To Issue 133
Citation: Kearns J, Huang K, “Putting Process Engineering into Action”. ONdrugDelivery, Issue 133 (May 2022), pp 8–12.
Jonathan Kearns and Kevin Huang consider how engineering competencies are being driven to the next level by leveraging process engineering and how this can transform drug-device projects.
“SHL Medical has actively devised ways to develop and tightly integrate such competencies further into its end-to-end device development process.”
It would be remiss not to acknowledge that, in many industries at the intersection of science and engineering, there is an integrated network of disciplines that allow us to deliver products successfully. For example, the untrained eye may think that engineering is an all-encompassing field and profession that gets the work done in any manufacturing firm. This is partly true. However, the matter at hand is not just of semantic relevance but also practical, regarding what and who successfully delivers the work and commercial products to its targets across the value chain.
The concept of engineering has existed since ancient times, as evidenced by the invention of elementary but fundamentally groundbreaking tools, such as the lever, wheel and pulley. Much like science, problem-solving is common to all engineering work, with the ultimate goal of converting natural resources for use by humankind. From ancient times, engineering has evolved to become a complex and highly specialised field, with its subdisciplines branched according to their decreasing emphasis on science (Table 1). Now, there are chemical engineers who design and develop chemical manufacturing processes in the textile, food and pharma industries. There are also biomedical engineers who focus on advancing translational work in biology and medicine for the improvement of health. As the list goes on, it becomes increasingly apparent how important engineering is towards the continuous development of society.1,2
Engineering Function | Description |
Research | Research engineers seek new principles and processes using mathematical and scientific concepts, along with experimental techniques and inductive reasoning. |
Development | Using creative application of new knowledge, development engineers apply the results of research for new purposes, such as creating a working model of a new electrical circuit, clinical process or industrial machine. |
Design | Methods are selected by the engineer designing a structure or product and determines shapes and performance specifications to meet safety technical requirements. |
Construction | Preparation of the site is the responsibility of the construction engineer. He/she also determines procedures that result in the desired quality, economically and safely, and directs the placement and organisation of materials, personnel and equipment. |
Production | Processes and tools are selected by the production engineer who is responsible for the plant layout and equipment selection. He/she also integrates the flow of materials and components and presents for testing and inspection. |
Operation | Machines, plants and organisations providing power transportation and communication are all controlled by the operating engineer. Personnel supervision is also within his/her remit to ensure reliable and economic operation of complex equipment. |
Management and other functions | In this category, the analysis of customer requirements falls under the engineer’s responsibility. He/she also resolves problems and recommends units to satisfy economical needs. |
Table 1: Engineering functions and their brief descriptions. (Adapted from Ralph J Smith, Professor Emeritus of Electrical Engineering at Stanford University, CA, US.)
“The importance and edge of having a well-developed process engineering function is clearly evident for SHL Medical, whose vertically integrated ecosystem allows it to design and develop its own tools and machines that produce its autoinjector devices.”
PROCESS ENGINEERING IN AUTOINJECTOR DEVELOPMENT
The autoinjector industry has seen the need to harness a mix of various engineering approaches to ensure quality devices reach the hands of patients across disease areas. After all, the US National Academy of Engineering identifies “engineering of better medicines” as one of the “14 Grand Challenges for Engineering” in the 21st century. SHL Medical, with more than two decades of historical work and experience, has seen how a number of relevant industrial competencies have matured over time to take their place in the conventional device development approach. In its active pursuit of leading the industry, as well as delivering beyond what is required, SHL Medical has actively devised ways to develop and tightly integrate such competencies further into its end-to-end device development process. Here, the authors would like to present process engineering – an actively evolving discipline within the organisation.
One may ask, what is process engineering and what do process engineers do? As process engineering is a rather complex and continuously developing field, it would be quite difficult to formulate a textbook definition. Nonetheless, process engineering in general (as well as how it is attributed within SHL Medical) is primarily responsible for the design, implementation, control and eventual optimisation of the production process. Process engineers work as intermediaries between product design engineers and production teams – at the outset, focused on transforming raw materials into finished products via the process in question.3
In more practical terms, a process engineer has the know-how to make products while ultimately considering quality and cost. In a review paper on process engineering, Hartfield and Vezza (2016) interestingly describe a process engineer as one who “sees the manufacturing equipment and materials as one entity in a state of flux”. Their description is, however, resonant to the fact that reducing complexity and process variation is a cornerstone of process engineering. Likewise, the importance and edge of having a well-developed process engineering function is clearly evident for SHL Medical, whose vertically integrated ecosystem allows it to design and develop its own tools and machines that produce its autoinjector devices. Having a well-defined checks and balances system within its engineering operations is thus important.4
PROCESS ENGINEERING IN ACTION
A critical look within SHL Medical points us to the successful practice of process engineering in the organisation’s extensive disposable autoinjector (DAI) programme with one of its longstanding pharma partners. First launched commercially in 2006, the DAI is one of the world’s first modern prefilled pens. The device is a button-activated, three-step autoinjector that houses prefilled syringes containing volumes of up to 1.0 mL, and its technical specifications have paved the way for how SHL Medical’s device portfolio is maturing and expanding through platform modularisation.
Over the course of approximately 15 years, the DAI technology has supported the regulatory approval and commercialisation of around 20 combination products. These self-injection devices, available in varying dosage presentations, are indicated for diseases such as rheumatoid arthritis, anaemia, migraine, hyperlipidaemia and osteoporosis, to name a few. Figure 1 exemplifies the diversity of disease areas that the technology has addressed over time.
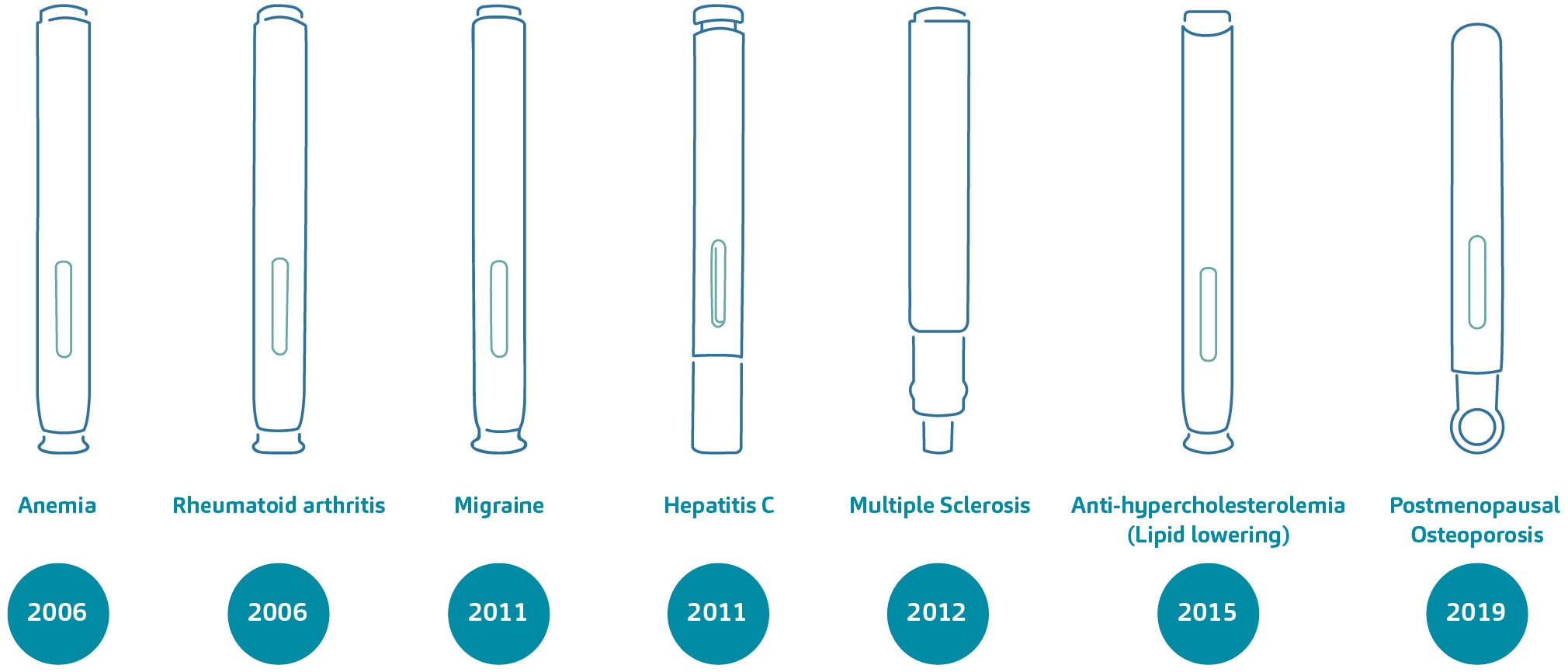
Figure 1: A non-exhaustive overview of combination products based on the DAI technology and their treatment areas; a number of these devices were part of the DAI programme.
“SHL Medical’s driving force and guiding compass is to continue enabling patient independence, and the proof is in the innovative drug delivery solutions that the company has engineered over the decades.”
The first DAI project was developed for a multinational biopharmaceutical company headquartered in the US. The accomplishments of this partnership gave rise to successive device projects using the DAI technology, effectively creating a product range for SHL Medical’s pharma partner. Given that the first project dates back to around 2006, the present-day market landscape enabled SHL Medical to evaluate, upstream and downstream, of all the concurrent device development programmes and production streams that it co-managed with its pharma partner. Both parties saw the need for a product portfolio consolidation while addressing market demands to scale up the programme.
STREAMLINED PROCESS ENGINEERING SOLUTIONS ON A MULTIVARIATE SCALE
A caveat of this programme overhaul was that it was multivariable in many aspects. Each combination product project within the programme presented its own set of manpower, machines, materials and methods – the composite of which had to be evaluated according to both a macro- and micro-perspective. This complex yet holistic activity was addressed through a streamlined, layer-by-layer approach to programme consolidation and scaling up (Figure 2). In many ways, the solution was built upon various process engineering principles. Among many tools, part of a process engineer’s arsenal is the effective use of descriptive statistics and statistical process controls, which were used as part of a larger exercise conducted to interrogate existing variables and corroborate data.
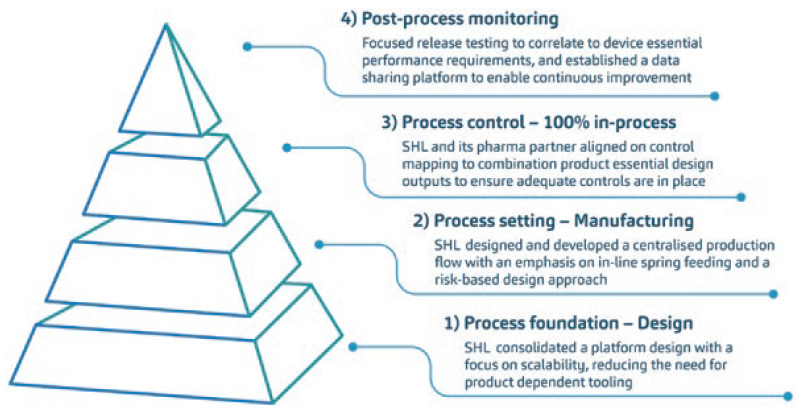
Figure 2: Diagrammatic representation of the streamlined, layer-by-layer approach to programme consolidation and ramp-up conducted by SHL Medical. The extent of this activity was large, covering five combination product projects co-developed with one of SHL Medical’s long-standing pharma partners. The proceedings of this project were first presented at the 2021 PDA Universe of Pre-filled Syringes and Injection Devices conference.
The whole process touched on all device designs, production and in-process controls, through to batch release testing, across the programme, ensuring that complexities were minimised and process variations were reduced throughout. In brief, a design for manufacturability and assembly assessment was conducted to optimise the designs from an automated and scalable process perspective. This assessment enabled the maintenance of brand recognition and colour differentiation across the industrial designs of each device within the programme. With SHL Medical moving towards automating many of its processes, this exercise also enabled centralisation of programme production flow. Now, the assembly process is automated across the programme, incorporating historical learnings and controls.
ENGINEERING THE PATH TOWARDS NEXT-GENERATION DRUG DELIVERY
The words engineering and ingenious come from the same Latin root word, ingeniare, which means to create or to devise. SHL Medical’s driving force and guiding compass is to continue enabling patient independence, and the proof is in the innovative drug delivery solutions that the company has engineered over the decades. SHL Medical realises that part of its strength is due to the network of engineering disciplines that it has mastered over time, allowing the company to transform drug device projects from concepts to mass production. SHL Medical’s work will continue to advance its core competencies further, developing devices for various use cases and drug formulations (Figure 3) and, in parallel, meeting and exceeding its goals in the adjacent areas of digital health and sustainability.
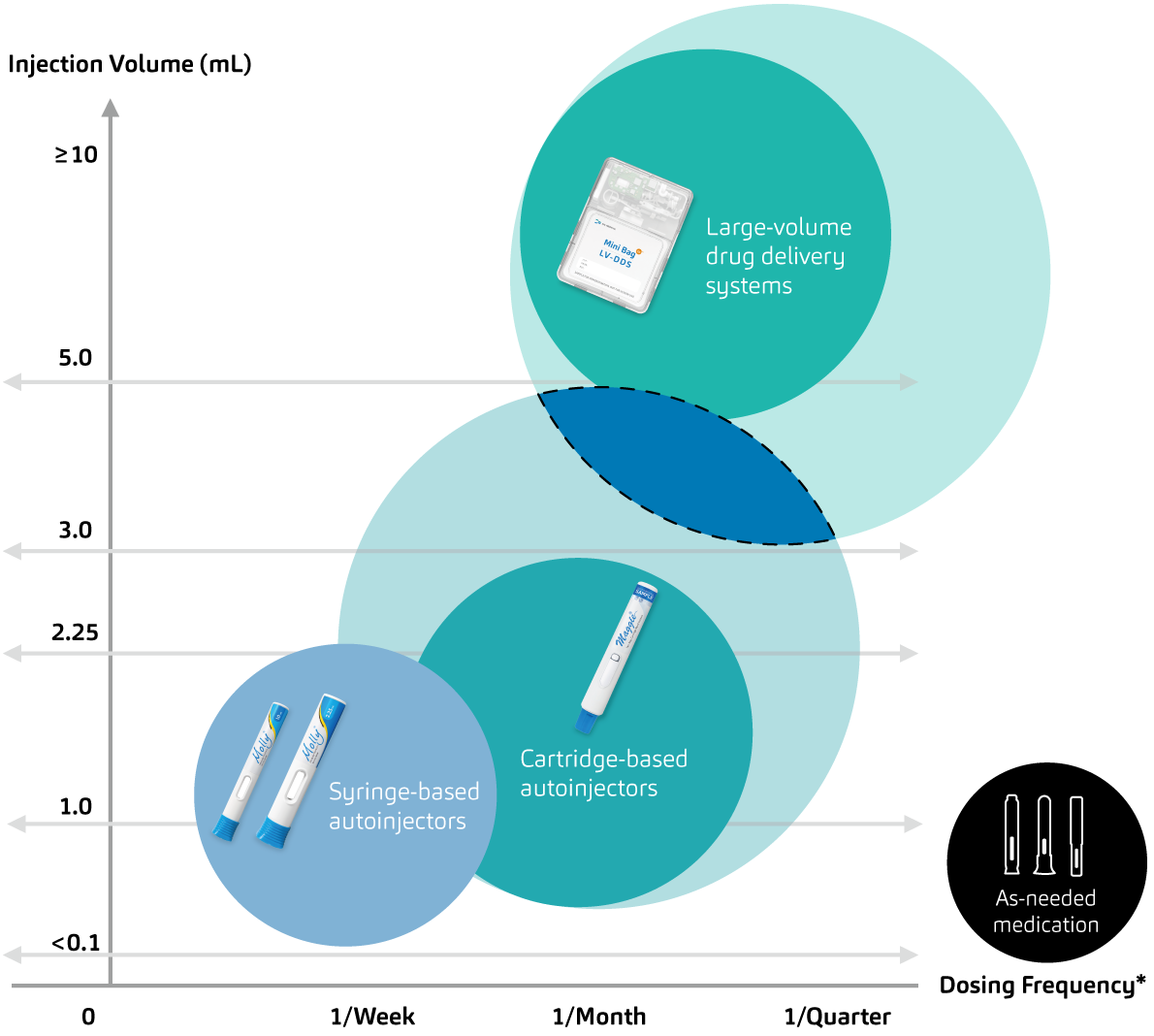
Figure 3: Towards next-generation drug delivery – SHL is constantly investing in engineering efforts to redefine what we know about autoinjectable self-injections (areas of interest marked in blue with dashed lines) and co-lead advances in the subcutaneous delivery of many formulations.
Given the constantly evolving landscape of 21st-century medicine, SHL Medical sees a need to actively lead and innovate the development of drug delivery technologies that inspire its thinking and efforts to push the boundaries concerning subcutaneous injections, injection self-administration and adjacent domains. The pharmaceutical industry has seen recent advancements in the delivery of parenteral formulations, as evidenced by translational technologies that allow for the administration of more complex biologics through subcutaneous means. The company argues that, instead of a disconnected and independent approach between pharma and medtech, a proactive and interdependent approach is critical in the race towards engineering better medicines.
For patient-centric drug delivery, while the path remains open-ended regarding the future of syringe- and cartridge-based autoinjectors, SHL Medical will continue to extend its efforts to redefine the industry’s understanding of self-injection devices, their usability and the formulations they can deliver. A proactive and interdependent approach between pharma and medtech does not necessarily require business agreements, but rather the active cognizance of developing technologies that augment the means to delivering patient therapies in a contemporary but disruptive manner.5,6
REFERENCES
- Smith RJ, “Engineering”. Britannica.com, accessed Apr 2022.
- “Engineering, a Brief History”. Linkengineering.org, accessed Apr 2022.
- Black P, “Process Engineering – Everything You Need To Know!”. Process Industry Informer, Apr 8, 2022.
- Hatfield E, Vezza V, “Process Engineering”. ScienceDirect, 2016, pp 129–136.
- Bittner B, Richter W, Schmidt J, “Subcutaneous Administration of Biotherapeutics: An Overview of Current Challenges and Opportunities”. BioDrugs, 2018, Vol 32, pp 425–440.
- Vargason AM, Anselmo AC, Mitragotri S, “The evolution of commercial drug delivery technologies”. Nat Biomed Eng, 2021, Vol 5, pp 951–967.