To Issue 156
Citation: Palmer-Felgate J, “An Eco-Friendly and Economical Approach to Autoinjectors”. ONdrugDelivery, Issue 156 (Jan 2024), pp 64–67.
John Palmer-Felgate introduces Eco-inject‘s patented innovation – a single-use, two-step autoinjector that is both eco-friendly and economical.
“Many existing autoinjectors were developed long before sustainability was recognised as an important requirement.”
The Eco-inject autoinjector has been specifically designed to provide an efficient and user-friendly drug delivery device that minimises carbon emissions and is deliverable at a competitively low cost. A single compact platform for the Eco-inject device provides the option to incorporate either 1 or 2.25 mL prefilled syringes (Figure 1), while maintaining a common tooling and assembly set-up. The unique “latch and release” mechanism employed within the platform facilitates the use of biopolymers for every plastic component.
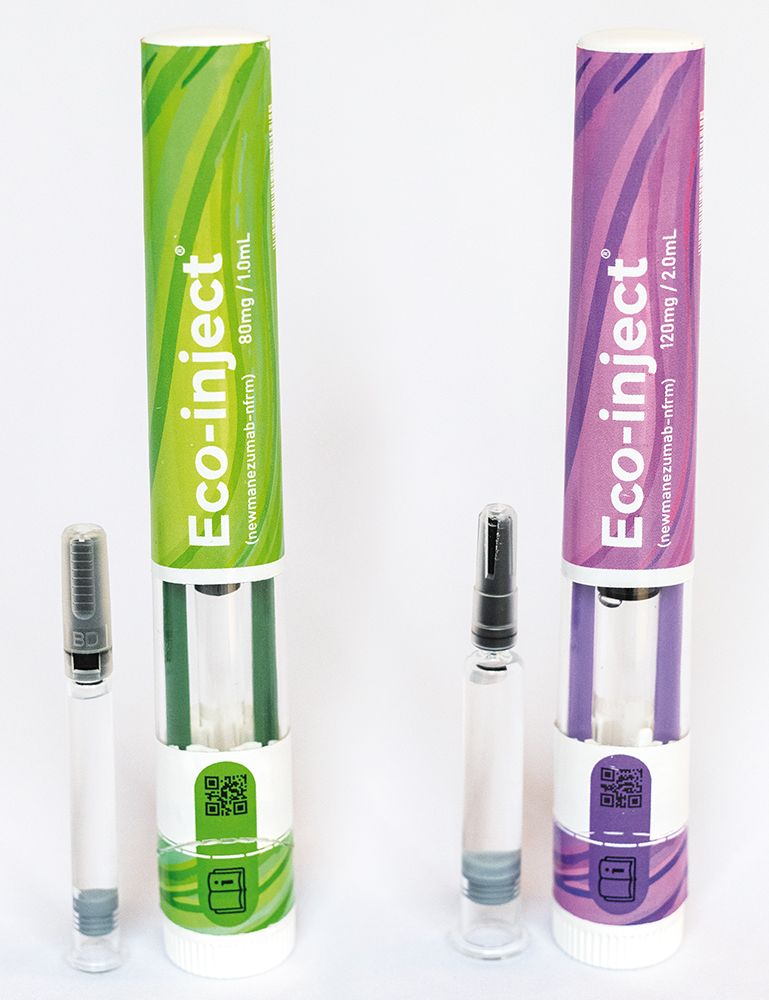
Figure 1: The Eco-inject can incorporate either 1 or 2.25 mL prefilled syringes.
UNPACKING BIOPOLYMERS
There is a widely perceived misunderstanding that all carbon emissions are “bad”, with many climate-change initiatives focusing on decarbonisation – the process of reducing carbon emissions into the atmosphere. However, this is only addressing one key area of carbon management.
A Renewable Carbon Initiative paper on Comprehensive Carbon Management, published in October 2023, outlines the broader approach required to achieve sustainable carbon cycles, even when carbon-reliant materials are used in industry.
In it, vom Berg et al wrote: “Comprehensive carbon management goes beyond CO2 emissions, capture and long-term storage – which it is often reduced to. It decouples the whole industry from fossil feedstock, eliminates the use of fossil carbon wherever possible and allocates renewable carbon (from biomass, CO2 and recycling) as efficiently and effectively as possible where carbon use is unavoidable. The aim is to achieve the lowest possible CO2 emissions, reducing the need for carbon dioxide removal to achieve net zero and to provide a secure supply of renewable carbon to all dependent industries, such as chemicals and materials. Only when carbon is recognised as a raw material in carbon management strategies can truly sustainable carbon cycles be achieved. With proper comprehensive carbon management, the carbon reliant material and energy sectors will be de-fossilised and the remaining energy sector will be decarbonised. And only for the remaining share of truly unavoidable emissions, carbon dioxide removal and carbon capture and storage should come into play.”
Biopolymers can now be made, on an industrial scale, using biogenic carbon – harvested from sources such as wood pulp, anaerobic digesters (waste food compost) or waste from sugar production – to generate the chains of carbon and hydrogen required. This allows plastic to be produced without using any carbon derived from fossil fuels. Using only biopolymer plastic components to make Eco-inject devices facilitates the retention of familiar manufacturing, handling and disposal processes, while only using and releasing carbon within a closed-loop carbon cycle.
“Eco-inject’s simple architecture and patented novel mechanisms have been specifically designed to work reliably using the available low-cost biopolymers.”
MEETING THE NEEDS OF THE EVOLVING MARKET
The market for autoinjectors is increasing rapidly, facilitated by the wider availability of generic and biosimilar drugs – as many blockbuster drugs come off patent – and driven by a greater demand for home therapies. Concurrently, there is acute pressure on pharmaceutical companies and healthcare providers to set and meet targets to reduce their carbon footprint.
Many existing autoinjectors were developed long before sustainability was recognised as an important requirement. Also, when used to deliver high-value originator drug products, device cost was less important. The launch of biosimilar and generic therapies, available at lower price points, is driving the demand for lower-cost autoinjectors to deliver these therapies.
Most healthcare buyers are now implementing sustainability impact assessments to guide their purchase decisions. Single-use autoinjector therapies typically carry a very high carbon footprint compared with other drug products, largely as a result of their fossil fuel-derived plastic device parts. Therefore, there is a risk that the use of these devices may be restricted unless their carbon footprint can be dramatically reduced.
By considering sustainability at all stages of the design process and across the product lifecycle, Eco-inject offers a solution to both the demand to minimise carbon footprint and the increasing requirement for low-cost autoinjectors.

Figure 2: Eco-inject is easy and intuitive to use.
QUEST FOR SUSTAINABILITY
Autoinjectors are typically used by home users who are not medically trained, which is vital to consider when designing any new autoinjector. A new device must be as easy and intuitive to use as currently marketed devices (Figure 2).
For many people, questions that will spring to mind when considering a product’s sustainability include:
- Is it reusable?
- Is it recyclable?
- What has it been made from?
Many drugs administered via autoinjectors are harmful if they contaminate or leak into the local eco-system. Needles that become contaminated after injections must be disposed of in a sharps waste handling stream, typically ending with commercial incineration. These factors present a significant challenge to the demand for autoinjectors to be reusable and/or recyclable.
The used product would need to be disassembled for its constituent parts to be disposed of and/or reused in different waste pathways. This would require a user to disassemble and separate parts of the product, which increases the risk of needlestick injury (to users and waste handlers). The potential confusion between contaminated and recyclable parts also presents an unacceptable risk within the recycling loop.
In addition, reusable devices often include electrical components and require additional handling steps, which sometimes means the user has to reprime a drive system or plug in to recharge. Where the frequency of use of these devices is only once or twice a month, or where patients suffer from multiple comorbidities, it is often not practical to train users to take devices apart reliably and safely or to learn to cope with multiple handling steps or electrical complexities.
Eco-inject has been developed with sustainability at the very core of its design, right from first concepts through to final secondary packaging. It offers simple usability and safe disposal while achieving dramatic carbon savings.
The volume of required plastic components and manufacturing elements has been substantially reduced in Eco-inject, while the metal parts are 100% recoverable and recyclable, following commercial incineration. Carbon emissions are reduced at all stages of production and manufacture: from moulding process conditions and a novel single-tray sub-assembly solution through to final device packaging. These carbon savings are synonymous with financial savings, which are designed to appeal to companies seeking a low-cost autoinjector with a dramatically reduced carbon footprint.
Eco-inject’s unique patented design, which incorporates 100% low-cost biopolymers, sets it apart in the current market for sustainable drug delivery products.
NOT JUST A SIMPLE SWAP
Converting an existing product to a more sustainable version, simply by swapping the type of plastic used, presents problems. Most types of biopolymer, currently producible at a reasonable cost, are based on ethylene or styrenics – and these biopolymers do not possess the mechanical properties required for high load paths, such as the load from a compressed drive spring during the shelf life of a drug/device product. Higher-grade biopolymers are available but these are significantly more expensive. Any plastic swap in an existing product would require revalidation and could require significant alterations to existing tooling, automation and handling systems, adding further to the overall cost.
Eco-inject’s simple architecture and patented novel mechanisms have been specifically designed to work reliably using available low-cost biopolymers. With the production and availability of these biopolymers now reaching maturity, this offers a timely opportunity for Eco-inject to enter the market.
WHO IS IT FOR?
The demand for at-home therapies, facilitated by autoinjectors, is expanding – driven by the appeal of convenience, patient independence, minimised travel requirements and reduced demand on overwhelmed healthcare systems. Medical conditions currently treated using therapies delivered by subcutaneous autoinjector include rheumatoid arthritis, Crohn’s disease, ankylosing spondylitis, multiple sclerosis and clinical obesity, as well as other inflammatory and autoimmune conditions.
Typical use of autoinjectors varies from once a week to once a month. However, other application areas could also include one-off or seasonal administration of preventative therapies, for example, flu or covid-19 vaccines. Autoinjectors enable a potentially intimidating injection process to be embraced by a wider user base and help to ensure that medicines are administered correctly and safely.
Eco-inject is keen to connect with contract manufacturers and pharmaceutical companies that may have an interest in licensing its platform technology technology and bringing it to market. Eco-inject devices are available, on request, for handling assessment and evaluation.