To Issue 156
Citation: Green P, Charlton D, Abbott K, “Capa Valve’s Patented Technology Transforms any Syringe into a DCD”. ONdrugDelivery, Issue 156 (Jan 2024), pp 52–56.
Phil Green, Dale Charlton and Kevin Abbott introduce Capa Valve’s novel valve system for converting standard syringes into prefilled dual-chamber devices, capable of simplifying and improving the delivery of liquid-liquid and liquid-powder drug products, including reconstitution of lyophilised powders.
“The valves within the syringe barrel have excellent inherent container closure integrity, so seal each chamber fully until such times as the valve is activated.”
DUAL-CHAMBER DEVICES MADE EASY
Dual-chamber devices (DCDs) are combination products that typically contain a freeze-dried drug and a diluent in two separate chambers of the device. In particular, they are designed to provide stability and convenience for biopharmaceuticals that require reconstitution before administration. They can also significantly reduce the number of handling steps and therefore the potential for preparation errors by the patient or caregiver. DCDs are of growing interest in large part due to self-administration trends and needs but their wider adoption, even after several decades of availability, is, arguably, still quite limited, most likely due to challenges in manufacturability, product formulation and costs.
The Capa Valve DCD was developed to address many of the issues around the current limitations of DCDs and overcome some of the challenges in the manufacture and economics of their use. The patent protected technology is a simple and cost-effective way to realise a DCD for injection, be it for reconstitution within a prefilled syringe (PFS), such as for a lyophilised drug, or a liquid-solid powder for injection (PI). The additional parts needed can be sized for any standard syringe suitable for prefilled applications. To date, the Capa Valve technology has been tested for suitability from standard 1 mL PFSs up to larger 60 mL infusion syringes.
“The Capa Valve DCD was developed to address many of the issues around the current limitations of DCDs and overcome some of
the challenges in the manufacture and economics of their use.”
The multi-chamber Capa Valve PFS device, when compared with the current methods of reconstitution for lyophilised drugs for injection, reduces risk to the patient, reduces packaging, transport and logistics costs, and drastically reduces the time required to reconstitute prior to injection, as well as addressing some of the limitations in manufacture and wider adoption. Figure 1 shows the stages of pre-mixing a liquid and solid with the device’s sliding valve rod arrangement.
Figure 1: Liquid-solid pre-mix video.
Additionally, the versatility and simplicity of the design allows for a variant of the Capa Valve system to create a multi-chamber device where two or more separate liquids can be dispensed sequentially via a single injection. A typical application for this arrangement would be the injection of a liquid API followed by a saline flush. The valves within the syringe barrel have excellent inherent container closure integrity, so seal each chamber fully until such times as the valve is activated. Upon reaching the end of its stroke, the stopper comes into contact with the bottom of the syringe, at which point the valve opens to allow the liquid in the second chamber to flow through the valve and into the needle for injection. Figure 2 shows the stages of injection for sequentially injecting three separate liquids using two valves within a standard syringe.
Figure 2: Sequential dispense of three separate liquids video.
Another distinct and novel use of the Capa Valve technology for near-patient injection is the installation of the valve at the end of the syringe and filling the chamber between this valve and the plunger stopper with a flush. There are a number of companies offering a PFS with a flush, however, by installing the valve at the bottom of the syringe, it is possible to create a PFS with a flush that can draw up any drug of choice into the PFS (Figure 3).
Figure 3: Draw up and sequential delivery video.
The variant of the technology that enables pre-mixing liquids or a solid and a liquid uses the same principle of having a stopper with a central hole located part-way down the barrel of the syringe, but for pre-mixing the hole is sealed with a cylindrical rod attached to the syringe cap. The sealing rod (valve rod) is either removed by removing the syringe cap or, for use in a contaminated environment, the valve rod can slide through a seal in the cap to unseal the stopper, thereby avoiding drawing in any air from the immediate environment during mixing, which is done by back flushing the valve.
MARKET NEED AND THE CAPA VALVE VALUE PROPOSITION
“The Capa Valve technology was originally developed to address the significant growth and application of PFSs in the growing market of injectable lyophilised drugs, which require reconstitution before administration.”
The costly, time-consuming and relatively high-risk process of reconstituting lyophilised drugs or PIs can be addressed by a PFS using the Capa Valve technology. The technology provides both a packaging solution and a mixing solution, as the action of back-flushing the drug and diluent through the valve generates a gentle but effective mixing of liquid-solid or liquid-viscous liquid combinations. This mixing technique can also be used for mixing viscous liquids and the emulsification of oil-based products, such as vitamin K, for injection.
The Capa Valve technology was originally developed to address the significant growth and application of PFSs in the growing market of injectable lyophilised drugs, which require reconstitution before administration. There is an abundance of information providing data supporting the rapid growth of lyophilised injectables (Figure 4).
The use of lyophilisation for both pharmaceutical and biopharmaceutical manufacturing has grown around 13.5% per year over the last five years.1 At present, around 16 of the top 100 pharmaceutical drugs are lyophilised.2 The percentage of lyophilised biological drugs is even greater – 35%.2 This growing market for biologics requires storage and delivery systems – Acumen Research & Consulting predicts the market value for novel drug reconstitution systems at US$5.1 billion (£4 billion) by 2030.3
Just one example of an application for potential use of the Capa Valve is in the routine immunisation schedule in the UK, for which around five million injections of lyophilised drugs are delivered each year by the NHS (Figure 4).
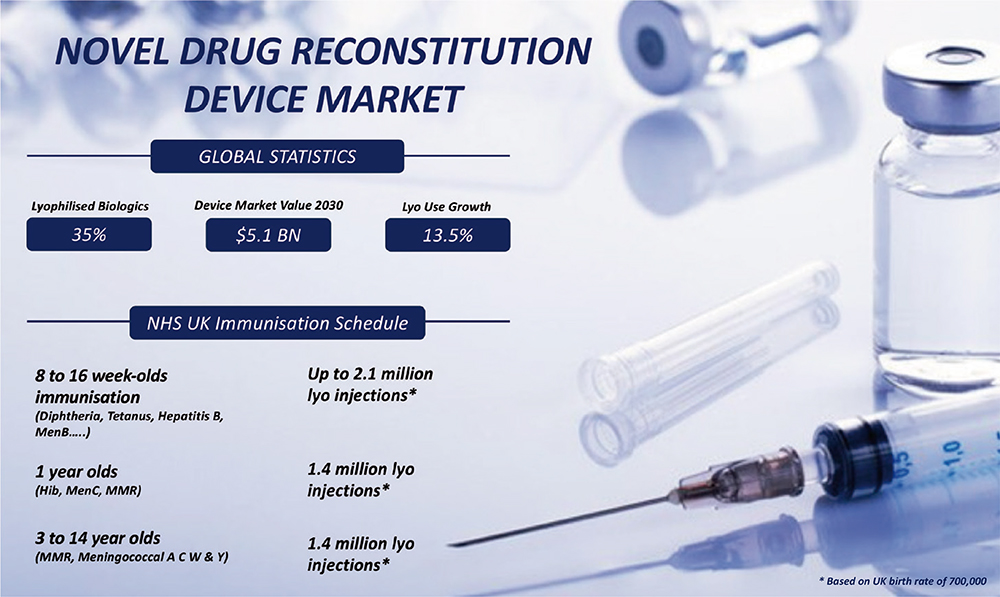
Figure 4: Market opportunity for lyophilised injectable novel device.
TRADITIONAL RECONSTITUTION PRACTICE AND CURRENT NOVEL DEVICES
Currently, there are risks involved in the reconstitution and delivery of lyophilised drugs for injection, such as contamination, incorrect diluent drug ratio, partial reconstitution and incorrect dosage. Additionally, the time taken for reconstitution can be lengthy and the packaging can be excessive, which carries both financial cost and environmental implications. The current practice of administering a lyophilised drug by injection requires a trained healthcare professional to perform the reconstitution, meaning that these drugs are currently not suitable for self-administration in a home environment.
At present, there are a few companies offering dual-chamber syringes for either sequential delivery of two liquids or pre-mixing of a diluent and powdered or lyophilised drug. However, these companies’ devices have only seen limited adoption for widespread use. Without exception, these current DCDs feature a custom-design syringe, often using a bypass valve within the syringe, which significantly increases manufacturing costs, prohibiting widespread adoption. Complex tooling for these bespoke syringes also generates a significant carbon footprint in the process of bringing these into the market.
The Capa Valve solution is the installation of two small, low-cost parts within existing standard syringes suitable for prefilled applications. This system can reconstitute a diluent and a powder, a lyophilised cake or a second liquid extremely efficiently (in seconds) using a standard syringe prefilled with the desired drug combination. This prefilled solution addresses many risks associated with current practices for reconstitution and the ease and speed of reconstitution and administration by injection lends itself to both self-administration and emergency situations. All of the Capa Valve variants have been tested and conform to the ISO 11608-3:2012 standard for break-loose and glide forces.
The Capa Valve technology could not only save significant time and money within the healthcare community, it also perfectly complements the growing market for lyophilised drugs. There are significant benefits in developing drugs in lyophilised form, such as increased shelf-life, lower associated waste, reduced packaging and decreased logistics costs. Therefore, a low-cost solution for both storage and delivery of lyophilised drugs will provide the necessary incentive to continue to develop this more environmentally friendly and convenient form of drug.
FILL/FINISH AND SCALABILITY
The simplicity of the Capa Valve design does not pose significant challenges to the fill/finish process or automation of PFS production. There is minimal disruption to the primary chamber and existing infrastructures can be used with little or no modification. The installation of the sequential valve uses the same process as the installation of the central stopper in a dual-chamber bypass syringe. Figure 5 shows the fill/finish stages for the pre-mix variant.
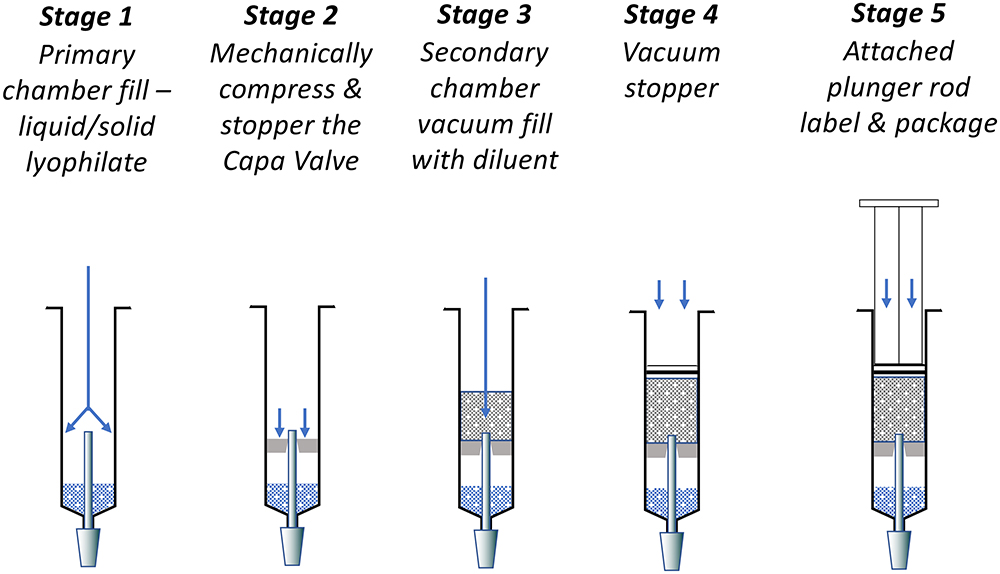
Figure 5: Fill-finish stages of the Capa Valve pre-mix variant.
BUSINESS MODEL AND GROWTH STRATEGY
Capa Valve is currently negotiating a sizeable manufacturing contract based in Europe for the worldwide supply of the technology. The company is also working with several companies looking to license the technology for a broad range of applications, including nutraceuticals, pharmaceuticals and biologics.
Visit Capa Valve at Pharmapack 2024 in Paris, France, Stand J32.
REFERENCES
- DiFranco N, “Lyophilization of Pharmaceuticals: An Overview”. Lubrizol Life Science, Aug 2023.
- “What is driving the growing demand for lyophilization?”. SEQUENS, Aug 2019.
- “Lyophilized Injectable Drugs Market Size – Global Industry, Share, Analysis, Trends and Forecast 2022 – 2030”. Market Report, Acumen Research And Consulting, Nov 2022.