Citation: Schopferer B, “Z.BLIZZARD Automation System for PFS: Improving the Lives of Patients. ONdrugDelivery Magazine, Issue 101 (Oct 2019), pp 98-100.
With the ultimate objective of improving patients’ lives, Berthold Schopferer provides an overview of the company’s customer-specific automated manufacturing and assembly equipment offering for prefillable polymer syringes.
Readily packaged, ready-to-fill staked-needle syringes have one goal: making handling medication easy. After all, the chronically ill are already burdened enough by their state of health. Cumbersome handling of their daily dose of medication – often more than one – would place an even greater burden on these patients. Not to mention the fact that dosing would be challenging. Prefilled syringes (PFS) actively contribute to making life easier for patients.
“If Z.MISTRAL, which handles downstream processing, and the Z.LODOS palleting system are added, the system covers the full process from COC/COP granulate to prefillable syringe.”
This places a demand on industry as well. Mould and mechanical engineering specialist ZAHORANSKY builds automation systems in different, very customer-specific variants for serial production. In doing so, the business implements the desired and required elements of modularity one by one. It goes without saying that this is based on the premise that the finished product will meet the high quality standards required and demanded in medical technology to ensure that the systems built protect the integrity of the product and thus the safety of patients.
GREATEST FREEDOM OF CHOICE FOR A TAILOR-MADE SYSTEM
Z.BLIZZARD (Figure 1), is the automation system from ZAHORANSKY that includes injection-moulding, and is therefore specially equipped with a sophisticated quality-assurance system: in current systems and upon request, more than ten camera systems ensure ongoing product control in the production process while an integrated 100% X-ray system ensures product control after assembling. More comprehensive quality assurance according to modern-day standards is barely possible. However, ZAHORANSKY does not rest on this success: and its mechanical engineering specialists are currently testing the use of an additional CT module in future systems for even finer quality control.
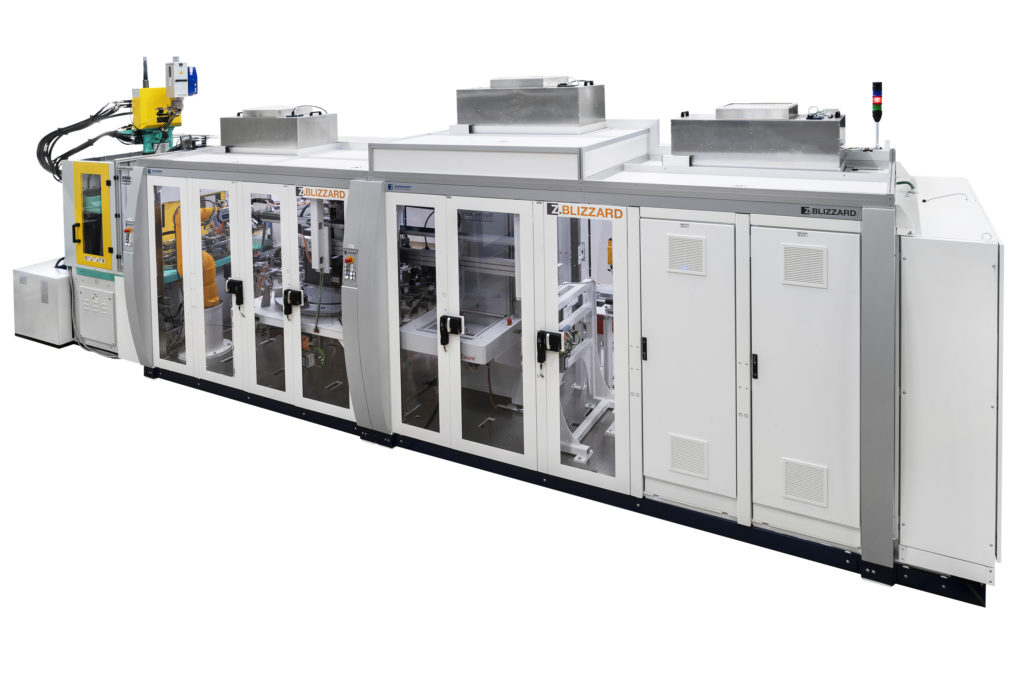
Figure 1: Z.BLIZZARD produces ready-to-fill, staked-needle-syringes from COC/COP polymers with a very high autonomy time.
The same careful procedure is also applied to clean-room modules. In this area, ZAHORANSKY relies on industry-proven systems to enable its customers to produce their products hygienically.
Customers can determine numerous specifications:
- Orientation of the needle – is it straight or bent?
- Areas covered by integrated X-ray examination
- Z.BLIZZARD configured with additional access doors.
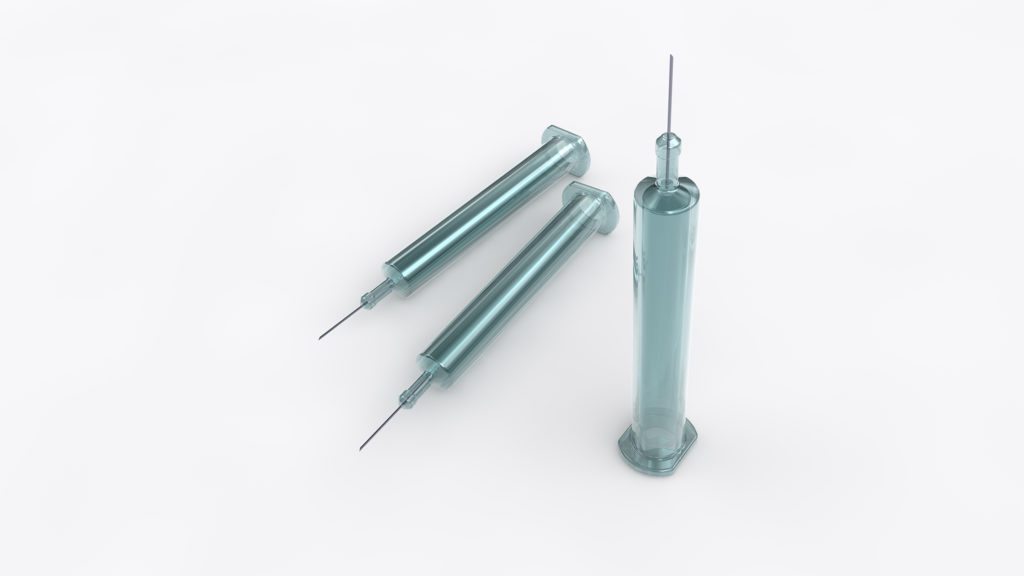
Figure 2: Z.BLIZZARD manufactures COC/COP prefillable syringes with distinct advantages over their glass counterparts, e.g. the needle is over-moulded, not welded or glued in.
From early in the process, these and other details are determined and subsequently executed precisely in close co-operation with the customer, who is consulted throughout the design and production process, which usually takes 12 months. Close collaboration throughout provides the customer with the best possible product.
Further customisation is made possible with additional integrated systems. A system that covers the full process chain from cyclic olefin copolymer/ cyclic olefin polymer (COC/COP) granulate to prefillable syringe (Figure 2) is formed when Z.MISTRAL, which handles downstream processing, and the Z.LODOS palletising system are connected with Z.BLIZZARD (Figure 3).
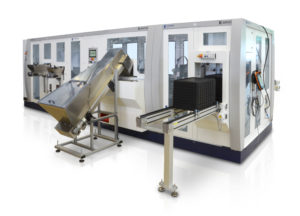
Figure 3: Z.MISTRAL and Z.LODOS connected with Z.BLIZZARD to form a system that covers the entire process chain, from polymer granulate to prefillable syringes.
ZAHORANSKY CUSTOMERS CHOOSE POLYMER SYRINGES
“Customers can contribute their own know-how to specific assemblies or technologies required for the production of the final product. ZAHORANSKY gladly provides comprehensive advice to its customers and makes recommendations in accordance with cGMP guidelines.”
Why do ZAHORANSKY customers choose plastic as their preferred material for their prefilled syringe products? The greatest advantage COC/COP syringes have over their glass counterparts is that the needle is over-moulded and not melted in or glued in. In the melting process for glass syringes – in which a heat-resistant material such as tungsten is used in temperatures of more than 1,000 °C – heavy metals can enter the glass container and may later be found in the product, despite the containers subsequently being washed, dried, and sterilised. These aspects are crucial when it comes to ensuring that the already impaired health of patients is not burdened further by their treatment. Other persuasive aspects of the plastic version are its minimal risk of breakage and greater freedom in design.
NO HUMAN CONTACT FOR CLEANROOM CONFORMITY
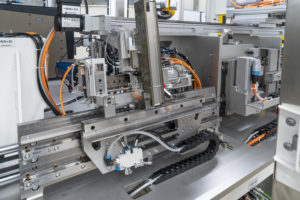
Figure 4: The combination of the Z.NFS with the Z.BLIZZARD, as shown here, forms an integrated system which guarantees maximum purity in the production process, since there is no human contact and the process is cleanroom compatible.
The Z.NFS needle feeding system (Figure 4) ensures the first-in-first-out principle, which means that the system is filled with the required number of cannulas and works in series. This prevents needles from remaining in the system for long periods of time. Z.NFS can process up to 32 needles or cannulas with up to 12 cycles per minute, i.e. 400 units per minute.
Currently, the system can process diameters from 0.2 mm upwards, and lengths of up to 45 mm. In addition to this, Z.NFS is an integrated system that guarantees the highest levels of cleanliness in the production process since no human touches the product, and the process can run in accordance with clean-room conditions. This is a decisive plus in the production of particularly sensitive prefillable syringes. A higher quality in the production of a product for medical technology is barely conceivable.
“The clinical characteristics and requirements of their ultimate customers – patients – are highly individual. In turn, ZAHORANSKY ensures that its pharma customers have maximum freedom in the design of their automation and production systems.”
FULL-SERVICE CONSULTING
The entire pharma and biopharma industry is geared towards guaranteeing the well being of patients through the highest quality production of medication solutions. The clinical characteristics and requirements of pharma companies’ ultimate customers – patients – are highly individual. In turn, ZAHORANSKY ensures that its pharma customers have maximum freedom in the design of their automation and production systems.
For example, customers can contribute their own know-how to specific assemblies or technologies required for the production of the final product. ZAHORANSKY gladly provides comprehensive advice to its customers and makes recommendations in accordance with cGMP guidelines, always mindful that just because something works in the laboratory, it does not necessarily work in an industrial setting. Evidence is provided that the solutions suggested are implemented in a manner that customers can have audited. Should customers already have a firm idea of units or technologies that have proven their worth and that they would like to see integrated in their systems, this can be arranged. ZAHORANSKY thoroughly validates such integrations.
ALWAYS WITH A FOCUS ON IMPROVING THE LIVES OF PATIENTS
Customers receive support even after the system has been delivered to ensure that they have an innovative and future-proof mould and machine. Because even if pharma is not known for making quick changes due to the heavily regulated environment in which it operates, the industry does continue to evolve with modern demands. Likewise, machine manufacturers and producers must continuously optimise their products. This is the basic prerequisite for further and constant improvement of the lives of patients.