To Issue 142
Citation: Morgan V, Kuschel A M, “Being Prepared for Pharma Innovation is Key in 2023”. ONdrugDelivery, Issue 142 (Feb 2023), pp 60–63.
Victoria Morgan and Ana Marques Kuschel discuss three recent innovations that West Pharmaceutical Services has introduced to help pharma companies adapt to the evolving pharma landscape. They highlight how these technical solutions enable West’s partners to respond to specific market-driven challenges, from pandemic-driven pressures on fill-finish productivity to the underlying shift towards biologics and the accelerated growth of home-based treatment.
For such a heavily regulated industry, where safety and the mitigation of risk are paramount, those on the outside could be forgiven for thinking that pharma is not an environment conducive to fast-paced innovation.
However, in reality, innovation has always been at the sector’s core – you only have to look at the fact that around 50 new, US FDA-approved drugs are consistently delivered each year,1 and further evidence can be found in the whiplash speed with which the industry collectively responded to the demand for covid-19 vaccines.
Behind every one of those successful drugs is an effective drug-delivery platform, supported by a resilient and innovative partner that has both the competence and determination to keep pace with the ever-evolving macro, regulatory and patient landscape.
ANSWERING UNMET NEEDS IN INJECTABLE DRUG PACKAGING
Throughout the covid-19 pandemic, indeed throughout its 100-year history, West has continued to innovate by delivering products that demonstrate better quality, greater strength and more environmentally sustainable designs.
In response to the challenges posed by the pandemic and the existing industry hurdles, West partnered with Corning Incorporated to deliver innovation in drug containment and delivery system solutions. A significant milestone in this collaboration was recently achieved with West’s introduction of the ReadyPack System™ with Corning Valor® Glass at Pharmapack Europe.
The new ReadyPack System offering includes Valor ready-to-use (RTU) vials with SG EZ-fill® (Stevanato Group) technology. Valor Glass’s unique aluminosilicate composition and chemically strengthened surface has been developed to deliver superior chemical durability and physical integrity. This, combined with the exterior coating, which can improve throughput efficiency and reduce particle contamination in robust processing environments, improves both the drug manufacturer’s and the end user’s confidence in the product. Valor Glass therefore represents a significant development in primary packaging materials.
As the pharmaceutical and biotech industries broaden their drug offerings, they must manage more complexity and mitigate risk in the drug development process. Valor RTU vials with SG EZ-fill® technology respond to a demand for flexible manufacturing, increased speed to market, improved glass quality and reduced risk. Combining these qualities with the ReadyPack™ System creates a complete packaging system that allows companies to maximise their time and resources to get a drug to market quickly and safely – and provides a proven vial containment solution that scales from research and development to commercial manufacturing.
Valor® Glass vials undergo an ion exchange strengthening process during production that results in improved load-bearing qualities and helps prevent the formation of cracks. The compressive stress imparted on the glass surface during this process also exceeds the tensile stress levels observed during freeze-thaw processes, such as lyophilisation. Indeed, laboratory tests conducted between -100°C and room temperature using aggressive 15% mannitol with 50% fill volumes have shown that Valor® Glass demonstrates a dramatically lower potential for breakage compared with traditional borosilicate glass vials.2
Valor® Glass eliminates the risk of delamination, which can be costly if discovered too late, through the material’s boron-free composition. In the absence of boron, the vial possesses a uniform surface chemistry that does not feature boron-rich heterogeneities, eliminating a factor that can increase the likelihood of delamination.
Furthermore, because it has a chemically strengthened surface that is engineered with higher internal energy compared with conventional glass vials, Valor® Glass offers enhanced protection against cracking. In typical borosilicate vials, surface flaws can develop into more substantial cracks under subsequent loads experienced during processing and downstream distribution. In the case of Valor® Glass, relatively minor surface flaws are contained within the outermost compression layer, leading to an intact vial with improved breakage resistance. More severe damage that can cause cracking in conventional vials is instead converted into complete breakage by Valor® Glass, thereby rendering the container unusable.
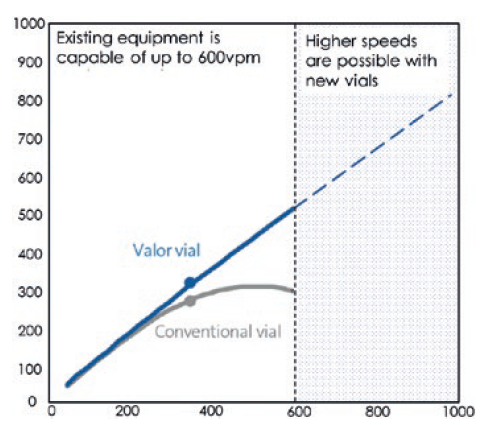
Figure 1: Effective throughput versus filling-line set speed.
Valor® Glass also features an exterior coating with a low coefficient of friction, which has been shown to protect against scratching and reduce peak particle counts on commercial filling lines by 96%.2 Combined with its highly consistent dimensional geometry and chemical strengthening, this presents production line managers with the ability to operate equipment at higher speeds (Figure 1).
In tests at a set filling-line speed of 350 vials per minute (VPM), Valor® Glass is shown to be highly efficient, registering an overall equipment effectiveness (OEE) rate in excess of 80% compared with 60% for conventional vials (Figure 2). Furthermore, this OEE rate can be maintained at a line speed of 750 VPM, meaning that the door is open to demonstrable reductions in filling costs on a per-unit basis.3
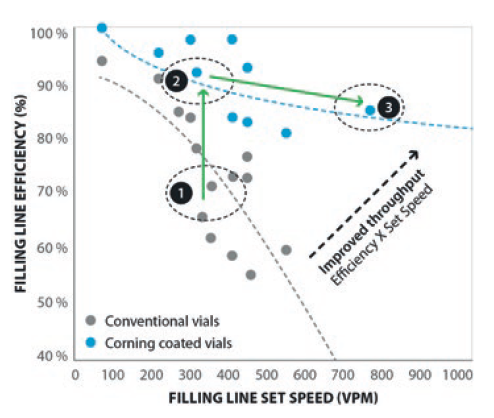
Figure 2: Line speed versus efficiency.
“Transitioning infusion therapies from hospitals or clinics to at-home care could result in a cost saving of up to 70% for both patients and HCPs.”
PROTECTING LARGER VOLUME, SENSITIVE MOLECULES
Vials are, of course, not the only primary packaging platform where changing trends are creating new challenges in terms of drug protection. In recent years, the industry has witnessed a sustained shift of treatment location from hospital to home, driven by patient demand for greater convenience, which has led to increasing recognition of the value of autoinjectors for delivery across multiple therapy areas.
In tandem with the growing market share of biologic formulations, where higher volumes may be required to deliver the desired effect, and the emergence of results from human factors studies showing patient tolerance for an extended injection duration of approximately 15 seconds,4 the door has been opened to the self-administration of a wider range of biologic therapies via subcutaneous injection for applications that would previously have required multiple injections or intravenous delivery within a clinical setting.

Figure 3: The Daikyo Crystal Zenith® component portfolio protects modern biologics from filling to patient injection.
One of the challenges associated with this growing opportunity, however, is compatibility with glass primary packaging options – most notably that some sensitive biologic drug formulations become unstable when exposed to silicone oil. Siliconised glass syringes can also pose a risk to the supply chain and the patient, with challenges around aggregation, contamination and breakage. For some formulations, there is also a requirement to expand the potential drug volume delivered via autoinjectors from the typical dose of 1 mL up to 2.25 mL and even 5 mL.
The question, therefore, is how to protect the integrity of a highly valuable, yet sensitive, biologic formulation at a 2.25 mL volume in a non-glass-based container without compromising the cleanliness and robustness required of the primary packaging.
One answer can be found in the Daikyo Crystal Zenith® (CZ) component portfolio, which includes a 2.25 mL insert needle (IN) prefillable syringe (PFS) system (Figure 3). CZ is a cyclic olefin polymer (COP) that presents a sterile containment system for silicone-oil-sensitive drug formulations. The elastomeric plunger used in the CZ PFS system is coated with an inert FluroTec® barrier film, which reduces the risk of leachables from the elastomer and prevents absorption of the drug formulation. By supporting syringe functionality, the film also avoids the need for additional silicone oil to be used, dramatically reducing exposure to a key source of protein aggregation. Indeed, studies conducted by West on a randomised selection of syringe samples detected no silicone oil, down to 1 ppm, extracted from the assembled syringe.
In further evidence of CZ’s credentials for safeguarding formulation integrity, the precision injection-moulding process used to engineer CZ polymer PFSs facilitates a four-log reduction in endotoxin levels while enabling needles to be attached free of tungsten or glue, which are additional possible sources of drug contamination.
Break-test data recorded during tests carried out by West also demonstrate how CZ mitigates against the risk of breakage. This is not only an important consideration in relation to the fill-finish process, where breakages result in costly downtime, but also in transportation environments and for the activation of the autoinjector itself, where higher forces can be required to deliver larger volume or high-viscosity injections.
LARGE-VOLUME ON-BODY DELIVERY SYSTEMS
One consequence of the sustained shift of treatment from hospital to home is the evolution of on-body delivery systems (OBDSs). Today, OBDS platforms can deliver higher volumes of medicines that traditionally would have been administered intravenously via an infusion at a clinic under the supervision of a healthcare professional (HCP).
West’s SmartDose® OBDS platform helps to provide patients with confidence in their therapy while reducing or preventing the need for frequent visits to infusion centres. Additionally, by using the FluroTec® film-laminated 5-10 mL cartridge plunger, patients can, for the first time, self-administer more than 1 mL, which would have historically been via multiple injections or administered intravenously.
Not only that, but there is also a great deal of evidence to suggest that supporting self-management delivers many patient benefits, including an increase in overall wellbeing, improved mental health, better clinical outcomes and smarter, more cost-effective use of healthcare services.5 Such innovation has implications for the wider ecosystem too, including pharma, payers, HCPs and regulatory bodies in terms of adherence, symptom management and, of course, cost.
From a pharma perspective, OBDS platforms can play a key enabling role in delivering on the patient experience and safety, regimen efficacy and adherence priorities. And, as advances in therapeutic proteins, biologics and monoclonal antibodies (mAbs) deliver improved treatments for diseases such as cardiovascular disease and cancer, then the scope for OBDS platforms grows too.
There are other benefits, too. For companies working on lifecycle management, the FluroTec® film-laminated 5-10 mL cartridge plunger opens up a previously untapped market and, together with the compatible stopper, drug manufacturers can simplify their lifecycle management by selecting one platform with multiple delivery options.
With the increase in patient engagement derived from at-home care comes better outcomes, and the net effect is often a lower total cost of care – a key driver for payers. Transitioning infusion therapies from hospitals or clinics to at-home care could result in a cost saving of up to 70%6 for both patients and HCPs, demonstrating the value OBDSs bring to the payer community.
ADDRESSING THE IMPLICATIONS OF EU GMP ANNEX I
Irrespective of where drugs are administered and the packaging used to contain them, maintaining sterility and avoiding product contamination are critical to patient safety, and pharmaceutical companies face new regulatory challenges in this area. The EU GMP Annex I: Manufacture of Sterile Medicinal Products was first published in 1971 with a major revision finalised in August 2022. The review process was a collaborative effort with the WHO and the Pharmaceutical Inspection Co-operation Scheme (PIC/S).
The latest iteration aims to correct inaccuracies and clarify ambiguities, as well as align the guideline with international requirements. The new version of EU GMP Annex 1 focuses on the need for a holistic contamination control strategy, with an expectation for a formal document that reflects the site-wide strategy for minimising contamination, such as particulates, microbes and pyrogens, throughout the whole sterile manufacturing process. Another focus is a guidance for the usage of new technologies, such as restricted access barrier systems (RABSs) and isolators. In addition, greater attention has been given to an in-depth understanding of container closure integrity (CCI) and container closure integrity testing (CCIT). Finally, the current revision embraces the philosophy of a holistic risk management system – the expected benefit being that there will be fewer deviations in manufacturing and improved supply chain integrity.
As always, with increased market opportunity comes greater oversight, and the evolving regulatory landscape does require pharma and biotech companies to partner with a true expert who can help them navigate the drug/delivery interface development path successfully. West has a full-service portfolio of expertise – including device development, containment systems, regulatory support, analytical testing, combination product manufacturing and fill-finish solutions – to enable partners to develop devices faster, more safely and with less risk, while ensuring the end product is reliable and usable.
CONCLUSION
Today, with greater market focus on sensitive, high-value biologics and advanced therapies extending their reach into several therapeutic areas, including the treatment of chronic conditions, innovation and quality remain the bywords for the pharma supply chain. West has risen to that challenge, delivering a vial technology with demonstrably superior chemical durability and physical integrity to aid patient safety, while simultaneously enabling seismic improvements in operational efficiency.
The company’s advancements in OBDS technology have enabled larger volumes to be administered subcutaneously, over a longer period and in a non-clinical setting, by ensuring user requirements are at the heart of the patient experience. The consequence of this innovation can be felt right across the pharmaceutical ecosystem. For patients, disruption to daily life is limited, with growing evidence that outcomes are improved via the patient-driven care route.6 For payers, there is the potential of a very real cost saving. For HCPs, this technology can offer reduced treatment times and workload. Lastly, pharma partners now have an opportunity to develop more complex therapies, with higher volume capacities than have been possible before.
Finally, with the advent of changes to EU GMP Annex 1, West is continuing to develop innovative responses to help its pharma partners prepare for what lies ahead – in recent years, the only constant has been change, and 2023 promises to be no different.
REFERENCES
- “2021 drug approvals: In a year dominated by COVID, biopharma managed to deliver 55 new drug”. Fierce Pharma special report, Jan 2022.
- “Valor® Glass Product Information. 21st Century Drugs Require a 21st Century Glass”. Corning brochure, 2020.
- Dombrowski T et al, “Full Throttle For Vaccine Filling”. Corning, Apr 2021.
- Berteau C et al, “Evaluation of the impact of viscosity, injection volume, and injection flow rate on subcutaneous injection tolerance”. Med Devices (Auckl), 2015, Vol 8, pp 473–484.
- “Evidence: Helping people help themselves”. The Health Foundation, May 2011.
- “Wearable Injectors Market by Product Type (On-Body and Off-Body), Therapy (Immuno-oncology, Diabetes, Cardiovascular diseases), technology (Spring-based, Motor Driven, Rotary Pump, Expanding Battery), Care Setting (Hospitals) & Region – Global Forecasts to 2026”. MarketsandMarkets Research, Jul 2021.