To Issue 153
Citation: Bruce V, “Making Low-Carbon-Emission Single-Use Medical Devices a Reality”. ONdrugDelivery, Issue 153 (Oct/Nov 2023), pp 46–51.
Veluska Bruce discusses the design and development of single-use autoinjectors in the context of sustainable development.
Sustainability is a vast topic that could well be contextualised through the United Nation’s (UN’s) efforts on sustainable development over the decades. In 1987, the UN Brundtland Commission defined sustainability as “meeting the needs of the present without compromising the ability of future generations to meet their own needs”. Then, in 2015, the UN General Assembly agreed on the Sustainable Development Goals (SDGs), a normative concept that many countries embrace to achieve a sustainable future for humankind and the planet. Today, sustainability is a shared responsibility with multiple facets, which merits discussion and transformative action in the pharma and medical device industries.1
In light of this, it should be acknowledged that the development of the autoinjector helped set the standard for home-based parenteral treatments. In many ways, it manifests sustainable development focusing on healthcare. As a medical device that delivers precious drugs and biologics to patients with chronic diseases, the autoinjector has re-envisioned patient autonomy, particularly in parenteral therapy. SHL Medical is proud to be a significant part of the evolution of autoinjectors, and the company is committed to challenging, rethinking and embodying what it means to enable patient independence. SHL plans to expand its portfolio of innovative drug delivery devices by 2030, in turn helping more than eight million patients to be independent.
“Disposable medical devices, which include autoinjector products, must carefully balance materials, cost, performance, reliability, shelf life and end of life.”
SUSTAINABILITY BEYOND A LOW-CARBON-EMISSION PRODUCT
The promotion of health and wellbeing is a crucial piece of the UN SDGs. SHL uses its technical device expertise to help its pharma partners accelerate patient access to medical devices worldwide. Cognisant that these medical devices are essential to millions of patients suffering from chronic diseases, SHL believes that autoinjector products as a convenient treatment modality will stay. At the same time, advances in the medical device industry have led to the realisation of the urgent importance of product lifecycle management that supersedes current ideals. Thus, disposable medical devices, which include autoinjector products, must carefully balance materials, cost, performance, reliability, shelf life and end of life.
Time is of the essence when it comes to global sustainability. Current attempts by businesses across many industries to introduce eco-friendly and zero-impact products are laudable. Perhaps, resorting to introducing new products that claim to be eco-friendly may be the only solution. In any case, reality dictates that a persisting challenge remains to drive sustainability in existing products. For SHL, sustainability requires a dynamic, two-pronged approach: addressing what’s already existing while shaping the path toward a better sustainable future.
It remains a fact that the autoinjector embodies the improvement of lives in its DNA. While arguably metaphorical, this reflects the recognition that autoinjector products will remain integral to the limited options for delivering necessary parenteral treatment within modern medicine. As autoinjector products continue to proliferate now and in the future, sustainability should come from as early as product conceptualisation – embedded in the product’s DNA. At the same time, SHL acknowledges the need to intercalate sustainable designs into the identity of existing products and their processes. The company is calling on the rest of the industry to act upon this pressing challenge.

Figure 1: SHL Medical’s sustainable design principles.
Upholding the established importance of autoinjectors, SHL is investing efforts towards sustainable design thinking. It is reshaping the lifecycle of its solutions and their processes – driving impact and improving the quality of life for patients – without draining the planet’s resources further and respecting its limits. To this end, the SHL sustainable design principles (Figure 1) were developed – the company’s guiding compass to think and act sustainably beyond the confines of introducing a purported eco-friendly product. Going beyond impact neutrality, SHL focuses on driving regenerative thinking, design and innovation.
The application of the sustainable design principles implies following a systematic approach that strives to achieve products with the lowest possible environmental impact throughout the product lifecycle without compromising performance, patient safety, functionality or quality. SHL uses these principles as a foundation to design products following a circular approach.
EMBRACING A CIRCULAR DESIGN APPROACH
From the perspective of a single-use medical device manufacturer, it might seem that the ultimate goal is to reduce the device’s footprint. Indeed, this is true, but to fully acquire a circular mindset, one must think beyond any conventions and innovate products to maintain the starting material in the loop.
Product design is a crucial element in enabling circularity. It has been shown that up to 80% of the product emissions, from material usage to end-of-life product waste, can be tailored during the design phase. Particularly for autoinjectors, the intricate design of every component can affect the device’s circularity. To preserve resources, it is therefore vital to include circular inputs that have a low footprint, can be recycled or regenerate naturally.
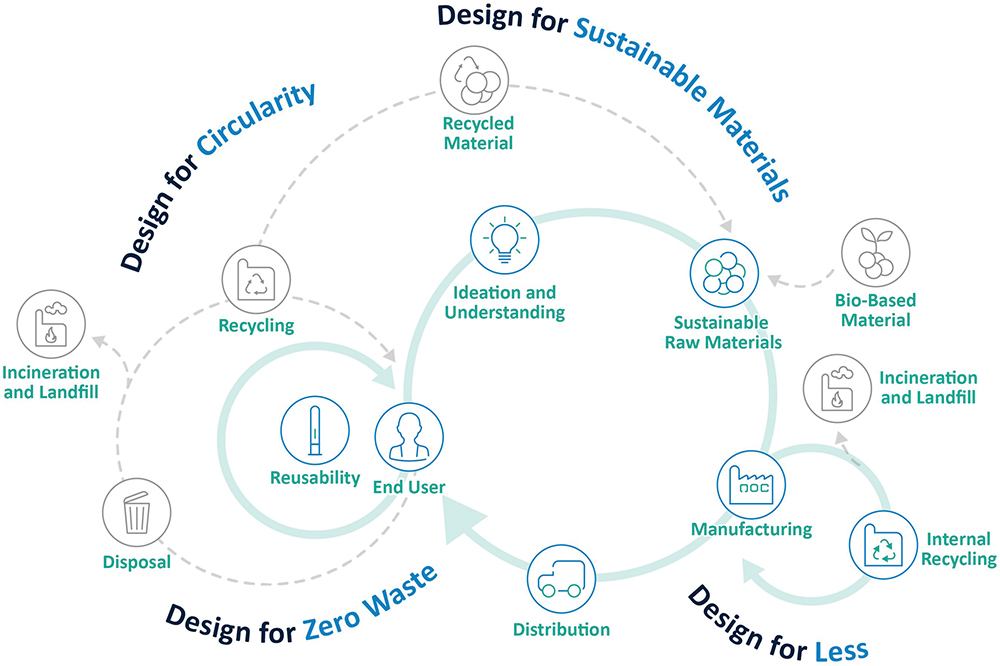
Figure 2: SHL’s sustainable design principles follow a circular design approach.
“Having a data-driven approach is essential for identifying areas for prioritisation and understanding the real environmental impact of products and processes.”
SHL’s sustainable design principles are based on eco-design and circular design theory.2 Following a circular approach (Figure 2) in the device design allows recovery after usage. Circularity in the context of single-use devices includes designing and producing products that can be recovered and reused after usage. Another would be reshaping operations to minimise consumption and eliminate waste by turning them into new resources.
DESIGN FOR REUSE AND REFURBISHMENT: A MATTER OF TRUE SUSTAINABILITY
In the context of circularity, recovery is a broad term that encompasses the process of recycling and reusing. It describes the recovery process ways in which a valued raw material can be used in other products and describes the implementation of reuse. Specifically, direct reuse may be defined as “any operation by which products or components that are not waste are used again for the same purpose”.3 To be able to reuse products or core parts of the products (e.g. refilling the drug in the same autoinjector), the result must be as good as the new product and comply with the functional requirements. Usually, the direct reuse strategy involves the collection of by-products from the waste stream of the already-used products, which entails cleaning, sorting and quality testing processes. Thus, before deploying the idea of refiling and re-dispensing a drug in the same autoinjector, SHL urges its fellows in the industry to bidirectionally quantify all the processes involved to identify the best option.
Further, autoinjectors, as healthcare products, are subject to the laws and regulations of the market where they are used. If the product is considered waste after usage, additional steps need to be considered for it to be reintroduced onto the market. At present, one must ask: “How does the regulatory landscape look when it comes to combining new and reused parts?” Recovery and refill mechanisms are promising options and need joint industry efforts to find the conditions for a successful deployment. SHL believes that careful planning is of utmost importance prior to setting foot into uncertainties. In the end, the decision to explore novel recovery programmes all boils down to the true essence of sustainability. Figure 3 shows SHL’s reflections when designing for circularity.
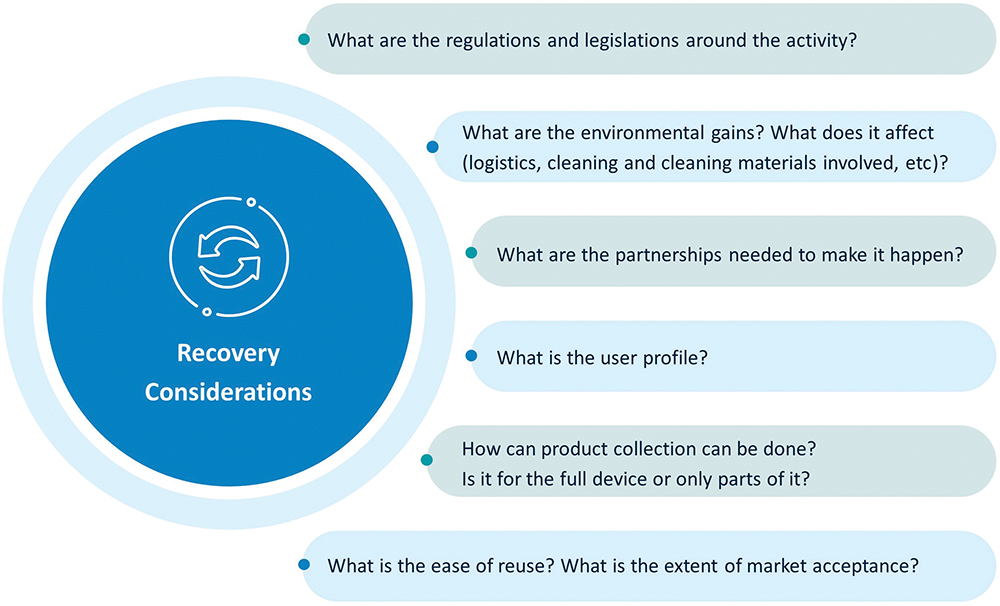
Figure 3: A main idea web showing SHL’s considerations regarding recent industry discussions on autoinjector recovery and refill mechanisms.
DATA-DRIVEN DECISION MAKING
For SHL’s sustainable design principles, design for circularity aims to uphold an innovative product design process that would result in the lowest environmental footprint across a product’s lifetime, supported by data-driven decisions.
One may then ask: “How do you generate an insightful amount of quantitative data to support the decision-making process to enable product circularity?” Here, lifecycle assessment (LCA) is critical to providing a framework for measuring the environmental footprint during the lifecycle of a product. Further, having a data-driven approach is essential for identifying areas for prioritisation and understanding the real environmental impact of products and processes.4
Through LCA, it is possible to analyse a product’s environmental impact across the entire lifecycle. This includes when raw materials are first produced or extracted and when the product is manufactured, used, disposed of and/or recycled. A quantitative compilation of energy, materials and waste for the product and the impacts of these are then evaluated and interpreted. Scientific results and findings are behind each standard environmental impact assessment method. The ecological impacts are sorted into several categories, including particulate formation, climate change (or carbon footprint), water depletion, etc.
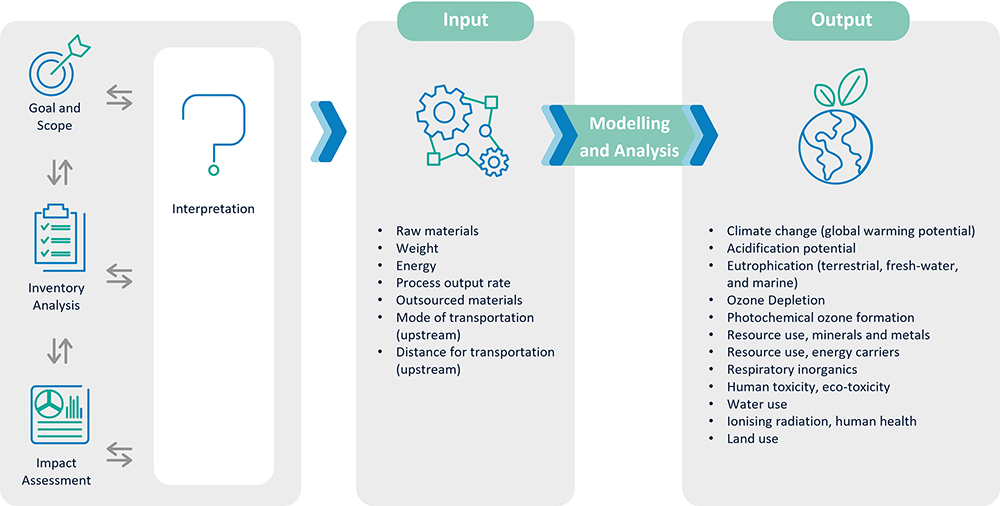
Figure 4: SHL’s environmental impact assessment process and its applications.
To this end, SHL has conducted ISO 14040/14044 compliant LCAs to quantify environmental impact. While there are several LCA environmental impact assessment methods to choose from, Environmental Footprint v3.0 is selected for the analysis shown in Figure 4. Furthermore, the usage of LCA is expanded for the following:
- Analyse the current product’s environmental footprint and leverage the results as input for new developments
- Analyse the footprint of internal processes to find improvement opportunities
- Analyse the frequency of the (potential) treatment and discuss the most sustainable solution.
Generally, LCA focuses on the lifecycle of a product, containing detailed data on each of the phases during its entire lifecycle. Thus, it can be very technical and extensive and usually focuses on only one autoinjector device.2 To design devices with the lowest environmental impact, it is necessary to understand the footprint beyond one product to go towards an entire portfolio (Figure 5).
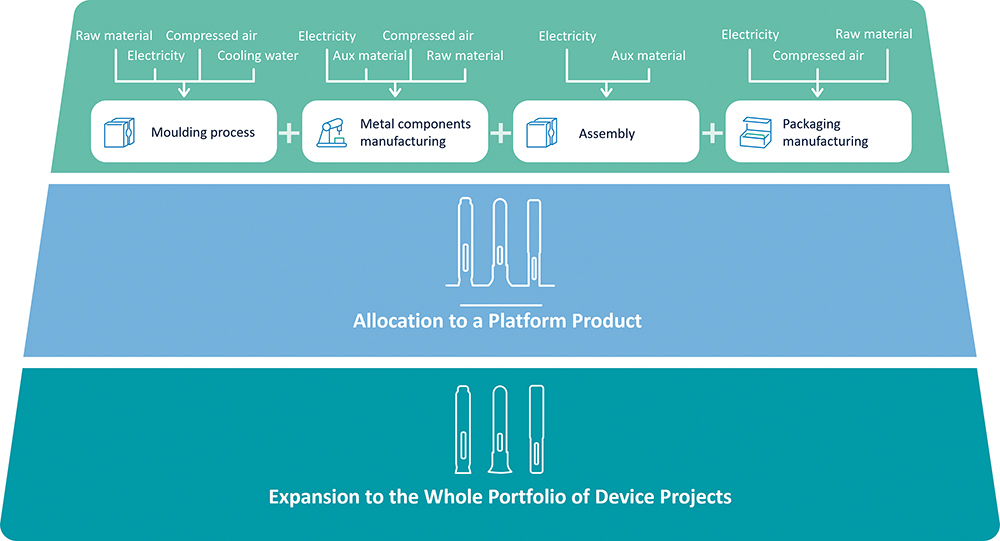
Figure 5: A diagram exhibiting the top-down approach for LCAs at SHL.
SHL has developed a flexible parametric model that monitors emissions during the device lifecycle by adjusting the process building blocks. The emissions data are then reflected throughout the cycle according to set logic, making it possible to iterate LCAs of different device products quickly.
The SHL model assigns material and energy usage that reflect the respective production processes. In turn, such material and energy usage data are associated with the respective output from production. In this sense, we have the footprint of the activities and, subsequently, the product based on specific process activities following a top-down approach.
SHL has set a cradle-to-gate boundary for its LCAs, assessing the product lifecycle until it leaves the factory gates and before it is transported to the consumer. This boundary strategy can significantly reduce the complexity of the analysis and create faster insights into internal processes (Figure 6).
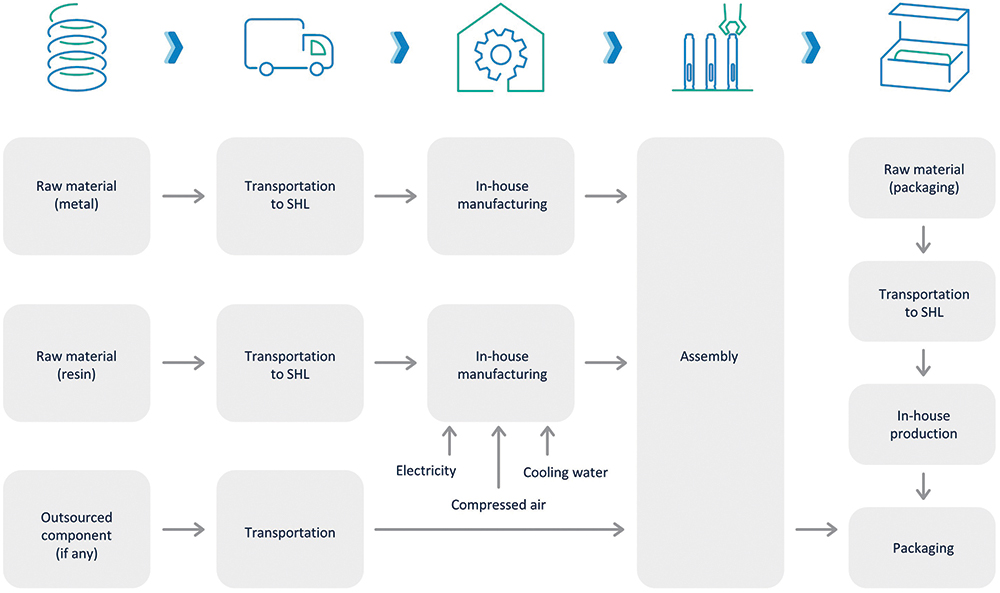
Figure 6: SHL’s parametrised LCA model with a cradle-to-gate approach for autoinjector manufacturing.
SHL’s ultimate vision is to go beyond its gates and work with its customers to achieve and analyse its products cradle-to-cradle. This approach supports circular design since, in contrast to a cradle-to-grave boundary where the analysis reaches up to the disposal of the product, it exchanges the waste stage with a recycling process by “closing the loop”. The combination of circular design with LCA methodologies allows the measurement of the environmental performance of various products, comparison of circular strategies, and the definition of targets to measure and foster circularity over time.
Additionally, quantifying the benefits of circular efforts is of great importance to carefully evaluate potential burden shifting and trade-offs between the applicability of the different principles. This highlights how scenario analysis becomes critical to applying other levers during the circular design.
UNDERSTANDING THE NATURE OF THE MATERIALS AND PROCESSES
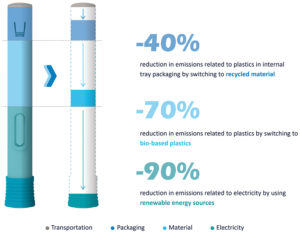
Figure 7: LCA of a single-use device.*
How could material choices be reconsidered to lessen the product’s impact without affecting performance? As part of SHL’s circular design approach, design for sustainable materials usage aims to employ low environmental impact materials that are equivalent in performance to the conventional raw materials used in the company’s processes. These materials could have renewable attributes, such as bio-based or recycled materials.
Raw materials are one of the highest contributors to emissions in autoinjector devices, taking up around 35% of a device’s total carbon footprint – plastics being the largest contributor in this category. For the plastics used, the high emissions are because these materials are typically taken from finite sources. Therefore, SHL is in the process of incorporating bio-based resins into its devices and recycled plastics for the packaging to minimise the emissions related to materials. This allows the company to reduce the environmental footprint, meet its design requirements and comply with regulatory standards (Figure 7).
SHL’s approach to circular design focuses on addressing the root causes of waste and pollution. For example, burning fossil fuels to generate energy can never be circular. Hence, using renewable energy plays an important role in the circular design approach. For a single-use device, SHL has found that this implies around a 90% reduction in the emissions related to electricity.
Aside from raw materials, waste management is also a pressing challenge in addressing product circularity. SHL’s design for zero waste aims to create products that can be more easily disassembled and raw materials returned into a circular economy (i.e. suitable for recycling, avoiding scrap and designing out waste from processes). For SHL, designing out waste means using the scrap from moulding or just designing the parts so that no scrap is obtained.
Furthermore, SHL upholds design with less material input (less weight), fewer material types, less volume and a smaller number of parts – following the “reduce by design” approach by focusing on being less resource intensive. One example involves eliminating the tray packaging for internal logistics. SHL has studied different scenarios whereby innovating the process and having a “no tray” approach could reduce emissions related to packaging for internal logistics by half.
CONCLUDING REMARKS
No matter the type of medical device, rethinking how SHL sources materials, manufactures products and reduces waste is one way towards its sustainability commitments to reduce its footprint and accelerate the transition to a circular economy.
In the last few years, SHL has found opportunities to decrease its single-use device footprint significantly. SHL recognises that every drug delivery device development process has its carbon mark, and we are committed to lowering it. The idea is for its existing device offerings to evolve into the most eco-friendly versions possible, without saying they are “eco-friendly/zero waste” products.
SHL is committed to following a decarbonisation path in alignment with the science-based targets initiative in the race to battle climate change. As the company pursues the true essence of sustainability, it is committed to reducing the environmental impact of its devices to as much as 30% by upholding eco-design principles. SHL is on course for a transformative journey of using fully renewable energy by 2030. The company’s progress motivates it to play its part and build a more sustainable future for all, and SHL is calling on other industry players to join it in this challenge.
REFERENCES
- “Take Action for the Sustainable Development Goals”. United Nations Web Page, accessed Oct 2023.
- “The Circular Design Guide”. Ellen McArthur Foundation Web Page, accessed Oct 2023.
- “Directive 2008/98/EC of the European Parliament and of the Council of 19 November 2008 on Waste and Repealing Certain Directives”. European Commission, 2008.
- Curran MA, “Life Cycle Assessment: A review of the methodology and its application to sustainability”. Curr Opin Chem Eng, 2013, Vol 2(3), pp 273–277.
* LCA of a single-use autoinjector. Calculations were derived from an ISO-compliant LCA study. The study was peer reviewed in 2023 using the Sphera LCA for Experts software (formerly known as GaBi) 2022 database. The external critical review of the report was conducted according to ISO 14044. Calculations depend on assumptions and methodologies used, as well as the recentness of the data. Comparison of these numbers to in-kind, non-SHL alternatives may not provide a direct comparison. This information may be subject to revision if assumptions change, or as modelling data becomes more current.