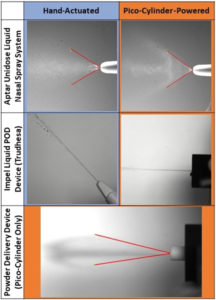
Figure 3: Plume videos from Pico-Cylinder-powered prototypes.
Pico-Cylinders can be used to achieve a wide range of spray outputs and are suitable for a range of single-use intranasal drug delivery applications. They are suitable for delivering both liquid and dry powder drug formulations. They can be used to actuate existing primary drug container mechanisms, such as cartridges, syringes and micro-vials, or to directly propel the drug formulation out of the device.
Pico-Cylinders do not limit the spray characteristics to a specific profile – they can be used to generate a wide plume with a very diffuse spray and small particle size or to generate a narrow plume with a large particle size. Altaviz has designed and built several prototype configurations of common nasal spray actuators powered by Pico-Cylinders to demonstrate these capabilities. Images taken from high-speed video illustrate how Pico-Cylinder-powered prototypes can generate similar spray characteristics to currently marketed intranasal drug delivery devices using 0.9% saline solution (Figure 3).
REFERENCES
- Hoekman J et al, “The Upper Nasal Space – A Novel Delivery Route Ideal for Central Nervous System Drugs”. US Neurol, 2020, Vol 16(1), pp 25–31.
- Shrewsbury S, Hocevar-Trnka J, Hoekman J, “Drug delivery via the upper nasal space: A novel route for anesthesiologists, intensivists and emergency department physicians?” J Clin Anesth Intensive Care, 2021, Vol 2(1), pp 8–14.
- Hoekman J et al, “Nasal drug delivery device”. US Patent US20200078544A1, 2020.
- Auld J, “Design Strategy and Considerations for Compressed Gas-Powered Device Applications“. ONdrugDelivery, Issue 138 (Oct 2022), pp 52–57.
- “Innovations – Leak-Free Gas Containment”. Company Web Page, Picocyl, accessed Oct 2023.
- “Innovations – Gas Access”. Company Web Page, Picocyl, accessed Oct 2023.
- “About Montreal Protocol”. Web Page, UN Environment Programme, accessed 2023.
Previous article
TAKING A DRUG TO FIRST-IN-HUMAN TRIALS IN A BESPOKE DEVICE FOR TARGETED INTRANASAL DELIVERYNext article
THE END OF THE ROAD FOR pMDIs?