To Issue 158
Citation: Jarman-Smith M, Tréguier Y, “Advancing Pharmaceutical Contact Applications with PEEK: Meeting Increasing Demands”. ONdrugDelivery, Issue 158 (Apr 2024), pp 60–64.
Marcus Jarman-Smith and Yann Tréguier, discuss the myriad benefits that Victrex’s pharmaceutical-grade PEEK can offer to the drug delivery sector as a material of construction due to its versatile material properties.
INTRODUCTION
As drug delivery devices and pharmaceutical manufacturing processes make more demands during their operation, the use of traditional pharmaceutical-grade materials of construction can be limiting. Materials are being asked to do more and provide increasingly higher performance levels, so a pharmaceutical grade of the high-performance polymer polyetheretherketone (PEEK) can be a welcome addition to the options available to design engineers.
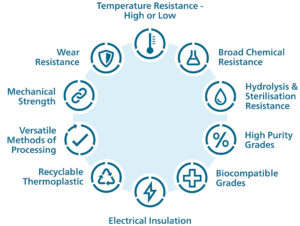
Figure 1: PEEK has many beneficial properties that can be simultaneously exploited at high levels of performance. PEEK often becomes the material of choice where designs require three or more of these at the same time.
PEEK IN PHARMACEUTICAL CONTACT APPLICATIONS
PEEK stands out as a candidate for a material of construction in the pharmaceutical industry due to its ability to provide multiple high-performing properties. It offers exceptional mechanical strength, chemical resistance, wear resistance and electrical properties. However, where it really stands out is in its ability to do several of these things simultaneously (Figure 1). Increasingly, PEEK, which until now has been used to solve only more challenging applications, is being turned to as engineers continue to push the operating boundaries and the condition of use of drug delivery devices.
MEETING FUTURE NEEDS
For drug delivery device development, a focus on patient centricity has meant miniaturisation, enhanced human factors and connectivity. For the materials of construction, this has often meant different or additional design inputs, sometimes in conjunction with a shrinking device footprint. PEEK has a high strength-to-weight ratio. Connectivity also means the onboarding of electronic and battery components, which require properties that facilitate telemetry, insulation and recharging. PEEK has excellent dielectric properties and can be used as insulative coatings or films. Flexible circuits can also be printed onto a PEEK film.
With miniaturisation comes precision and the need for dimensional stability. PEEK can be micro-moulded at shot sizes below 0.1 g,1 and can create miniature functional parts with wall thicknesses of 50 μm. It has been investigated to create microneedles for drug delivery with a tip radius of 30 μm.2 Additionally, PEEK has high resistance to creep, unlike other polymers, such as polytetrafluoroethylene (PTFE). PEEK’s glass transition temperature (Tg) of 145°C and melting temperature of 343°C also make it stable at high temperatures.
“In pharmaceutical process equipment, PEEK is indispensable for applications requiring aseptic conditions, sterility, corrosion resistance or wear resistance.”
PEEK does not have the optical clarity of, for example, cyclo-olefin polymers (COPs) or polycarbonates (PCs), which are common amorphous polymers used for pharmaceutical contact applications. Whilst PEEK can be produced as an amorphous polymer, usually as a film, it is typically a semi-crystalline polymer with high strength, stiffness, wear resistance and chemical resistance. PEEK is around 30% crystalline and usually sits alongside materials such as polyoxymethylene or acetal (POM) and nylon (PA66) as higher strength semi-crystalline thermoplastic polymers. PEEK can be used in place of POM or PA66 where higher strength, stiffness or temperature resistance is required. PEEK does not have the poor moisture absorption commonly seen with polyamides. Often, PEEK can be used as a gear component in drug delivery devices when conditions require more than can be met with POM.
The strength and stiffness of PEEK are being used in devices where the forces required would typically require the properties of metals (Figure 2). For example, on-body delivery systems and large-volume injection have seen increases in volume (e.g. from 1.5 mL to 3 mL) or a more-viscous rheology of the formulation (>50 cP), which can require pressures of 600 psi for 2.5 mL volumes.3 In respiratory devices, PEEK has been selected for inhalers using mechanical power to generate an aerosol, such as soft mist inhalers (SMIs).
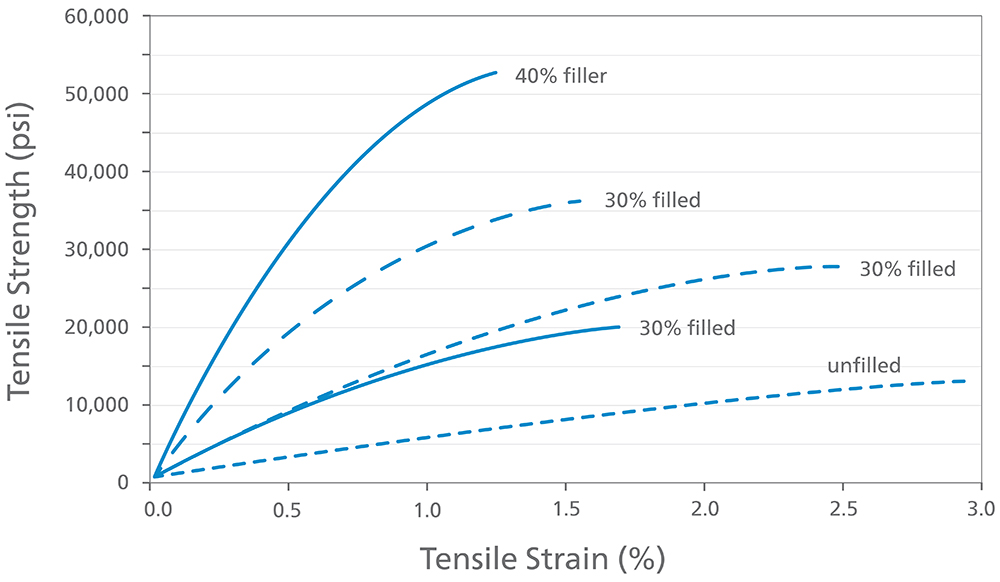
Figure 2: PEEK is a versatile base polymer that can be customised with suitable fillers to impart different properties.
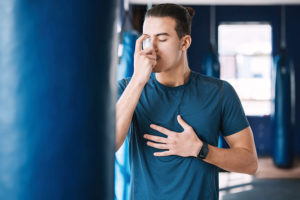
Figure 3: SMIs are an appealing alternative inhalation platform that can meet the needs of the modern respiratory sector, but can place high demands on their materials of construction.
PULMONARY ADMINISTRATION
The incidence of chronic obstructive pulmonary disease (COPD) and asthma is forecasted to rise to 600 million by 2050, which is a 23% increase over 2020.4 This means that drug companies can expect higher penetration rates for these indications, which have traditionally treated by inhalers. However, new treatments for cancers and central nervous system (CNS) disorders are now also using the inhalation route of administration. Moreover, traditional pressurised metered dose inhalers (pMDIs) are under pressure to remove or reduce the hydrofluoroalkane (HFA) propellants currently used in order to reduce their environmental impact. These factors are contributing to driving alternative platforms, such as SMIs (Figure 3). Offering improved drug delivery through a mechanically generated aerosol, the mist created by an SMI is comprised of smaller droplets, resulting in a more precise dose that can penetrate deeper into the lungs, enhancing absorption and effectiveness.
From a materials perspective, an SMI needs materials that can create precise parts that retain tolerances and dimensional stability throughout the device’s lifespan, and that are able to be exposed to chemical formulations at high pressures. SMIs, therefore, require strength, stiffness, chemical resistance and biocompatibility (in terms of minimal leachable or extractable substances coming from the material). The material needs can be summarised as:
- Material is suitable for pharmaceutical contact
- Material is resistant to forces
- Material can be precision manufactured and retains tolerances
- Carbon footprint is less than incumbent metal parts
- Mass production through injection moulding allows total cost reductions.
As such, PEEK is particularly suitable for SMIs due to their high performance demands. With patents such as Boehringer Ingleheim’s Spiriva expiring in the US in 2027, there is space for the development of generic competitors, such as from Lupin,5 and for alternative SMI devices, such as the MRX004 (Merxin Ltd) and Softhaler (InvoX, London, UK) to emerge.
Materials of construction in direct contact with the API must also consider the specific needs of liquid formulations and the US FDA’s requirement for all aqueous-based inhalers to be manufactured sterile (as per Section 21 CFR 200.51) and maintain that sterility for multiple doses.6 Materials like PEEK can offer options not only for the device and container closure system, but also for process line equipment required to prepare the formulations. For production environments where there is exposure to harsh chemicals, steam and abrasion through cleaning in place (CIP) or sterilisation in place (SIP), PEEK has a low water absorption rate (0.5 wt%), is extremely chemically resistant and able to endure multiple cycles of steam, gamma and ethylene oxide sterilisation methods.
PHARMACEUTICAL PROCESS LINE EQUIPMENT
Many millions of machines have already used PEEK in industrial manufacturing equipment components. In pharmaceutical process equipment, PEEK is indispensable for applications requiring aseptic conditions, sterility, corrosion resistance or wear resistance. Components such as seals, connectors, filling nozzles and biocompatible parts benefit from PEEK’s properties, ensuring product quality and regulatory compliance.
Typical applications are bioreactor components, such as connectors; sampling parts; mixing elements, such as impellers; and spray heads for CIP/SIP. Using PEEK for fermentation and vessel parts, such as impellers, can help reduce weight, heat generation and energy requirements. In-line sensor and electronics housings and insulation requiring non-metals, corrosion resistance and insulative properties are also common uses for PEEK, along with valves, sealing and connector components requiring low creep, precision and strength. Further downstream, pharmaceutical-grade PEEK can be used in filling nozzles, robotic grippers, conveyor belt gears and guiding components or cryogenic components.
SUSTAINABILITY
Commonly, PEEK finds its sweet spot as an alternative to metal. It offers the benefits of thermoplastics, such as mass production through injection moulding, but is able to compete with metals in many physical and mechanical aspects with its impressive strength-to-weight ratio and ability to outperform metals in terms of corrosion resistance, anti-fatigue failure and electrically insulative properties.
PEEK can also be used instead of metal parts that may require multi-step machining and subsequent assembly, which, with PEEK, can be consolidated or moulded for a lower cost at mass-production scale. This is where PEEK can have a real impact on companies’ sustainability and energy targets. For metals such as 316SS and titanium, where there are high energy requirements during their production, there can be a global warming potential (GWP) of 35 kg of CO2 per kg compared with PEEK’s 13 kg CO2 per kg.7
“In other industry sectors, PEEK has decades of use-case experience in highly demanding applications that could translate to the pharmaceutical and drug delivery device sectors.”
As a thermoplastic, PEEK can undergo multiple melt cycles and be reformed into new shapes, unlike thermoset polymers such as polyester resin. Commodity polymers may often have a lower GWP for their production, but in use are required in significantly greater volumes and often as single use. These vast quantities demand broader recycling initiatives to control their mass usage. On the other hand, high performance polymers, such as PEEK, tend to have a longer lifespan and are used for specialised components at lower volumes, such as in permanent medical device implants or reuseable or high-value components in devices or production lines.
Indeed, the switch to PEEK should be looked at from a total cost of solution perspective, rather than simply a price per gram. The difference in what PEEK can enable engineers to achieve has potentially far-reaching consequences. Prolonged durability or increased efficiencies have knock-on effects that improve the total cost of the solution and overall sustainability. Other high-performance industries with strong environmental, social and governance agendas, such as aerospace, have already adopted these materials for lighter weight and higher strength parts, consolidating parts or making assembly or usage easier. For example, PEEK wire bundle and tubing clamps for the Boeing 737/787 not only allowed a new design for one-handed user operation, which cut installation time by 30% versus the metal incumbents, but also cut the total weight of the many parts used in one aircraft by 20%, which led to significant fuel savings. All this would be overlooked if comparing simply on a material-to-material cost basis.8
REASSURANCE FROM THE MOST DEMANDING INDUSTRIES
In other industry sectors, PEEK has decades of use-case experience in highly demanding applications that could translate to the pharmaceutical and drug delivery device sectors. Diverse examples include back-up seal rings for low-temperature (sometimes cryogenic) energy applications, dimensionally stable thin films in mobile phone speakers, electrically insulating coatings in electric vehicles, chemically resistant sensors in food manufacturing and load-bearing implantable spinal devices. These applications are typically solutions in extreme environments or requiring industry-certified materials. With the advent of pharmaceutical-grade PEEK, these benefits can be transferred to applications that may also require direct contact with APIs and compliance with industry standards, such as US Pharmacopeia (USP) Class VI.
CONNECTIVITY
For drug delivery devices exploring connectivity, PEEK is already used in many electronic applications, such as thin films for acoustics in an estimated four billion mobile phones, since the material retains the tight dimensional tolerances required for this application. PEEK is also used as an insulator, with stable dielectric properties over a wide range of temperatures, humidities and frequencies. PEEK has a dielectric strength of up to 270 kV/mm, enabling higher voltage and power applications. PEEK also offers the benefit of being a structural material but, as a polymer, not interfering with telemetry or recharging.
COMPLIANCE
The fundamental requirement for materials of construction for pharmaceutical contact applications is the ability for the end part to meet industry standards. Pharmaceutical-grade PEEK has been specifically tested to standards relevant to the pharmaceutical industry, notably USP Class VI and USP <661> (Figure 4). This can reassure the part manufacturer that the material will be compliant and not pose any risk to end testing – while the end part will still need to be tested for compliance, the use of material grades that have passed industry standards offers risk reduction, reassurance and, potentially, reduced time to market.
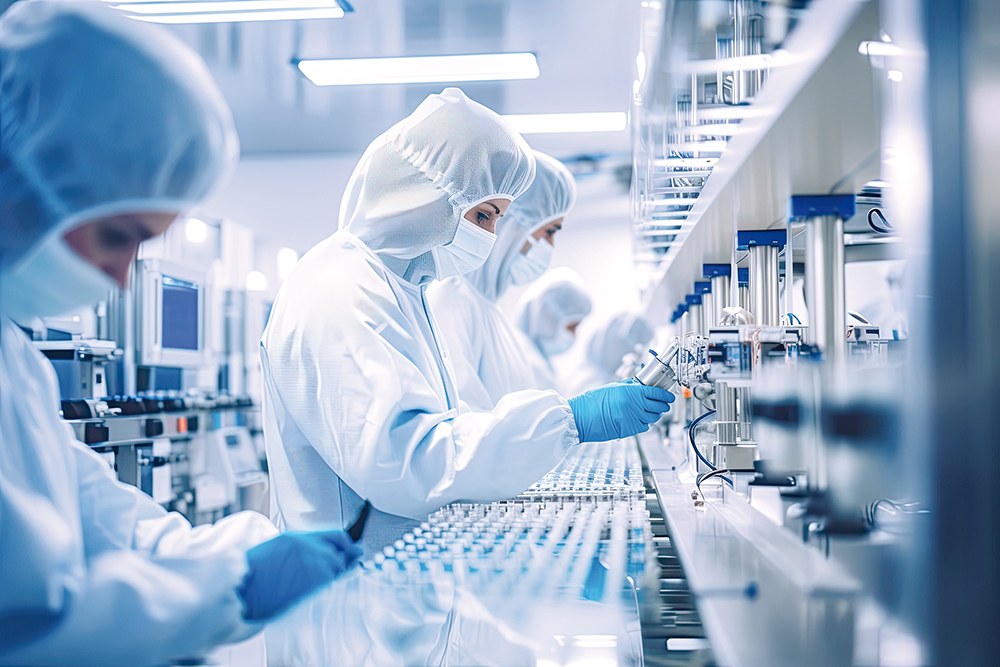
Figure 4: Victrex’s pharmaceutical-grade PEEK has been tested to pharmaceutical regulatory standards.
PEEK AS A PFAS-FREE ALTERNATIVE
PEEK may also be used in some scenarios as a replacement for per- and polyfluorinated substances (PFASs). In industry, PEEK has been used as a powder spray coating and is used as a PFAS-free, non-stick coating alternative for cookware. In energy applications, PEEK has been used as an alternative for PTFE and polychlorotrifluoroethylene (PCTFE) for sealing applications. Pharmaceutical-grade PEEK is available as a film, which is being explored as an alternative to PTFE on plungers in injection devices that require direct API contact.
CONCLUSION
To meet the growing needs of the industry, pharmaceutical-grade PEEK has been made available commercially. Pharmaceutical-grade PEEK’s versatility, high-performance properties and regulatory compliance to pharmaceutical standards make it an invaluable material in pharmaceutical contact applications. As the industry continues to evolve, PEEK polymers, such as Victrex PC™ 101, will play a pivotal role in driving innovation, meeting increasing demands and ensuring the safety and efficacy of pharmaceutical products and processes.
To find out more about applications of Victrex’s PEEK polymers in and around drug delivery, visit: www.victrex.com/en/industries/medical.
REFERENCES
- Ganz M, “PEEK Micro Moulding for Medical Parts – A Success”. CMM Magazine, Jul 2016.
- Nair K et al, “Investigation of Plasma Treatment on Micro-Injection Moulded Microneedle for Drug Delivery”. Pharmaceutics, 2015, Vol 7(4), pp 471–485.
- Roe MJ, “Challenges in High-Viscosity, High-Volume Drug Delivery”. ONdrugDelivery, Issue 125 (Oct 2021), pp 40–43.
- Boers E et al, “Global Burden of Chronic Obstructive Pulmonary Disease Through 2050”. JAMA Netw Open, 2023, Vol 6(12), Article e2346598.
- Dunleavy K, “Lupin wins approval for first US generic of Boehringer Ingelheim’s COPD blockbuster Spiriva”. Fierce Pharma, Jun 2023.
- Anderson P, “Use of Respimat Soft Mist inhaler in COPD patients”. Int J Chron Obstruct Pulmon Dis, 2006, Vol 1(3), pp 251–259.
- “Victrex Sustainability & ESG”. Presentation, Victrex, Mar 2023.
- “Your Partner in The Future of Flight”. Company Web Page, Victrex, Accessed Mar 2024.