To Issue 153
Citation: Severin M, “Driving Sustainable Drug Delivery Devices with Continuous Improvement Processes”. ONdrugDelivery, Issue 153 (Oct/Nov 2023), pp 28–32.
Marc Severin discusses the H&T Excellence programme and how it has been expanded to include methods and training to help H&T Presspart identify environmental impact at a product group level and take co-ordinated action to reduce carbon emissions across the organisation.
H&T Presspart’s products reach millions of patients every day, giving the company the responsibility and the opportunity to drive ecological and social transformation. Resources are finite, and the boundaries of the planet have already been partly exceeded. The scenarios of climate science show the drastic impacts of a rising global temperature on life on Earth. The 1.5°C target from the Paris Climate Conference in 2015 leads the way to preventing the most severe scenarios and is a model for all kinds of organisations to transform their businesses to contribute to this ambitious goal.
“During workshops and training sessions, which form part of the H&T Excellence programme, H&T Presspart encourages its employees to embrace continuous improvement culture and the benefits of lean principles, and to apply them to their own processes.”
Patients, societies, people and politics are becoming increasingly aware and have a greater sense of urgency to become active in the push towards environmental sustainability. Guidelines, regulations and standards like the Sustainable Development Goals (SDGs), the Corporate Sustainability Reporting Directive (CSRD) and the emissions reporting standard Greenhouse Gas Protocol provide organisations with multiple challenges and the potential to become more sustainable, contributing to a world that operates within the planetary boundaries. H&T Presspart is working with different kinds of standards to create sustainable pathways and is aligning them with legal, supply chain and customer requirements.
H&T Presspart has set ambitious targets for the transformation of its value chains. For example, it aims to achieve a greenhouse gas (GHG) emissions reduction of 80% in operations by 2033 and achieve net zero emissions across the value chain by 2050. To pursue these ambitions, the company has set further operational targets for different areas in strategic action fields.
Whilst seeking growth, industry needs to identify new ways of designing and manufacturing products, and a focus on the value stream is essential for responsible business practices. Reducing the input of resources, waste and linear streams requires a completely new mindset. Thinking circularly enables companies to drive positive change. Thinking circularly is the way to a world that respects planetary boundaries.
DRIVING TO PERFECTION
H&T Presspart, as part of the Heitkamp and Thumann Group, embarked on the implementation of H&T Excellence, an operational excellence management programme, over 10 years ago. Since then, operational excellence has been embedded into the organisation and is now an integral part of its organisational culture.
Joel Willerding, H&T Excellence Manager, explains, “The focus of H&T Excellence is on eliminating or reducing waste by creating a culture of continuous improvement. Such a culture can only be developed within the company if each employee experiences the benefits of the lean principles in their own workplace. On the one hand, we need a long-term strategy to show us the overall direction we need to take and the path to achieving our objectives. On the other hand, all employees must be included in the improvement process and the targets must be broken down, from senior management to shop floor employees.”
During workshops and training sessions, which form part of the H&T Excellence programme, H&T Presspart encourages its employees to embrace continuous improvement culture and the benefits of lean principles, and to apply them to their own processes. Generating a positive attitude towards change amongst employees, as well as sharing best-practice solutions and enabling the constant exchange of information across the organisation, is a key approach to continuous improvement within the Heitkamp and Thumann Group.
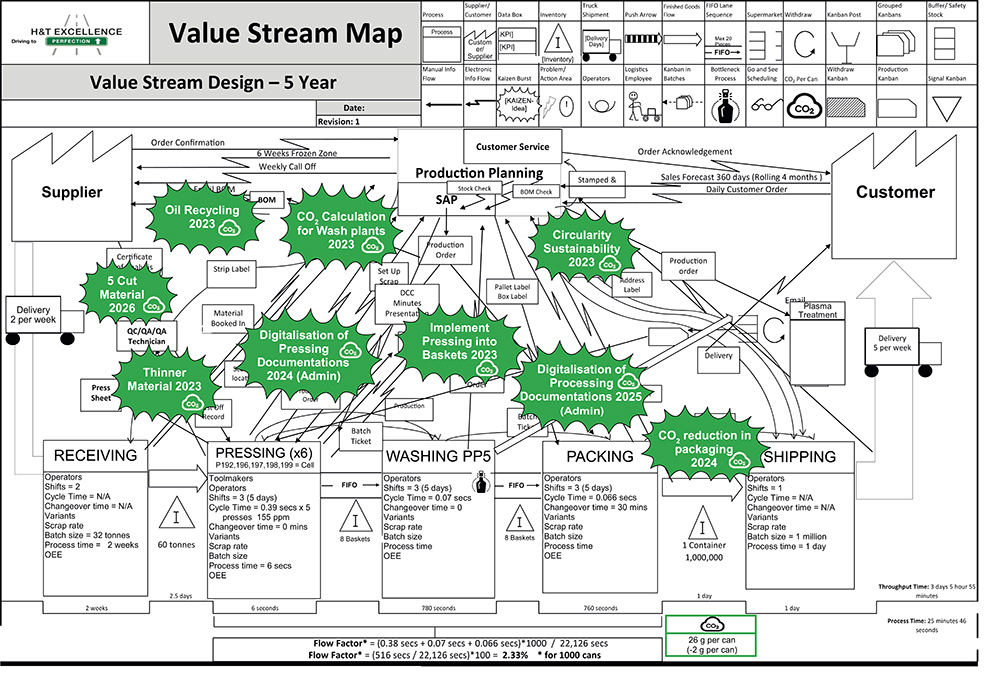
Figure 1: An example of a value stream mapping with all steps, with a focus on improvement areas.
As part of the H&T Excellence programme, H&T Presspart has adopted value stream analysis (VSA) as one of the central tools for the identification of improvement potential. This is a powerful methodology used to visualise and analyse the flow of materials, information and processes within an organisation (Figure 1).
“Going deep into the data, it is possible to understand the impact of various measures for improving material scrap, waste generation or packaging.”
MAPPING THE VALUE STREAM TO INCLUDE CARBON EMISSIONS
A major milestone for the sustainable business transformation at H&T Presspart has been the integration of sustainability into the H&T Excellence programme and the identification of carbon emissions at each point in the value stream, from goods and materials receipts to the takeover of final goods by the customer.
In the first step, the current state of the value stream is mapped from the extraction of raw materials through manufacturing, distribution and use, all the way to disposal. In addition to operational data, environmental data, such as GHG emissions, is now also collected at each stage of the value stream to help identify inefficiencies, sustainability hotspots and related improvement potentials in operational processes. H&T Presspart’s tools can help prioritise measures to reduce its environmental impact and carbon footprint, such as the optimisation of the transportation routes, energy efficiency or waste generation.
Next to concrete optimisation ideas, the results of VSA led the way for H&T Presspart’s product footprint calculator, which can assess the environmental impact of product groups from raw material extraction to delivery to customers. Thetool has been individualised for the specific needs and value streams of different product groups at each of the company’s sites. Each site can tailor its data input, such as for throughput times, materials and consumables, or electricity or energy use, to obtain information about which step of a particular value stream comes with the highest carbon footprint or potential for improvement. These potentials for positive change or improvement (kaizen)are then mapped in a kaizen diagram, which also shows the intended state after implementation of all actions or improvements (Figure 2).

Figure 2: Process design after the implementation of all kaizen measurements.
The product footprint calculator gives H&T Presspart a tool to map the pathways for a more sustainable product. Striving for this, the company differentiates between ideas it can implement itself and those that need strong co-operation and transparency along the supply chain. H&T Presspart works with suppliers and customers in partnership to evaluate alternative materials, product designs or production processes and analyses the potentials and benefits in co-operation with them.
CONTINUOUS IDENTIFICATION OF IMPROVEMENTS
The product footprint calculator gives H&T Presspart the chance to identify key drivers and large levers at a product group level. The company has identified that raw material has by far the highest share of a product’s carbon footprint, with more than 80% for a metered dose inhaler (MDI) canister and 65% for an MDI actuator. In contrast to this, energy consumption is comparatively low. This is mainly due to the fact that the electricity requirement to run a press or a coating line is high in general, but only a fraction of that applies on a single product basis. If a deep drawing press consumes 1.5 kWh per 1,000 parts, the electricity requirement to produce a single canister is only 1.5 Wh.
The same can be observed in terms of coating. While a canister weighs around 8 g, the lacquer weight per can is less than 1 g, so that >7 g is purely aluminium. When considering that aluminium has a carbon footprint more than 20 times higher than conventional electricity, it is possible to directly derive priorities and action from that analysis.
Going deep into the data, it is possible to understand the impact of various measures for improving material scrap, waste generation or packaging. Those measures often have a low impact on the total carbon footprint when looked at in isolation. However, working on a series of these improvements leads to significant improvements over time. For example, by implementing a series of energy consumption improvements and optimisations in H&T Presspart’s cold air and water supply management, the company was able to realise an estimated carbon footprint reduction of about 35 Tn, in addition to significant cost reductions.
There are multiple tools in addition to VSA that can help identify potentials to avoid waste, reduce energy or material consumption or improve production and material efficiency. These tools have been embedded into H&T Presspart’s operational excellence culture and can now be used not just to identify cost savings, but also to identify potentials for GHG emission reductions. With Total Productive Maintenance (TPM) programmes and training, H&T Presspart is constantly reducing unplanned downtime or increasing the lifespan of equipment. With frequent Single Minute Exchange of Die (SMED) initiatives, workshops and training, the organisation identifies and realises measures to reduce the planned downtime of machinery and complete production lines.
SUSTAINABLE DRUG DELIVERY FOR TOMORROW
The H&T Presspart operational excellence programme was embedded in the organisation more than 10 years ago. The evolution to integrate sustainability into the programme, its tools and training has given H&T Presspart a structured approach to identifying improvement areas and quantifying potential ways to reduce the company’s carbon footprint and to help create a pathway to more sustainable drug delivery devices. The development of a product footprint calculator through VSA is one method that has enabled the organisation to not only measure the environmental impact at product group level, but also identify and act upon opportunities for sustainability improvements. By bringing together a cross-functional team, leveraging data-driven insights, and integrating sustainability into its decision-making processes, the company is well equipped to navigate the challenges and opportunities of a more sustainable future.