Citation: McGowan M, “30 Years in the Making – an Inside Perspective on the Emergence of Autoinjectors”. ONdrugDelivery Magazine, Issue 101 (Oct 2019), pp 20-23.
Michael McGowan gives a perspective on the emergence of the autoinjector as a key component of the drug delivery industry, in the context of autoinjector pioneer SHL Group celebrating its 30th anniversary this year – a journey of rapid development that reflects the growing demand for advanced drug delivery systems in the healthcare market.
“It was already recognised back in the early 1990s that combining a prefilled syringe with a mechanical autoinjector would present a number of important challenges to ensure the safe and effective delivery of the drug.”
The prevalence of self-injection in the home setting has developed considerably in recent years and the advent of digitally enhanced, connected devices will certainly take the industry in new directions that were unimaginable until recently. However, looking back over the past 30 years, to the end of the 1980s, the prefilled syringe was still in its relative infancy and the first reusable insulin pen devices were only just emerging on to the market. As a primary drug container, the prefilled syringe was used principally to deliver calcium and sodium heparins as well as a broad range of vaccines. The global prefilled syringe market size was at that time under 200 million units per year and the dominant barrel sizes were 0.5 mL and 1 mL standard.
However, the advent of low-molecular-weight heparins around the late 1980s and early 1990s resulted in a marked acceleration of the prefilled syringe market. This led to the introduction of what is now commonly referred to as the 1 mL long barrel dimension. Heparins still represent around 50% of the prefilled syringe market, which, according to IQVIA, now exceeds 2.2 billion units.
EARLY AUTOINJECTOR PROJECTS ACCELERATE THE LEARNING CURVE
It was also around this time that one of the world’s leading pharmaceutical companies started to investigate the use of a prefilled syringe in conjunction with a self-injection device for a new anti-migraine drug that was in development. Because of the unpredictable nature of migraine attacks and the improved outcomes experienced after a rapid administration of the injectable form of the drug, it was recognised that self-administration would be advantageous for the migraine patient. However, it was also understood that the potentially debilitating effects of a migraine attack could significantly reduce a person’s ability to think clearly and to follow a multi-step injection preparation procedure.
One of the early presentations of this anti-migraine drug consisted of a standalone prefilled syringe that had to be manually inserted into a reusable injector device. This relatively complex procedure was still less than ideal for users who were suffering from a migraine. Subsequent improvements during the early and mid-1990s saw the introduction of a new generation of self-injection devices that was much easier for patients to use.
“As a leader in the industry, SHL has been at the forefront of autoinjector development, supporting customers with solutions best suited to their requirements for either automatic or manual needle insertion.”
It was already recognised back in the early 1990s that combining a prefilled syringe with a mechanical autoinjector would present a number of important challenges to ensure the safe and effective delivery of the drug. At the outset, a glass prefilled syringe was designed for manual use where the user could quite easily adapt their technique to manage natural variances in the characteristics of the prefilled syringe. Examples of these include the variable force required to remove the elastomer needle shield or the changing pressure required to fully depress the plunger rod to inject the drug. For a prefilled syringe to work properly with a mechanical autoinjector, syringe manufacturers would need to closely manage critical process parameters, such as the siliconisation of the barrel and the plunger stopper.
It was also clear that the syringe’s dimensional tolerances, as well as the variance in the strength of the glass finger flange, would present further challenges for the use of the syringe in the autoinjector. The stress introduced into the glass barrel during the manufacturing process could lead to breakage when subjected to the high-force delivered by the mechanical spring of the autoinjector. Once again, it was vital to understand and manage the manufacturing process of the prefilled syringe in combination with the design of the autoinjector for the two to function well together. For example, the prefilled syringe used in the anti-migraine autoinjector project referred to earlier, was adapted to have a small, round and unclipped flange – the purpose of which was to generate less structural stress in the barrel and to distribute more evenly the force generated by the autoinjector spring. The small round flange syringe was developed but its introduction inadvertently introduced a new manufacturing challenge as the standard finger flange was used to transport the syringe during the production and processing steps.
Thinking back on my experience as a business development manager with the prefilled syringe manufacturer at the time, I am convinced that the experience of working in collaboration with a leading pharmaceutical company on the anti-migraine autoinjector project helped them to improve considerably their understanding of their own products and manufacturing processes. To this day, the rigorous investigation of the dimensional and functional variances of the prefilled syringe remains an important part of any autoinjector development project. It is paramount to identify and understand the potential challenges these variations will have on autoinjector design. The prefilled syringe has progressed tremendously over the intervening two decades and many options, both glass and polymer, are now available to optimise the syringe and device combination.
INTEREST IN AUTOINJECTORS GROWS BUT COMMERCIAL SUCCESS REMAINS ELUSIVE
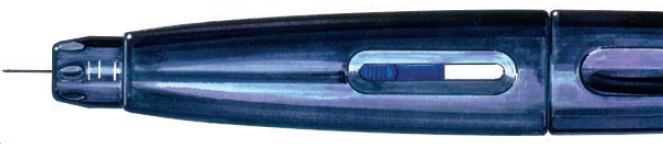
Figure 1: SHL’s first injector product was launched with an ED drug in 1996.
The interest of the pharmaceutical industry in the self-administration of drugs did not waver during the 1990s when a number of projects were started, but then abandoned, for a variety of reasons. Mainly, the technical challenge of producing a reliable device that could work in conjunction with the prefilled syringe was not easy to achieve cost-effectively. Thus, the number of self-administration products on the market remained few.
However, in 1996, SHL’s first commercialised self-injection device was launched on the market with a drug prescribed for erectile dysfunction (Figure 1). The strong customer-centric approach of the drug manufacturer combined with the entrepreneurial skills of SHL helped drive this high-profile project through to commercialisation. Working together with the pharma partner, the device was designed by SHL to be easy to use, non-medical in appearance, and less intimidating before and after use. The entire project was completed from start to finish in around nine months.
THE ERA OF BIOLOGICS –A WINDOW OF OPPORTUNITY FOR AUTOINJECTORS
Although many events contributed to the development of the autoinjector market, it was the advent of biologics at the end of the 1990s and throughout the 2000s that really accelerated the pharmaceutical industry’s interest in self-injection systems. At the same time, awareness of injection safety as a result of the Occupational Safety and Health Administration (OSHA) guidelines was also increasing. The new generation of drugs coming to the market were approved for long-term treatment of chronic diseases, and self-injection devices integrating safety features from needlestick injury, would become an integral part of creating market differentiation.
Some of the first biologics that were introduced were targeting rheumatoid arthritis patients who suffered from quite specific dexterity difficulties. The discussions between the biopharmaceutical companies and the device suppliers were therefore initiated quite naturally at an early stage in the drug development process. The end user needs were relatively well defined, but the technical challenge of meeting these needs in a self-injection device built around a prefilled syringe remained significant. For example, the interaction of the biologic drug with the syringe materials and the silicone lubricants presented difficulties that have required prefilled syringe manufacturers to develop new product offerings to address the specific needs of biologic compounds.
THE EVOLUTION AND REFINEMENT OF THE AUTOINJECTOR
Biologics, on the whole, are available only in an injectable form and often command a relatively high selling price. It is important therefore that the self-injection device functions reliably so that users are able to use the device successfully without the supervision of a healthcare professional. The first autoinjector devices introduced to the market typically required three or four steps that were usually sequence-dependent (Figure 2).
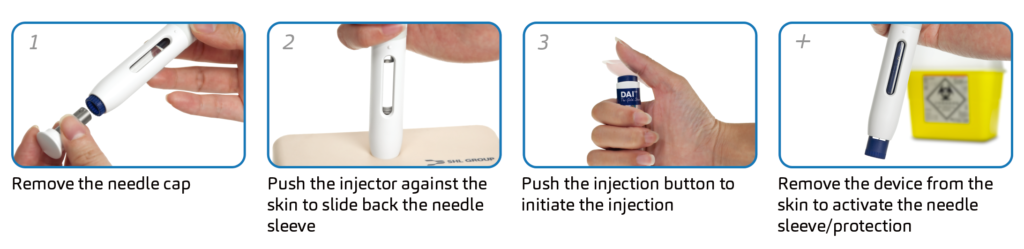
Figure 2: Injection sequence of a three-step autoinjector.
As experience with autoinjectors grew and further insight was gained into the preferences of end users, their designs became simpler, with fewer steps to complete the injection. For example, SHL’s DAI®, a three-step, button-activated autoinjector first introduced in 2006, has continued to evolve over the years to give rise to a number of different designs and new product families. More recent development projects have shifted to two-step solutions where the users simply uncap and inject to complete the administration of the drug.
DAI® is an example of automatic needle insertion where the needle is inserted into the skin by the force of the spring, while Molly® utilises a manual insertion method where the needle is pushed into the skin by the action of the user pushing down on the injector. There is still much discussion on the merits of automatic needle insertion versus a manual needle insertion and, in SHL’s experience, both options remain valuable and are accepted by patients for different reasons, such as device size, sound, insertion control and more. As a leader in the industry, SHL has been at the forefront of autoinjector development, supporting our customers with solutions best suited to their requirements for either automatic or manual needle insertion.
BIOLOGICS AND THE ERA OF BIOSIMILARS
Over the past 10-15 years, the number of approved and commercialised combination products in prefilled syringe-based autoinjectors has increased substantially. Over 30 drugs have been commercialised in SHL Group devices alone, reflecting the growth and dynamism of the market. The therapy areas in which autoinjectors are used have broadened over the period to include many auto-immune/inflammatory diseases and conditions such as multiple sclerosis, migraine, Type 2 diabetes, anaemia and hypercholesterolaemia, to name a few.
“As digital healthcare becomes a reality, self-injection devices with integrated connectivity will become an important element of the digital ecosystem.”
Based on experience in developing and commercialising projects, SHL understands that each device project is unique and that, in many ways, each development is a bespoke collaboration between the device supplier and drug company. However, many elements of a project are quite common and a recent “Voice of Customer” survey conducted by SHL Group highlighted the interest from the pharmaceutical industry for platform products that can be customised to a given drug or customer need. This concept is not new. For example, SHL’s preconfigured device technology, Molly®, has been successfully adapted and customised across a number of projects for a number of years already.
One of the drivers of interest in preconfigured products is certainly coming from the growth in the number of biosimilars entering the market. As the first wave of biologics comes off patent, biosimilars are looking to gain market share based mainly on their cost-effectiveness. The biosimilars companies, therefore, need a device with a proven track-record of reliability, end user acceptance and a short but cost-effective development timeline. The need for customisation remains a relevant element of the development process, the extent of which will depend on the customers’ needs, timelines and commercial strategy.
CONCLUSION
As medical research progresses and our understanding of some of today’s major healthcare challenges increases, the development of complex biologics will continue. Likewise, novel delivery devices will be needed to deliver these compounds. The mechanical autoinjector market is likely to branch off into many different routes to accommodate the specific properties of compounds that will emerge from pharmaceutical research.
As SHL Group celebrates its 30th anniversary, the company is preparing for the next phase of its expansion through investment in state-of-the-art production facilities in Liufu, Taiwan, the establishment of a new global headquarters in Zug, Switzerland, and through its active partnerships in the digital healthcare sector.
For a number of years already, there has been a trend towards less frequent injections – weekly, monthly or even quarterly injections will become the norm. Increasing drug viscosity and larger injection volumes may also result from current research, as formulation scientists find ways to get new compounds into an injectable format. Electromechanical autoinjectors, liquid/dry mixing autoinjectors, on-body injectors and cartridge-based autoinjectors will all probably find their space and place in the market alongside the traditional, prefilled syringe-based mechanical devices (Figure 3).
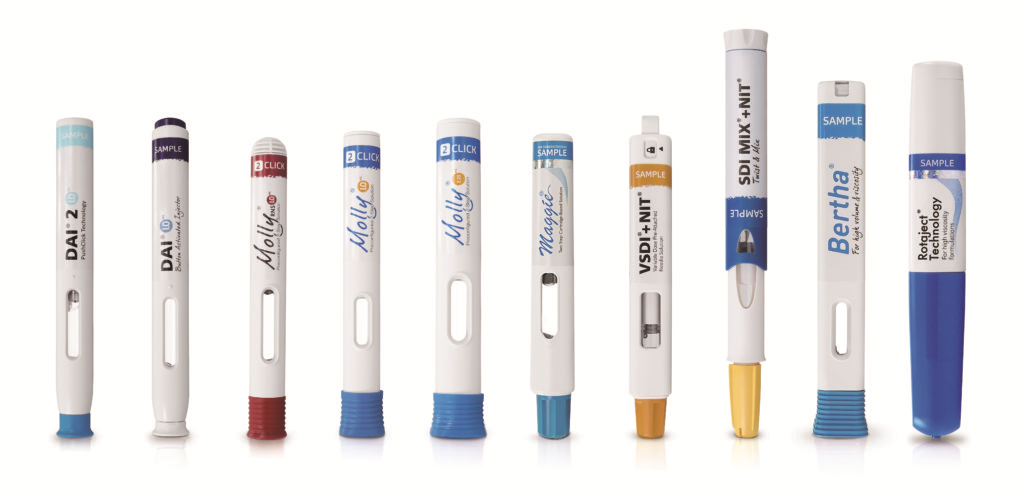
Figure 3: With 30 years in the industry, SHL offers range of autoinjectors for prefilled syringes and cartridges.
As digital healthcare becomes a reality, self-injection devices with integrated connectivity will become an important element of the digital ecosystem. Evolving from simple Bluetooth-enabled devices that connect to self-management applications, the smart autoinjector of the future will be able to provide wide-ranging data to key stakeholders on the injection, handling errors, adherence, prescription renewal, reimbursement, clinical trial reporting, complaint management and more. The possibilities are endless and the implications are far-reaching.
The unique position of drug delivery devices within this future digital health ecosystem will certainly result in a new phase of growth for the industry. As SHL Group celebrates its 30th anniversary, the company is preparing for the next phase of its expansion through investment in state-of-the-art production facilities in Liufu, Taiwan, the establishment of a new global headquarters in Zug, Switzerland, and through its active partnerships in the digital healthcare sector.