Citation: Caelers A, “Regulatory Affairs: the Underestimated Role of Primary Packaging”. ONdrugDelivery Magazine, Issue 102 (Nov 2019), pp 51-54.
Antje Caelers explains how increasingly complex products and production chains, restrictive industry standards and differing regulations mean that regulatory affairs are becoming more important than ever and manufacturers need to work with a partner who is well versed in both primary packaging production and regulatory requirements.
“Primary packaging manufacturers who have established a regulatory affairs department offer their customers – manufacturers of food, pharmaceuticals and medical products – added value.”
Primary packaging materials are either in direct contact with food, medicines or medical devices or could come into contact with them – and must therefore comply with strict regulations. The regulations are just as manifold as the packaging itself. The goal, however, is the same for everyone involved, from the drug manufacturer to regulatory authorities to the packaging manufacturer: safety, quality, function and compatibility are the focus of all efforts. Those who have specialised in the development of primary packaging materials should know for which purpose and for which final product the packaging is intended. Packaging that fits perfectly for a certain food product or dietary supplement is not automatically suitable for pharmaceutical contents.
REGULATORY AFFAIRS – AN IMPORTANT COMPETENCE
What does a manufacturer of food, pharmaceuticals or medical devices need to launch their product, including primary packaging, safely and in compliance with the directives? First, they need a partner for primary packaging production who has special expertise in all regulations for the various dosage forms and applications, and is able to develop safe solutions.
This is the task of the regulatory affairs department: it must ensure that all materials used comply with the required regulations, that the required limit values are adhered to and that this is consistently documented –from different regulations for food contact materials to pharmaceutical pharmacopoeias and Drug Master Files of the US FDA. Primary packaging manufacturers who have established a regulatory affairs department offer their customers – manufacturers of food, pharmaceuticals and medical products – added value. Not only do they receive tailor made packaging but they can also rely on the fact that all materials comply with the applicable guidelines.
Customers receive a declaration of compliance that ensures conformity with the applicable regulations and in which all regulations applicable to the raw materials used are listed. In addition, all suppliers’ compliance declarations are stored and updated in a database, making them available at any time.
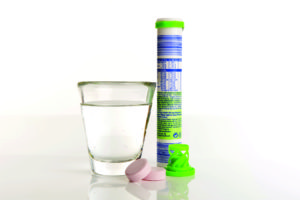
Figure 1: Primary packaging materials must not transfer any ingredients or constituents that could impair the health of consumers.
FOOD CONTACT MATERIALS
Primary packaging materials for food fall under the term “food contact materials” and are articles in daily use which come into contact with food, such as plastic tubes for nutritional supplements. They must not transfer any ingredients or constituents that could impair the health of consumers (Figure 1). Further, they must not result in any unacceptable modification of the food product or adversely affect its odour or taste. Accordingly, food contact materials must be manufactured in compliance with GMP, as required by Regulation (EC) No 2023/2006.
The general requirements for the safety of food contact materials are laid down in Regulation (EC) No 1935/2004. For plastic primary packaging manufacturers, Regulation (EU) No 10/2011 is decisive. It includes a list of authorised additives. To ensure that food contact materials do not pose a health risk, limit values have also been defined. Before substances are included in the register, a comprehensive health assessment is performed by the European Food Safety Authority (EFSA).
PRIMARY PACKAGING IN THE PHARMACEUTICAL INDUSTRY
Primary packaging materials for pharmaceutical products are considered an integral part of the drug and therefore subject to special requirements. In addition to the active ingredient and formulation, the packaging – especially the primary packaging – also influences the quality, efficacy and safety of a drug (Figure 2). This is illustrated by the manifold requirements of the European Pharmacopoeia (EP) for medicinal products and medical devices as well as the detailed characterisation which a manufacturer has to submit when applying for market approval of a new drug.
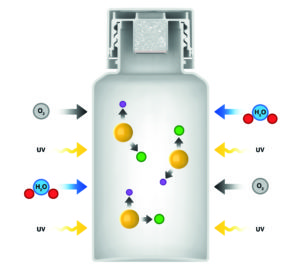
Figure 2: In addition to the active ingredient and formulation, the primary packaging also influences the quality, efficacy and safety of a drug.
The area of regulation is highly complex because the regulatory fundamentals for pharmaceutical packaging materials result from many laws and guidelines. In addition, each guideline on drug development, manufacture and testing also includes information on the requirements for primary packaging materials.
Primary packaging materials have a crucial protective function. They protect drugs from loss of efficacy due to oxidation, from exposure to light, and from microbial contamination. An interaction between packaging and medication that alters essential properties of the packaging or the product is not permitted. The packaging materials must not release toxicologically relevant substances such as bisphenol A, carcinogens or mutagenic substances into the formulation, which has to be proved by the pharmaceutical manufacturer when applying for marketing authorisation for a new drug. If the primary packaging performs other tasks in addition to the container function, such as dosage, these must be maintained until the end of the shelf life of the drug.
“In addition to the active ingredient and formulation, the packaging – especially the primary packaging – also influences drug quality, efficacy and safety.”
PHARMACEUTICALS, MEDICAL DEVICES AND COMBINATIONS
Determining the applicable regulations requires a distinction between medicinal products and medical devices, which is unfortunately not always obvious. Drugs (according to Regulation 2001/83/EC) act pharmacologically, immunologically or metabolically. Medical devices, in turn, (according to Regulation 2017/745) realise their intended principal use primarily by physical means.
Items such as dental products, bandages and laboratory diagnostics are considered medical devices, as well as pacemakers, implants, products for injection, transfusion and dialysis, and human medical instruments. There are also combinations of drugs and medical devices – such as inhalers for asthma or adrenaline injectors for the treatment of anaphylaxis. Depending on their administration and effect, they are subject to different regulations from classical medicines.
PHARMACOPOEIAS – FUNDAMENTAL RULES
A pharmacopoeia is a collection of recognised pharmaceutical rules concerning the quality, testing, storage and labelling of drugs and the substances, materials and methods used for their production and testing. The EP and the US Pharmacopeia (USP) are particularly relevant. They include, for example, special test methods for plastics (USP, EP) and desiccants (USP).
EU guideline CPMP/QWP/4359/03 for the development of plastic primary packaging differentiates between solid and liquid as well as between oral, topical, ophthalmic, inhalation and parenteral dosage forms. Depending on the dosage form, certain information or tests may be required. The testing requirements of pharmacopoeias for non-solid dosage forms for parenteral or inhalation applications are much more comprehensive and stringent than for solid dosage forms for oral use. The USP also places additional requirements on the biological reactivity of polymeric primary packaging components.
DRUG MASTER FILES – NOT MANDATORY, BUT DECISIVE
The management and maintenance of the DMF is especially important in the pharmaceutical industry. The DMF is a document submitted to the FDA that documents the pharmaceutical production and quality assurance of drugs for the purpose of marketing approval. In a DMF Type III, for example, confidential information can be stored specifically for primary packaging. Once the letter of authorisation has been issued by the DMF owner, the FDA, as a third party, has the opportunity to verify its contents.
The creation of a DMF is not legally binding. However, it is of great relevance for companies operating globally, as the document is required for all drugs that are intended to receive marketing authorisation in the US. The preparation is very complex. Its main purpose is to protect intellectual property, such as the manufacturing process, for the benefit of the DMF owner. Accordingly, partners entrusted with the production of the primary packaging material should not only be familiar with the subject of DMF and be able to draw on the corresponding expertise. They should also deposit all standard products relevant for the packaging of pharmaceuticals that are to be registered in the US in DMFs Type III and update them on a regular basis.
MDI AS EXAMPLE FOR REGULATORY AFFAIRS
An example helps to illustrate the complexity of the regulations that need to be considered for primary packaging: a metered dose inhaler (MDI) is a device which delivers medicine directly into the lungs. It consists of a pressurised cartridge containing a solution or suspension of the active substance. The active ingredient is released by propellant gas. The cartridge is anchored in a plastic housing, which is connected to a mouthpiece. When the cartridge is pressed down, a valve delivers a fixed dose of the active ingredient in a fine mist, which is inhaled into the lungs via the mouthpiece.
From a regulatory perspective, we must distinguish between the packaging type in which the MDI inhaler is provided pre-assembled (for single use) and the packaging type where the plastic housing is added to the packaging of the cartridge containing the drug without being assembled. The first case refers to a fixed combination of drug and medical device, which is regarded as a drug according to the requirements of the new Medical Device Regulation (MDR) 2017/745.
The term “combination product” is not legally defined in the EU. A distinction is made between:
- a medical device containing a complementary substance which is a drug or a derivative of human blood or human plasma
- a product intended to supply a drug, where the product and the drug form a combined product intended exclusively for use in this combination.
For our example, this means that the assessment is carried out as part of the drug approval process (Figure 3). This implies that all test results according to ISO 10993 must be available in the approval documentation. This ISO standard is particularly relevant for manufacturers of medical devices and for testing laboratories – with the aim of assessing the biological compatibility of the materials with the body.
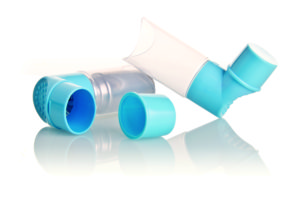
Figure 3: From a regulatory perspective, the assessment for the MDI is carried out as
part of the drug approval process.
Thus, not only products, but also starting materials for the manufacture of medical devices and pharmaceuticals are examined. Accordingly, it is important to ensure that raw materials already have a statement on their use in medical devices and an ISO 10993 test report. CE marking of the medical device components is not required in this case.
Since the inhaler has to be regarded as a drug for regulatory purposes, USP and EP apply – meaning that the materials should contain a confirmation of the relevant chapters. Moreover, regarding primary packaging materials for parenteral and inhalation preparations, only materials of the USP “class VI” (strictest compatibility class) should be used.
PRIMARY PACKAGING – MUCH MORE THAN A CONTAINER
The example of the MDI shows that primary packaging is much more than a container for a particular formulation. It also shows the effort behind drug approval. It is no longer sufficient to test only the substances contained in the medicinal product. Primary packaging plays an increasingly important role, which requires appropriate expertise and experience (Figure 4). After all, primary packaging has an influence on the quality, safety, compatibility and function of the product that should not be underestimated.
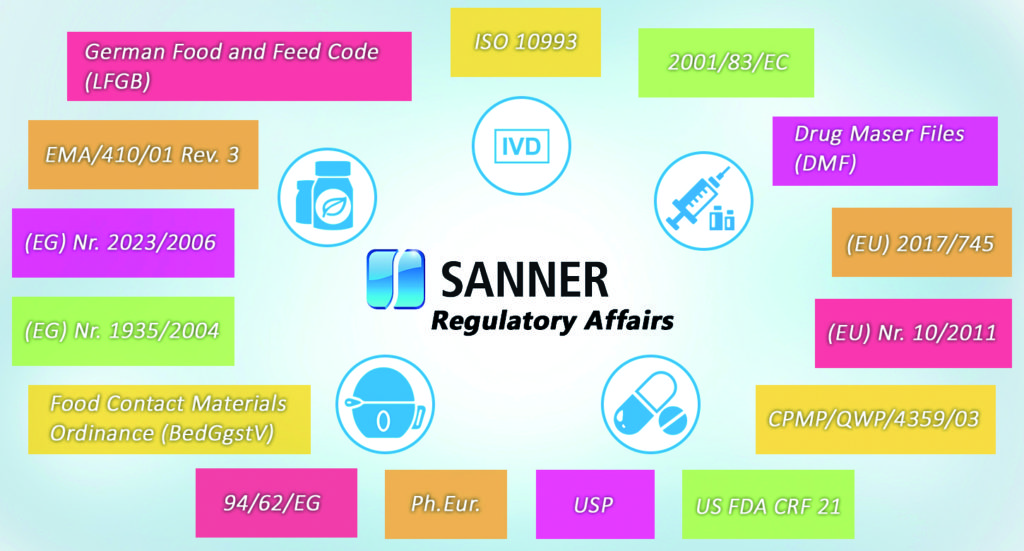
Figure 4: Primary packaging plays an increasingly important role, which requires appropriate regulatory expertise and experience.
The increased requirements imposed on products and primary packaging materials both enable and require constant innovation – and, above all, a partner that is familiar with the regulations. This makes the role of regulatory affairs all the more important. Fulfilling this role requires many years of experience in the development and manufacture of primary packaging for food, pharmaceuticals and medical products. At the same time, profound knowledge of and experience with the different regulations is needed. Continuous updates of the DMF should be just as self-evident as providing advice on regulatory affairs from the very beginning of packaging development. This is the only way to ensure efficient implementation and mutual satisfaction.
Previous article
SUCCESS FACTORS FOR THE YPSOMATE FAMILY OF AUTOINJECTORSNext article
WHEN EVERY SECOND COUNTS…