Citation: Reuter S, “High Precision in Plastics Improves the Quality of Life of Diabetes Patients”. ONdrugDelivery, Issue 124 (Sep 2021), pp 26–29.
Steffen Reuter discusses the importance of high precision when manufacturing injection moulded components for wearable insulin delivery devices, with particular reference to three such parts from a recent project as a case study for Weidmann Medical Technology’s approach.
“Plastic injection moulding plays a crucial role in the manufacture of such highly sophisticated components – injection moulding processes can be used to produce precise parts to a high degree of accuracy in high volumes and at low cost.”
Today, there are more than 460 million people living with diabetes, and the number is increasing day by day.1 As such, medical scientists and the drug delivery industry are looking for new solutions to improve the user-friendliness of insulin injections, and thus the quality of life of millions of diabetics. This is why the current trend is moving away from conventional methods of treatment – injecting long-acting and rapid-acting insulin infusions by using a pen injector – and more towards the use of automated insulin delivery (AID) devices worn on the body.2 Such devices are preferable because they provide a continuous subcutaneous insulin infusion that attempts to simulate the natural function of the pancreas.
This therapeutic use of insulin pumps is to balance a patient’s blood glucose level so that it remains as constant as possible within the required target corridor. Correct insulin management prevents major fluctuations in blood glucose levels, thus significantly reducing the risk of damage due to hypoglycaemia or hyperglycaemia. Furthermore, additional burdens on the patient’s day-to-day life due to their condition are avoided, and the increased comfort of using an AID leads to greater freedom for those affected.
HIGH-PRECISION COMPONENTS
Successful diabetes therapy via continuous subcutaneous insulin infusion not only requires continuous measurement of blood glucose levels and an excellent algorithm for calculating the necessary dose of insulin according to the patient’s state of stress but also a highly precise pump for delivering an accurate dose (Figure 1).
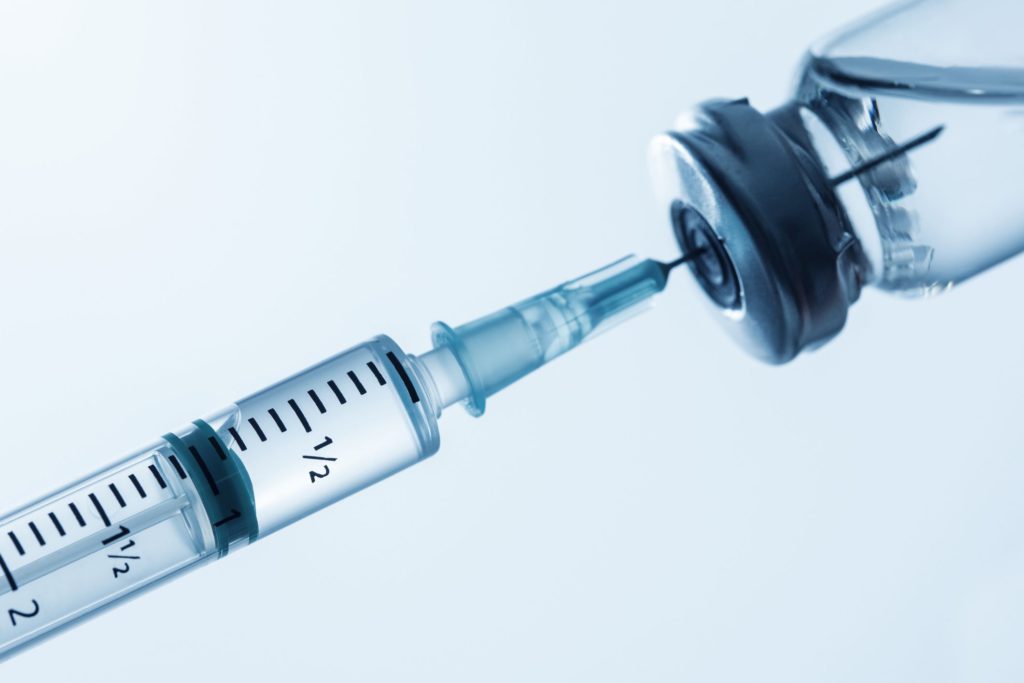
Figure 1: High-precision elements are key when it comes to delivering an accurate dose.
Plastic injection moulding plays a crucial role in the manufacture of such highly sophisticated components – injection moulding processes can be used to produce precise parts to a high degree of accuracy in high volumes and at low cost. Designing the right production concept, consisting of an injection moulding machine, injection mould and production periphery, is mandatory for success.
Weidmann Medical Technology supports its customers with in-house know-how in the development of production solutions for highly precise and sophisticated plastic components, applying the ISO 13485 based “Stage and Gate” development process (Figure 2). Such expertise is a requirement for realising the components needed for an AID pump.
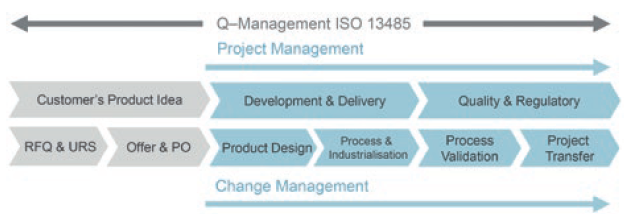
Figure 2: Stage and Gate process at Weidmann Medical Technology. Overview of the process steps for handling a client’s project from the product idea to industrialisation.
“The knowledge in design and experience in building such high temperature moulds is of limited availability on the market. Therefore, carefully selecting a supplier is highly recommended to get the right one for the project’s needs.”
DEVELOPING PRECISION PARTS FOR AN INSULIN DELIVERY DEVICE
Using the example of three key components for insulin delivery – the fluid reservoir, dispenser piston and dosing spindle – this article briefly presents Weidmann Medical Technology’s development approach, as well as the challenges faced during product realisation.
Because the design responsibility for the product rests with the customer, the first step of good design for manufacturing (DFM) is to recognise and identify the key requirements at the beginning of the project. At this stage, it is crucial to provide the drawings and specifications from a detailed feasibility study based on computer-aided design data. Any critical requirement should be addressed, jointly discussed and agreed with the customer. If possible, all optimisations necessary for stable and robust serial production should be implemented to the part design at this point in the development cycle. The next important step is to translate those results into individual user requirement specifications for the injection moulds and production equipment.
Dispenser Piston
Of the key components discussed in this article, the interface of the plunger with the reservoir is the most sensitive to imprecise manufacturing. In this case, an elliptical cross-section was selected for the reservoir design in order to maximise simultaneously the level of comfort for the patient wearing the device, the size of the insulin tank and the ability for the device to be worn as inconspicuously as possible on the body. This required that the components have the tightest shape and position tolerances possible in order to position the seal precisely in the piston mechanism. On the one hand, there cannot be any leakage due to excessive play between the two components, and on the other, the sealing forces must not unduly influence the metering accuracy. The great challenge was in realising the geometric specifications and the tolerances on the component – as well the compliance with those requirements during series production.
For the reasons outlined so far, a manufacturing concept for the piston consisting of a three-plate mould with multiple cavities produced on a micro injection moulding machine was selected. Because of the low shot volumes required, such an injection moulding machine offers many advantages for achieving the maximum possible component quality – for example, through the injection of thermally homogeneous material, low-stress metering, the possibility for short flow paths, and high process and repeat accuracy.
The high-performance plastic selected for the component needed to be processed at a very high melt temperature, as well as a very high mould temperature. The knowledge in design and experience in building such high temperature moulds is of limited availability on the market. Therefore, carefully selecting a supplier is highly recommended to get the right one for the project’s needs.
The complex geometry of the component required a sophisticated mould with several moving components and sliders. The moulding components needed to be precisely matched to each other in order to prevent over-moulding and burrs. To maintain the required tolerances of a few thousandths of a millimetre, it was necessary in this case to carry out the final matching of the mould on the injection moulding machine at its operating temperature. In this way, burr build-up could be significantly reduced even further. In addition to the quality of the mould, a robust production process is equally important in order to deliver the required quality during serial production. For this reason, process development is of the utmost importance. Systematic process variations were carried out and several loops have to be performed until the “right” process had been found. Based on this, in the final step, the potential standard variations of the most important process parameters were run in so-called “process windows”. All parts produced in this way were measured and found to be within the required specification of the multi-stage approval process according to ISO 13485 (design, installation, operational and performance qualifications), at which point the product validation was considered complete.
Fluid Reservoir
“In the future, digitisation will make even greater inroads into medical technology. The integration of electronics in plastic components is already playing a major role, and the combination of high-precision plastic with inserted and over-moulded components will only evolve further.”
In addition to compliance with the geometric requirements for guiding the dosing piston, the challenges with the fluid reservoir were the integration of an additional sealing lip to seal the entire system, as well as the high optical requirements of the transparent insulin tank. There are multiple different mould concepts for the production of multi-component parts such as this. When a concept is decided on, it is mounted on an injection moulding machine with plasticisation units for each resin in order to be able to produce it in the required quantities.
In this case, a multi-cavity mould was selected using core back technology. In the first process step, the cavity of the transparent insulin container is injected with polypropylene. Once that step is complete, the sealing geometry is created by pulling back a slider and then filling the reveal with a thermoplastic elastomer as a second process step. Due to the good adhesion between the two plastics, a durable seal is created. Particular attention had to be paid to the injection gate geometry of the soft component to ensure that the gate “rubs off” cleanly and that there are no unwanted protrusions.
Another important quality feature concerns the inner surface of the tank. This influenced the sliding properties of the piston seal, and therefore the metering accuracy. For this reason, a high-gloss surface is generally desirable. However, this can lead to demoulding problems – severe deformation when the component is removed from the open injection mould. To avoid this effect, which is similar to two sheets of “sticky” glass, the cores are withdrawn before the mould is actually opened. In this way, the injection-moulded insulin reservoirs can be easily removed from the mould by means of a gripper and placed on the cooling conveyor belt. From there, they are packaged in blisters ready for shipment.
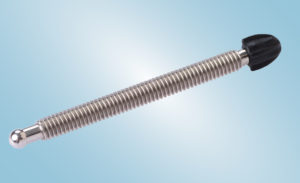
Figure 3: Metal screw over-moulded with plastic.
Dosing Spindle
The third sophisticated component of an insulin pump referred to in this article is the helical dosing spindle. The interface between the dosing spindle and the driving element that was designed by the customer was as a plastic head. This meant that the metal screw had to be inserted into the injection mould and then over-moulded with plastic resin (Figure 3). The shot weights required for this also lent themselves well to the use of another micro injection moulding machine. However, the associated automation required so much space that it would only fit on a standard injection moulding machine. One reason for this was that was the metal screws were delivered in blisters and then had to be placed back into blisters after over-moulding, a process that required a significant amount of machinery to automate.
Because of the need to use a standard injection moulding machine, the use of a very small metering screw for plasticisation was required. Additionally, in order to achieve the necessary injection shot volume, the mould inserts of the ball heads were filled using a cold runner manifold and the mould needed to have a large number of cavities. In turn, this further increased the effort and space required for automation!
Key to implementing automation for the process was ensuring the exact alignment and pre-positioning of the screw, so that the threaded screws were inserted precisely into the mould to prevent any unwanted over-moulding of the mould cavities. Furthermore, the screws had to be inserted and fixed in the designated cavities in such a way that they would not lose their position when the mould was closed, otherwise severe damage to the mould cavities, or even a total failure of the mould, could occur – an outcome that needed to be avoided at all costs.
To ensure the insulin pump’s high dosing accuracy, the screw was designed as a fine thread. It was imperative that it was not damaged during the multi-stage handling process under any circumstances, otherwise it could result in the insulin pump malfunctioning. Extensive tests with different grippers were conducted for removal from the blister, insertion into and removal from the tool, and storage in order to find the right design. In this way, it was possible to realise the required fast movement speed of the handling robots, which was necessary to achieve the desired cycle time, without losing the inserts or damaging the spindle’s thread.
CONCLUSION & FUTURE OUTLOOK
In the future, digitisation will make even greater inroads into medical technology. The integration of electronics in plastic components is already playing a major role, and the combination of high-precision plastic with inserted and over-moulded components will only evolve further. The experience already gained in projects, such as the one discussed in this article, will help to industrialise high-precision components in future implementations.
Weidmann Medical Technology offers solutions from a single source. This is because the company uses a holistic approach to find the right balance between the necessary complexity (a combination of injection moulds and automation systems) and economic efficiency in the industrialisation of highly demanding products. A great deal of experience and passion in implementation are necessary to correctly assess the complexity of a project and to find sophisticated, tailor-made solutions for the customer, as demonstrated by the examples outlined here.
REFERENCES
- “Diabetes Facts & Figures”. International Diabetes Federation, 2019.
- “Automated Insulin Delivery (Artificial Pancreas, Closed Loop)”. diaTribe Foundation, Aug 2020.