Citation: Stops A, Fortina W, “Key Considerations for an Optimal Emergency-Use Autoinjector”. ONdrugDelivery, Issue 125 (Oct 2021), pp 46–50.
Adam Stops and William Fortina introduce Maverick, an emergency-use autoinjector, and discuss key considerations during the device design and development, for primary packaging and manufacturing and assembly.
Some life-threatening medical emergencies – such as anaphylaxis shock, uncontrolled hypoglycaemia or opioid overdose – require swift injection with life-saving drugs. Emergency-use autoinjectors (EAIs) have become the device of choice in these situations, due to their quick administration and systemic action.
Regulators understand the importance of the EAI’s reliability for such circumstances and have established higher device reliability requirements as a result. The US FDA’s latest guidelines, for instance, require manufacturers to achieve a 99.999% functional reliability with a 95% confidence level.1
“Creating an EAI starts from the device design, with multiple aspects requiring consideration before even building prototypes, and throughout various design iterations as well.”
Multiple aspects require careful consideration to achieve these standards and create an optimal emergency autoinjector. This article introduces Maverick, an innovative autoinjector for emergency use, by reviewing key factors of consideration during the device design and development, for primary packaging and during manufacturing and assembly.
DESIGN CONSIDERATIONS
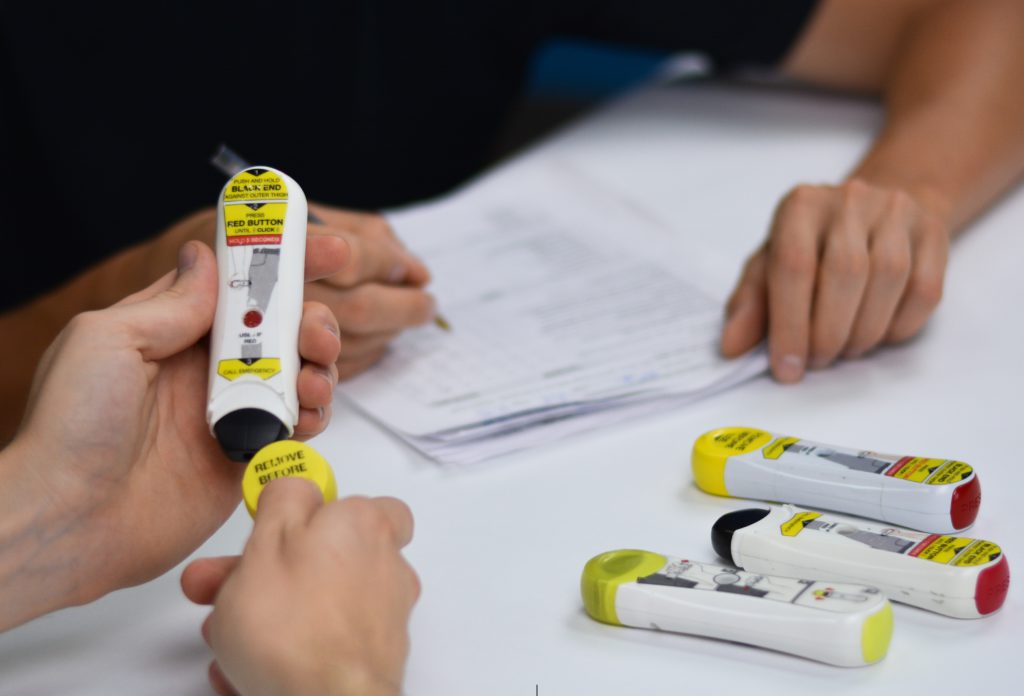
Figure 1: Patient interviews and user studies are important tools to design an optimal device.
Creating an EAI starts from the device design, with multiple aspects requiring consideration before even building prototypes, and throughout various design iterations as well (Figure 1).
Understanding the Use Scenario
First and foremost, designers must thoroughly understand the use scenario(s): the user, the drug, its characteristics, the medical emergency’s circumstances, the patient’s reaction, possible bystanders (family, friends, co-workers, strangers), to name a few key aspects. Before conceptualising its Maverick EAI, Duoject conducted a thorough use scenario analysis and several patient interviews. This exercise highlighted three major concerns:
• First, the level of user experience with emergency treatments varies greatly from one user to the next.
• Second, as an article published in The Psychologist2 explains, cognitive failures in emergency situations mean that actions taken can be ineffective at best and, in some cases, can even reduce chances of survival. In other words, during life-threatening events, humans tend to demonstrate difficulties in making rational decisions that could transform even the simplest action into a complex one. A critical factor to consider for creating an optimal EAI design.
• Finally, since medical emergencies happen unexpectedly and require immediate care, patients must have access to their EAI at all times, and administer it within an acceptable time span.
EAI Optimisation by Design
This use scenarios analysis tells us that minimising or eliminating potential misuse becomes a matter of patient survival. Consequently, the ideal EAI design must incorporate the following qualities – first, the device must be as straightforward to use as possible. During a medical emergency, the user should not have to deal with packaging removal, assembly steps or dose setting, and the use sequence must accommodate both naïve and experienced users. Second, the system should be foolproof to prevent any use other than the intended one – and avoid losing a life-saving dose. Third, the design must be convenient to carry around at all times. Finally, to avoid any additional health risk, the EAI must prevent reuse and needlestick injuries.
Duoject designed its Maverick EAI to integrate these attributes; for instance, its patented double-trigger system minimises the chance of activation in the wrong orientation or before the intended use. Once activated, the device’s injection mechanism is fully automated, including its needle retraction sequence. Its compact size also fits in regular trouser pockets while maintaining acceptable ergonomics. Finally, cartridges helped achieve both this pocket-sized format and better sterility assurance than syringe-based systems.
“Emergency parenteral administration is often challenging, yet even inexperienced users must be able to effectively deliver the injection. Making the user experience seamless, while not compromising on reliability and safety, will support the goal of mitigating misuse. “
Optimising User Experience
As previously mentioned, emergency parenteral administration is often challenging, yet even inexperienced users must be able to effectively deliver the injection. Making the user experience seamless, while not compromising on reliability and safety, will support the goal of mitigating misuse. The ideal EAI design must therefore strike a fine balance between integrating fail-safe features and remaining quick to use and intuitive for all.
The Maverick EAI was designed to enhance ergonomics: the colours, shape and on-device instructions for use were created and refined through various human factor studies to be as intuitive as possible. For instance, the red colour of the finger trigger is universally recognised as a call to action. Meanwhile, the triple feedback – visual, tactile, auditory – of the mechanism signals to the user the injection is completed.
In summary, a close examination of use scenarios reveals that an optimal emergency autoinjector must be easy to carry around, extremely intuitive for even the most inexperienced users to administer a dose correctly, and with a foolproof design to prevent misuse in the most stressful situations.
DEVICE DEVELOPMENT CONSIDERATIONS
Once a design fulfils the needs of life-saving parenteral administration, the development of the EAI becomes the focal point. Done well, it ensures the reliability of the mechanism, validates its drug compatibility and confirms it is used correctly by patients. Two essential considerations arise during this process.
Planning for Superior Reliability
The first is to build a robust test plan to prove the design’s reliability with the highest confidence level practically possible – remember that the patient’s life depends on the EAI’s reliability to perform the injection. This implies adhering to more standards, performing more tests, and using a significantly larger number of samples and more stringent pass criteria.
Sterility Options and Validations
The second is to develop and guarantee the sterility of the drug’s fluid path. The validation of the sterilisation process must be impeccable and the device must remain sterile until activation. This must be true even under the most challenging conditions. For instance, users could remove the cap without the intention to activate the device; there can be exposure to extreme temperatures, humidity, dust or sand; or the EAI may be dropped or knocked around during its shelf life.
Duoject responded to these challenges by devising an appropriate test plan for its Maverick EAI to reach a high reliability confidence level. The development team also used a cartridge as the primary container, to allow the fluid path to remain sterile even when uncapped – as opposed to prefilled syringe autoinjectors exposing the needle when the cap is removed – and to increase is tolerance to high stress during injection.
“Stevanato Group combined its glass expertise with proven testing protocols focused on mechanical characterisation methods and statistical analysis to engineer a stronger cartridge solution compared with the standard ones.”
SG NEXA®
The experience gained from developing primary containers, analysing the interaction with drug delivery devices and performing contract manufacturing services has enabled Stevanato Group to gain an intimate perspective of the critical path for any medical device project. This know-how is used to streamline processes and harmonise products and services.
To meet the market requirements, Stevanato Group developed highly resistant glass cartridges suitable for EAIs that can be easily integrated with such injectors. Stevanato Group combined its glass expertise with proven testing protocols focused on mechanical characterisation methods and statistical analysis to engineer a stronger cartridge solution compared with the standard ones. Enhanced performance was achieved by improving the production line to reduce the number and the depth of potential inner glass flaws, and by applying silicone to the outer surface of bulk packaging to prevent friction defects. In fact, Nexa® 3x glass cartridges are characterised by superior cosmetic quality and mechanical resistance, due to a 100% camera inspection and Stevanato Group’s proprietary highly automated process know-how around critical no-metal-to-glass and no-glass-to-glass operations.
Nexa® 3x glass cartridges benefit from Stevanato Group’s in-house proprietary inspection controls to check the most critical dimensions (such as total length, internal diameter and mouth and shoulder) and cosmetic defects (such as scratches).
Nexa® 3x cartridges are also available in EZ-fill® format, which, in addition, provides reduced variability in forced breakages, which is of particular interest, given the importance of reliability for emergency autoinjectors.
All these improvements are made with the entire pharmaceutical development process in mind, which is one of the advantages of Stevanato Group being a full-solution provider. A concrete example is interpreted by Nexa® 3X cartridges, with its optimised and high-value features suited to the specific needs of the Maverick autoinjector.
HIGH-PRECISION TOOLING
Once there is a stable design for the device, the first step when manufacturing injection-moulded components is to design an appropriate mould that can produce the parts in a uniform and stable process. While the moulding process has a large influence on the consistency and capabilities of the moulded components, the foundation is the injection-moulding tool. It needs to provide the necessary architecture for a controlled and consistent flow of the polymer through the hot runners, which is done by rigorous design qualification procedures and built-in sensors which then monitor the process during the operation. These tools also require appropriate temperature control through well-designed cooling channels, also with the appropriate sensors in place.
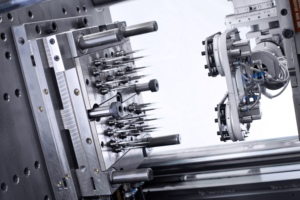
Figure 2: Achieving maximum-quality outcomes with high-precision tooling.
Following the approach of using advanced sensors and software enables constant high-quality outcomes throughout the production cycle. Certain parameters to optimise the moulding process – such as temperature, pressure, flow and cooling – are provided, all under the close watch of Stevanato Group’s in-house moulding experts. The data recorded by those sensors can then be used to assess the quality of the moulded parts – ensuring only high-quality moulded components are used during assembly of the device (Figure 2).
To ensure the quality of the tools, Stevanato Group has a carefully selected group of trusted suppliers that work closely with the company’s own highly qualified mould process engineers and device design engineers to guarantee good adaptation of the moulds to the injection-moulding process. The company also has a small group of in-house tool makers and tool maintenance engineers who work closely with suppliers.
All these experts are involved in the specification and design of the mould tools, together with the tool makers. This multidimensional approach is crucial to achieve high-dimensional capabilities with state-of-the-art technology, all enabling Stevanato Group to manufacture with reliable processes. With more than 160 high-precision injection-moulding machines – some of them having up to 128 cavities and clamping forces of up to 500 tones – the company produces on average 1.5 billion plastic components a year.
ROBUST ASSEMBLY PROCESSES
The assembly equipment offered by Stevanato Group for the Maverick assembly processes performs 100% inline inspection. While Stevanato Group typically ships sub-assemblies directly to pharma companies for final device assembly, with Maverick, it is possible to perform the assembly process through Novocol Pharma, Duoject’s parent company, using equipment supplied by Stevanato Group. With extensive experience in providing automated assembly equipment to leading pharmaceutical companies for drug delivery devices, Stevanato Group has built automated assembly equipment for its customers that is currently being used to manufacture millions of devices every year.
Similar to the approach in moulding, inspection and measurement are key to maintaining control over manufacturing processes. If it is possible to control as much as possible early in the process, then downstream critical functions will be better controlled. To achieve this, Stevanato Group has fully validated camera inspection systems that can be used at every step of the assembly process, including snap-fit clips and mechanical features. Force and torque monitoring algorithms can then be programmed, along with the precise position of the axis, to control and verify the assembly – providing valuable measurement data.
” In every autoinjector design, the goal is always simplicity in the assembly process, but there are still multiple steps that must be completed, each using technology to measure and verify the correct assembly –which is essential to achieve high reliability.”
For Maverick – as with most autoinjectors – there are two main sub-assemblies for roughly 10 injection-moulded parts and some metal components. In every autoinjector design, the goal is always simplicity in the assembly process, but there are still multiple steps that must be completed, each using technology to measure and verify the correct assembly – which is essential to achieve high reliability.
Furthermore, there are sensors for assessing functional aspects in the assembly – to verify functionality in every device; all inline and with 100% inspection. As an example, if a component within the device is not in the correct position after assembly, the device is automatically rejected. However, if the component is in the correct position, it continues through the remaining assembly processes – ensuring the device meets the requirements for reliability and functionality.
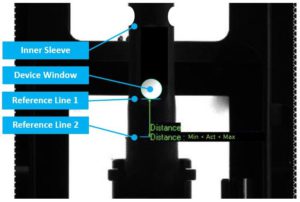
Figure 3: With 100% in-line controls, sensors can check, amongst other things, if device components are in the correct position, and if not, automatically reject the device.
Besides positional features, these sensors can also be used for distances, shapes, colours, barcodes and even small visual defects, with every inspected item being pretested in bench conditions. These technologies provide valuable measurement data, which are important when considering reliability requirements for emergency autoinjectors (Figure 3).
Stevanato Group designs its equipment in a modular fashion, so whether the need is for low-volume clinical batches or high-volume full-scale production, they all share the same modules – enabling scalability. An example is a top-mounted visual inspection system to monitor the integrity of the glass cartridge when placed into position during final assembly. This system inspects for glass defects and foreign objects. Once the system identifies a defect, it automatically rejects the single component. Stevanato Group can also equip its lines with many other modules, including dimensional measurement systems and functional testing modules.
While Stevanato Group handles the sub-assembly process in its FDA-audited production site in Germany, Novocol can perform final assembly, using Stevanato Group’s assembly equipment. In addition, Novocol can also support clients with formulation and fill & finish, if required. In case customers need additional in-process controls for the filled cartridge, it can be part of the one-stop-solution service offered. Stevanato and Novocol performing production and assembly during the device development phase also means there would be no need for revalidation or technology transfer once a customer switches from clinical to commercial. These are just two of the many advantages this one-stop-shop solution offers to pharma companies.
CONCLUSION
When a medical emergency requires parenteral administration of a life-saving medication, the injection device used must demonstrate superior reliability and ergonomics to comply with strict regulations and preserve patients’ lives.
To develop and to produce such a device requires special expertise and careful consideration at every step of the development and production. The Maverick emergency autoinjector combines Duoject’s expertise in device design, Stevanato Group’s outstanding drug containment, moulding, tooling and assembly capabilities and, optionally, Novocol’s experience in formulation and fill-finish. Together, these companies offer a one-stop shop for the highest standard emergency autoinjector that is ready today to perform the final device customisation to suit the client’s unique drug needs (Figure 4).
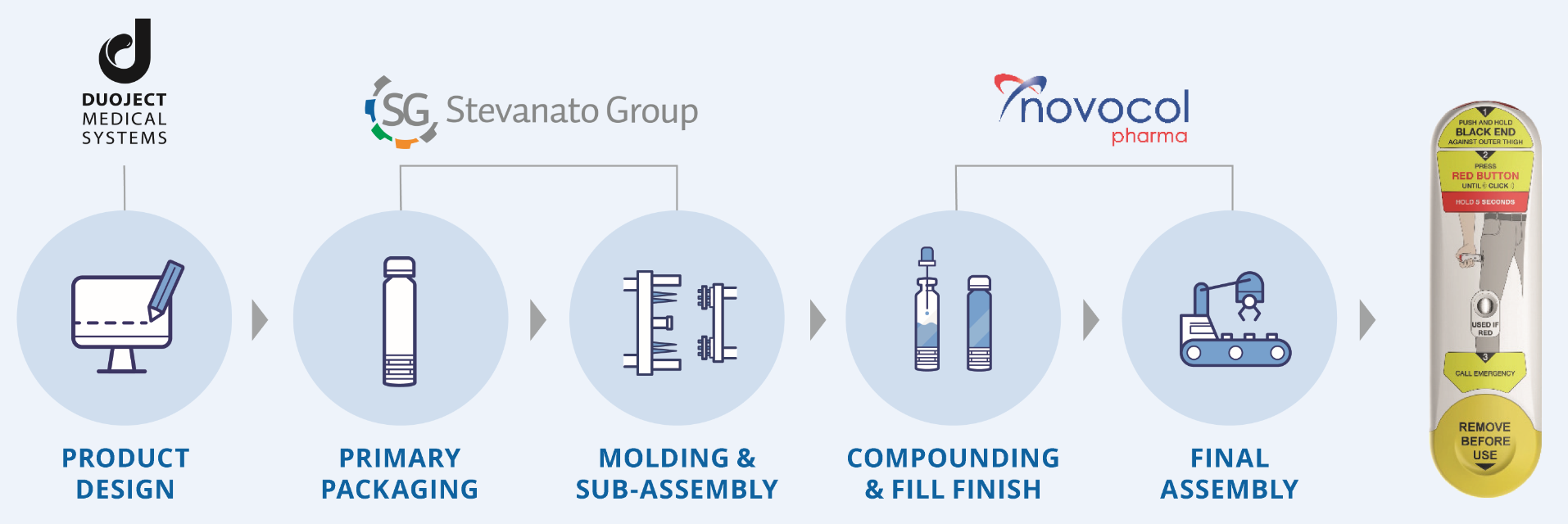
Figure 4: The one-stop-shop solution offered for Maverick is a way to better keep under control the key development steps linked to device reliability.
REFERENCES
- “Draft Guidance for Industry: Technical Considerations for Demonstrating Reliability of Emergency-Use Injectors Submitted under a BLA, NDA or ANDA: Guidance for Industry and Food and Drug Administration Staff”. US FDA, Apr 2020.
- Robinson S, Bridges N, “Survival – mind and brain”. The Psychologist, 2011, Vol 24, pp 30–33.