To Issue 156
Citation: Douse S, Smith J, Wessman B, “Santoprene® TPV – A Next Step in Elastomeric Components for Conventional, Safety and Prefilled Syringes and Autoinjectors”. ONdrugDelivery, Issue 156 (Jan 2024), pp 73–76.
Shiva Douse, Jeff Smith and Brad Wessman introduce Santoprene® TPV, a novel medical-grade thermoplastic elastomer for use in syringes and autoinjectors that offers significant benefits over traditional thermoset rubbers.
INTRODUCTION
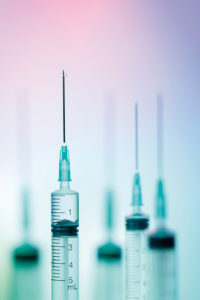
Figure 1: Santoprene® TPV is ideal for single-use and prefilled syringe seals and other medical devices that require long-term sealing performance, flexibility or a soft touch for human contact.
Across the pharmaceutical industry, a variety of factors are coming together to drive ever-increasing interest in subcutaneous and intramuscular parenteral delivery, especially via prefilled syringes (PFSs) and autoinjectors. For one, the huge potential of biologics can best be tapped into via the parenteral route, as the delicate protein molecules are unsuitable for delivery via the hostile environment of the gastrointestinal tract. Another factor is the push towards moving administration of medicines from the clinic to the home, with both patient convenience and environmental concerns fuelling this trend.
With this surging interest, it falls to drug delivery device designers to make their products stand out in the market, both in terms of device quality and value. As such, innovation is a major part of the parenteral delivery landscape, with device designers pushing boundaries on safety, patient-centricity, manufacturability and product quality. A critical component of achieving this is material selection, which comes with a variety of considerations, including material properties, supply and processability.
“As a specialist materials provider, Celanese is constantly innovating
to provide the medical and drug delivery industries with the necessary materials for their components.”
One of the critical materials in a syringe is the elastomer used for the plunger stopper, which may also be used for the syringe or needle cap (Figure 1). A similar stopper application exists in autoinjectors, which enclose a PFS driven by a mechanical delivery system. Celanese is constantly innovating to provide the medical and drug delivery industries with the necessary materials for their components, including advanced thermoplastic elastomers. To this end, Celanese offers an ideal thermoplastic vulcanizate (TPV) solution for use in conventional, safety and prefilled syringes and autoinjectors – Santoprene® TPV.
THERMOPLASTIC ELASTOMERS VERSUS THERMOSET RUBBER
Traditionally, elastomeric components in syringes have been made of thermoset rubbers, the most common examples being styrene-butadiene rubber and butyl rubber. While these materials have excellent sealing properties, they require significantly more processing than thermoplastics. To produce parts by injection moulding a thermoset rubber, the raw materials must be mixed or compounded, then moulded and cured to produce a usable component, with waste product generated throughout the process that is scrapped in its entirety (Figure 2).
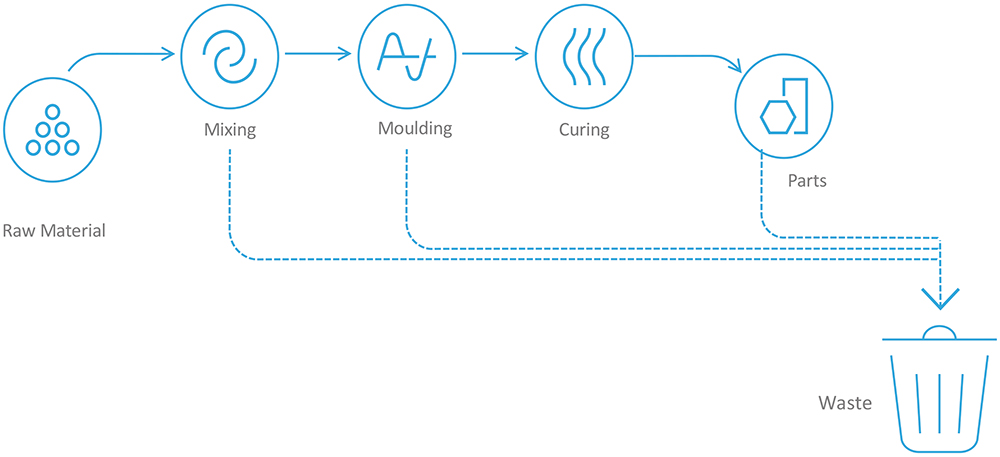
Figure 2: The process for producing traditional thermoset rubbers.
Thermoplastic elastomers, on the other hand, provide the elastomeric properties often sought when selecting thermoset rubber but are processible like a plastic. This includes manufacturing final products from a single pellet feedstock, which eliminates the mixing step prior to moulding and provides a cleaner material solution. The high-precision moulding translates to a flashless process that reduces scrap. Santoprene TPV also allows for waste material to be reprocessed and recycled into raw material, significantly reducing overall waste, as well as making the process more sustainable if adopted for certain applications. Additionally, the faster curing times of TPV compared with thermoset rubber significantly reduce cycle time and energy usage. Taken together, these factors can lead to a reduction in waste of up to 30% and in energy usage of up to 50% when compared with thermoset rubbers (Figure 3), which can be a powerful contributor towards meeting sustainability targets.
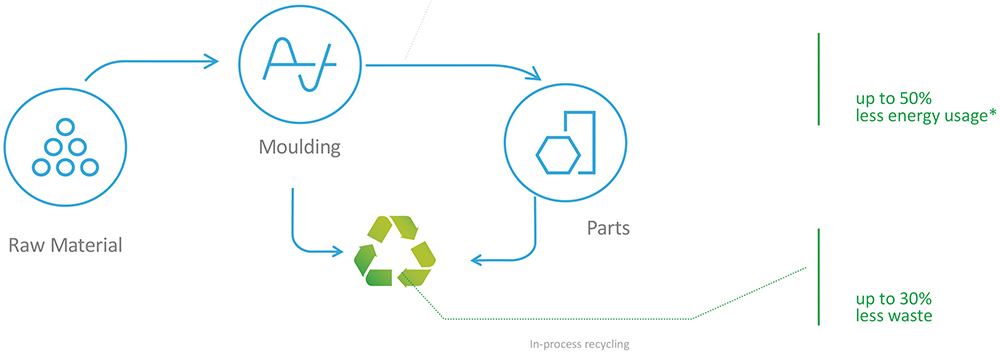
Figure 3: The process for producing thermoplastic elastomers, leading to major reductions in energy usage and waste production compared with that for
thermoset rubbers (*calculations based on non-medical commercial part).
In addition to the economic and sustainability advantages, the production process of thermoplastic elastomers presents exciting possibilities for component design that thermoset rubbers do not allow. For example, thermoplastic elastomers are suitable for over moulding processes or moulding softer and harder parts. This allows device developers to think more flexibly when designing syringe components and potentially to consolidate parts, reducing the overall number of components in the final device.
Maximising the efficiency of material use is a key factor in material selection, for both cost and sustainability considerations. As mentioned prior, thermoplastic elastomers enable in-process and end-of-life recycling, which significantly decreases overall waste, but that is not their only advantage. Thermoplastic elastomers typically have a lower density (by approximately 20%) than rubber compounds, meaning less material is required to make the same part, increasing the overall efficiency of the manufacturing process and reducing the weight of the final product.
“Santoprene TPV can maintain excellent seal integrity and is therefore ideal thermoplastic elastomer for use in conventional, safety and prefilled syringes and autoinjectors.”
SANTOPRENE® TPV – MEETING THE NEEDS OF MODERN SYRINGES AND AUTOINJECTORS
When designing a syringe or autoinjector, there are several requirements the developer must meet; not only must the device deliver the contained drug consistently and reliably, for a prefilled device, it must keep the contained drug sealed and sterile for the duration of its shelf life. This means that all components must be fully compatible with the drug, offer impeccable reliability and be suitable for manufacturing, fill-finish, storage and delivery processes.
Excellent Seal Integrity
For elastomeric stoppers, the absolutely critical aspect is how well they form and maintain a seal within the barrel of the syringe. Poor seal integrity could lead to drug leakage or the therapeutic being contaminated by outside substances. A key indicator of seal integrity for an elastomer is its compression set and stress relaxation – compression set measures the permanent deformation once a compression force is removed, while stress relaxation measures the sealing force over time when strain is held constant. Compared with other medical-grade thermoplastic elastomers, Santoprene TPV demonstrates a very low compression set and better stress relaxation, meaning that Santoprene TPV components show minimal change after deformation, maintain seal integrity over longer periods of time and minimise the risk of leaks or failures (Figure 4). Santoprene TPV can maintain excellent seal integrity and is therefore ideal thermoplastic elastomer for use in conventional, safety and prefilled syringes and autoinjectors.
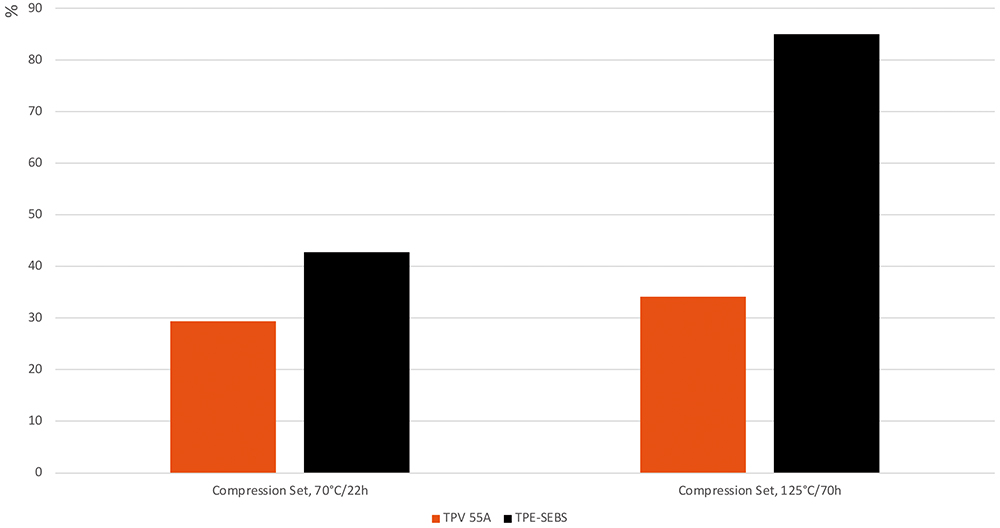
Figure 4: TPV has better compression set and long-term sealing performance compared with other thermoplastic elastomers.
“To keep up with device developers, materials providers have had to push further with their own innovation, creating more advanced medical-grade materials that can offer the reliability and flexibility to meet the demands of modern drug delivery devices.”
Low Coefficient of Friction
Next, the stopper must facilitate reliable, consistent delivery of the contained therapeutic. The fundamental aspect here is the material’s coefficient of friction, which dictates the break-loose and glide forces. A high-quality stopper should have a low coefficient of friction to optimise usability, ensuring that patients and healthcare providers can depress the syringe plunger smoothly, without the need for excessive force. Santoprene TPV demonstrates this critical quality.
This aspect is critical for devices targeting self-administration by patients, especially for geriatric patients or those with limited dexterity. Often for indications targeting these populations, drug developers will opt for an autoinjector rather than a simple PFS, where the patient only needs to press a button and a spring or other driving force automatically depresses the plunger. Autoinjectors are also frequently used in emergency applications, such as delivering adrenaline (epinephrine) after an allergic reaction, where all device components must be optimised to ensure that the mechanism operates reliably upon device activation, even by an injection-naive user.
When device functionality would be improved by a lower coefficient of friction, a common approach to achieve this is to use an external lubricant, which has traditionally been silicone oil.1 However, the interaction of silicone oil with biologics has come under scrutiny, particularly in PFSs with a longer shelf life. As such, the ideal solution would be to minimise the need for lubrication altogether if possible.
High Manufacturability
As part of optimising the stopper for use in a syringe or autoinjector, the device developer may opt for a wide variety of stopper designs. Santoprene TPV demonstrates high-precision dimensional tolerances, which can enable developers to use their ideal stopper design with fewer concessions to manufacturability.
Thermoplastic elastomers, such as Santoprene TPV, also open the door to advanced moulding techniques unsuitable for the thermoset rubbers currently in use. One such technique is over moulding, in which a layer of Santoprene TPV can be moulded around an existing polymer component, enabling device developers to get the most of their materials and consolidate the overall number of parts in the device, which can contribute to improved reliability.
Another key aspect of manufacturing PFSs is sterilisation. All components in contact with the drug must be fully sterilised to eliminate the risk of contamination. Pharmaceutical manufacturers employ a variety of sterilisation techniques. Santoprene TPV is suitable for steam, gamma and ethylene oxide sterilisation, giving the manufacturer the flexibility to use the sterilisation method most suitable for the project overall.
Regulatory Compliance
One of the major hurdles that must be overcome by any pharmaceutical product on its way to market is meeting the demands of regulators. Celanese fully supports its customers by ensuring that Santoprene TPV meets all the necessary regulatory standards set out by the US Pharmacopeia, ISO and US FDA. Santoprene TPV has USP Class VI and ISO 10993-4, 5, 6, 10 and 11 compliance, and a drug master file is maintained with the FDA. Furthermore, Celanese can provide a notification of change on medical grades to give peace of mind to device manufacturers on material qualification.
CONCLUSION
The modern drug delivery landscape has placed a significant emphasis on the role of PFSs and autoinjectors as a key part of meeting the needs of pharma companies and patients alike. The trend towards more patient-centric care focused on self-administration at home demands injection devices that are robust and reliable enough to be used by laypeople rather than requiring the expertise of a healthcare professional in a hospital environment. Simultaneously, the rapid growth of the biologics sector has demanded drug delivery devices suitable for containing and delivering these large, often delicate molecules.
The drug delivery industry is rising to the challenges presented by these trends by innovating on traditional designs, making safer, more efficient, more reliable syringes. To keep up with device developers, materials providers have had to push further with their own innovation, creating more advanced medical-grade materials that can offer the reliability and flexibility to meet the demands of modern drug delivery devices.
Elastomers are no exception to this advancement. Modern thermoplastic elastomers, such as Celanese’s Santoprene TPV, offer significant advantages over traditional thermoset rubbers when developing syringes and autoinjectors, especially in terms of manufacturability. Santoprene TPV offers excellent seal integrity and coefficient of friction, while also using thermoplastic manufacturing processes, with a single feedstock, reduced overall manufacturing costs, lower energy consumption and greater recyclability options.
As a well-established player in medical-grade materials, Celanese is able to help customers select the ideal grade of Santoprene TPV to meet the specific needs of their device. In partnering with Celanese, syringe and autoinjector developers gain access to a wealth of knowledge and expertise, as well as full regulatory support to facilitate the smoothest possible journey from device development to manufacture to market.
REFERENCE
- Thornton JD, Jonsen D, Sakhrani V, “Next-Generation Lubrication Solutions”. ONdrugDelivery Magazine, Issue 61 (Oct 2015), pp 10–15.