Citation: Roe MJ, “Challenges in High-Viscosity, High-Volume Drug Delivery”. ONdrugDelivery, Issue 125 (Oct 2021), pp 40–43.
Michael Roe discusses the development of the Aerio™ Platform of gas-powered injection systems.
In 2020, biologics accounted for more than half of the world’s 20 top selling drugs.1 The molecules that comprise most biologics, including monoclonal antibodies (mAbs), have molecular weights in the hundreds of thousands of Daltons (Da). As the concentration of drug formulations increases, so does the drug’s viscosity or “thickness”. The higher the viscosity, the greater the force required to push the drug through the narrow cannulas typically used for parenteral delivery, especially at lower temperatures.
The force needed to push a fluid through a cylinder is governed by the Hagen-Poiseuille equation:2
Where:
- F is the plunger force
- L is the length of the needle
- μ is the viscosity
- Q is the flow rate
- A is the area of the plunger
- D is the internal diameter of the needle.
Figure 1 shows the pressure drop needed to deliver the indicated volume in 15 seconds. Increased viscosity requires a corresponding increase in pressure to ensure delivery of the volume in the same length of time. For viscous fluids (50 cP), the required pressure can be as high as 600 psi for a 2.25 mL volume.
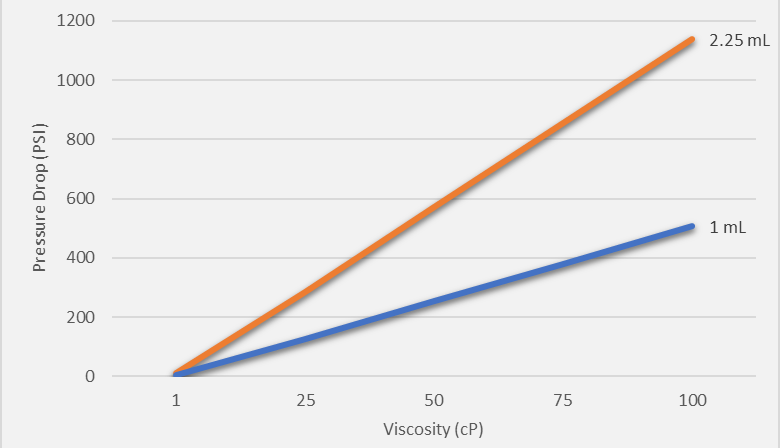
Figure 1: Pressure drop needed to deliver 1 mL or 2.25 mL of fluid of indicated viscosities in 15 seconds.
Many higher molecular weight formulations can also be susceptible to molecular shear at higher flow rates.3 Shear force can break apart weaker hydrogen bonds present in the structure, which can denature or “tear” proteins. This can result in aggregation and a loss of solubility, to the point that the protein can no longer perform its intended function. This problem may be exacerbated by the move to smaller cannulas and quicker injection times, which require an increased flow rate of fluid through the needle.
Concurrent with the rise of higher concentrations of mAbs has been a shift in delivery trends. Currently, large doses of high-concentration drugs are most commonly administered intravenously (IV) by a healthcare professional at hospitals, clinics and infusion centres. Most IV infusions are given over several hours, during which time the patient must stay at the infusion location and remain relatively sedentary.
Even before the covid-19 pandemic upended daily life, such infusions could be inconvenient and time-consuming for both patients and healthcare professionals.4,5 Pharmaceutical companies have responded by introducing formulation technology that allows high-volume IV formulations to be administered instead via subcutaneous injection over the course of minutes rather than hours.4 In addition, market trends indicate a move towards less frequent dosing schedules to increase convenience and, potentially, prescription adherence.4 Pharmaceutical companies are responding to these pressures by increasing the duration of activity of their products through encapsulation and other timed-release technologies. The result is the potential for longer periods between injections, during which time it is plausible that the patient or caregiver might become less familiar with the correct operation of the injector.
Biopharmaceutical and drug delivery stakeholders have therefore sought injection systems that improve high-volume and high-viscosity performance while simplifying the self-injection process to facilitate home use. To address these needs, many injection systems have emerged with novel drives (e.g. compressed gas, electromechanical, chemical) that enable the delivery of viscous formulations at a constant rate while maintaining a small form factor and improving ease of use.
“Kaléo successfully developed and marketed a line of gas-powered autoinjectors. This same proven technology is used in Kaléo’s Aerio Platform of pressurised gas-powered injection devices.”
Devices for the subcutaneous administration of medicinal products have typically consisted of two types: needle-based and needle-free, with needle-based products comprising the bulk of the offerings. Within the needle-based class, there are manual injection pens and autoinjectors. The manual injection pens are used primarily by patients with diabetes who require multiple injections of small, precise doses during the day. Autoinjectors typically administer a dose that does not need to be adjusted and are commonly used by individuals with chronic or emergent (life-threatening) conditions. A pressurised gas-powered autoinjector was envisioned by twin brothers with severe food and other allergen sensitivities. They sought a compact adrenaline autoinjector to facilitate transport while also incorporating features that would enhance ease of use. The resulting company, Kaléo, successfully developed and marketed a line of gas-powered autoinjectors. This same proven technology is used in Kaléo’s Aerio Platform of pressurised gas-powered injection devices.
As the container diameter increases – as often happens with larger containers – the force at the plunger must also increase to counter the increase in the plunger’s surface area and provide consistent pressure. A conventional device would require the use of larger, higher-force springs. A gas-powered device would be largely unaffected by the container diameter because the same gas pressure applied to a larger area results in a higher force; thus, gas-powered devices are largely immune to the impact of container diameter. This attribute allows the use of a larger diameter container in the design, which reduces overall length.
The patented non-coaxial layout of the Kaléo system can reduce the overall length of the device by placing the drive system adjacent to, rather than in line with, the primary container. The Aerio Platform does not require a separate piston to drive the plunger, resulting in a device that, in many instances, is only slightly longer than the container/needle assembly. These features provide greater flexibility to the designer to tailor the device to the unique aspects of the use/carry environment of the therapy under consideration.
In addition, while spring force typically drops with plunger travel distance, gas pressure remains relatively constant throughout the injectable length. These factors make pressurised gas well suited for the delivery of higher volumes of high-viscosity formulations from a variety of primary container closures.
“Using the same proven gas-powered technology used in the company’s US FDA-approved products, along with additional enhancements, Kaléo has developed the Aerio line of injection systems to enable injection of larger volumes of high-viscosity formulations.”
Using the same proven gas-powered technology used in the company’s US FDA-approved products, along with additional enhancements, Kaléo has developed the Aerio line of injection systems to enable injection of larger volumes of high-viscosity formulations. The Aerio Platform consists of four different types of autoinjector: AerioUno (single container), AerioDuo (dual container), AerioMix (dual chamber) and AerioOn-body (Figure 2).
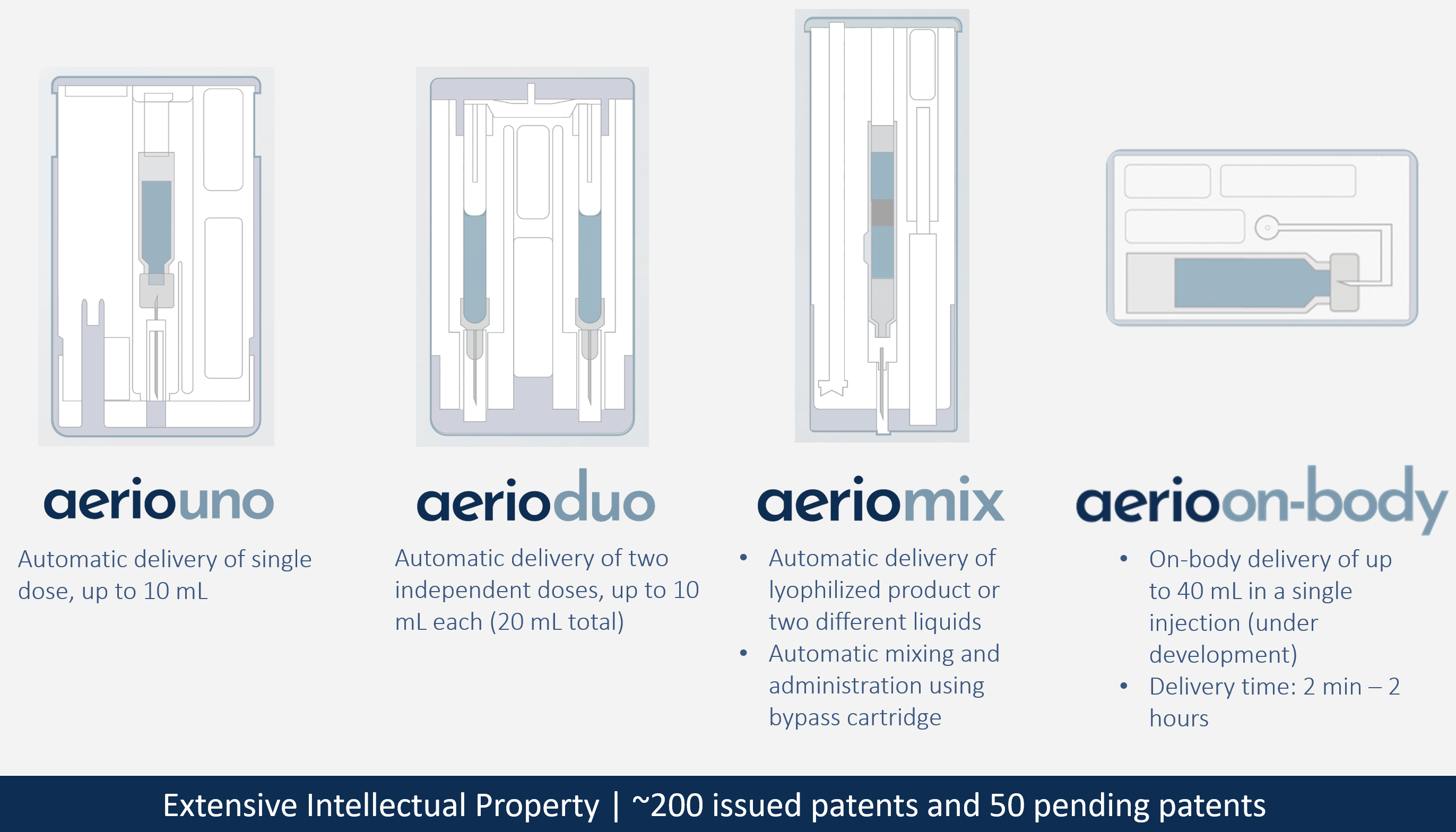
Figure 2: The Aerio Platform from Kaléo.
The Aerio Platform is designed to have the following capabilities:
- Constant delivery rate through gas-powered technology
- Reliability
- Accurate and precise administration of dose volumes ranging from 0.1–40 mL
- The ability to deliver high-viscosity formulations through a range of needle gauges
- Potential flow velocity ranging from 1 mL/min up to 90 mL/min
- The ability to use standard or custom syringes or cartridges
- Rapid automatic needle insertion and retraction (the patient never sees the needle)
- Injection steps tailored to the use environment
- Form factor flexibility to suit a variety of patient needs.
All Aerio devices use Kaléo’s proprietary non-coaxial configuration, which enables a shorter overall length than conventional spring-powered autoinjectors. This, combined with the company’s proprietary plunger-drive technology, means that in many instances, the Aerio device is only slightly longer than the combined length of the drug constituent container and the needle. In addition, the pressure in the gas cylinder can be modified to accommodate larger volumes and higher viscosities without an increase in cylinder size, whereas the spring in a conventional autoinjector must typically increase in length or diameter.
This results in a compact unit that is designed to be easy to handle and configure according to specific patient/caregiver needs.
With gas power, the Aerio Platform has the ability to deliver high-volume formulations at a constant rate, regardless of injection stroke or delivery time. This helps make the injection more predictable and comfortable, as there is no immediate “rush” of flow at the start, as can be experienced with the high initial spring force that comes with conventional autoinjectors.
As part of a post-marketing commitment to the FDA, Kaléo evaluated the reliability of two approved autoinjectors and verified 99.999% reliability (otherwise known as “five nines”) for successful injection. This was documented using a quantitative fault tree analysis of the manufacturing process to assess the system-level reliability. Additionally, the two products were subjected to “worst-case” sequential testing to mimic the results of product condition throughout the shelf life. The result of this work was verification that the products met the FDA’s draft requirement for reliability for emergency-use injectors. The FDA recently published its draft guidance containing this recommendation for emergency-use autoinjectors.6 Kaléo was also chosen to develop a 10 mg naloxone autoinjector using the Aerio Platform for the US Department of Defense. During this development, Kaléo has demonstrated that its 10 mg naloxone autoinjector meets the rigorous requirements of MIL-STD-810H testing.7 This same approach to reliability and ruggedness would be applied to the Aerio Platform to assure consistent device performance.
The Aerio Platform can use either cartridges or syringes as its primary container, with drug volumes of 1–40 mL.
The primary container can be either standard or custom and can be made of conventional glass or polymer technology. Furthermore, any standard or custom elastomer can be used to seal the container. The power of the pressurised gas technology can also enhance the ability to inject high-viscosity formulations through small bore needles.
“Through Kaléo’s proprietary gas flow modulation technology, Aerio devices can control the drug injection flow to protect formulations that may be damaged by high-velocity molecular shear.”
Through Kaléo’s proprietary gas flow modulation technology, Aerio devices can control the drug injection flow to protect formulations that may be damaged by high-velocity molecular shear.
In addition, Kaléo has developed proprietary connected health technology capable of the following:
- Automatic pairing with a mobile device to facilitate setup
- Motion detection to confirm proper carrying and adherence
- Automatic detection of proper activation
- Automatic temperature trend notification to warn of unsuitable temperatures
- Last known location feature to help locate the device and/or user
- Power management features to facilitate extended battery life.
Any of these features can be added to any of the Aerio Platforms (Uno, Duo, Mix, On-body).
Kaléo is also the first company to include electronic voice prompts to guide the user through the injection process. This has proven to be very useful for first-time users and in the high-stress environment emergency-use autoinjectors are typically used in.8 This prompt system is intended to guide users through the administration process, which may be helpful in situations where there are long durations between injections. Kaléo has also developed an electronic trainer to aid instruction on correct use to keep the patient/caregiver current on training between injections.
Kaléo’s proprietary pressurised gas technology, combined with its patented non-coaxial configuration, automatic needle insertion and retraction, and proven reliability, makes the Aerio Platform well positioned to address the emerging need for home administration of high-volume, high-viscosity formulations.
REFERENCES
- Saganowsky E, “The top 20 drugs by worldwide sales in 2020”. Fierce Pharma, May 3, 2021.
- Batchelor GK, “An introduction to fluid dynamics”. Cambridge University Press, 2000.
- Le Basle Y et al, “Physicochemical stability of monoclonal antibodies: A review”. J Pharm Sci, 2020, Vol 109(1), pp 169–190.
- Bittner B, Richter W, Schmidt J, “Subcutaneous administration of biotherapeutics: An overview of current challenges and opportunities”. BioDrugs, 2018, Vol 32, pp 425–440.
- Overton PM et al, “Patient preferences for subcutaneous versus intravenous administration of treatment for chronic immune system disorders: A systematic review”. Patient Prefer Adherence, 2021, Vol 15, pp 811–834.
- Draft Guidance for Industry and Food and Drug Administration Staff: Technical considerations for demonstrating reliability of emergency-use injector submitted under a BLA, NDA or ANDA”. US FDA, Apr 2020.
- “Environmental Engineering Considerations and Laboratory Tests”. US Department of Defense, Military Specification [MIL]-STD- 810H, Revision H, Jan 31, 2019.
- Edwards ES et al, “Design validation and labeling comprehension study for a new epinephrine autoinjector”. Ann Allergy Asthma Immunol, 2013, Vol 110(3), pp 189–193.