To Issue 171
Citation: Lotz J, “Bioplastics in Drug Delivery: Getting Rid of Critical Substances and Carbon Emissions”. ONdrugDelivery, Issue 171 (Apr/May 2025), pp 36–40.
Julian Lotz introduces bio-based solutions from BIOVOX for drug delivery devices, excelling in quality while meeting upcoming sustainability regulations, and explores the future of bioplastics in the healthcare sector.
The sustainability and safety of materials is driven by four main factors. First, the sheer need to reduce the use of substances that harm human health and the environment, including the climate. Second, there is increasing regulatory pressure on human and environmental health. Third, the use of safer and more sustainable materials is a valid marketing advantage in many tenders across Europe. Finally, having no critical substances and a low carbon footprint is a mandatory risk management strategy for product risks. Ultimately, future-proof materials strengthen business. These four aspects will influence the materials selected for autoinjectors, inhalers, sprays and squeeze dispensers in the future (Figure 1).
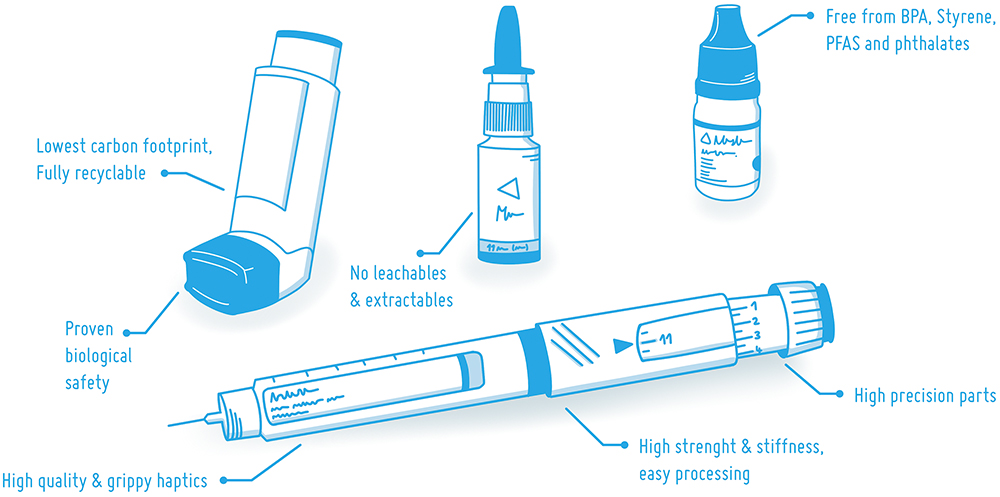
Figure 1: Medical-grade bioplastics can be used in a variety of drug delivery devices – with full safety and great sustainability.
“THE HEALTHCARE INDUSTRY CANNOT RISK DRASTIC HEALTH PROBLEMS AND IRREVERSIBLE ENVIRONMENTAL DAMAGE THAT IS, IN TURN, DETRIMENTAL TO THE HEALTH OF US ALL.”
The healthcare industry cannot risk drastic health problems and irreversible environmental damage that is, in turn, detrimental to the health of us all. The threat posed by critical substances is also being recognised by legislation, such as the EU’s Registration, Evaluation, Authorisation and Restriction of Chemicals (REACH) and the polyfluoroalkyl substances (PFAS) ban already in place in Minnesota (US), with a similar ban proposed by the European Chemicals Agency for the EU. The healthcare industry will see the phase-out of critical substances, such as ultra-persistent PFAS, or additives and monomers that act as endocrine disrupters, causing all kinds of hormone-related health problems, often affecting sexual reproduction. Examples include not only polytetrafluoroethylene (PTFE) but also PFAS-containing additives in polyethylene (PE) grades, bisphenol A in polycarbonates (PC) or phthalates such as di(2-ethylhexyl) phthalate (DEHP) used as a plasticiser in PVC, both highly critical endocrine disruptors.
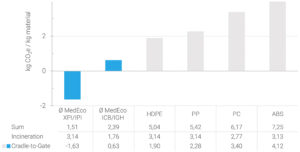
Figure 2: Carbon footprints of various plastics used in drug delivery devices.
In addition to direct health risks, plastics contribute to climate change at all stages of their lifecycle. Incineration is still the most common end-of-life scenario for drug delivery devices, thus releasing the carbon from fossil-based plastics directly into the atmosphere. Some of them, such as the PC and acrylonitrile butadiene styrene (ABS) often found in drug delivery devices, are not even particularly efficient to produce, resulting in a huge overall carbon footprint of around 6 kg CO2e per kg of PC and almost 7 kg CO2e per kg of ABS1 (Figure 2).
This is significant when you look at pharmaceutical companies’ targets: GSK is aiming for an 80% reduction in carbon emissions by 2030, Novo Nordisk a 33% reduction in Scope 3 emissions by 2033 and Sanofi a 55% reduction in CO2e by 2030. Additionally all three are aiming for net-zero emissions by 2045, as is Johnson & Johnson, which wants 80% of its supply chain to meet science-based targets by 2028. Pfizer is aiming for net zero by 2040. All in all, this is slightly more ambitious than what the EU climate legislation requires. With 80% to more than 90% of emissions coming from the supply chain, the need for carbon-efficient plastics in drug delivery and packaging is clear (Figure 3).
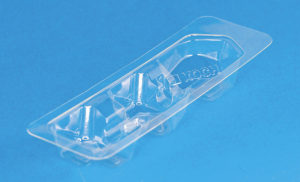
Figure 3: Medical blister packaging made from MedEco XCB – a substitute for PET.
For example, the Packaging and Packaging Waste Regulation (PPWR) will drive a number of material changes for recyclable products over the next few years, moving the industry away from fossil-based polymers currently in use. What does this mean for drug delivery devices?
FUTURE-PROOFING INJECTORS AND DRY POWDER INHALERS WITH PLA?
With bioplastics being the simplest material solution that can meet industry requirements, such as medical-grade plastics defined in the VDI 2017 Medical-Grade Plastics guideline, they can address both health and environmental risks.
“BIOVOX’S MEDECO PLASTICS ARE PARTICULARLY SUITED TO THE HEALTHCARE MARKETS – THEY ARE NOT ONLY SUSTAINABLE BUT ALSO PATIENT SAFE AND LONG-TERM STABLE IN FORMULATION AND PROVENANCE.”
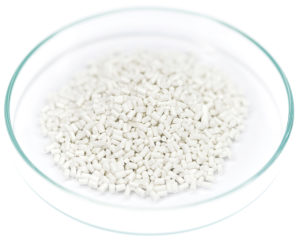
Figure 4: MedEco IGH inside a dish made of the transparent MedEco ICB; one of the preferred bioplastics for autoinjectors and inhalers
With no critical substances and up to 85% lower carbon emissions, including when incinerated at the end of their life, a range of bioplastics offers the potential to meet future requirements and mitigate regulatory risks. BIOVOX’s MedEco plastics are particularly suited to the healthcare markets – they are not only sustainable but also patient safe and long-term stable in formulation and provenance. BIOVOX offers comprehensive change notifications, proven biocompatibility, extensive documentation – including the effects of ageing and various sterilisation methods on the material – and development and production under ISO 13485 quality management. These are necessary prerequisites for the use of plastics in drug delivery devices but, in particular, the PLA-based MedEco ICB and MedEco IGH offer properties that are perfectly suited to the autoinjectors and inhalers of the future (Figure 4). Why is this the case?
BIOVOX’s PLA-based MedEco ICB and IGH offer key benefits for drug delivery devices, such as autoinjectors and inhalers. Their high mechanical strength and stiffness ensure durable, reliable and material-efficient designs that reduce the use of plastics without compromising device integrity. Both of these MedEco grades have higher stiffness than PC or ABS and are easy-flowing, enabling thinner parts to be used that reduce cycle times and save material, while decreasing costs and environmental impact. Lower processing temperatures – approximately 50°C lower than ABS and 100°C lower than PC – also save energy. Additionally, minimal energy is required to produce PLA, with a cradle-to-gate footprint of only about 0.6 kg CO2e per kg of MedEco ICB. The materials are fossil-free, which also reduces dependence on fossil resources from politically unstable regions.
ICB also offers excellent glass-like transparency, making it ideal for components that require visual monitoring of the drug or mechanism. In addition, low shrinkage, high surface hardness and precise detail reproduction enable the production of high-precision components, which are critical for consistent performance of drug delivery devices. The feel of a material further enhances perceived quality – IGH offers excellent grip with vinyl and nitrile gloves, both wet and dry, improving the user experience of autoinjectors. A prime example of these benefits in action is a trocar system developed and demonstrated by Röchling Medical.2
ADDRESSING PLA END-OF-LIFE AND RECYCLING MYTHS
However, the real bonus of PLA comes at the end of its life. PLA is one of the most versatile polymers when it comes to disposal. With 100% bio-based carbon, today’s standard disposal – incineration – is climate neutral. The CO2 emitted has been captured by the plants from which the polymer is made, closing the carbon cycle over a growing season.
In addition to incineration, PLA has faced a number of misconceptions in the past, particularly with regard to recycling. Recycling, such as that being set up in Denmark and France for autoinjectors, is necessary to move healthcare towards a circular economy. It further reduces the consumption of energy and raw materials, thereby reducing the carbon emissions and impact categories associated with agricultural processes.
Let’s clear up a common misconception right away – yes, PLA is recyclable within existing industrial processes. For post-consumer waste, current recycling rates remain low due to limited volumes. However, as PLA adoption increases, mechanical recycling will increase for economic reasons. Post-industrial PLA waste is already being mechanically recycled today. BIOVOX has conducted tests and found that its PLA-based MedEco grades degrade only slightly over six cycles of production and regranulation – similar to medical polyolefins, such as the company’s MedEco Bio-PE grades. Moreover, PLA does not interfere with the recycling of other polymers – it can be easily and reliably identified by near-infrared sorting technologies and then separated using modern sorting technologies. Traces of other polymers are inevitable in any recycling process, and PLA is no more problematic than any other material.3
“BEST OF ALL, AS POLYESTERS, MEDECO ICB AND IGH CAN BE EASILY CHEMICALLY RECYCLED IN A MONOMER-RECYCLING PROCESS.”
Best of all, as polyesters, MedEco ICB and IGH can be easily chemically recycled in a monomer-recycling process. With double the yield and half the energy consumption compared with pyrolytic chemical recycling, a medical-grade recyclate can be produced with half the footprint of virgin material but with 100% patient safety. BIOVOX is currently demonstrating this in research projects, including in contaminated waste streams.
SPRAYS, DROPPERS AND PHARMACEUTICAL PACKAGING
BIOVOX is constantly researching formulations with new biopolymers and drop-in polymers to expand the possibilities for sustainable healthcare materials (Figure 5).
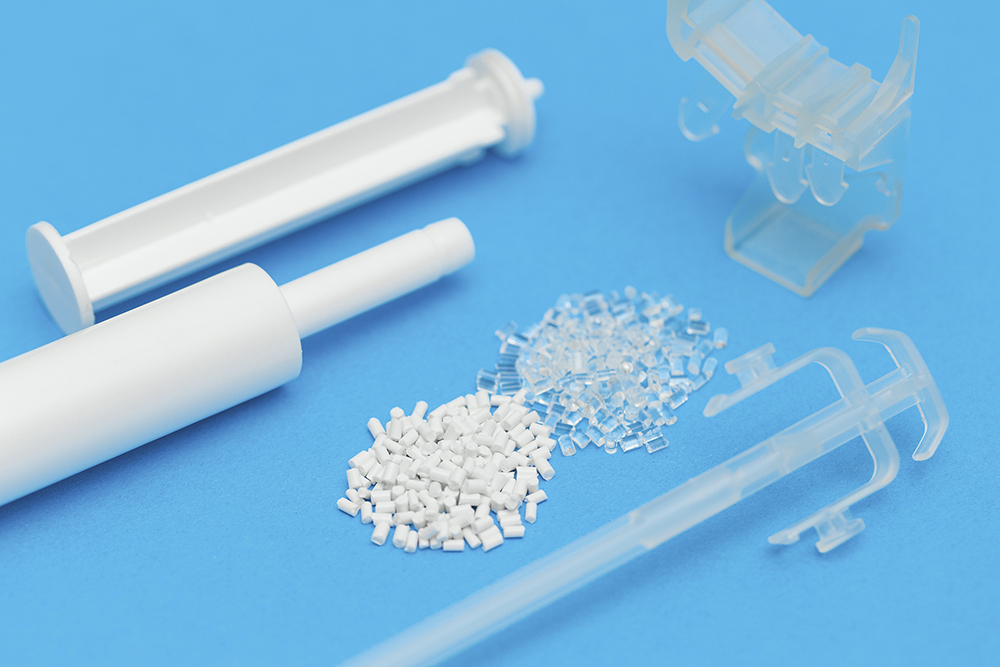
Figure 5: Injection-moulded parts of surgical devices, device packaging and a syringe using BIOVOX MedEco bioplastics.
One promising material is bio-based PE, which is emerging as a viable option for soft packaging, tubes and ophthalmic squeeze dispensers, for example. It offers excellent barrier properties against water vapour diffusion and performs as well as its fossil-based counterpart, while significantly reducing environmental impact. Its carbon footprint is negative on a cradle-to-gate basis and releases only about 20% of the emissions of fossil-based PE in incineration scenarios – just over 1 kg CO2e per kg PE compared with 5 kg CO2e per kg fossil-based PE, cradle-to-grave, including incineration at end of life.
Another exciting innovation for bottles and blisters is PE furanoate (PEF) – a polymer made from renewable resources. PEF also has superior barrier properties against oxygen and other gases, making it particularly attractive for pharmaceutical packaging that requires extended shelf life and high protection against external factors. BIOVOX is always happy to start pilot projects with customers who want to be at the forefront of sustainability by using development-stage MedEco grades.
IN A NUTSHELL: FUTURE-PROOFING DRUG DELIVERY DEVICES WITH BIO-BASED MATERIALS
Transforming healthcare by using materials without critical content is an imperative for all pharma and medtech companies. Combining this effort with the transition to a sustainable, circular economy for healthcare plastics is the icing on the cake – it is not a separate issue from patient safety, it can be solved synergistically. This reduces product risk while improving image and market position.
Many will say there is no room for expensive niche materials. The facts are different – in most of its projects, BIOVOX sees a small 2–5% increase in part cost while reducing the carbon footprint by 60–85% and eliminating BPA and similar substances. In rare cases, the cost per part can be up to 10% higher, however, costs can also be reduced too. On the whole, using bioplastics is a good investment in risk mitigation and marketing.
By implementing sustainable materials such as the MedEco range, manufacturers can future-proof their products and stay ahead of the competition. With EU sustainability regulations and the industry already moving towards circularity – just look at this year’s Pharmapack – now is the time to innovate.
BIOVOX is committed to being at the forefront of these advances – working agnostically with polymers to provide the best solutions for each case. BIOVOX achieves this with regulatory and technical competence, with full material safety according to the VDI 2017 Medical-Grade Plastics guideline and with minimal impact on human and environmental health.
REFERENCES
- Rubio-Domingo G, Halevi A, “Making Plastics Emissions Transparent”. Coalition On Materials Emissions Transparency, Feb 2022.
- “A Single Use Medical Device Designed for Sustainability”. Röchling Medical, Mar 2025.
- “PLA in the Waste Stream”. Fachagentur Nachwachsende Rohstoffe and Federal Ministry of Food and Agriculture, Oct 2017.