Citation: van Noort J, “Choosing the Right Label Material for Prefilled Syringes”. ONdrugDelivery Magazine, Issue 105 (Feb 2020), p 88-90.
Jos van Noort outlines some of the key factors that must be taken into consideration when selecting a label for prefillable syringes.
“Labelling requires a label facestock that is conformable enough for application on a small-diameter syringe, but also stiff enough to facilitate high-speed labelling.”
The preferred marking technology for prefilled syringes and autoinjector cartridges is self-adhesive labels, which offer the versatility that the pharmaceutical industry is looking for. As is the case when selecting a packaging solution, many influencing factors and tests need to be conducted in order to choose the right label material and to minimise the risk of a failed labelling solution. Typical label material is built from three layers: facestock, adhesive and release liner which is the label carrier (see Figure 1).
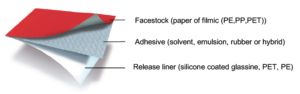
Figure 1: Self-adhesive label construction.
Four key application parameters must be taken into account when choosing a label material for an injectable device:
- Diameter of the primary packaging: the typical diameter of a prefilled syringe is between 7 and 20 mm (0.5 mL).
- Dispensing speed: the products are usually packed on packaging lines at labelling speeds up to 600 pcs / min.
- Temperature across the supply chain: medications are sensitive to temperature and some have to be kept in a cold environment (for example, 2-8°C, or below -20°C).
- Patient safety: syringes and injectors contain liquid medicine, so they must resist migration of any label components.
SMALL CONTAINER DIAMETERS
Prefilled syringes are typically small containers with diameters down to 7 mm. This means that they have higher curvature. Thus, labelling requires a label facestock that is conformable enough for application on a
small-diameter syringe, but also stiff enough to facilitate high-speed labelling.
The choice of label adhesive is also critical, since it must have a high resistance to shearing away from the surface, so that lifting of label edges over time is avoided. In the pressure-sensitive materials industry this resistance is known as mandrel hold, and is specified by FINAT (European association for the self-adhesive label industry) test method 24 (FTM 24). In the label industry, general testing methods are established by FINAT. These methods measure label material performance, however, it is important to note that, whilst often useful, they are not always relevant in the pharmaceutical industry because of its very specific application requirements.
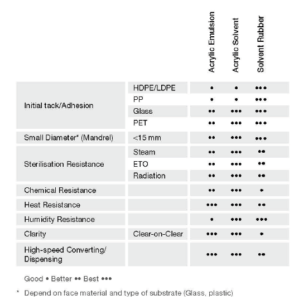
Figure 2: Type of adhesive and performance matrix.
During the FTM 24 test, sample label is applied onto three-quarters of the circumference of the test rod (diameters 7 mm and 15 mm). Samples are then inspected after seven days and the edge-lift is measured. To meet the needs of the pharmaceutical industry, it is recommended to additionally inspect the samples after 14 and 30 days.
The type of adhesive chosen should offer good adherence to the substrate and a well balanced internal strength. The adhesion to the substrate depends also on its surface energy – high-surface-energy substrates like metal or glass have strong molecular attraction, so the mandrel hold on this type of substrate tends to be better. On the other hand, low-surface-energy substrates like high-density polyethylene (HDPE) or polypropylene (PP) have weaker attractive forces meaning weaker mandrel hold. Figure 2 summarises adhesive performance according to type.
DISPENSING SPEED
Label materials intended for use on high-speed packaging lines (faster than 150 pcs/min) must be robust and have high initial tack. Loop tack test (FTM 9) is used to assess the adhesive initial tack (see Figures 3 and 4).
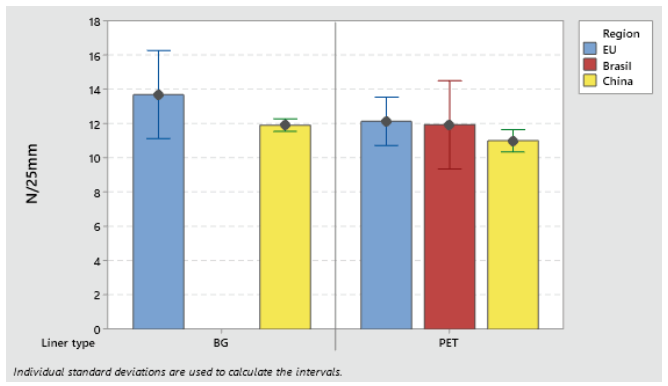
Figure 3: Loop tack adhesion on glass S692NP low-migration adhesive.
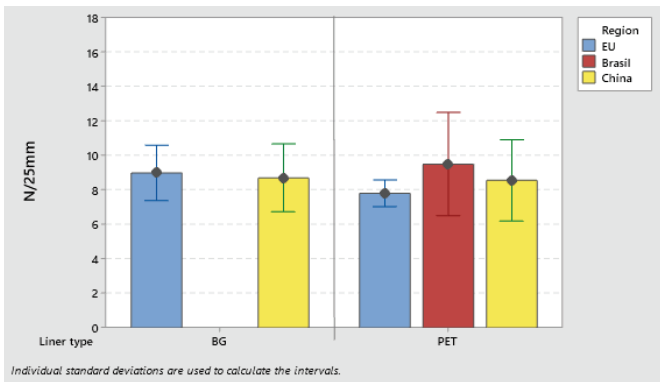
Figure 4: Loop tack adhesion on PP S692NP low-migration adhesive.

Figure 5: Example of flagging (top) compared with proper mandrel hold (bottom).
A release liner made from PET is advised, since PET has a significantly higher internal strength than paper or glassine liners to withstand the application speed. Thinner PET grades (>30 μm) are suitable for most applications.
Another important consideration is choosing an adhesive with high initial tack. Labels are released from the liner and onto the substrate at very high speeds, with an application time less than a quarter of a second. It is critical that the label material’s adhesive has a high initial tack to facilitate good pick-up of the label from the liner to the syringe. However, ensuring a balance between high tack and high adhesion is also important to reduce the potential for flagging of the label over time (Figure 5). It is by balancing these adhesive characteristics in combination with the face material that a construction is made suitable for an application.
Additionally, when using UV detection systems to confirm the label presence, the label has to be luminescent. Label materials with luminescent topcoat are a good solution thanks to the stability and durability of the luminescence they provide. Finally, because of the variety of dispensing machines and application mechanisms, labelling materials must be tested in real-world circumstances in order to confirm the outcome of laboratory testing
TEMPERATURE ACROSS THE SUPPLY CHAIN
As well as dispensing speed and container size, temperature and humidity must also be considered. The conditions experienced by a product across the supply chain influences label material selection and performance.
With more advanced medicines such as biologics, there is a more complex supply chain. Prefilled syringes can be exposed to extremely high temperatures and humidity during autoclave sterilisation, or to low temperatures when the finished product is stored or transported. This creates another challenge for label materials, which must stay on the substrate with unchanged performance and appearance.
Changing temperature also causes condensation on the surface of syringes and label substrate. Extended exposure to moisture might cause adhesive whitening and label creasing if the wrong label material is used. With these parameters in mind, it is crucial to distinguish between application temperature and service temperature when choosing the adhesive. Application temperature is the temperature when the label is applied, and service temperature is a range within which the adhesive will function once the label has been applied.
FTM 13 assesses the ability of a pressure-sensitive material to adhere under low temperature conditions. Labels are applied to various substrates (polyethylene terephthalate (PET), glass, polyethylene (PE), stainless steel) and stored under chill (4°C) and deep freeze (-25°C) conditions. After one hour, and at seven days, the removability of the labels is accessed. It is recommended to also test cyclic olefin copolymer (COC) and cyclic olefin polymer (COP) substrates and extend the testing to 14 and 30 days. Additionally, high temperature resistance is tested in steam sterilisation at 121°C for 20 minutes.
PATIENT SAFETY
Surpassing all technical requirements is patient safety and brand protection. Prefilled syringes made of plastics like COC or COP can generate benefits such as convenience and possible cost improvements, when compared with traditional glass syringes. Plastic syringes containing liquid medicine can be exposed to contamination from label adhesives, inks, coatings and varnishes – any of which may migrate through the container if specified incorrectly.
To prevent potential contamination of the medicine inside containers, certified labelling materials must be used, alongside an adequate printing technique from the label material converter. Migration studies and testing of specific label materials can be conducted by independent testing institutes on request.
The migration potential of the label material should be assessed by its manufacturer, in co-operation with an independent testing institute. Dedicated pharmaceutical adhesives must have a complete set of certificates (such as migration and toxicology. among others).
Brand owners also need to consider consumer and brand protection against counterfeit products. These can enter their supply chain and ultimately reach the consumer. The International Federation of Pharmaceutical Manufacturers and Associations (IFPMA) estimates that 15% of medicines worldwide may be fake. Although, protection from counterfeit medicines is a complex topic, which requires multiple prevention systems and solutions to protect the value chain, label materials can be a useful element. One solution is luminescent labelling, revealing a specific colour or pattern under UV light. Label materials with luminescent top-coating can have different colours, and these can be difficult to copy. They can also have a customised pattern with a brand logo or medicine name, which is visible only under UV light.
CONCLUSION
We have highlighted four main factors to address when choosing a label material for prefilled syringes: diameter, dispensing, temperature, and patient safety. All four factors are important considerations when choosing a label material for a syringe. Of course, there can be other considerations specific to a product and/or value stream. These may include exposure to certain chemicals or sanitisers, the type of secondary packaging used, the type of printing technology, and the types of inks used.
In order to ensure that an optimal label solution is selected, it is also desirable to involve the label material manufacturer early on in the development of drug packaging. This allows the design and administration of a specific testing regime that aims to mimic the product’s real-life application and service environment. The result is a reduced risk of selecting an inappropriate label solution, and a shorter trial time at lower cost.
Previous article
NEXT-GENERATION WEARABLE DELIVERY DEVICES FOR LARGE-VOLUME BIOLOGICSNext article
OXYCAPT MULTILAYER PLASTIC VIAL AND SYRINGE