To Issue 147
Citation: Cordier S, Brocco B, Verger E, Clausse A, “Cold Storage and Container Closure Integrity – Demonstrated Performance of ETFE-Coated Components.” ONdrugDelivery, Issue 147 (May 2023), pp 6–11.
Sebastien Cordier, Benjamin Brocco, Estelle Verger and Arnaud Clausse discuss the results of a series of tests to demonstrate that Aptar Pharma‘s PremiumCoat® can maintain closure integrity down to -80°C.
It is no surprise that injectable biologics are becoming more prevalent on the market;1 their effectiveness for treating complex diseases, such as cancers or autoimmune disorders, accurate administration and minimised side effects compared with traditional small molecules make them ideal to address unmet medical needs and improve patient outcomes. Advances in biotech techniques are attracting investment from the pharmaceutical industry, resulting in a wider range of options being brought to the market.
“Biologics are more likely to be sensitive and require extra protection from the earliest manufacturing steps all the way through to administration.”
Due to their complex molecular structures and the biotech processes required to produce them, biologics are more likely to be sensitive and require extra protection from the earliest manufacturing steps all the way through to administration. To maintain the potency and safety of these drugs throughout their lifecycle, developers must ensure that their formulations are compatible with the primary packaging and drug delivery device. These validation steps remain challenging, and drug container compatibility can become an obstacle to achieving rapid time to market. The primary packaging industry has been supporting progress in this regard and has developed an array of solutions, such as laminated rubbers and advanced washing processes, that help promote drug/container compatibility.
In addition to using new primary packaging technologies, drug manufacturers have investigated the importance of storage conditions for maintaining the stability of sensitive molecules. Deep-cold storage has been identified as a key strategy and proved to be pivotal during the covid-19 pandemic, with critical mRNA vaccines requiring storage at -80°C. Although the benefits of deep-cold storage for supporting long-term drug stability are undeniable, such extreme storage conditions are challenging for the primary packaging and container closure integrity (CCI).
Glass, which is the most common material used for primary containers, can be submitted to deep-cold storage without significant dimensional changes. On the other hand, rubber, which is the material of choice for closure, is sensitive to cold.
For standard halobutyl formulations, the glass transition temperature (at which the rubber goes from a viscoelastic state to a glass-like state2) is between -60°C and -80°C for Aptar Pharma’s rubbers. Beyond the glass transition temperature, the rubber properties evolve, causing components to shrink and become hard and brittle.
One of the key functions of the rubber closure component is to maintain a seal with the glass – a function that is allowed by the viscoelastic properties of the material. The disruption of these viscoelastic properties may pose a risk to the CCI. Therefore, pharma companies, glass manufacturers and closure component makers must work together to ensure that the packaging parameters, such as the residual seal force (RSF), are under control and that CCI is maintained, even below the glass transition temperature of rubber.
“For most drugs that require deep-cold storage conditions to ensure their long-term stability, PremiumCoat® stoppers must be able to maintain CCI down to -80°C.”
PremiumCoat® film-coated solutions combine a market-proven ethylene tetrafluoroethylene (ETFE) film with Aptar Pharma’s proprietary bromobutyl formulation. The chemical performance of these solutions has been extensively demonstrated and the ETFE film has been shown to reduce the quantity of extractables and leachables that may be transferred into the drug product significantly. For most drugs that require deep-cold storage conditions to ensure their long-term stability, PremiumCoat® stoppers must be able to maintain CCI down to -80°C.
“Aptar Pharma performed a series of tests, leveraging its knowledge of rubber products, technical know-how and state-of-the-art analysis methods.”
Aptar Pharma has extensively characterised the Bromobutyl formulation used for PremiumCoat®, in which the glass transition temperature was evaluated to be at -77°C. To confirm that PremiumCoat® can maintain closure integrity and that the precisely positioned ETFE film does not interfere with CCI (Figure 1), Aptar Pharma performed a series of tests, leveraging its knowledge of rubber products, technical know-how and state-of-the-art analysis methods.
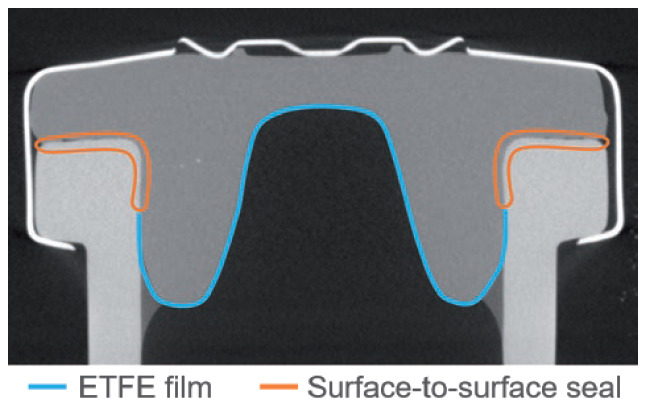
Figure 1: X-ray tomography of a PremiumCoat® stopper inserted onto a 6R ISO NBB vial. The ETFE film coating is represented in blue and does not interfere with the valve, transition or land seal area, as defined by the Parenteral Drug Association.3
METHODS
Stopper RSF and compression: 6R ISO European blowback (EBB) and non-blowback (NBB) vials were crimped using laboratory automatic crimping equipment. Three levels of crimping force were tested and referred to as low (worst-case scenario), medium and high. The RSF was measured using dedicated measurement equipment that applies force on the crimped vial to find the force at which the stopper starts to further compress (Figure 2A). The compression of the stopper was also measured directly using X-ray tomography (Figure 2B). This analysis enabled an evaluation of the force that keeps the stopper secured on the vial’s neck.
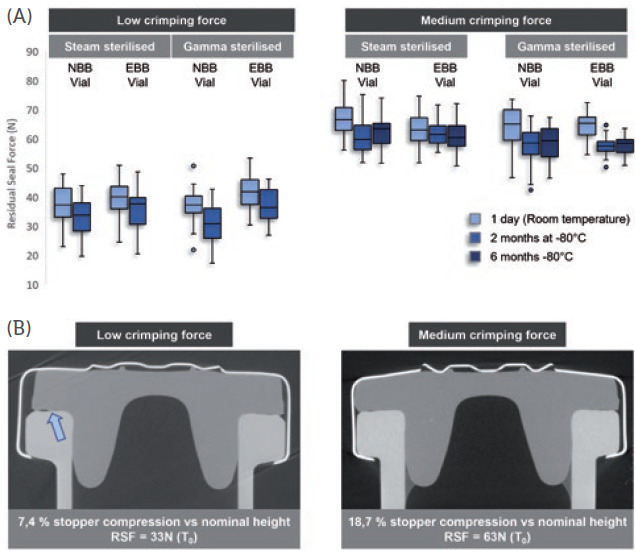
Figure 2: Comparison of the effect of low and medium crimping forces on stopper compression and RSF. (A) RSF measurements were performed on 6R ISO NBB and EBB vials, using steam and gamma-sterilised stoppers, after one day at room temperature, and after two months and six months at -80°C. Two crimping forces were tested, the low crimping force representing a worst-case scenario. (B) X-ray tomography performed after crimping at low (33N) and medium (61N) RSF. The compression of the stopper was calculated as a ratio of the uncompressed stopper thickness and compressed stopper thickness.
Laser headspace analysis: 6R ISO EBB and NBB vials were stoppered under vacuum (85 torr) and then crimped before being stored at -80°C (Figure 3). If, during cold storage, the stopper shrinks to the point where it does not maintain CCI, air gets inside the vial and equilibrates with the freezer’s pressure. When placed back at room temperature, the stopper thaws, resealing the system and trapping the air inside. As temperature rises, the pressure inside the vial increases. Therefore, a significant increase of pressure inside the vial indicates CCI defects at –80°C.
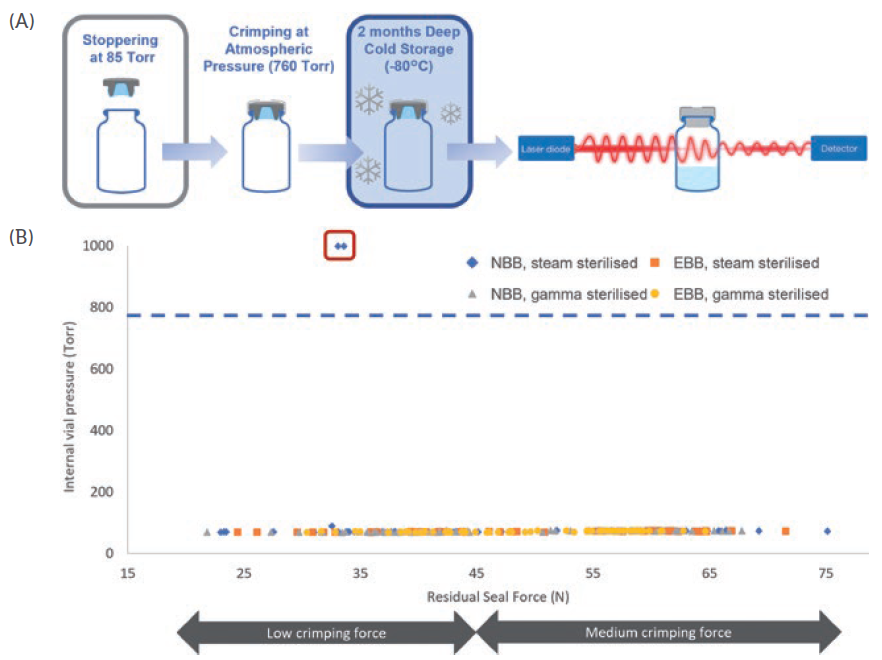
Figure 3: Laser headspace analysis. A) Representation of the laser headspace analysis experimental set-up. B) The experiment was performed using 6R ISO EBB and NBB vials. The internal pressure of the vials was measured using laser headspace analysis and the results were plotted against the measured RSF for each vial. NBB and EBB vials were tested with PremiumCoat® stoppers that had been steam or gamma sterilised. RSFs below 45N were obtained using low crimping forces and RSFs above 45N were obtained after crimping at medium force. The red box represents the two data points that are indicative of a faulty CCI.
Helium leak: The vials were pierced and connected to a helium inflow. An aspiration system was connected around the stopper. The helium flow was quantified by mass spectrometry on the stopper’s side. The baseline detection of helium was measured and the helium flow measured again when the helium supply was turned on. For each vial/stopper system, the experiment was done at room temperature, -80°C and again at room temperature. For the simplicity of representation, only the data at -80°C are represented in Figure 4. A sharp increase in the helium flow at -80°C is indicative of a CCI defect.
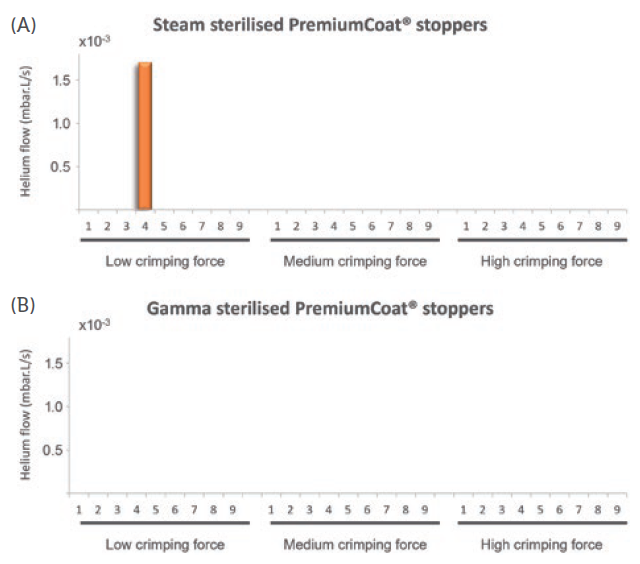
Figure 4: Helium leak test performed at -80°C, different crimping forces and for
(A) steam and (B) gamma-sterilised PremiumCoat® stoppers. The data represent the helium flow measured in mbar.L/s. A sharp increase of helium flow is indicative of a leak. For all samples except Sample 4 of the steam-sterilised stoppers crimped with low force, the measured helium flow was too low to be visible on this plot and not significantly different from the background measurements.
RESULTS
Higher Crimping Forces Lead to Higher Stopper Compressions and RSF
The industrial protocol used to package drugs is of prime importance for ensuring that the drug remains protected throughout packaging, storage and delivery. The crimping force is a critical parameter that ensures that the stopper and vial’s neck maintain close contact, ensuring that a proper seal is formed (Figure 1, above).
In the conditions of this test, Aptar Pharma observed in that storage at -80°C only had a mild reducing effect on the measured RSF, whether at low or medium crimping force (Figure 2A, above). In both cases, for the two vial necks tested and sterilisation methods used, the RSF remained consistent throughout the storage period, indicating that cold storage does not have a lasting negative impact on the elastic properties of the rubber.
Figure 2B (above) further exemplifies the importance of putting the crimping force under control, as low crimping force may lead to incomplete contact between the stopper and the glass (see arrow), and potentially lead to a faulty CCI.
“Storage at -80°C does not significantly affect the RSF of crimped PremiumCoat® stoppers and, when crimped at medium force, PremiumCoat® establishes full contact with the vial’s neck, indicating that PremiumCoat® would maintain CCI under deep-cold storage conditions.”
These data demonstrate that storage at -80°C does not significantly affect the RSF of crimped PremiumCoat® stoppers and that, when crimped at medium force, PremiumCoat® establishes full contact with the vial’s neck, indicating that PremiumCoat® would maintain CCI under deep-cold storage conditions.
Premiumcoat® Stoppers Maintain CCI Down to -80°C When Crimped According to Medium Parameters
To evaluate whether PremiumCoat® can maintain CCI down to -80°C, two complementary methods were used. The laser headspace analysis measured differences of headspace pressures before and after storage at -80°C, with a significant increase of inside pressure indicating a loss of CCI. Although this method is non-invasive and does not require any modification of the vial, it does not allow the measurement of headspace pressure in real time during -80°C storage. This method is therefore completed by helium leak analyses, which requires the alteration of the glass vial for connecting the glass supply, but allows measurement to be performed continuously, even at -80°C. The combination of these two complementary methods can therefore give a complete picture of whether CCI was compromised during -80°C storage.
Laser Headspace Results
Using laser headspace analysis, it was determined whether PremiumCoat® was capable of maintaining CCI down to -80°C, according to the protocol shown in Figure 3A. The data in Figure 3B indicate that only two vial/stopper couples out of 120 could not maintain CCI at -80°C. It is important to note that both CCI failures happened for vials displaying a RSF of about 30 N, which is obtained when using the lowest crimping force and is therefore a worst-case scenario. In all other cases, PremiumCoat® was able to maintain CCI. These data indicate that, when applying the appropriate crimping force (medium), PremiumCoat® stoppers can maintain CCI down to -80°C and therefore protect the drug’s integrity during deep-cold storage.
Helium Leak Results
To further confirm these results, complementary helium leak tests were performed at -80°C and the results are presented in Figure 4 (above). As described previously, each vial/stopper system was sequentially submitted to the helium leak test at room temperature, -80°C and then again at room temperature. This protocol enabled the identification of potential leaks at room temperature or -80°C, and the last measurement ensured that, after having been submitted to -80°C, the stopper retained its visco-elastic properties for maintaining CCI after thawing.
For all the vial/stopper systems crimped at low, medium or high force, and for stoppers that were steam or gamma sterilised, no leak was observed at room temperature (data not shown). For steam-sterilised stoppers crimped at low force, a significant leak was observed at -80°C for Sample 4, where the detected helium flow increased by a factor of 1,000, with a final value of 1.5×102 mbar.L/s. For all steam-sterilised stoppers crimped at medium or high force and RTU stoppers crimped at low, medium or high force, no leak was observed at -80°C. All measured flows of helium were not significantly different from the background measurement.
It is important to note that, for all the conditions tested, no leak was observed when returning the vials to room temperature after exposure to deep-cold storage conditions (data not shown). This observation is also valid for Sample 4 of the steam-sterilised stoppers crimped at low force (Figure 4), indicating that, even if a leak was observed at -80°C, the stoppers demonstrated their resilience and restored seamless CCI at room temperature (data not shown).
“These data position PremiumCoat® as an ideal solution for protecting sensitive drugs that need to be stored at -80°C.”
CONCLUSION
In this study, Aptar Pharma’s technical experts used complementary methods to understand the visco-elastic properties of PremiumCoat® stoppers and tested the ability of the stoppers to maintain CCI under various conditions. By using commonly accepted evaluation methods, such as laser headspace analysis and helium leak, it was demonstrated that PremiumCoat® can maintain seamless CCI down to -80°C when crimped appropriately. Although Aptar Pharma recommends crimping forces of 60 N, when used under sub-optimal conditions (30 N crimping force), PremiumCoat® was still able to maintain CCI in the large majority of cases. Taken together, these data position PremiumCoat® as an ideal solution for protecting sensitive drugs that need to be stored at -80°C.
When developing a new drug or evaluating a second-source supplier to de-risk operations, it is essential for drug developers to select the right closure components. The covid-19 pandemic emphasised the rising importance of security of supply, fast regulatory approval and cold storage. As the market is moving toward more complex and sensitive drugs, such as monoclonal antibodies, bispecific proteins and nucleic acids, primary packaging manufacturers must adapt their solutions to ensure that these drugs are appropriately protected from extractables and leachables, and meet regulatory requirements for chemical properties and ensure that the packaging remains perfectly sealed, even under the most strenuous conditions.
“PremiumCoat® ETFE film-coated stoppers were proven to reduce the number and quantity of extractables and leachables transferred into the drug product.”
In addition to protecting the drug’s integrity during deep-cold storage, PremiumCoat® ETFE film-coated stoppers were proven to reduce the number and quantity of extractables and leachables transferred into the drug product. Aptar Pharma’s experts performed a wide variety of studies to demonstrate the chemical and functional performances of PremiumCoat® and compiled data packages for partners to better understand PremiumCoat®, de-risk their component selection and facilitate their validation process. Aptar Pharma’s experts are also working in close collaboration with drug developers to provide a full range of analytical services to take the burden of packaging validation off them, so they can focus on their drug development.
All the data shown in this article are extracted from internal studies MDNFET001 and CET0202737.
REFERENCES
1. Senior M, “Fresh from the biotech pipeline: fewer approvals, but biologics gain share”. Nat Biotechnol, 2023, Vol 41, pp 174–182.
2. Kumar S et al, “Tailoring permeation characteristics of bromobutyl rubber with polyepichlorohydrin and graphene nanoplatelets”. Materials Research Express, 2015, Vol 2(10), 105007.
3. “Identification and classification of visible nonconformities in elastomeric components and aluminium seal for parenteral packaging”. PDA Technical Report No. 76, Oct 2016.
For more information about PremiumCoat®, visit: www.aptar.com/products/pharmaceutical/premiumcoat-coated-vial-stoppers-and-syringe-plungers.