To Issue 156
Citation: Jamal H, Köhler C, “Navigating ISO 11608 with Automated Equipment for Customised Pen and Autoinjector Testing”. ONdrugDelivery, Issue 156 (Jan 2024), pp 112–116.
Hisham Jamal and Carsten Köhler discuss how teamtechnik’s automated testing machines – built on the foundation of assembly automation legacy – seamlessly align with the ISO 11608 regulations, effectively shaping the future of pen and autoinjector testing.
“Manufacturers can benefit from teamtechnik’s fully automated testing equipment as it combines robotics, cutting-edge sensor technologies and clever software algorithms to carry out the testing process.”
The easy administration, high reliability and mobility of pen injectors and autoinjectors has led to widespread acceptance of these self-administered medical devices, resulting in a projected compound annual growth rate of 11%–16% from now until 2030.
Teamtechnik has been active in the development and manufacturing of these injection devices for more than 40 years and continues to support its global customer base with current and future manufacturing needs. Grounded in the assembly of these devices, teamtechnik’s experience has offered unique insights into their intricate functionalities. This deep-seated understanding of the devices and their operation is what has guided the company in the development of its automated testing machines. This understanding is applied to ensure that the devices not only function optimally but also adhere strictly to the quality and safety standards mandated by the international medical community.
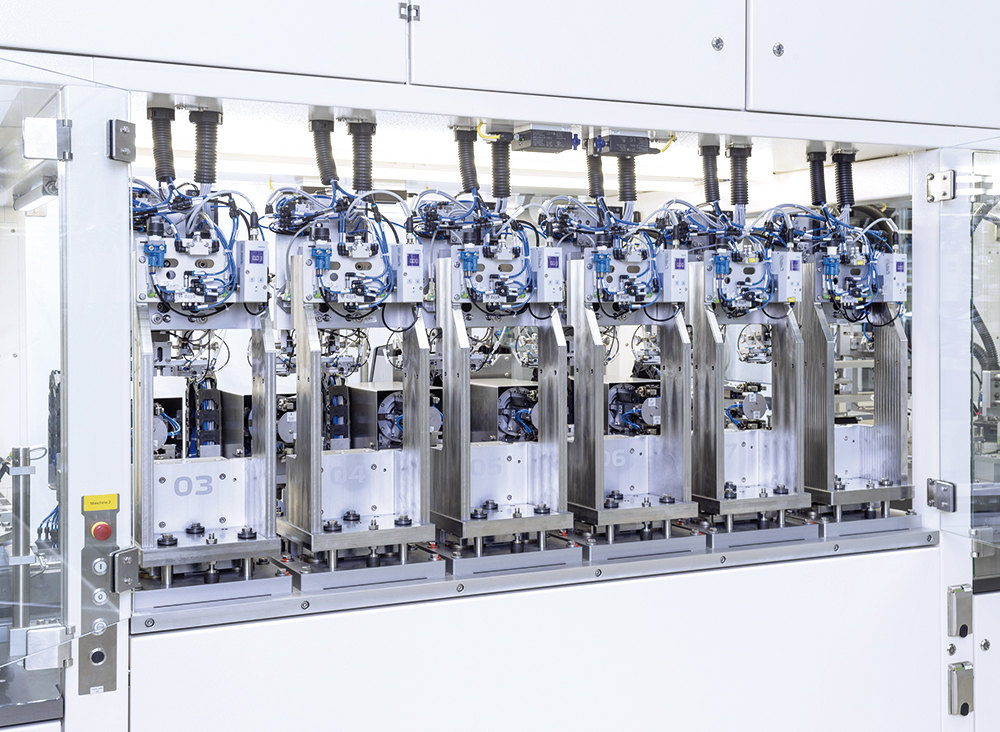
Figure 1: Process detail of an injector test system.
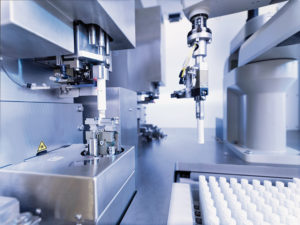
Figure 2: TEAMED injector test system by teamtechnik.
From simple table top test benches to fully automated batch and/or 100% inline tests (depending on the product and functionality), teamtechnik’s machines – designed with a blend of practical experience and keen understanding of ISO 11608 – are setting new standards in medical device testing (Figures 1 and 2).
UNDERSTANDING REGULATIONS
The medical regulations in the EU and other sophisticated markets are now viewing pen injectors and autoinjectors less as secondary packaging and more as a combination product as their popularity and demand soar on the global market – with a combination product defined as a fully integrated drug and delivery device unit. The regulations for these devices are therefore becoming more stringent in order to guarantee their quality, safety and efficacy.
The EU Medical Devices Regulation (MDR) 2017/745 mandates that combination products must conform to the general safety and performance requirements as listed in Annex 1 of the MDR, thereby holding these devices to stricter requirements on quality, safety and performance, as well as measures such as unique device identification on packaging and devices to improve traceability.
The US FDA also categorises pen injectors and autoinjectors as combination products. They must therefore comply with the FDA’s 21 CFR Part 820 and cGMP requirements. The subpart H of the 21 CFR Part 820 is attributed to acceptance activities where it mandates each manufacturer to establish and maintain procedures for finished device acceptance so as to ensure that each production run, lot or batch of finished devices meets acceptance criteria. The acceptance activities, and the documentation and review prior to release for distribution and the maintenance of acceptance records, are also specified in this section.
ISO 11608 details the applicable standards for a needle-based injection system (NIS),1 with ISO 11608 part 52 specifically outlining the definitions, requirements and testing criteria pertaining to needle-based injection systems with an automated function (NIS-AUTO). Injection devices, such as pen injectors and autoinjectors, are governed by these standards. While adherence to certain ISO standards is largely voluntary for companies, regulatory authorities, such as the FDA and EMA, are increasingly referring to ISO standards for their device approval framework.3
“Testing the dosing mechanism prior to final assembly acts as the first line of defence in preventing the integration of a flawed dosing mechanism that could compromise the efficacy and reliability of the entire device.”
Global regulatory frameworks for these devices are developing and evolving constantly in response to industry, market and customer requirements. Further updates to existing regulations are also expected over the coming years – making it important for device manufacturers to work closely with expert partners so that they can be confident they have the right resources to help them meet the strict regulatory requirements and ensure that they offer a seamless experience for their end users. Manufacturers can benefit from teamtechnik’s fully automated testing equipment as it combines robotics, cutting-edge sensor technologies and clever software algorithms to carry out the testing process, while guaranteeing complete traceability and accurate and consistent documentation.
AUTOINJECTOR TESTING
An autoinjector is a single-use device that consist of a triggering unit, a holder for the prefilled syringe and an integrated cannula. When the triggering unit is activated, it drives the cannula and a spring-loaded plunger helps to administer the dose in the cartridge to the user. A needle retraction or needle shielding mechanism is also usually incorporated in an autoinjector to ensure the safety of users. As an NIS with an automated function as described above, regulations specified under ISO11608 (in general) and specifically ISO11608-5 are applicable here.
The ISO 11608-5 outlines the requirements and test methods for medicinal product preparation, needle inspection, needle hiding, priming, needle extension, dose accuracy, injection time, disabling, needle retraction and needle shielding – and recommends using a risk-based approach for verifying functions such as dose setting, recording device functions and needle removal. Of these, product preparation, dose accuracy, injection time, needle extension, retraction, disabling and shielding are relevant for autoinjectors.
Aligning with ISO11608 requirements, teamtechnik has developed and executed autoinjector tests with associated parameters, as listed in Table 1.
11608-5 requirement | teamtechnik test executed | Test type/ parameter |
Product Preparation | Needle Cap Removal Force | ≤30 N |
Priming/Activation | Activation Force (for 2 or 3 step AI) |
4–18 N |
Needle Extension | Injection Depth | 4–7 mm |
Dose Accuracy | Dosing Volume Measurement | by weight |
Injection Time | Injection Time | 3–18 sec |
Needle Retraction | Needle Retraction Check | Camera Check |
Needle Shielding | Needle Shield Check | ≤3 mm @ 75 N |
Table 1: Autoinjector tests as per ISO 11608-5.
PEN INJECTOR TESTING
A pen injector is a multi-use, variable dosage device that consists of dosing mechanism and a cartridge holder. A rotary button on the pen injector is used to adjust the dosage to be administered and a display window shows the set dosage quantity. Pressing down the button will administer the set dosage to the user. To use a pen injector, however, the user needs to attach the injector to a pen needle. Teamtechnik’s test machine for pen injector testing executes both the assembly and the testing of the complete pen injector unit. The testing machine removes the cap of the pen injector and connects it to a pen needle before the following tests are executed as per the regulations.
Aligning with ISO11608 requirements, teamtechnik has developed and executed, pen injector tests with associated parameters, as listed in Table 2.
11608-5 requirement | teamtechnik test executed | Test type/ parameter |
Product Preparation | Pen Needle Assembly on Pen Injector |
Assembly |
Priming/Activation | Dosing Force Measurement | 0–45 N |
Dose Accuracy | Dose Measurement | by weight |
Dose Setting | Set Dosage Measurement |
0–45 N By weight |
Recording Device Functions | Dosing Window Inspection Corresponding to Dosing Force/Dose Measurement | Camera Check |
Table 2: Pen injector tests as per ISO 11608-5.
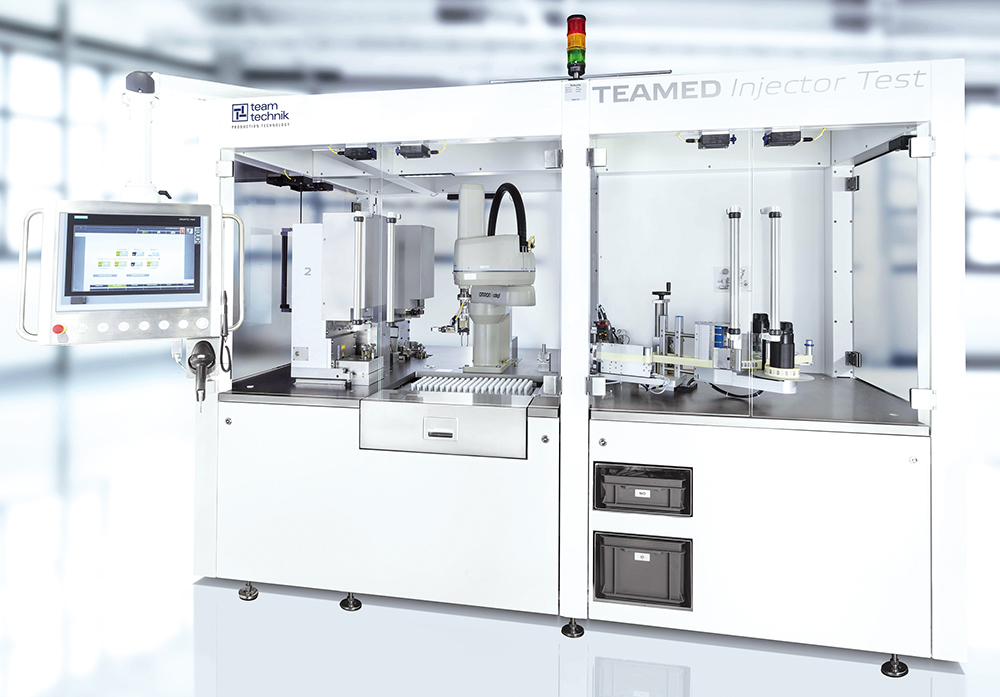
Figure 3: 100% inline test of an injection pen.
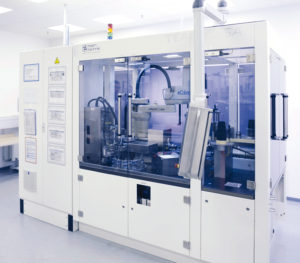
Figure 4: Standalone test system for injection systems.
DOSING MECHANISM TESTING
The dosing mechanism plays a crucial role in accurately delivering medication to patients through an injector pen. Testing the dosing mechanism prior to final assembly acts as the first line of defence in preventing the integration of a flawed dosing mechanism that could compromise the efficacy and reliability of the entire device. Identifying and rectifying any issues with the dosing mechanism at this early stage in the production process significantly reduces the unnecessary wastage of pharmaceutical products, as well as ensuring that only devices with impeccably functioning dosing mechanisms proceed to final assembly. Although ISO11608 or other regulations do not mandate the testing of the dosing mechanism in itself, but rather on the complete injector pens, manufacturers are increasingly testing the dosing mechanism pre-assemblies prior to final assembly align their principles of operational efficiency with their commitment to responsible use of pharmaceutical resources. To help them with this, teamtechnik has developed and executed both inline (Figure 3) and standalone (Figure 4) testing machines for dosing mechanism testing.
With the inline testing machines, each and every dosing mechanism is tested for its functionality as it progresses through the assembly line. This real-time assessment ensures that every device meets the required operational standards and provides immediate feedback for any necessary adjustments or interventions. This is particularly well suited for high-volume production lines where real-time quality control is essential for maintaining efficiency and precision.
Standalone testing machines, on the other hand, test a representative sample of dosing mechanisms in a separate, dedicated testing phase, in the same way that most batch release tests are executed. This allows for a more comprehensive assessment of a batch of components, offering a holistic view of their collective quality – making this a more suitable testing approach for smaller production runs where heightened scrutiny is required.
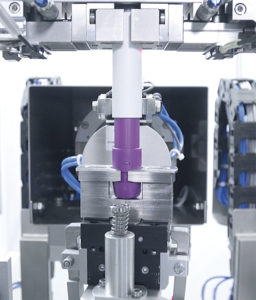
Figure 5: Torque measurement.
CALIBRATION
To ensure the accuracy and consistency of the testing equipment to perform the highest standards of compliant testing, teamtechnik – together with its customers – develops stringent calibration protocols that cover the various equipment and instruments that need calibration and defines their corresponding frequency or intervals of calibration schedules, depending on factors such as frequency of use, required accuracy, etc.
The protocol includes both functional and metrological calibration, either by comparison with the source of known standard value or by comparison with measurement from a calibrated reference instrument. For precision-critical tests, such as dose accuracy, activation force, etc, a more frequent calibration schedule is often warranted to ensure the integrity of the test results, while less sensitive tests may require less frequent calibration. In any case, the testing machines are programmed to run automated calibration modes at defined intervals where they automate the execution of the predefined calibration processes. For example, Figure 5 shows torque measurement and Figure 6 shows weight calibration.
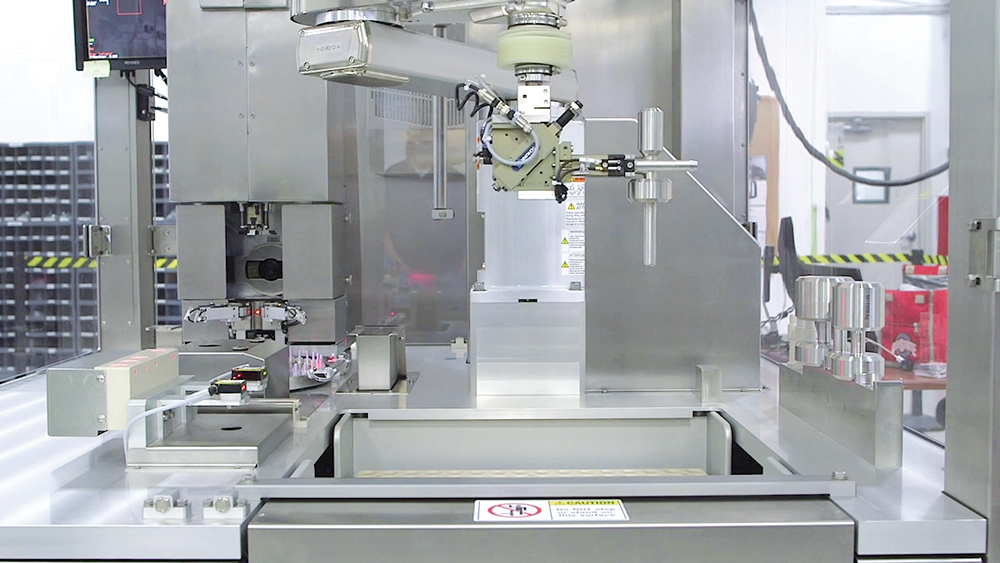
Figure 6: Weight calibration.
A comprehensive documentation of calibration activities, including the recording of calibration results and adjustments made, is also recorded by these machines –thereby providing a new level of traceability, transparency and accountability in adhering to the reference standards.
QUALIFICATION
The testing machines play a vital role in the quality control of pen and autoinjector devices and, as such, their qualification is essential to ensure the safety and efficacy of the final products they test. Teamtechnik follows a comprehensive qualification process in line with GMP compliance, satisfying relevant machine directives and ISO standards – ensuring that the testing machines are fit for their intended purpose and comply with regulatory guidelines, such as those set forth by the FDA and EMA.
It is important to note that the qualification process for these automated testing machines shares similarities with the process of assembly machines for pen injectors and autoinjectors, particularly in terms of ensuring compliance with regulatory standards and the specific requirements of the devices being tested and assembled. However, the focus and criteria for validation differ significantly, as the testing machines are primarily assessed based on their ability to accurately and reliably test the functionality and performance of finished pen injectors and autoinjectors, while assembly machines are evaluated based on their ability to consistently and accurately assemble the devices according to predefined specifications.
CONCLUSION
Teamtechnik develops high-quality and reliable testing machines in line with international standards and regulations. By doing so, the company contributes to its broader goal of enabling its customers to produce and bring consistently high-quality medical devices to the market – and thereby contributing to improving overall patient health and safety.
Drawing from its rich history in custom machine building, teamtechnik has acquired a deep understanding of the unique challenges and complexities involved in the production and testing of pen and autoinjector devices. This expertise, coupled with the company’s proven track record in qualification and validation of complex automation machines, uniquely positions teamtechnik as a leading automated testing equipment manufacturer for pen injectors and autoinjectors. Combined with the company’s knowledge and commitment to compliance with EMA, FDA and ISO standards, it means teamtechnik can deliver cutting-edge testing solutions that not only meet but exceed the industry’s most stringent regulatory and quality demands.
Teamtechnik customers can be confident of receiving a state-of-the-art automated testing solution tailored to their specific needs, designed to uphold the highest standards of quality and regulatory compliance, and thoroughly validated and qualified to ensure the utmost precision, accuracy and reliability.
REFERENCES
- “Needle-based injection systems for medical use – Requirements and test methods – Part 1: Needle-based injection systems”. International Organisation for Standardization, 2012.
- “Needle-based injection systems for medical use – Requirements and test methods – Part 5: Automated functions”. International Organisation for Standardization, 2022.
- “Guidance for Industry and FDA Staff: Technical Considerations for Pen, Jet, and Related Injectors Intended for Use with Drugs and Biological Products”. US FDA, Jun 2013.