To Issue 153
Citation: Astle M, Jenkins G, Mayo E, “Transforming Pharmaceutical Manufacturing to Drive Sustainability and Cost Efficiency”. ONdrugDelivery, Issue 153 (Oct/Nov 2023), pp 33–35.
Bettine Boltres and Shivani Polasani discuss how pharma can progress towards a more sustainable future, and consider the role that the collaboration between Corning and West Pharmaceutical Services can play in supporting pharma’s sustainability goals.
In an industry where compassion and empathy for humankind are deeply rooted and values widely subscribed to, it should come as no surprise that the pharma industry is making significant efforts to address the sustainability conundrum. Whether as a pharmaceutical manufacturer or drug containment provider, the industry’s primary role is to enhance and help save the lives of patients, ensuring that the safety and efficacy of the drugs used are safeguarded without compromise. That said, there is now an equally vital imperative – to support the global impetus to reduce carbon dioxide equivalent (CO2e) emissions and help to create a more sustainable planet.
The question is therefore not if, but how, we can work towards a more sustainable future while protecting the interests of the patients we serve. The answer, specifically in injectables, has unequivocally been answered by the work undertaken by the West Pharmaceutical Services and Corning collaboration.
“The simple reality is that pharma and its supply chain partners must continue to do more work together to achieve greater sustainability heights while ensuring that the safety and efficacy of the drugs manufactured is maintained.”
THE SIZE OF THE CHALLENGE SHOULD NOT BE UNDERESTIMATED
According to Deloitte, the global greenhouse gas emissions directly generated by the pharma industry are estimated to be around 52 megatonnes of CO2e per year.1 This figure does not include indirect energy-related emissions through the entire supply chain, such as transportation, cold chain, etc, which contribute further to the final figure.
Another report estimates that the industry generates about 48.55 tonnes of CO2e per US$1 million (£821,000) in revenue generated, which is 55% higher than the emission intensity estimated for the automotive industry, i.e. 31.4 tonnes of CO2e per $1 million generated.2
If we take the injectables segment, Corning estimates that over 150,000 tonnes of Type 1 borosilicate glass is used annually in the global production of pharmaceutical vials. Due to complex regulations, most of this glass is discarded as medical waste each year, filling landfills across the world, according to internal estimates based on Corning Type 1 glass tubing production and awareness of industry capacity.
The simple reality is that pharma and its supply chain partners must continue to do more work together to achieve greater sustainability heights while ensuring that the safety and efficacy of the drugs manufactured is maintained. West believes that sustainability should be considered an integral component along with safety, efficacy and the manufacturability of pharmaceutical drugs.
In response to this imperative, many pharma companies have adopted ambitious plans with measurable goals; however, such a transformative change does not happen overnight and, for some, bridging the gap between high aspirations and meaningful, measurable action can be challenging.
THE HEAT IS ON
A greater number of consumers and investors are paying real attention to a brand’s sustainability track record and overall values when it comes to company reputation and ethics. Beyond product performance, more and more are now actively discerning which brands to purchase or invest in based on criteria such as sustainable packaging, reduced waste in manufacturing, a commitment to ethical manufacturing standards and reducing overall global warming potential (GWP).3
This attitude is not lost on pharma executives. Indeed, in one report, 80% of sustainability leaders in pharma said that they “strongly agreed” or “agreed” that their organisation was extremely concerned about the impact of climate change on their business, with 92% reporting that they were concerned about their organisation’s impact on the environment.4
As global warming continues to threaten the planet, there is therefore no question that the heat is on to address the GWP of all manufacturing operations, including pharmaceuticals. There is, of course, another important dynamic to this imperative – how to ensure any improvements made in terms of sustainability do not compromise the safety, efficacy and operational efficiency embedded in the manufacturing of pharmaceutical products (Figure 1).
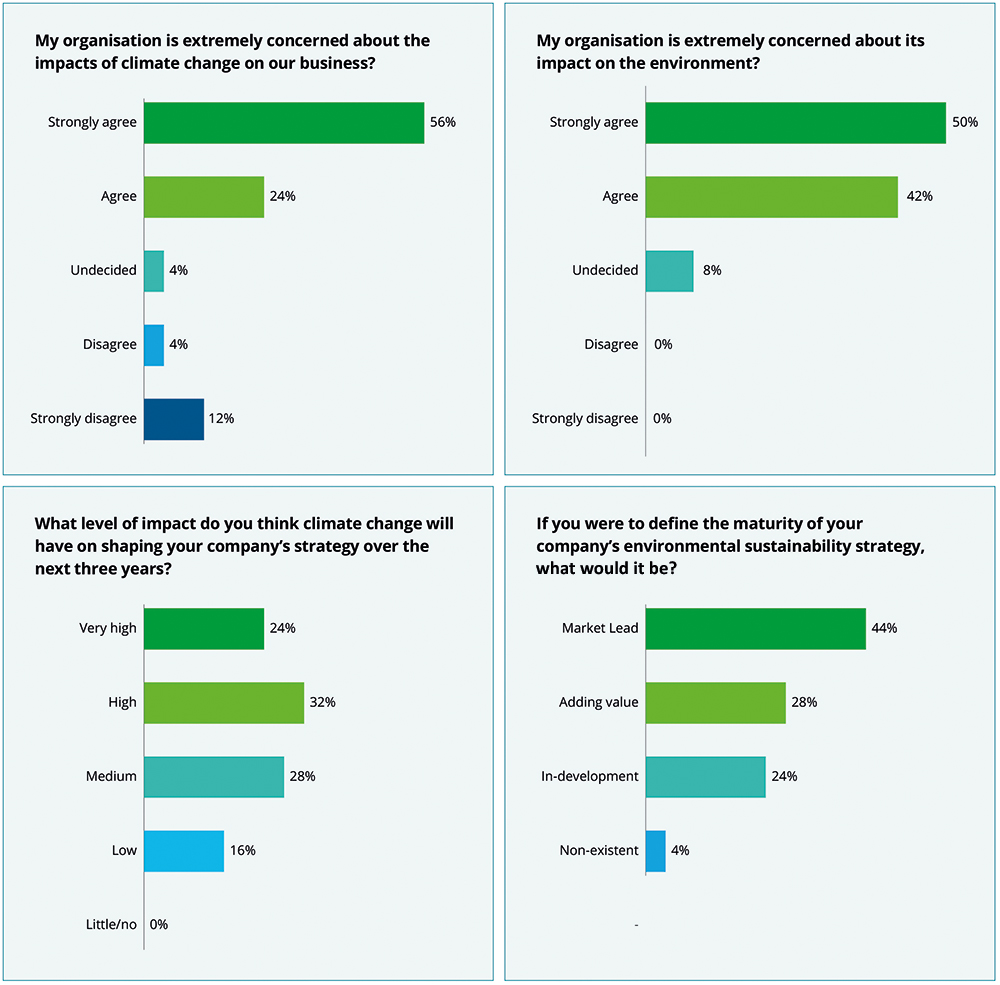
Figure 1: Pharma’s attitudes towards sustainability.4
PERFORMANCE MUST MEET SUSTAINABILITY
Building on the recent collaboration with West and Corning, which brings together more than 200 years of experience, the team is now taking on this challenge and is excited to bring Corning® Viridian™ vials to the market, directly addressing the thorny challenge of meeting performance and sustainability together in a system-level containment solution. The exclusive supply and technology agreement provides pharma partners with access to some of the most innovative products in parenteral drug delivery.
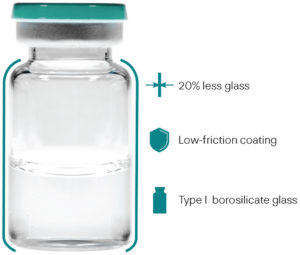
Figure 2: Viridian Vials’ protective external coating can reduce damage that leads to cracks, breaks and cosmetic rejects.
Corning® Viridian™ Vials are a transformative innovation that reduce glass waste and manufacturing emissions without compromising manufacturing efficiency. Indeed, data demonstrate that Viridian™ Vials reduce material waste by 20%, while reducing CO2e emissions by up to 30%.* Additionally, filling-line data with Optima (a leading manufacturer of fill-finish equipment based in Schwaebisch Hall, Germany) demonstrates the ability of Viridian™ Vials to increase fill-finish efficiency by up to 50%.** It can also reduce cosmetic rejects and lower glass particle generation by up to 96% (Figure 2).
As a design that included sustainability from first principles, the Viridian™ Vial is a market first. The metrics have been achieved by reducing the wall thickness of the vial, reducing the overall mass from the conventional 2R that weighs 4.4 g. There is another added sustainability advantage too – a thinner wall creates additional capacity in the vial itself, enabling the use of potentially fewer vials to meet demand.
Taking the additional step to substantiate emission reduction claims, Corning worked with Sphera, a leading provider of Environmental, Social and Governance performance and risk management software, to conduct a cradle-to-gate, third-party lifecycle assessment (LCA), which compared Corning® Viridian™ vials with conventional borosilicate vials. The report discusses how Viridian™ Vials can reduce CO2e emissions by up to 30%. Furthermore, the report additionally shows that even compared with conventional vials manufactured with 100% renewable electricity, Viridian™ Vials can reduce emissions by up to 15%. The LCA is currently undergoing independent peer review to further validate the claims.
LOWER GWP, SAME SPECIFICATION, NO COMPROMISE
Breaking down the per-vial CO2e improvement by category, the LCA shows a reduction of 0.3 g of CO2e from raw material extraction, 11.2 g of CO2e from manufacturing (tube forming, converting and coating) and 0.03 g of CO2e from tube and vial transportation. If these data were extrapolated to 10 million vials, Viridian™ Vials could save up to 114,000 kg of CO2e, which is equal to consuming more than 12,900 gallons of fuel, and eliminate around nine tonnes of glass from landfill waste (Figure 3).5
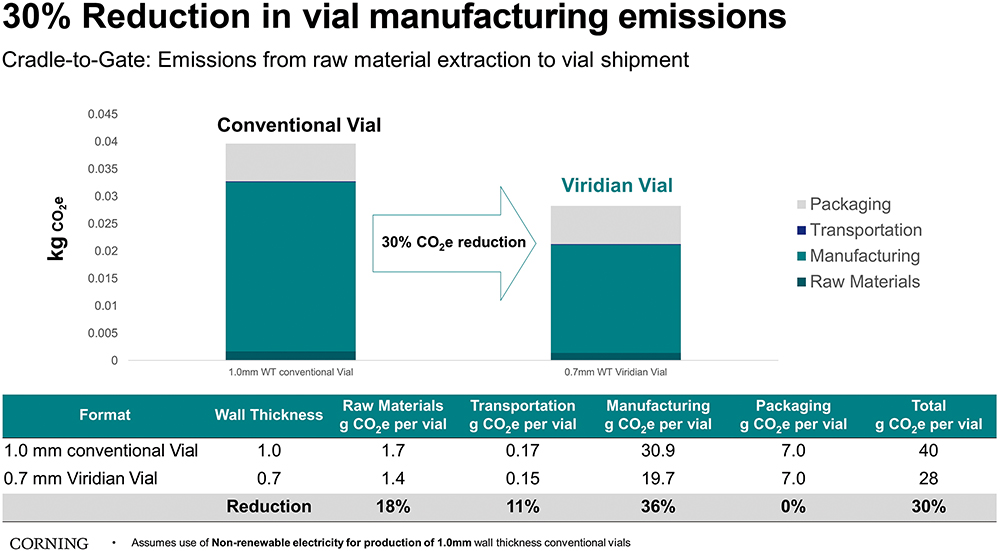
Figure 3: Third-party LCA of 2R standard conventional vials with 1.0 mm thickness vs Viridian Vials with 0.7 mm wall thickness.
Additionally, Viridian™ Vials, being borosilicate glass, are compliant with USP <660> Type I hydrolytic resistance testing and Ph. Eur. 3.2.1. They also meet ISO standards regarding outer and neck dimensions to mitigate the need for change parts on customer filling lines that already use ISO standard borosilicate vials (Figure 4).
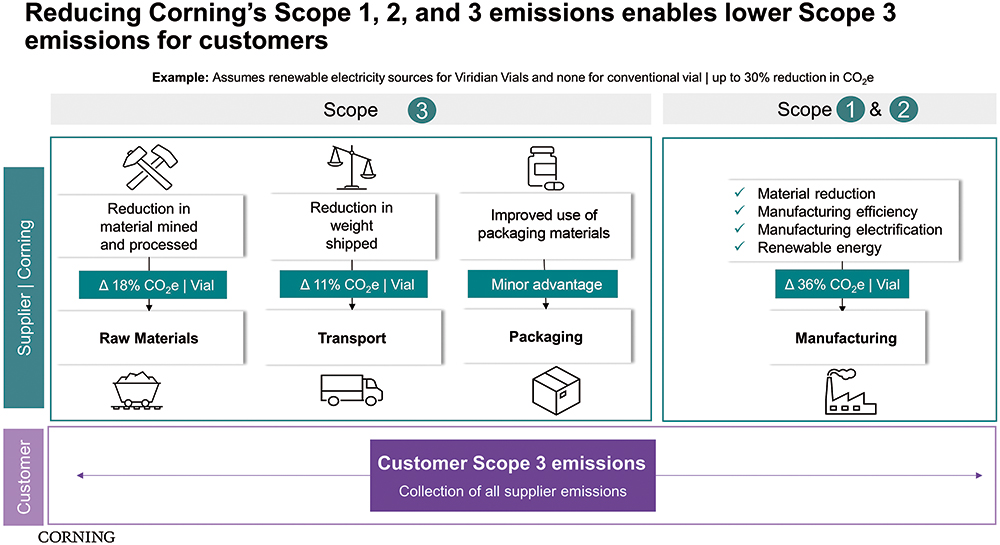
Figure 4: Reducing Corning’s scope 1, 2 and 3 emissions enables lower scope 3 emissions.
A PRODUCT IS NO GOOD IF YOU CAN’T HANDLE IT
In the development of Viridian™ Vials, it was essential that vial performance was not impacted by the product design. To this end, Viridian™ Vials can be seamlessly integrated into current fill-finish production facilities without the need for change parts on filling-line equipment and with equivalent or better vial breakage rates. The important point here, as the Optima data demonstrate, is that a thin-wall vial will have a high breakage rate and will not maintain performance rates without Corning’s protective coating.
Viridian™ Vials are equipped with Corning’s proprietary exterior coating that ensures the vial has a low coefficient of friction and maintains glass strength through fill-finish processing and transportation. This provides the basis for improved throughput and reduces the likelihood of vial damage, rejects and glass particles. Indeed, the external coating used on Corning® Valor® Vials and Viridian™ Vials can improve filling-line efficiency by 20% to 50%,6 with a reduction in the likelihood of damage that leads to cracks and breaks and a 96% reduction in glass particles.7 Improved efficiency also supports a reduction in pharmaceutical production costs.
PROVING PERFORMANCE
In collaboration with Optima, two vial types were tested; a standard uncoated 2R borosilicate vial (4.4 g) and a 2 mL Viridian™ Vial (3.5 g). The vials were run at 450 vials per minute and recirculated >120 times, simulating >200,000 vials processed for each group. The trial resulted in no breakages being observed in washing, depyrogenation, accumulation, singulation or while at the star wheels. The Viridian™ Vials demonstrated a lower tip over rate compared with conventional vials. There were no functional issues with washing or depyrogenation and no need for modification of fill-finish processes not additional change parts required.
THE PHARMA SUPPLY CHAIN HAS AN OBLIGATION TO DO MORE
When reporting emission data, the international standard is to classify energy usage and emissions into three categories, scope 1, 2 and 3. The three scopes are a way of categorising the different kinds of emissions that a company creates in its own operations (scope 1 and 2) and in its wider value chain (scope 3). The Greenhouse Gas Protocol defines it as “Developing a full [greenhouse gas] emissions inventory – incorporating scope 1, scope 2 and scope 3 emissions – enables companies to understand their full value chain emissions and focus their efforts on the greatest reduction opportunities”.8
While scope 1 covers emissions that an organisation owns or directly controls, scope 2 emissions are those that a company indirectly causes and come from the energy it purchases. Scope 3 encompasses emissions that an organisation is indirectly responsible for, up and down its value chain. Pharmaceutical companies are looking for suppliers to develop innovative solutions to support scope 3 emission reductions. Recently, much of the narrative at industry events has been about engaging the supply chain in helping pharma manage its scope 3 commitments.
Of course, in this setting, innovation needs to be “feasible”, meaning a drop-in solution that is accessible and balanced with pragmatism – the time/cost/risk paradigm is a paramount consideration for pharma. This is where Viridian™ Vials really deliver true value – they deliver demonstrable benefits with careful consideration to maintaining specification and operational efficiency. But this is just the beginning; the Corning/West collaboration will continue to innovate and further improve to support pharma’s sustainability efforts.
CONCLUSION
The supply chain has responsibility to work in partnership with pharma to better support its scope 3 commitments. There are, of course, many ways to achieve that goal, such as to improve operational efficiencies to increase the speed of manufacturing and reduce energy consumption, or invest in renewable energy, among others. To change the game regarding sustainability, there needs to be a measured and innovative approach. The first-of-its-kind Viridian™ Vial was created not only from a product perspective but from a wider ecosystem standpoint, delivering real gains in sustainability while positively impacting the overall sustainability credentials of the manufacturing environment. Hence, designing for sustainability does not need to cost the earth or compromise on traditional key performance indicators. The heat is on, but there is now a tangible opportunity to contribute to dialling down the temperature and delivering on those scope 3 sustainability aspirations.
* Corning in-house data – independent LCA by Sphera.
** Corning in-house data.
REFERENCES
- Murray K, “The future of the pharma industry can be sustainable”. CPI, Feb 24, 2022.
- “Overview report: Embedding environmental sustainability into pharma’s DNA”. Deloitte, Oct 2022.
- “How consumers are embracing sustainability”. Deloitte Web Page, accessed Sep 2023.
- “Overview report: Embedding environmental sustainability into pharma’s DNA”. Deloitte, Oct 2022.
- Greenhouse gas equivalencies calculator. United States Environmental Protection Agency. Accessed Sep 2023.
- Hall M et al, “Unlocking pharmaceutical fill/finish manufacturing with an innovative glass packaging solution”. White Paper, Corning, accessed Sep 2023.
- Timmons C L, Yuen Liu C, Merkle S, “Particulate Generation Mechanisms during Bulk Filling and Mitigation via New Glass Vial”. PDA J Pharm Sci Technol, 2017, Vol 71(5), pp 379–392.
- “We set the standards to measure and manage emissions”. Web Page, Greenhouse Gas Protocol, accessed Sep 2023.