To Issue 175
Citation: Parmee R, “Harnessing X-Ray and AI for a New Era of Quality Control”. ONdrugDelivery, Issue 175 (Jul 2025), pp 40–42.
Dr Richard Parmee discusses the multitudinous applications of X-ray inspection technology for high-speed pharmaceutical production lines, covering the value of introducing artificial intelligence and machine learning techniques to enhance detection and improve safety.
Patients and healthcare professionals take it for granted that there will be one tablet in each cavity of a blister pack when they open a new box of drugs – and that they will all be the tablets described on the packaging. However, for pharma manufacturers, it is no mean feat to ensure that there are no extra, missing or incorrect tablets in a sealed blister pack on a high-speed production line.
“ALL THESE ISSUES – AND MORE – ARE NOW BEING ADDRESSED BY A NEW GENERATION OF X-RAY TECHNOLOGY THAT CAN DO SO MUCH MORE THAN DETECT A FRAGMENT OF METAL OR GLASS IN A DRUG CONTAINER OR AUTOINJECTOR.”
Products containing multiple tablet formulations that are to be taken at different times add to the complexity for manufacturers. Other everyday challenges where the stakes are high include checking for dangerous air bubbles in a prefilled drug-device combination product, such as an insulin pump, and ensuring that the needle of an autoinjector is in the correct position. All these issues – and more – are now being addressed by a new generation of X-ray technology that can do so much more than detect a fragment of metal or glass in a drug container or autoinjector.
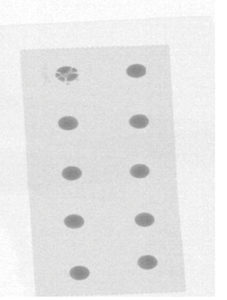
Figure 1: A broken tablet in a blister pack.
HIGH SENSITIVITY AND HIGH RESOLUTION
The latest X-ray systems combine low-energy X-ray imaging with active pixel sensor (APS) technology to achieve high sensitivity, with resolutions 10 times greater than traditional end-of-line X-ray machines. This means that these machines can detect not only missing or broken tablets (Figure 1), with an inspection zone created around each tablet pocket, but also contaminants, such as metal, even though the products are packaged in metallic foil blister packs. X-ray technology can even detect paper inside cardboard by using adaptive algorithms to check that each box contains an instructions for use (IFU) leaflet to ensure regulatory compliance (Figure 2).
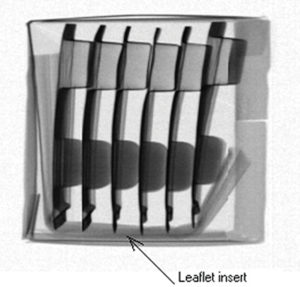
Figure 2: Checking for the presence of an IFU leaflet.
X-ray technology can also be used to check the mass of a product, such as to ensure that the dose carriers for powder inhalers meet the therapeutic dose limits or confirm that containers of common over-the-counter medications meet the necessary weight requirements. It can also check the individual masses of a series of items within a pack, enabling it, for example, to detect and reject an underweight bottle of cough syrup in a multipack, even if some of the other bottles contain slightly too much medication. Another potential functionality is to verify the number of products, such as syringes, in a sealed multipack. Furthermore, it can provide an elemental analysis to differentiate tablets with different formulations.
Foreign body detection has always been crucial for formulations in drug containers. The new generation of X-ray inspection equipment can detect metal or glass particles with diameters as small as 0.1 mm, which would not be visible to the naked eye on a high-speed production line. Image processing software now provides the tolerance levels required to deal with the variable shape and thickness of glass containers. The technology can cope with tapered shapes, ridges and bulges, enabling it to detect tiny shards of glass within a glass vial – as well as confirming that the container is filled to the correct level. The presence of potentially dangerous bubbles in a vial or ampoule of liquid medicine can also be detected.
QUALITY CHECKS
As medical devices become ever more complex, the latest technology can also perform quality checks on drug delivery devices such as autoinjectors (Figure 3), ensuring that the needles are in the correct position and that other parts of the device mechanism are within position tolerances. In-line inspection machines are automatically fed and motorised on different axes so that the autoinjectors can be rotated for the required quality checks.
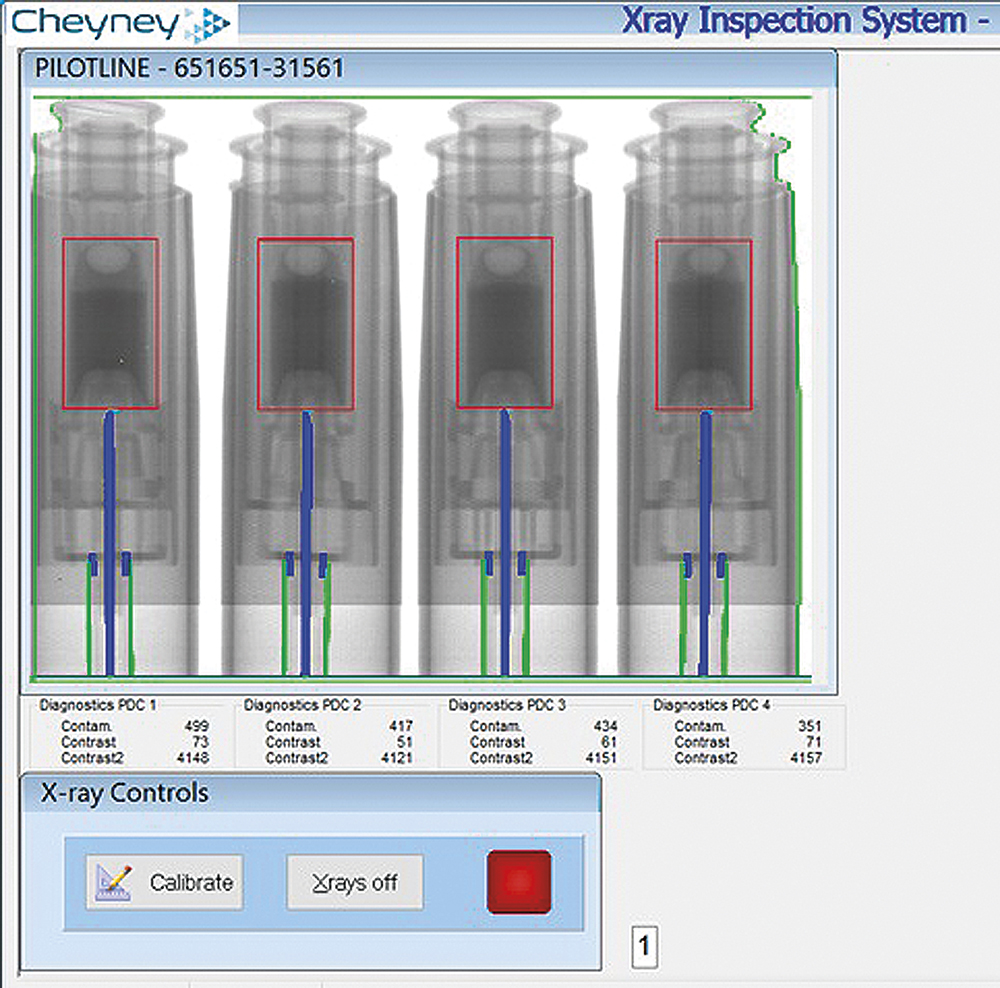
Figure 3: Checking the position of autoinjector needles.
The technology can even cope with the challenge of subcutaneous osmotic insulin pumps, where the drug is packaged in a hollow titanium rod where it is vital there are no bubbles, which could cause the flow of insulin to be interrupted. The radiography is challenging as it involves inspecting organic material with air voids through a machined titanium enclosure. However, techniques such as mechanical stabilisation and combining multiple image sets can be used to enhance the feature contrast.
Packaged dressings containing silver salts, which provide anti-microbial properties, are another example of where the latest X-ray inspection technology can help manufacturers. In this case, it provides a way of checking the presence and assay level of these elements on the production line, as well as ensuring that the contents are correctly positioned within the packaging.
ARTIFICIAL INTELLIGENCE AND MACHINE LEARNING
Until now, automated inspection systems have generally used rule-based algorithms, which require skilled software resources and substantial testing. However, with the advent of artificial intelligence (AI) and machine learning (ML), X-ray imaging can be combined with AI-based algorithms so that manufacturers can automate the training and defect detection processes with unparalleled accuracy.
“ONCE TRAINED, THESE ALGORITHMS CAN RAPIDLY ANALYSE LARGE VOLUMES OF IMAGES AND FLAG POTENTIAL DEFECTS, SUCH AS FOREIGN BODIES, LOCATIONS, VOIDS, MISALIGNMENTS OR OTHER IRREGULARITIES THAT MIGHT OTHERWISE GO UNNOTICED.”
AI algorithms, particularly those based on ML and computer vision, are trained to recognise patterns and anomalies within X-ray images. Once trained, these algorithms can rapidly analyse large volumes of images and flag potential defects, such as foreign bodies, locations, voids, misalignments or other irregularities that might otherwise go unnoticed. This automation not only reduces human error but also speeds up the inspection process, resulting in higher throughput and lower production cost.
PREDICTIVE MAINTENANCE
Maintaining equipment and machinery in optimal working condition is essential for minimising downtime and avoiding costly repairs. Predictive maintenance is an area where AI and X-rays are proving to be game changers. Traditionally, maintenance approaches rely on scheduled service intervals, often leading to unnecessary downtime or missed opportunities to address emerging issues.
By combining X-ray imaging with AI, pharma manufacturers can implement predictive maintenance strategies that allow for real-time monitoring of machinery components. X-rays provide detailed insights into the condition of critical parts, while AI analyses the data to predict when a part is likely to fail. This enables companies to perform maintenance only when it is truly needed, avoiding unplanned breakdowns and reducing the costs associated with unnecessary repairs.
For example, AI-powered X-ray systems can be used to monitor the structural integrity of critical components, ensuring that wear and tear are detected before they lead to failure. This proactive approach to maintenance increases operational efficiency and extends the lifespan of machinery and equipment.
WORKER SAFETY
Worker safety is a paramount concern in manufacturing environments, especially when dealing with heavy machinery, hazardous materials or complex assembly processes. AI and X-rays can contribute to safer working conditions by automating inspection processes and reducing the need for human workers to interact with potentially dangerous equipment.
AI algorithms can process X-ray images and identify high-risk areas where failure is likely. By identifying and addressing these risks early, pharma companies can prevent accidents and protect their workers from harm. Moreover, by automating routine inspections, AI and X-rays can reduce the exposure of workers to harmful radiation, toxic substances or dangerous machinery – further contributing to a safer workplace.
INTEGRATION TO TRANSFORM MANUFACTURING
The integration of AI and X-rays in manufacturing and production is set to transform the pharma industry. By automating critical tasks and providing real-time insights into the condition of materials, machinery and products, this powerful combination allows manufacturers to achieve higher efficiency, reduce costs and maintain competitive advantages.
As AI and X-ray technology continue to evolve, their impact on the manufacturing landscape will only grow. And, with millions of patients relying on their medication every day, that represents a helping hand for pharma manufacturers when it comes to ensuring that each dose is right the first time – every time.