Citation: Trenfield S, Basit A, “Personalising Drug Products Using 3D Printing”. ONdrugDelivery Magazine, Issue 99 (Aug 2019), pp 28-32.
The use of 3D-printing technology to create personalised drug therapies is providing some exciting opportunities for improving patient care. Sarah Trenfield and Abdul Basit look at the potential applications in fields such as multiple drug therapy and paediatric/geriatric care and explore how FabRx’s 3D-printing system can produce a range of different formulations to suit a variety of situations.
“Due to the highly flexible nature of the 3D-printing process, the applications
of this technology are extensive.”
Consumers are increasingly interested in shaping the services and products they receive. Recent research has highlighted that more than 50% of consumers express an interest in purchasing customised products or services. This demand will require adaptation by multiple industries,1 including the pharmaceutical sector. Since the Precision Medicine’s Initiative was released in the US in 2015, pharmaceutical research has been pursuing the development of more tailored treatments in an attempt to make medicines safer and more effective. This is critical for complex medication regimes, e.g. multiple dose changes and those with a narrow therapeutic index (i.e. where the level between the therapeutic and toxic is very narrow).
However, the main manufacturing methods for oral dosage forms (tableting and encapsulation) are not able to meet the need for this type of therapy – they were invented over 200 years ago, when cheap, high-volume processes were prioritised over smaller scale, personalised treatments.2 We therefore need to look at new technologies that can provide bespoke tailoring of drug products to suit the individual needs of each patient.3 One such possible technology is three-dimensional (3D) printing. 3D printing is an additive manufacturing process where dosage forms are designed using digital software and sent to a 3D printer to enable on-demand, layer-by-layer production of printlets (3D printed tablets).
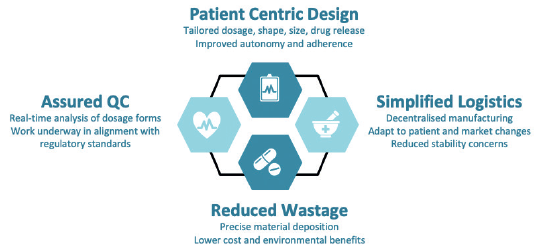
Figure 1: Key benefits of FabRx’s 3D-printing technology for pharmaceuticals.
Since 2014, FabRx has been driving the use of 3D printing in pharmaceuticals by developing a wide range of 3D-printing technologies and formulations suitable for personalised oral dosage form and medical device production. So far, FabRx processes have produced printlets for multiple drugs, flexible dosages, tailored aesthetics (shape, size, flavour and colour) and drug release, giving patients a truly personalised treatment approach. In 2018, FabRx was awarded a grant of nearly £1 million from the UK government’s innovation agency, Innovate UK (Swindon, UK), to develop the world’s first regulatory-approved personalised medicine 3D printer, enabling it to conduct the first clinical study in the world using 3D-printed medicines in paediatrics.4
Advantages
The key benefits of FabRx’s proprietary formulations and 3D-printing processes (Figure 1) include:
- Patient-centric design: The pharmacist can input parameters such as the dosage, shape, size and type of drug release (immediate through to controlled release) to create a tailored drug product, which maximises medication adherence, clinical efficacy and safety.
- Simplified logistics: The 3D-printing systems are both compact and portable, meaning pharmaceuticals can be manufactured on-demand in decentralised locations. Systems can be integrated into clinical settings e.g. hospital, community pharmacies and out-patient clinics, or within remote areas such as disaster zones or even space. On-demand production makes it easier to adapt to changes in patient or market needs, and can also highly benefit medicines that have poor stability or those that require costly cold-chain storage.
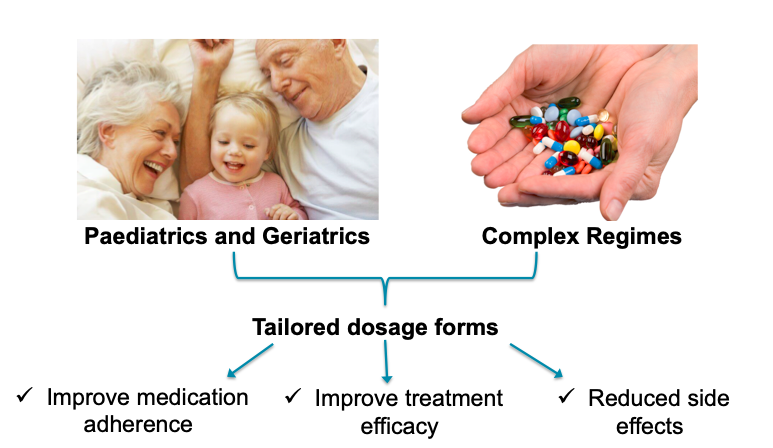
Figure 2: Main applications of 3D-printed medicines.
- Reduced wastage: FabRx’s 3D printers are able to deposit the exact amount of drug product material. This reduces material waste, which is a common problem in pharmaceutical manufacture. It could also reduce costs for preclinical and clinical studies conducted with highly expensive drugs, e.g. in orphan diseases, as well as have environmental benefits.
- Assured Quality Control: FabRx’s pharmaceutical systems are being developed in close communication with regulatory agencies, e.g. the UK MHRA, US FDA and EU EMA, and hospital end-users to create a system that is fit-for-purpose.5 The team are integrating real-time quality control measures to ensure product efficacy and safety.6
Using FabRx’s 3D-printing process could generate increased revenue for pharmaceutical companies through increased medication adherence, improved efficacy and safety profiles, as well as increased product margins via premium pricing.
“Direct powder extrusion enables the production of drug products in a single-step process directly from powdered materials, avoiding the lengthy methods usually required to produce 3D-printer filament feedstock.”
APPLICATIONS OF 3D PRINTING MEDICINES
Due to the highly flexible nature of the 3D-printing process, the applications of this technology are extensive. Although it is unlikely to match the economies of scale for mass-manufactured drug products, 3D printing is well suited to more niche conditions and patient populations, for which current treatment pathways are substandard.
Dose Changes and Geriatric/Paediatric Patients
One such application is for drugs that require frequent dose changes e.g., those with a narrow therapeutic index, or in geriatric and paediatric populations, where dosing requirements can vary markedly (Figure 2). Patients often manually crush or split tablets to achieve the correct dose, which has inherent safety risks. FabRx has therefore focused on developing 3D printers as automatic compounding systems to get the correct dosage. Using a process called semi-solid extrusion, FabRx can produce chewable tablets with precise dosages, shapes and flavours, which can improve medication adherence and acceptability particularly in paediatrics (Figure 3). Indeed, it could be possible for the patient to become involved with the medicine design process, which facilitates patient autonomy.
Clinical Trials
“FabRx has created dosage forms impossible to produce using conventional methods.”
In 2019, FabRx invented a revolutionary 3D-printing system for the production of pharmaceuticals. The system, known as direct powder extrusion, enables the production of drug products in a single-step process directly from powdered materials, avoiding the lengthy methods usually required to produce 3D-printer filament feedstock.7 This technology enables flexible and tailored dosing with minimal development times, which is showing promise in the field of preclinical studies and early phase clinical trials.
Multiple Drugs
Using 3D printing, FabRx has created dosage forms impossible to produce using conventional methods (Figure 4). In one study, the FabRx team 3D-printed pellets (termed miniprintlets) containing two drugs for tailored analgesic therapy (Table 1).8
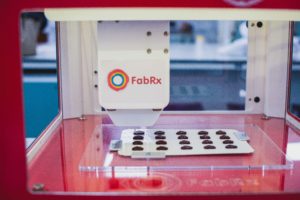
Figure 3: FabRx’s semi-solid extrusion 3D-printing process to create chewable printlets – ideal for treating children.
3D printing could also be useful for those on complex medication regimes. Polypharmacy (the administration of more than one medicine) is a common practice for elderly patients. However, this can cause confusion and difficulty managing the medication. FabRx 3D printers have instead been used to print multiple drugs into the same dosage form to create 3D-printed polypills (aka polyprintlets). As an example, six different drugs were printed in a multi-layered configuration, reducing the number of tablets to just one (Table 1).9 Furthermore, dosage forms with unique and tailored drug release profiles, ranging from rapidly disintegrating dosage forms through to controlled release, have also been produced, simply by altering the printlet geometry or excipient composition.10,11
Global Health
The benefits of 3D printing could also have a wide-reaching impact on global health, tackling major challenges such as the counterfeiting of medicines. It is estimated that 10.5% of low- and middle-income countries are affected by substandard or falsified medicines, costing an estimated US$30.5 billion (£24 billion) annually. To overcome this, the FabRx team developed a unique track-and-trace and anti-counterfeit method, whereby QR codes and smart material inks were printed directly on the surface of drug-loaded tablets to ensure product authenticity (Table 1).12
“With the adoption of non-invasive diagnostics or drug
monitoring strategies, 3D printing could provide a novel,
digitised platform to create tailored medicines in
response to changes in clinical needs.”
CLINICAL TRIALS
As a world first, FabRx’s personalised medicine 3D printer was integrated into a hospital setting to treat children (aged 3–16 years) with maple syrup urine disease (MSUD).13 The first-line therapy for MSUD involves dietary leucine restriction and the oral supplementation of isoleucine and valine. The dose administered to patients requires strict tailoring according to age, weight and blood levels. In current clinical practice, however, practitioners are required to prepare extemporaneous formulations due to the lack of suitable oral treatments for MSUD.
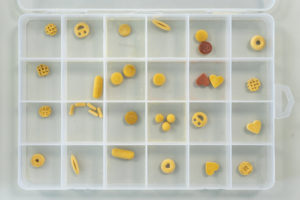
Figure 4: Printlets created using FabRx’s pharmaceutical 3D printer.
To overcome these challenges, FabRx’s 3D printer was integrated into the Pharmacy Department of the Clinic University Hospital in Santiago de Compostela, Spain, to produce chewable tablets containing personalised dosages of isoleucine.14 A variety of dosages, colours and flavours were created, which were evaluated for patient acceptability and therapy control. The researchers found that 3D printing enabled a tighter control over target blood concentrations compared with the standard therapy (capsules), and that the flavours and colours of the 3D printed dosage forms were well accepted amongst all patients.
This study was a significant milestone in 3D-printing history and demonstrated the true benefits of such technology.
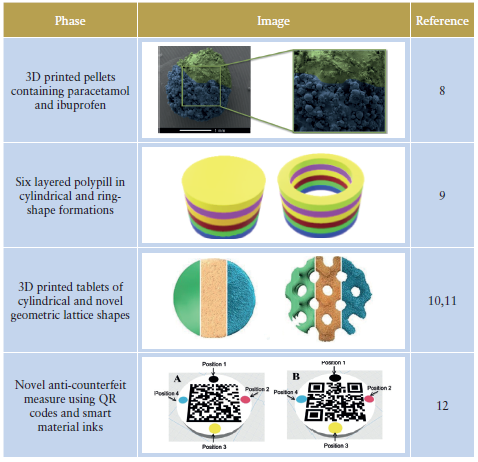
Table 1: Novel applications of 3D printing using FabRx technologies.
CONCLUSION
It is becoming clear that 3D printing has a promising role in the future of oral drug delivery, transforming medicine production away from mass manufacture towards highly tailored dosage forms on demand. With the adoption of non-invasive diagnostics or drug monitoring strategies, 3D printing could provide a novel, digitised platform to create tailored medicines in response to changes in clinical needs. FabRx is providing a flexible dosage form production system using 3D printing to realise the potential of this technology in pharmaceuticals, making treatments safer and more effective for patients.
REFERENCES
- “The Deloitte Consumer Review Made-to-order: The rise of mass personalization (11th Edition)”. Research Report, Deloitte, 2019.
- Trenfield SJ et al, “3D Printing Pharmaceuticals: Drug Development to Frontline Care”. Trends in Pharmacological Sciences, 2018, Vol 39(5), pp 440–451.
- Basit A, Gaisford S (Eds), “3D Printing of Pharmaceuticals”. Springer, 2018.
- “FabRx Awarded Innovate UK Grant to Design the World’s First Personalised Medicine 3D Printer”. Press Release, FabRx, Apr 14, 2019.
- “FabRx meet with the MHRA and AEMPS to discuss 3D printing for personalised medicines”. Press Release, FabRx, Apr 11, 2019.
- Trenfield SJ et al, “3D printed drug products: Non-destructive dose verification using a rapid point-andshoot approach”. Int J Pharm. 2018, Vol 549(1), pp 283–292.
- Goyanes A et al, “Direct powder extrusion 3D printing: Fabricationof drug products using a novel single-step process”. Int J Pharm, 2019, Vol 567, p 118471.
- Awad A et al, “3D Printed Pellets (Miniprintlets): A Novel, Multi-Drug, Controlled Release Platform Technology”. Pharmaceutics, 2019, Vol 11(4), p 148.
- Robles-Martinez P et al, “3D Printing of a Multi-Layered Polypill Containing Six Drugs Using a Novel Stereolithographic Method”. Pharmaceutics, 2019, Vol 11(6), p 274.
- Fina F et al, “Fabricating 3D printed orally disintegrating printlets using selective laser sintering”. Int J Pharm. 2018, Vol 541(1), pp 101–107.
- Fina F et al “3D printing of drug-loaded gyroid lattices using selective laser sintering”. Int J Pharm, 2018, Vol 547(1), pp 44–52.
- Trenfield SJ et al, “Track-and-Trace: Novel Anti-Counterfeit Measures for 3D Printed Personalised Drug Products using Smart Material Inks”. Int J Pharm, 2019, Vol 567, p 118443.
- Goyanes A et al, “Automated therapy preparation of isoleucine formulations using 3D printing for the treatment of MSUD: First single- centre, prospective, crossover study in patients”. Int J Pharm, 2019, Vol 567, pp 118497.
- “FabRx completes a clinical study for the treatment of a rare metabolic disease in children using 3D printed dosage forms”. Press Release FabRx, Apr 11, 2019.