Citation: Kaufman S, Golfetto P, “Can Wearable Devices Bridge the Gap Between Pen Injector and Pump?”. ONdrugDelivery Magazine, Issue 100 (Sep 2019), pp 14-18.
Steven Kaufman and Paolo Golfetto explore the potential for wearable injectors to be disruptive technologies in the drug delivery market.
“A new category of wearable products is emerging, bridging the gap between functionality and cost, while introducing improvements to patient safety and quality of life.”
As we consider the drug delivery market today, there is a convergence of trends pointing towards a demand for innovative device solutions that can administer medicine reliably, monitor compliance and improve patient quality of life. This is providing fertile ground for disruptive technologies to emerge that offer new levels of functionality and usability – even in a therapeutic area such as diabetes, that helped to pioneer the use of self-injection systems.
DIABETES GROWTH RATES
According to the International Diabetes Federation (IDF) Diabetes Atlas 2018, the global diabetic population is expected to grow by 48% per year between 2017 and 2045. Global trends show how diabetes incidence will rise much more in low- and middle-income countries than in high-income countries: India is predicted to have the highest growth in absolute values (+70 million diabetic people), moving from second in 2017 to first in 2045 in terms of diabetic population, while the North Africa region will almost double with a 106% increase, and China will move to having 119 million people with diabetes.
DEVICE LANDSCAPE
The landscape of devices used to deliver insulin has traditionally been divided into two categories: pen injectors and vials/syringes on one side, and insulin pumps on the other. Each category offers different levels of functionality and usability at a very different therapy cost.
At present, for patients who inject insulin, approximately 95% of those receiving treatment for Types 1 and 2 diabetes use a syringe or pen injector. Patients on multiple daily injection (MDI) therapies for Type 1 and Type 2 typically require 3–5 injections of insulin a day. Administration requires several, non-discreet preparation steps that can lead to patients delaying therapy to avoid injecting in public.
The frequency of injections can also be difficult to track, leading to missed doses or even double doses. Monitoring patient compliance is difficult for doctors, making it hard to make effective adjustments to treatment. These challenges are compounded when administering injections to children.
Compared with pen or syringe systems that only dispense discrete doses of insulin, pumps are intended to deliver insulin continuously at an adjustable flow rate, are therefore better suited for complex therapy regimens, and are typically adopted for Type 1 diabetes. The electronics and software architecture of the device gives patients and healthcare professionals better monitoring capabilities – and the ability to conceal the device is preferable for patient quality of life and compliance.
However, preparing the pump for use requires a more complex handling process, including programming the device correctly and transferring the drug to an internal reservoir. Ensuring the pump delivers a small and precise dose brings an increase in the device development and manufacturing costs. With an annual cost of therapy that is more than double that of a pen injector, many countries will only reimburse a pump system for Type 1 diabetes.
THE PATIENT EXPERIENCE
A quantitative internal survey was conducted in 2017 by the agency Curth & Roth for Medirio, a Stevanato Group company, involving a sample of 960 participants aged from 20 to 65. The survey was conducted in Germany, Italy, France, UK and the US – and included 460 diabetic patients and 500 professionals including nurses/educators, internists, diabetologists and endocrinologists.
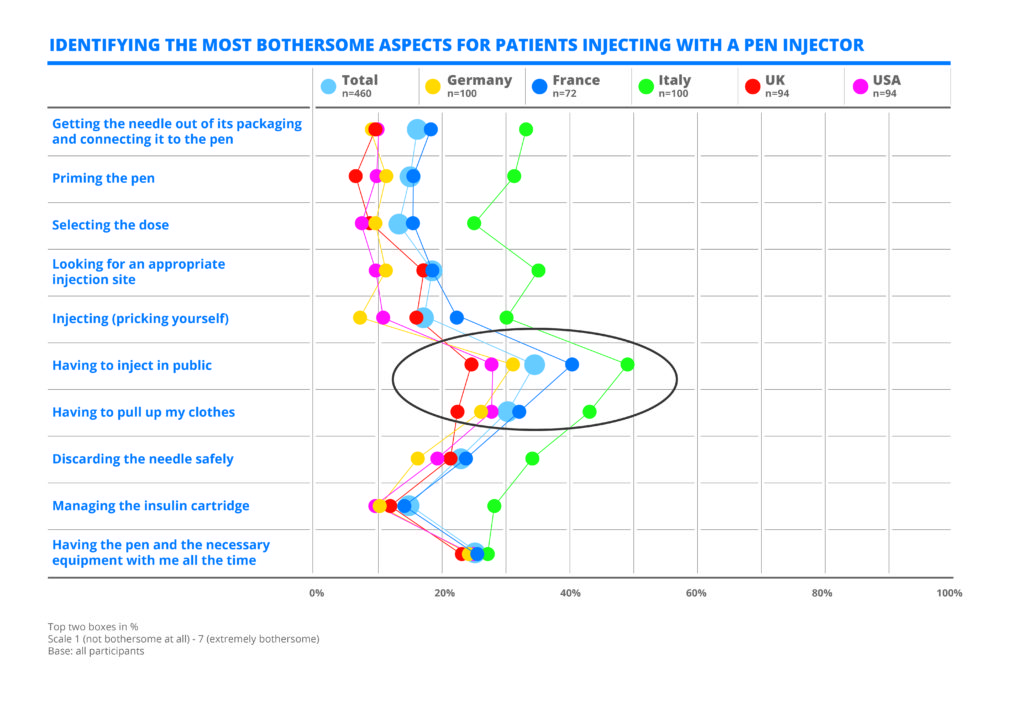
Table 1: A quantitative survey by Curth & Roth performed in 2017 for Medirio, a Stevanato Group company, shows diabetic patients using pen injectors objected most to having to inject in public and having to pull up their clothes.
The survey (Table 1) showed that insulin-dependent people who used pen injectors objected most to:
- Having to inject in public
- Having to pull up their clothes.
Besides discretion, other concerns included the fear of needles and of painful injections, which was reported mostly by new insulin users. Many patients expressed shock at the lifestyle changes required, continually having to carry medical supplies and ensuring that insulin doses were accurate and never missed. The feedback provided an insight into the desire of patients to be able to live with regular medicinal treatment while still having an active and social lifestyle.
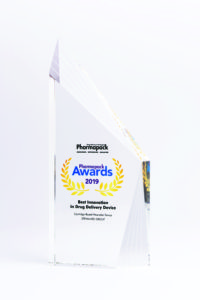
Figure 1: Stevanato Group’s cartridge-based wearable device received the Best Innovation in Drug Delivery Device award at this year’s Pharmapack event in Paris.
WEARABLES – BRIDGING THE GAP
A new category of wearable products is emerging, bridging the gap between functionality and cost, while introducing improvements to patient safety and quality of life. One example is the cartridge-based wearable device currently under development by Stevanato Group, which received Best Innovation in Drug Delivery Device award at this year’s Pharmapack event in Paris (Figure 1). The product comprises a disposable, wearable pod and an intelligent, reusable handheld controller that serves as the user interface and control unit for the pod (Figure 2).
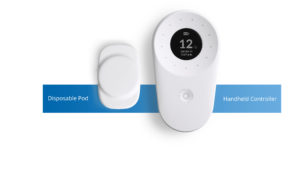
Figure 2: The reusable handheld controller
activates the disposable pod, bridging the gap
between the functionality of pump technologies and the cost of peninjector technologies.
By separating the drug delivery system’s mechanical components into a disposable pod, and the electronic components for dose selection and verification into a reusable handheld controller, this new self-injection device can bridge the gap between the functionality of pump technologies and the cost of pen-injector technologies. The system has several features that have been carefully considered from an end-user perspective (Table 2).
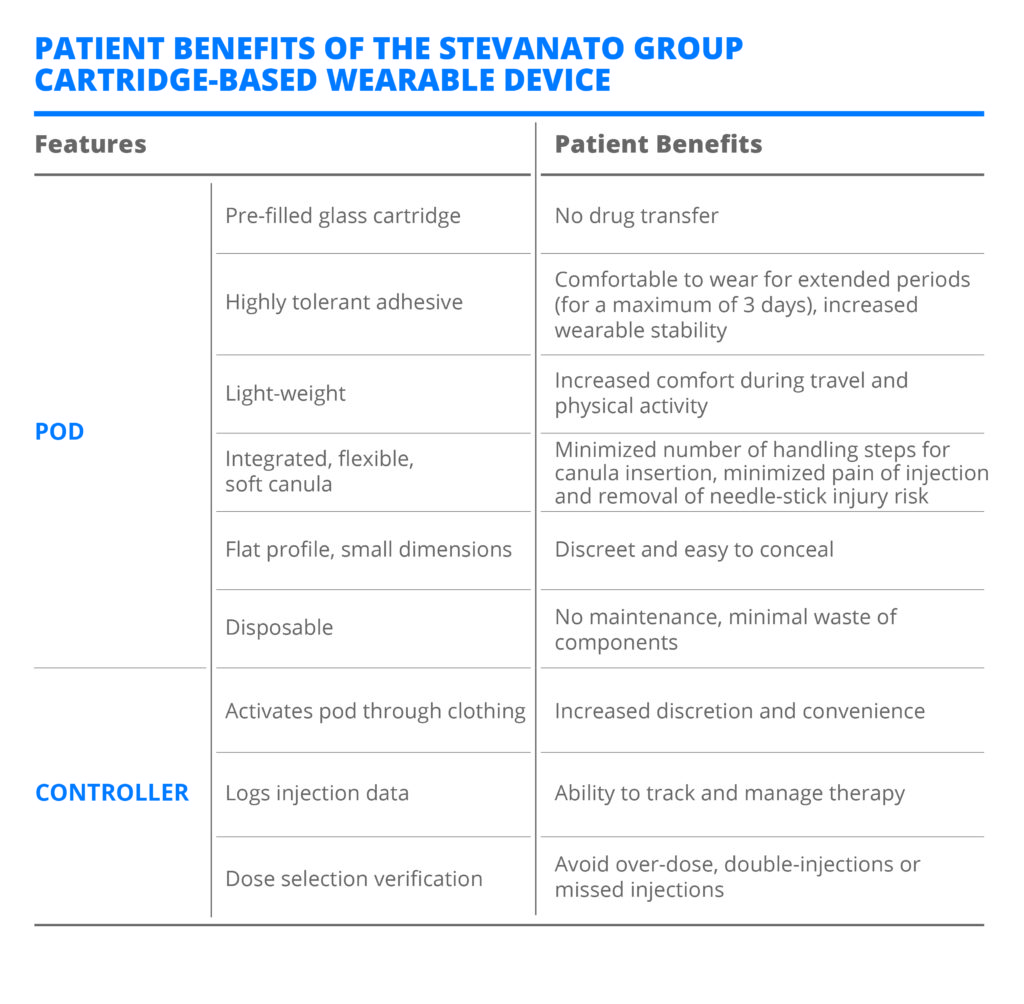
Table 2: Patient benefits of the Stevanato Group cartridge-based wearable device.
PRODUCT HANDLING
In terms of handling the product, the user – or the healthcare provider, if used for other non-insulin therapies – first inserts the factory-sealed, sterile cartridge into the pod (Figure 3). This is designed to be intuitive, easy to use and quick. The patient then removes the backing to an adhesive sticker and places the pod on the body. This can be done earlier than required and then activated later during the day.
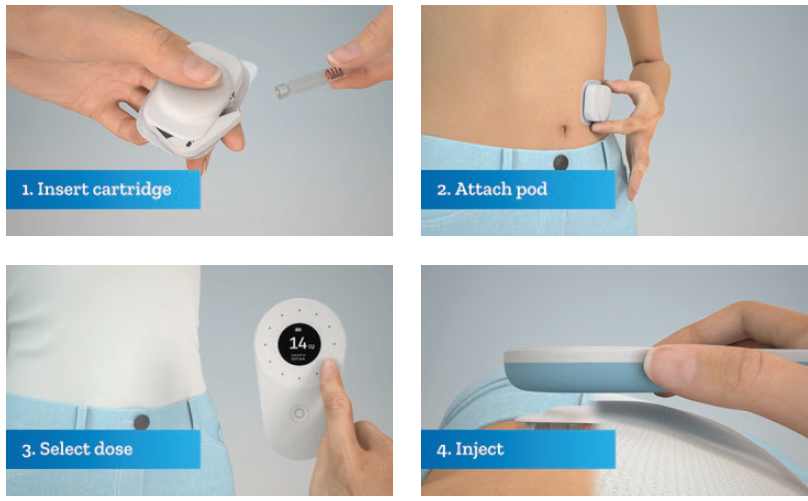
Figure 3: Steps to activate the self-injection cartridge-based wearable device by Stevanato Group.
Once attached to the body, the user triggers the cannula insertion with the controller and the system is ready to begin injection. Then, for each dose required, the user selects the dose using the handheld controller. The user then places the controller in proximity above the pod to mechanically activate the injection. The pod unlocks and receives energy to begin the drug delivery. Injection durations can last up to 10 seconds and the pod remains attached to the skin for up to 72 hours.
ADVANCING THE INDUSTRY
Thanks to its innovative yet simple technology, this system provides new levels of comfort, convenience and discreetness that can improve patient quality of life in therapeutic areas (TAs) other than diabetes. The handheld controller uses magnetic coupling to manage the interaction with the pod and, thanks to Bluetooth connectivity, it allows injection data to be exchanged.
The ability to track and share injection data can help to improve patient adherence and therapy outcomes. Stevanato Group is currently evaluating how additional features and customisations could be integrated for different TAs, such as:
- Hormone therapy
- Pain relief
- Alzheimer’s disease
- Rare/orphan drugs.
Since these TAs may require a different user interface or different ways for doctors patients, a thorough case study needs to be developed around the device, according to each different area, in co-operation with biopharma partners. Thanks to its integrated capabilities, Stevanato Group can manage the product development up to industrialisation as well as having the ability to add customisation.
DEVICE MANUFACTURING PARTNER READINESS
Bringing a device to market is complex. Biopharma companies are required to work with a range of speciality service providers in manufacturing, primary container, equipment and so on. Having one partner that can offer the required capabilities and services under one roof – from the container closure system to the assembly technology – is a key advantage to help ensure manufacturing readiness and reduced time to market.
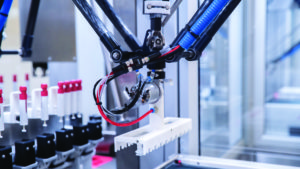
Figure 4: Flexible and modular assembly line developed and produced at Stevanato Group for pen injectors.
Stevanato Group provides a range of flexible, scalable capabilities to handle device projects such as safety systems, pen injectors (Figure 4), autoinjectors, wearables and inhaler systems – whether it’s done with proprietary IP developed by Stevanato Group or when Stevanato Group is acting as a contract manufacturer to produce the devices of biopharma companies.
Services range from designing, producing, testing and controlling a glass container’s integrity to the integration of ready-to-use prefillable syringes and cartridges into the ever-increasing number and range of drug delivery devices. Stevanato Group provides precision injection moulding and tooling, and product development services, within an ISO13485 quality system at US FDA-audited facilities.
Flexible, modular sub-assembly and final assembly and packaging of medical devices is carried out, with inline quality control to ensure final product quality. Stevanato Group is well positioned to optimise performance of the entire system, with one point of contact and responsibility for the customer.
Since the 1990s, Stevanato Group’s high-performance glass primary containers – whether they’re syringes, cartridges or special formats – have been used effectively in a number of devices on the market today. With the acquisition of further knowledge in injection moulding and tooling – as well as the incorporation of inspection, assembly and packaging capabilities – the company is now looking forward to bringing its wearable device and other self-injection devices to market to support the needs of biopharma customers, in co-operation with its partners. or pharmacists to prescribe the device to patients, a thorough case study needs to
be developed around the device, according to each different area, in co-operation with biopharma partners. Thanks to its integrated capabilities, Stevanato Group can manage the product development up to
industrialisation as well as having the ability to add customisation.
DEVICE MANUFACTURING PARTNER READINESS
Bringing a device to market is complex. Biopharma companies are required to work with a range of speciality service providers in manufacturing, primary container, equipment and so on. Having one partner that can offer the required capabilities and services under one roof – from the container closure system to the assembly technology – is a key advantage to help ensure manufacturing readiness and reduced
time to market. Stevanato Group provides a range of flexible, scalable capabilities to handle device projects such as safety systems, pen injectors (Figure 4), autoinjectors, wearables and inhaler systems –
whether it’s done with proprietary IP developed by Stevanato Group or when Stevanato Group is acting as a contract manufacturer to produce the devices of biopharma companies.
Services range from designing, producing, testing and controlling a glass container’s integrity to the integration of ready-to-use prefillable syringes and cartridges into the ever-increasing number and range of
drug delivery devices. Stevanato Group provides precision injection moulding and tooling, and product development services, within an ISO13485 quality system at US FDA-audited facilities.
Flexible, modular sub-assembly and final assembly and packaging of medical devices is carried out, with inline quality control to ensure final product quality. Stevanato Group is well positioned to optimise performance of the entire system, with one point of contact and responsibility for the customer.
Since the 1990s, Stevanato Group’s high-performance glass primary containers – whether they’re syringes, cartridges or special formats – have been used effectively in a number of devices on the market today. With the acquisition of further knowledge in injection moulding and tooling – as well as the incorporation of inspection, assembly and packaging capabilities – the company is now looking forward to bringing its wearable device and other self-injection devices to market to support the needs of biopharma customers, in co-operation with its partners.